Automatisch kalibriert
Daimler AG - Deutschland
Kontakt
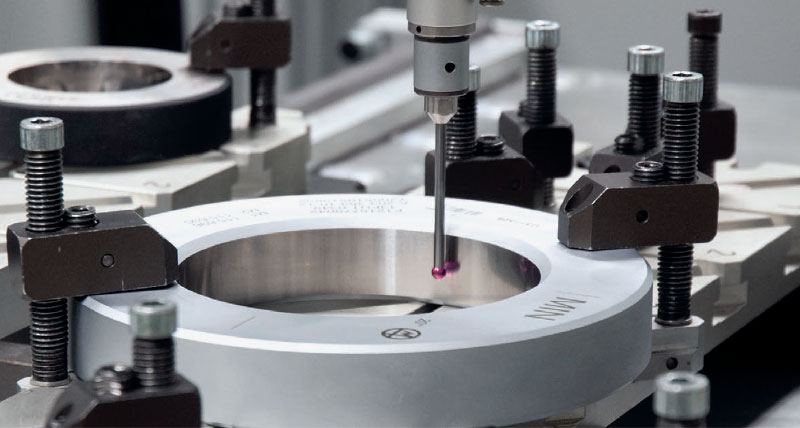
Jean-Charles de Borda ist einer der Persönlichkeiten, die hinter der Einführung des metrischen Systems Ende des 18. Jahrhunderts in Frankreich stehen. Ein Jahrhundert später unternahm Carl Benz in Deutschlanddie erste motorisierte „Spazierfahrt“ der Menschheit. Im Stammwerk der Daimler AG in Stuttgart-Untertürkheim vereint sich die Geschichte: Hier werden Lehren und Einstellmeister auf die nationalen Normale zurückgeführt. Mit hochgenauen und effizienten Messsystemen von Hexagon Metrology PTS.
60.000 Prüfmittel hat die Prüfmittelüberwachung am Standort Untertürkheim unter ihren Fittichen. Das Lehrenmesszentrum (LMZ) führt im Auftrag der über 500 Abteilungen (Meistereien) die regelmäßige Kalibrierung aller Prüfmittel durch, also die maßliche Rückführung auf nationale Normale.
Die begleitende Überwachung der Lehren ist die Garantie für zuverlässige, normenkonforme und reproduzierbare Prüfergebnisse im Motorenund Aggregate-Bau. Das Team in Untertürkheim setzt bei der Kalibrierung von Standardlehren auf ein ausgeklügeltes Mess- und Handlingssystem von Hexagon Metrology PTS. Das automatisierte System basiert auf einem klimatisierten Messraum (Güteklasse 1), zwei hochgenauen Messmaschinen der Marke Leitz und dem Softwarepaket QUINDOS.
Der Bedarf nach automatisierten Messprozessen für die Lehrenkalibrierung entstand bei Daimler bereits Ende der 80er Jahre. Bis dahin reicht auch die Zusammenarbeit mit Hexagon Metrology. „Unser Ziel war es, den Bedienereinfluss bei der Kalibrierung der Lehren so gering wie möglich zu halten. Zudem muss der Prozess reproduzierbar bleiben. Mit dem Konzept von Hexagon Metrology PTS haben wir das geschafft“, sagt Andreas Keim, Leiter des Lehrenmesszentrums.
Das Konzept für die automatische Messprogrammgenerierung aus charakteristischen Daten der jeweiligen Lehren ist bis zum heutigen Tag unverändert geblieben. Dem Wandel von Normen und Technologien hielt es dank seiner gut durchdachten Struktur und Flexibilität stand. Das Kernstück bildet ein Palettenspeicher, der mit einer Lager- und Administrationssoftware von Hexagon Metrology PTS verbunden ist. Mit dem System lassen sich Palettenbestückung und Lehrenmessung getrennt voneinander durchführen. Die Messung läuft mannlos - ohne Bediener - in der Nachtschicht oder auch parallel zum Auf- und Abrüsten der Prüfmittel. Das erhöht die Effizienz des Messbetriebs. Auch die Datenverwaltung erfolgt vollautomatisiert. Das dazu notwendige Softwarekonzept wurde von Hexagon Metrology PTS mit Hilfe von QUINDOS umgesetzt.
Lehrenkalibrierung genau getaktet
Der Kalibrierungsprozess für die Lehren wird über die Lager- und Administrationssoftware exakt getaktet.
Damit die Bestückung der Paletten ebenfalls effizient durchgeführt werden kann, hat Hexagon Metrology ein spezielles Spannleisten-System für jeden Lehrentyp entwickelt. Dieses System garantiert eine schnelle und exakte Positionierung der Prüflinge.
Jede Lehre ist mit einer Identnummer gekennzeichnet, über die der Zugriff auf ihre Stammdaten (Kenn- und Einsatzdaten, Baumaße, Kalibrierergebnisse, etc.) erfolgt. Sie sind im elektronischen Prüfmittelüberwachungssystem (ePÜS) archiviert.
