Developing new numerical tools to boost the application of digital twins
Hexagon’s unique laser scanner and vision system combination helps numerical simulations of the manufacturing of complex-shaped composite parts.
Contact us
The University of Applied Sciences and Arts Northwestern Switzerland (Fachhochschule Nordwestschweiz – FHNW) is one of Switzerland’s leading universities of applied sciences and arts. Its broad range of degree programmes, hands-on teaching concept, innovative and applicationoriented research and global network make FHNW a diversified and appealing educational institution, a soughtafter partner to industry and an attractive employer in northwestern Switzerland.
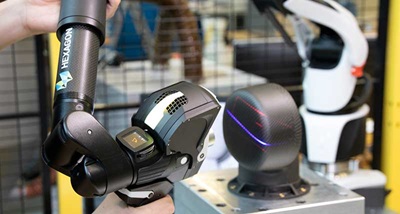
Nägeli is a family-owned enterprise founded in 1941 and situated in Güttingen on the shores of Lake Constance. It develops and manufactures high-precision parts out of metal and advanced composites for different market segments, such as defence, textiles, mechanical engineering, automotive, optics or space. The low weight and high stiffness of the parts used in advanced composite technology (glass and carbon fibre reinforced plastics) offer various essential advantages and allow a significant increase in the performance of mechanical systems.
One of Nägeli’s tailor-made parts is an element of a moving section from an autonomous space robot. FHNW had been brought onboard with the goal of helping Nägeli to produce those composite parts right on the first try.
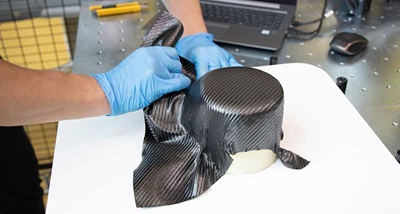
“When we started with the project, we did not have any measurement equipment. We had to play around and made a lot of trial and error. This is a critical issue in the development of the project because of time and resource limitation.
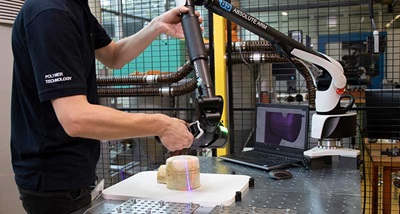
“We succeeded in this unique solution thanks to our great cooperation with Hexagon and the use of their innovative technologies. Hexagon not only sold us a product but offered a lot of support and interaction in developing a measurement strategy in order to find the best solution to incorporate the measurement system into our production environment and handle the data.”
The requirements on these composite parts are very high, and not only because the final product will end up in space, meaning failure would be catastrophic. The composite fibres must be aligned in a very exact position with correct fibre angles in a well-defined condition across every layer of the material in order to ensure the final part has the required strength and flexibility.
FHNW calls this “as-designed” manufacturing. While manufacturing the part, the textile is draped onto the mould, creating an unavoidable interaction between the mould geometry and the fibre architecture, especially for very complex geometries. Besides the skill of the worker and the way that the fabric is laid, the type of fabric also influences how the fibre will end up in the final part.
Using the as-built configuration as a basis for numerical simulation would not be possible without the evaluation of the actual fibre orientation with the Hexagon system. “We’re developing new numerical tools to boost the application of digital twins,” said Dr -Ing. Oliver Döbrich, Research Associate at the University of Applied Science. “We’re applying several approaches with many inputs for the material and the geometry.
“The manufacturing of composite materials is done by draping the textile reinforcement structure onto complex-shaped moulds. Here geometry, fibre orientation and material define part stiffness and final material properties. As draping the prepreg material layer-over-layer onto the mould is a fully manual process, deviations from the ideal developed geometry appear often and easily, especially with regards to the defined fibre orientation (resulting shearing angles differ from nominals) in the stack of reinforcement layers.”
