Building BLOODHOUND SSC the 1000mph office
BLOODHOUND Project - United Kingdom
Contact us
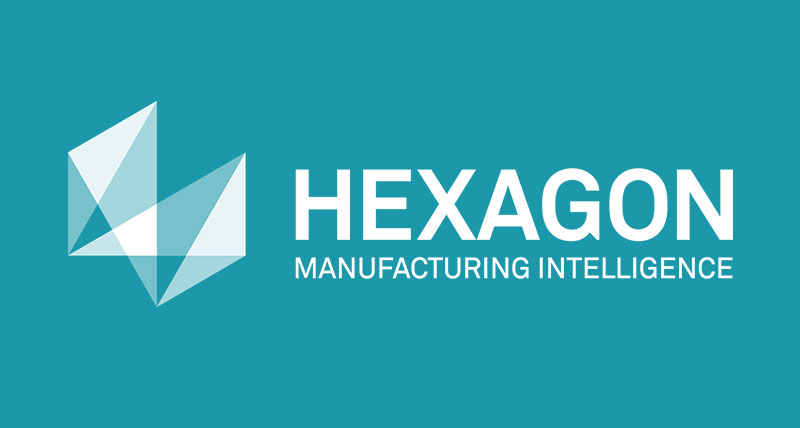
When the BLOODHOUND SSC car makes its runs in the South African desert its wheels will be subjected to forces up to 50,000 G, the solid aluminium wheels each weighing 95kg will spin at 10,200 rpm – 4x faster than a formula one car. At peak speed the car will be moving faster than a bullet from a .357 magnum, covering 1 mile in only 3.6 seconds.
To achieve these amazing feats of engineering the BLOODHOUND Project team are using cutting edge techniques to design and manufacture a car capable of breaking the current land speed record and going faster than 1000mph. A key element in the build is metrology, precision data is required to make sure the car can achieve the desired results and set a new world record, and that is where Hexagon Metrology come in.
At a technical park in Bristol, UK, the BLOODHOUND Project’s base from the outside is an unassuming industrial unit which looks like any other, but on the inside some of the greatest minds in the UK are working to build the world’s fastest car. The project is headed by non-other than Richard Noble, himself a previous land speed record holder. Richard has assembled a team of professionals from motorsport and aircraft manufacture to give Wing Commander Andy Green, BLOODHOUND’s driver, quite literally the fastest office on land.
Due to the many elements that make up the 12.8m long car, the build process is being split into several modules, allowing work to continue on several elements at the same time. To ensure that the modules remain intrinsically accurate with each other the team are using fixtures. This is the first place where the Leica Absolute Tracker AT402 makes its mark. Utilizing the tracker the team are able to pick out key alignment points on each module and fixture, and can therefore virtually check that all parts are in the correct place as they build them.
Luke Dee, Components & Assembly Management Engineer at BLOODHOUND commented on using the new probe, “Collecting measurement data is so much quicker with the Leica B-Probe than using traditional reflectors, we can now set the tracker up and get all the data we need without having to move and re-reference the tracker, combine that with the excellent SpatialAnalyzer software and I would estimate that its halving the measurement time.”
Commenting on the contribution of Hexagon Metrology, BLOODHOUND SSC Project Director, Richard Noble said: “As we push the boundaries beyond 1000mph we need a partner that can match our ambition and provide us with mission critical measurement services using a range of leading-class equipment at the forefront of metrology. From the smallest detail on the car to the alignment of the major car components over its total 12.8-meter length, everything has to be right.”
Hexagon Metrology is proud to be a part of this amazing project and looks forward to working further with the team as the car completes assembly, goes through runway testing, breaks the sound barrier and then ultimately achieves a new world land speed record of 1000mph. We are pleased to be along for the ride.
To achieve these amazing feats of engineering the BLOODHOUND Project team are using cutting edge techniques to design and manufacture a car capable of breaking the current land speed record and going faster than 1000mph. A key element in the build is metrology, precision data is required to make sure the car can achieve the desired results and set a new world record, and that is where Hexagon Metrology come in.
At a technical park in Bristol, UK, the BLOODHOUND Project’s base from the outside is an unassuming industrial unit which looks like any other, but on the inside some of the greatest minds in the UK are working to build the world’s fastest car. The project is headed by non-other than Richard Noble, himself a previous land speed record holder. Richard has assembled a team of professionals from motorsport and aircraft manufacture to give Wing Commander Andy Green, BLOODHOUND’s driver, quite literally the fastest office on land.