Beim Rüsten der Palette wird der Techniker von einer speziellen Benutzerführung unterstützt. Identnummer der Lehre und Spannplatz werden über einen einfachen Eingabedialog dem System mitgeteilt. Die für jede Lehre hinterlegten ePÜS-Informationen werden beim Rüstprozess abgerufen und in eine temporäre QUINDOS Datenbank für die jeweilige Trägerpalette hinterlegt. Am Ende des Rüstvorgangs wird die Palette in das Pallettenlager transportiert und bis zu ihrer Messung zwischengelagert. Rüstprozess und Palettentransport werden von der Software Automation-Manager zuverlässig gemanagt.
Kurz vor Beginn der Nachtschicht startet das Team des LMZ den Prozess. Danach übernimmt der AutomationManager im Zusammenspiel mit QUINDOS routiniert die Schicht. QUINDOS ruft die Paletten gemäß der bestehenden Messliste aus dem Zwischenspeicher ab. Die Bestückung der beiden Leitz Messmaschinen erfolgt mit Hilfe des Automation-Managers von Hexagon Metrology.
Auf dem Messplatz angekommen, generiert QUINDOS für die komplette Bestückung der Palette sämtliche Verfahrwege und normgerechten Antastungen in Echtzeit. Hier kommen die vom ePÜS an QUINDOS über die ASCII-Schnittstelle übertragenen Daten zum Einsatz. Prüfumfang, Prüfschärfe und Umfang der Protokollierung werden aus der palettenspezifischen Datenbank gelesen. Dieter Wissel, Projektleiter bei Hexagon Metrology PTS: „QUINDOS ist eine datenbankbasierte Software. Daher kann sie bestimmte Funktionen gewährleisten, die andere Software nicht unterstützt, z.B. kann QUINDOS Baumaße und Stammdaten aus einer anderen Datenbank abfragen und daraus Messprogramme generieren.“
Die Messprogramme werden daraufhin erstellt und laufen in der angeforderten Reihenfolge komplett parametrisiert ab. Die normgerechten Messergebnisse, als Abweichungen zum Normal definiert, werden in eine für ePÜS lesbare Ergebnis-Datei übergeben.
Nach abgeschlossener Messung wird die Palette automatisch zurück in den Palettenspeicher transportiert. Erst beim Abrüsten, nachdem die verantwortlichen Prüfer die Stabilität und Qualität des gesamten Messsystems validiert haben, werden die Messergebnisse für das Prüfmittel-Managementsystem freigegeben. Bei der Beurteilung der Prüfergebnisse steht den Technikern eine angepasste Lösung von QUINDOS Statistik zur Seite.
Die Lehren gehen nach der Plausibilitätsprüfung zurück an die internen Auftraggeber, die online direkt auf das ePÜS und damit auf die protokollierten Kalibrierergebnisse zugreifen können.
Da das Messsystem des Kalibrierzentrums ebenfalls einer Prüfmittelüberwachung unterliegt, wird regelmässig sowie bei sich ändernden Messbedingungen, eine Referenzpalette – die so genannte P15 - eingeschleust. Sie stellt das ‚Maß aller Dinge‘ der Kalibrierung dar und ist für die Überwachungsmessung mit repräsentativen DKD-kalibrierten Meisterlehren bestückt.
Automatisierung ausweiten
Der Bedarf nach den Fahrzeugen mit dem Stern ist weiterhin ungebrochen. Ein steigendes Prüfmittelaufkommen ist die Folge. Keim dazu: „Über die Jahre haben wir das System auch immer wieder optimiert, um wirtschaftlich kalibrieren zu können.
Zuletzt haben wir eine der beiden Koordinatenmessmaschinen mit einer schnelleren Leitz PMM-C 12.10.7 ersetzt. Mit ihrer Grundgenauigkeit von 0,4 Mikrometern haben wir auch in dieser Hinsicht eine Verbesserung im Vergleich zum Vorgängermodell erreicht“, so Keim.
Durch die höhere Dynamik der neuen Maschine wurden Kapazitäten frei und es können neue Ansätze für die Kalibrierung der Einstellmeister eingebracht werden. Bislang erfolgt die Kalibrierung der Einstellmeister für Pleuel, Kurbelwellen, Nockenwellen und Verzahnungen in der ersten und zweiten Schicht manuell – ohne Paletten und ohne automatische Zuführung. Das wird sich ändern: Das Portfolio der automatischen Messung soll erweitert werden. Im ersten Schritt sollen Verzahnungseinstellmeister automatisch der Leitz PMM-C in der Nachtschicht zugeführt und kalibriert werden.
„Alle Einstellmeister, die wir von der Spanntechnik her bewältigen können und von denen es viele Gleichartige gibt, möchten wir in die Nacht packen. Das werden wir ganz stark ausbauen und sind damit dann wirtschaftlich unschlagbar“, führt Andreas Keim aus.
Auf die Umgebung kommt es an
Das Messkonzept im Lehrenmesszentrum bei Daimler hat sich bewährt. Neben moderner Klimatechnik ist die kontinuierliche Temperaturüberwachung der Messumgebung in das System integriert.