Prozesssicherheit in Schnellem Takt
Kontakt

Als typischer Zulieferbetrieb für die Automobilindustrie, den Büromaschinenbereich und für den Elektromaschinenbau fertigt die Firma Berger in Memmingen eine Vielzahl unterschiedlichster Teile und einbaufertige Komponenten. Mit etwa 1600 Mitarbeitern ist Berger weltweit präsent. Etwa 600 Mitarbeiter produzieren am Rande des Allgäus mit einem großen und modernen Maschinenpark Präzisionsteile in mittleren und großen Serien.
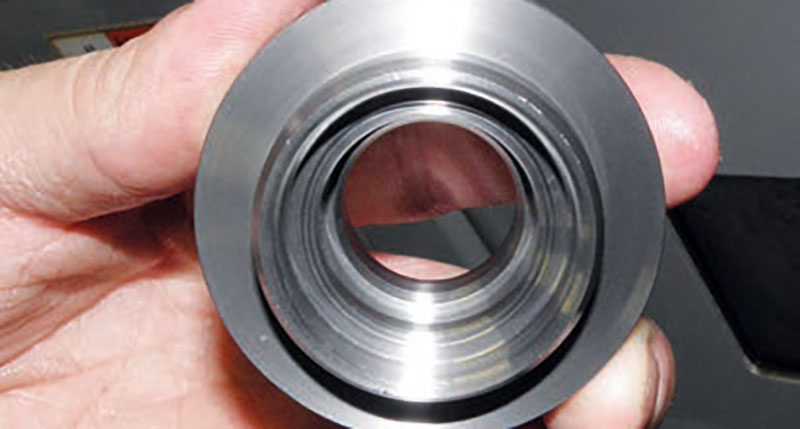
Gefordert wird eine störungsfreie Zerspanung bei gleich bleibender Passungsgenauigkeit in einem engen Toleranzband von 25μm in der Teilelänge von etwa 10 mm und 23μm bezogen auf den Durchmesser von 40 mm. Gelegentlich kam es zu Fertigungsfehlern, als deren Ursache sich eine Fehlpositionierung bei der automatischen Einlage des Teiles in die Bearbeitungsspindel entpuppte. Hier können sich Späne zwischen Anlage und Teil legen und zu einer schrägen Lage des Werkstückes in der Bearbeitungsspindel führen, was eine fehlerhafte Bearbeitung nach sich zieht.
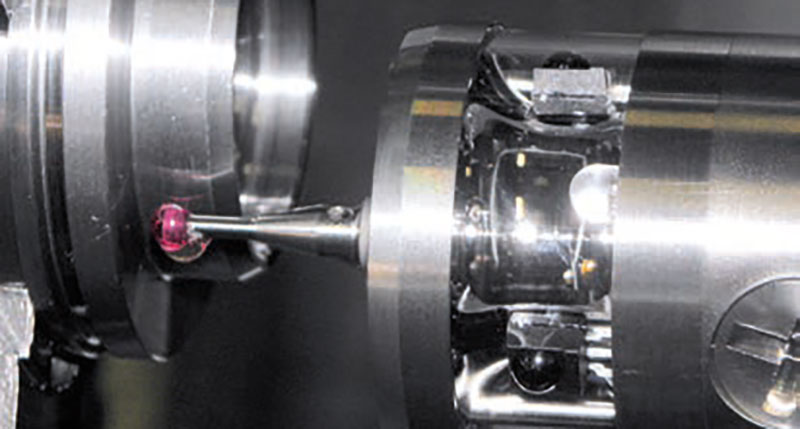
Nicht so beim speziell für den Einsatz in Werkzeugmaschinen ent-wickelten Messtaster IRP40.01 von m&h. Mit seinem Körper aus Edelstahl, der Diodenabdeckung aus gehärtetem Echtglas und der Abdichtung nach IP68 Standard, sowie dem bekannt robusten Messwerk ist er für diese Umgebung geschaffen und verspricht lange Lebensdauer. Die Datenübertragung über die besonders gesicherte, leistungsstarke HDR Infrarot-Technologie sorgt nicht nur für prozesssichere Signale, sondern zeigt sich auch unbeeindruckt von den Umfeldeinflüssen in der Drehmaschine, wie anhaftenden Spänen, Kühlmittelfilm, Ölnebel und Fremdlicht. Dies ist die entscheidende Voraussetzung für einen Einsatz auf dem Revolver einer Drehmaschine. Sein schlanker Durchmesser von nur 40 mm und die Länge von nur 50 mm vermeiden Kollisionskonturen und lassen selbst den Einbau in den kleinen Arbeitsräumen von Futterdrehmaschinen oder Drehautomaten zu.
