Manoeuvring 80 metres of wingspan in a few minutes
Hexagon global measuring equipment in cooperation with ARGON delivers an optimal man-machine interface for A380 control
Contact us

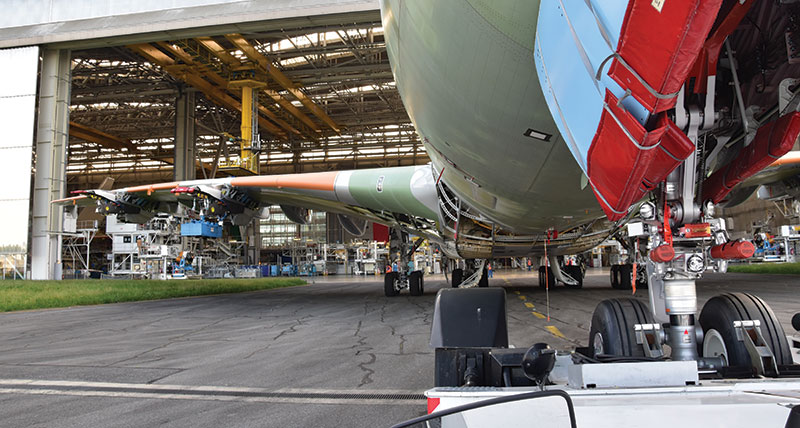
This giant of the air is 73 metres long for 80 metres of span and 24 metres of height – equivalent to an eight-storey building. Its nearly 280 tons when unloaded are supported by 20 wheels on the ground. Although the manoeuvrability of such a machine is only part of the problem; keeping an overview is also a difficult challenge to solve. ‘Previously, the “hangering” was done entirely visually, using two orientation bars fitted beneath the aircraft. It’s a very long and cumbersome mechanical system to manage. Sometimes the operation had to be repeated several times, which increased the stress factor for the pilot of the aircraft tractor’, explains Pascal Montoya, Head of the Tooling Design Office of the Final Assembly Line (FAL) A380 at Airbus.
Objective: first time success of the moulage process

Each aircraft reacts differently. But each of them tends to deviate along the line visualised on the ground. It is therefore extremely important to be able to “aim” correctly from the start and adjust the trajectory as the hangaring progresses. And this must be done while not wasting too much time and with a final accuracy of to within five centimetres.
A first test based on a total station was validated in 2012. ‘Airbus therefore wanted to duplicate the means while improving the basic version. Unfortunately, it turned out that the software used at the time was no longer updated. We therefore called on Hexagon, with whom we are already working in other areas, to develop a successor to our solution,” explains Cédric Dereux, Project Manager at the Tooling Design Office.
Although such a solution is not part of Hexagon’s standard product range, the technology already existed in the group, as well as the expertise in machine guidance. In fact, the total station used in the first version had been supplied by Hexagon. The idea was to use a more recent total station, accompanied by a state-of-theart man-machine interface developed by Hexagon partner ARGON.
Development of a state-of-the-art industrial interface

The Leica iCON is a high-performance robotic total station developed and manufactured by Hexagon Geosystems. Specialised for measurements in the construction industry, the Leica iCON fast-tracking system and unique automatic set-up measurement method make it an ideal tool for this precise application. Made for data capture, control surveys, installations, machine guidance or field surveys, the Leica iCON offers speed, precision and reliability. A single tablet manages the interface for the new total station as well as for the old one.
The solution adopted totally meets our needs“ARGON, Hexagon’s major partner in this project, has developed a protocol (SDK) for direct communication with the total station and the Airbus Guidage operator interface, which is simple and very easy to use. Key manoeuvring information is made available to the operator instantly. Hexagon’s expertise as project coordinator and specialist in aerospace constraints and solutions was very useful,” says Mr Dereux. The solution adopted today consists of a real-time laser guidance system accompanied by a tablet operated by the pilot of the aircraft tractor.
‘We can only think of the positives with this towing solution,’ says Nicolas Llorens, team leader for Poste 30 at Airbus Toulouse. ‘The time saving – up to an hour per manoeuvre – helps the whole station. The method is fast and more efficient, especially at night or in case of rain. The tablet system is ideal. It’s both a comfort for the drivers and the team. There’s much less pressure.’