Automatically calibrated
Daimler AG - Germany
Contact us
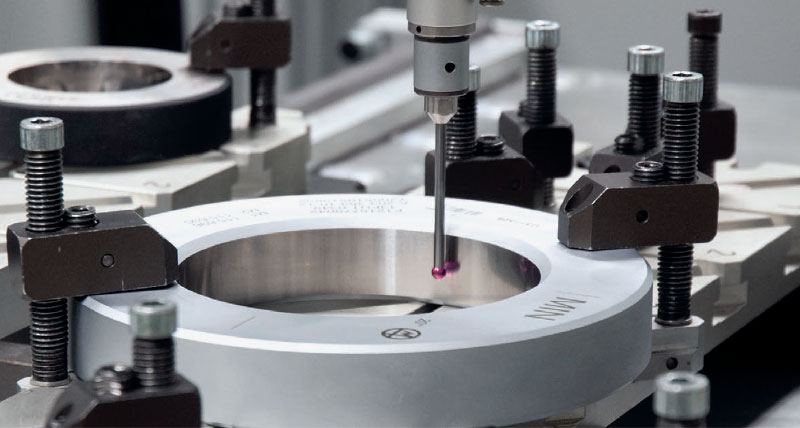
Jean-Charles de Borda was one of the personalities behind the introduction of the metric system in France at the end of the 18th Century. A century later, Carl Benz went for the world‘s first motorised „drive“ in Germany. At Daimler AG‘s main factory in Stuttgart- Untertürkheim, Germany, these two aspects of history come together. Here, gauges and setting masters are recalibrated to national standards with high-accuracy, efficient measuring systems from Hexagon Metrology PTS.
The gauge monitoring department has 60,000 pieces gauges and masters at their disposal on the Untertürkheim site. On behalf of the more than 500 departments (maintenance depots), the gauge measurement centre carries out regular calibration of all testing equipment, where dimensions are reset to national standards.
Gauge monitoring guarantees reliable, standard compliant and reproducible processes in the engine and sub-assembly departments. For the calibration of standard gauges, the team in Untertürkheim rely on an ingenious measuring and handling system from Hexagon Metrology PTS. This automated system is based on a climate-controlled measuring room, two Leitz brand high-accuracy measuring machines and the QUINDOS software package.
The demand for automated measurement processes for gauge calibration at Daimler arose in the late 1980s, and the company‘s cooperation with Hexagon Metrology also dates back to that time. "Our goal was to keep the influence of the operator to a minimum during gauge calibration. The process also had to remain reproducible. We managed to do this thanks to the concept from Hexagon Metrology PTS," said Andreas Keim, head of the gauge measurement centre.
The concept for automatic measurement program generation from characteristic data on the respective gauge has remained unchanged to this day. Thanks to its well thought out structure and flexibility, it is able to hold out in an environment of ever-changing standards and technologies. The centerpiece is a pallet storage system linked to storage and administration software from Hexagon Metrology PTS. This system enables pallet loading and gauge measurement to be carried out independently. Measurement is carried out unmanned, i.e. without an operator, during the night shift or even while the gauges are being set up or taken down. This increases the efficiency of the system. The data management is also fully automated. The software concept required here was implemented by Hexagon Metrology PTS using QUINDOS.
Precisely synchronised gauge calibration
The calibration process for gauges is synchronised precisely by storage and administration software.
In order for the pallets to be loaded efficiently as well, Hexagon Metrology developed a special clamping bar system for each gauge type. This system guarantees quick and precise positioning of gauges.
Each gauge is marked with an ID number which is the key to accessing it‘s master data (characteristic and operating data, dimensions, calibration results etc.). This data is archived in the electronic gauge monitoring system (ePÜS).
When a pallet is set up, the technician is supported by a special user interface. The ID number of the gauge and clamping location are reported to the system using a simple input dialog. The electronic gauge monitoring system information which has been archived for each gauge is called up and stored in a temporary QUINDOS database for the respective pallet. At the end of the set-up procedure, the pallet is transported to the pallet storage, where it waits to be measured. The set-up process and pallet transport are managed by the Software Automation Manager.
The gauge measurement centre team initiates the process just before the night shift begins. The Automation Manager then expertly takes over the shift, together with QUINDOS. Tha pallets are called out by QUINDOS according to the measurement list in temporary memory. The two Leitz measuring machines are loaded with the help of Hexagon Metrology‘s Automation Manager.
Upon arrival at the measuring point, QUINDOS generates all moving paths and standard-compliant touches in real time, for the entire pallet. The data is transmitted from the electronic gauge monitoring system to QUINDOS via an ASCII interface. The testing scope and accuracy, as well as the scope of logging, are read from the pallet-specific database. Dieter Wissel, project manager at Hexagon Metrology PTS: "The QUINDOS software is database-oriented.
As a result, it can guarantee certain functions that other software's cannot, e.g. QUINDOS can query dimensions and master data from another database and generate measurement programs."
The measurement programs which have been created in this way then run fully parameterised in the required order. The standard-compliant measurement results, which are defined as deviations from the norm, are transferred to a results file which can be read by the electronic gauge monitoring system.
Once the measurement is complete, the pallet is automatically transported back to pallet storage system. The measuring results are not released to the gauge management system until tear down, when the responsible technician has validated the stability and quality of the entire measuring process. When evaluating the test results, technicians have a customised QUINDOS statistics solution at their side.
After the plausibility check, the gauges go back to the appropriate department, who can access the electronic gauge monitoring system (ePÜS), and thus the calibration results, directly online.
The measuring system of the calibration centre is also subject to monitoring. A reference pallet (the so-called P15) is slipped in on a regular basis and when measuring conditions change. It represents the "measure of all things" calibration and is outfitted for monitoring measurement with representative DKD-calibrated master gauges.
Expanding automation
The demand for vehicles with the star has remained uninterrupted. The result has been an increase in the rise of testing equipment. Keim commented, "Over the years, we have continually optimised the system to enable us to calibrate economically.
Most recently, we replaced one of the two coordinate measuring machines with a faster Leitz PMM-C 12.10.7. Thanks to its base accuracy of 0.4 micrometres, we have also attained an improvement in comparison to the previous model in this regard," said Keim.
Thanks to the greater dynamics of the new machine, capacity was opened up and new approaches to calibration of the setting masters have been introduced. Until now, calibration of the setting masters for connecting rods, crankshafts, camshafts and gears occurred manually during the first and second shifts, without pallets or automatic loading. Times are changing, and the portfolio of automatic measurement needs to be expanded. In the first step, gear setting masters are to be fed to the Leitz PMM-C and calibrated automatically during the night shift.
"We would like to leave the night shift for the setting masters which can be manage with the current clamping technology and which are similar to each other. We‘re going to heavily expand in this area, which will make us economically unbeatable," explained Andreas Keim.
It comes down to the environment
The measuring concept at the Daimler gauge measurement centre has proven itself. In addition to modern climate-control technology, the system also features continuous temperature monitoring of the measurement environment. This enables temperature effects to be minimised. Keim continued, "With our automated system and the new Leitz PMM-C, we‘re optimally positioned for the coming years, if not decades."