Der Messtaster wird alle 45 Sekunden
aufgerufen und misst sechs Punkte
am Werkstück,
Ausgestattet mit einem kurzen Taststift wird dieser
Taster seit einiger Zeit in der Serienfertigung bei Berger
in Memmingen eingesetzt. Alle 45 Sekunden wird der
Taster aufgerufen und mit verschlüsseltem Infrarotsignal
eingeschaltet. Er tastet sechs Positionen an Flansch und
Außendurchmesser an und übermittelt gleichzeitig die
Tastpositionen an die Steuerung. Um Energie zu sparen, wird
er unmittelbar nach dem Antasten wieder ausgeschaltet.
Nur wenn alle 6 Werte innerhalb des zulässigen Bereiches
liegen, wird der Bearbeitungszyklus fortgesetzt. Für
den Kontrollvorgang selbst werden nur 5 Sekunden des Bearbeitungszyklus benötigt. Ursprünglich war die Maschine
so programmiert, dass Sie, bei Messwerten außerhalb der
vorgegebenen Toleranz, den Bearbeitungsvorgang nicht
fortgesetzt hat. Dies bedeutete dann aber einen ungeplanten
Maschinenstillstand, der die erreichbare Kapazität der
Maschine einschränkte. Schließlich musste immer erst ein
Bediener kommen, das Teil entnehmen und den Vorgang neu
starten. Um diese kostbare Produktionszeit zu sparen, wird
nun bei Fehlmessung das Werkstück automatisch wieder
entnommen und zurückgeführt. Ebenso automatisch wird ein
neues Teil eingelegt. Damit startet sofort ein neuer Zyklus,
ohne auf einen Eingriff von außen zu warten. Das spart Zeit
und erhöht die Autarkie der automatisierten Maschine. So
konnte die Kapazität und Produktivität dieser Maschine, die
meist dreischichtig läuft, spürbar gesteigert werden.
Weil es immer mal zu Fehlern in den Maschinen kommen
kann und weil besonders Späne in Drehmaschinen
gefürchtet sind, hat Berger einen Ersatzmesstaster
angeschafft. Aber bislang wurde der noch nie benötigt.
Der eingesetzte Taster verbleibt immer im Revolver der
Maschine und verlangt keine besonderen Wartungsarbeiten.
Eventuell anhaftende Späne am Messtaster stören nicht.
Späne und Anhaftungen an Taststift und Tastkugel werden
durch die starke Kühlmitteldusche entfernt und haben
bislang den Messvorgang noch nicht gestört.
Die nachträgliche Installation von Infrarotempfänger
und Messtaster bei Berger wurde von m&h-eigenem
Servicepersonal und einem m&h-Steuerungsspezialisten
für Fanuc-Steuerungen vorgenommen. Durch ihn erfolgte
auch die Erstprogrammierung vor Ort und die Anpassung
an die Fanuc-Steuerung der Takamaz. Die Maschine wurde im Beisein von m&h eingefahren und läuft seit
dem klaglos.
Eine vergleichsweise kleine Investition
zeigt im täglichen Einsatz große Wirkung, weil nun die
Produktion ohne ungeplanten Stillstand läuft. Selbst bei
Einlegefehlern produziert die Maschine weiter. Die wenigen
Sekunden, die für das Antasten benötigt werden, haben
sich längst über fehlerfreie und reibungslose Fertigung
amortisiert. Das Messen in der Maschine trägt auch in der
Serienfertigung zu deutlich gesteigerter Prozesssicherheit
und Wirtschaftlichkeit bei.