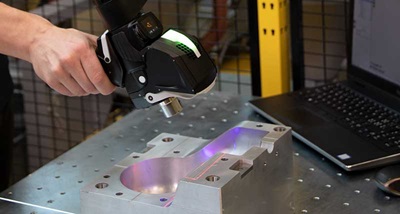
First comes the capturing of the geometry of the actual part, then the geometry of the real manufacturing mould (positive or negative) for every layer added to the stack, then the geometry of the final built part (preform and final cured state). There are several possibilities here to compare the part with the ideal CAD data.
Second comes the digitisation of the part surface texture and detection of the real fibre orientation after the draping process, layer-by-layer (or ply-by-ply).
The complete process chain is built on a virtual level. From the digital forming of the textile layers, which is done virtually for the complete stack by the drape simulation, to the layup of the plies and the curing in the oven, everything is done in a simulation able to estimate the deformation due to chemical shrinkage.
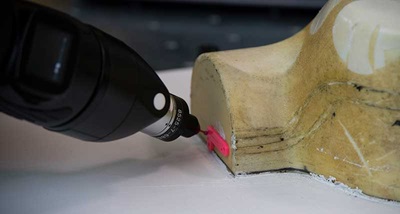
Manufactured parts never look exactly as planned, especially when it comes to the manual draping of prepreg-based composite parts. Here the manufacturer needs to have an idea about every single part being produced, which means either implementing a quality management system or developing a first-time-right strategy. A virtual system with the help of a numerical simulation helps a lot in any case, but the data still needs to be validated.
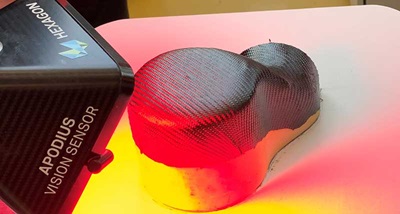
“Thanks to the Absolute Arm we can detect the complete surface structure and texture,” said Döbrich. “A point cloud is generated with the RS6 Laser Scanner, which gives us a very fine resolution of the surface. We use the 3D Vision System to map actual surface photographs onto the meshed surface. The Explorer 3D software then calculates the fibre orientation in every single location and provides a cloud consisting of arrows of every measured orientation at every location of the mesh. This is a unique way of reporting that can’t be provided by any other device.
“The produced digital twin can then be exported from the Hexagon software and be used as an input into the finite element analysis (FEA) software in order to carry out a virtual production test of the built part with the as-built data and not with the ideal as-planned information from our drape simulation.”
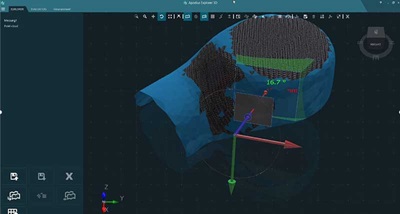
“Using the as-built configuration as a basis for numerical simulation would not be possible without the evaluation of the actual fibre orientation with the Hexagon system,” said Döbrich. “And even more, the RS6 Laser Scanner enables us to evaluate deformations from draping and curing as well as from the homogenous textile structure bringing deformation to the surface level.
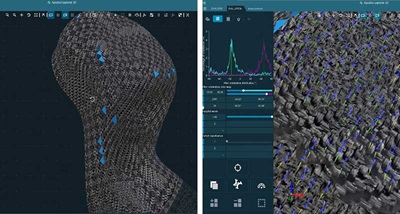
“A simulation can even be carried out to assess the behaviour of the as-built part in terms of critical part failure and discover whether the as-built part will meet the requirements for structural integrity, even if it has not been produced with 100 percent conformity to the design data. Often a part will still comply with mechanical requirements even though an applied quality management system has already declared the actual produced part as scrap. At FHNW we are now looking forward to applying this new technology in further research projects to support companies, especially small companies manufacturing complex parts.”
These additional analysis possibilities are well served by Hexagon’s Digimat software suite, a state-of-the-art multiscale material modelling platform that can simulate actual as-built part properties.