Inspiring a generation
Breaking 1000mph is not the main mission of the BLOODHOUND Project, the key driver of the project is to inspire the next generation to consider careers along the line of STEM subjects (Science, Technology, Engineering and Maths). There is a whole team of educational ambassadors that are working with over 5000 schools and colleges across the UK and beyond. Their duty is simple, use the exciting material of the BLOODHOUND Project to enthuse the engineers of tomorrow. Hexagon Metrology is pleased to have some of its own staff involved with the education programme.Straight and symmetrical
So how did Hexagon Metrology become an official Product Sponsor for the project? Conor La Grue, Engineering Lead Commercial at BLOODHOUND, comments “From the first moment components were being manufactured we knew we needed to find a suitable partner to achieve the ultimate in precision. With the forces subjected on the car’s structure when it reaches top speed we need confidence in build quality and most importantly that the car is straight and symmetrical. We originally met at an engineering event and Hexagon Metrology introduced to us the possibility of using their products and services to measure various stages of the car build, and we were pleased to sign them up as Product Sponsors.”Due to the many elements that make up the 12.8m long car, the build process is being split into several modules, allowing work to continue on several elements at the same time. To ensure that the modules remain intrinsically accurate with each other the team are using fixtures. This is the first place where the Leica Absolute Tracker AT402 makes its mark. Utilizing the tracker the team are able to pick out key alignment points on each module and fixture, and can therefore virtually check that all parts are in the correct place as they build them.
Measuring points the tracker cannot see
The Leica Absolute Tracker AT402 utilises spherical mounted retro-reflectors (SMR’s) to gather 3D point data. Traditional methods require that the tracker has line-of-sight to the SMR in order to take measurements, whilst it was still possible for the team to measure all the features they needed using this method, it meant that they constantly needed to move the tracker to achieve line-of-sight. This brought Hexagon Metrology to suggest that BLOODHOUND become an early user of the new Leica B-Probe, a handheld probing tool for the Leica Absolute Tracker AT402. The Leica B-Probe can gather hidden 3D points in a measurement volume of 20 m (ø). For very large structures that require highly accurate measurements, the volume can be extended within a working volume of 320 m (ø) with virtually no loss in probing accuracy by completing a laser tracker move station.Luke Dee, Components & Assembly Management Engineer at BLOODHOUND commented on using the new probe, “Collecting measurement data is so much quicker with the Leica B-Probe than using traditional reflectors, we can now set the tracker up and get all the data we need without having to move and re-reference the tracker, combine that with the excellent SpatialAnalyzer software and I would estimate that its halving the measurement time.”
Planning for measurement in the desert
The BLOODHOUND team have taken the use of the tracker one step further. The tail section of the car looks like it came straight from a jet fighter and the forces which will be placed on the tail during high speeds make it the hardest working tail fin ever produced. But to transport the car, the tail will need to be removed, which means when they reassemble it on the Hakskeen Pan (the dried lake bed in the Northern Cape of South Africa where the car will run) they will need to check it for accurate alignment. To do this the design team have opted to manufacture the tail fin with embedded SMR targets so that they can simply use the tracker to align the tail, a job suited to the Leica Absolute Tracker AT402 due to its IP54 protection, meaning the hot and dusty climate will not be a problem.A true partnership
“We are pleased to be able to rely on Hexagon Metrology for many different tasks including onsite and offsite measurement, quick turnaround at short notice, training, long term equipment loan and expert metrology advice. The support from Hexagon Metrology staff has been first class”, said La Grue.Commenting on the contribution of Hexagon Metrology, BLOODHOUND SSC Project Director, Richard Noble said: “As we push the boundaries beyond 1000mph we need a partner that can match our ambition and provide us with mission critical measurement services using a range of leading-class equipment at the forefront of metrology. From the smallest detail on the car to the alignment of the major car components over its total 12.8-meter length, everything has to be right.”
Hexagon Metrology is proud to be a part of this amazing project and looks forward to working further with the team as the car completes assembly, goes through runway testing, breaks the sound barrier and then ultimately achieves a new world land speed record of 1000mph. We are pleased to be along for the ride.