5 Axis edgecam and javelin pave the way for AI-Met's nuclear diversification
AI-Met - Wales
Contact us

Five-axis machining, and full traceability of parts, are combining to help an oil and gas specialist diversify into the nuclear market.
Al-Met’s sophisticated machine shop predominantly manufactures components for flow control valves, and assembling carbide parts onto Inconel or super duplex, thanks to a range of machine tools, including a recently-acquired 5-axis machining centre and 5-axis lathe, both programmed with Edgecam, from Vero Software.
The Javelin production control system, also part of the Vero suite, now ensures full traceability of those high precision components, as demanded by the two highly disciplined industries.
While the machine shop comprises both conventional and CNC lathes, mills and grinders, and a radial arm, it is their 5-axis capability that is helping the company take the next step.
Managing Director Phil Harmer says: “Our craftsmen have been comfortable for many years running parts through four or five operations, and it took a while for them to be fully confident with switching to the Mori Seiki MTX 2000 5-axis machining centre and doing everything in one set-up with Edgecam.
“But one particular job that used to take four or five days is now fully processed in just under two hours. It’s a massive time saving, and means we’ll be looking at increasing our 5-axis capability when we invest in further machinery.”
However, with over 2,000 parts on their system, and 500 Works Orders going through the shop floor each month, Al-Met knew that improvements were needed in their production control.
“As a certified material environment we have a lot of certification and drawing packs to go with our materials…and in some cases we’re actually using them on a manual tandem basis with our planning system, so with our old system there was always the risk of error. But we knew Javelin incorporates everything we need. We visited a number a local companies who were using it, and the Board of Directors agreed that Javelin was the way forward for us.”
The long-term strategy is that once Javelin is fully implemented at Al-Met’s 22,000sqft factory in Wales, it will also be installed at the other two manufacturing plants in the Group – at Glasgow and Rotherham.
“We’re working with up to 200 line items on the shop floor every day – mainly components for equipment used in controlling the flow of oil and gas after drilling – and each line has a different route card and different order of operations. Javelin fully controls that, and gives us full visibility of where every job is and what stage it’s at. It also shows how many hours each job takes, so we can capture all the costings as well.”
A major benefit for Operations Manager Craig Coomer is that Javelin has led to each user improving their productivity. “No matter which part of the system they’re on, it’s so quick and easy for them to drill up and down to find the information they need about everything from material origin to costings. Starting with the Sales Order screen they can drill through the Works Order right down to the subcontractor requirements, and back the other way to see where the order came from – even to the initial enquiry and quotation.”
Phil Harmer says Javelin contains all the functionality they need, both now and in the future with no bolt-ons required, which means it will grow with them as they expand and diversify. And he says it is extremely simple to use. “For example, it’s so easy to enter information into the Scheduling function and maintain it. Colour coding makes the whole system easily visible at a glance, and schedules can be readily moved around. If there’s an issue with a particular work centre – maybe because of a breakdown, or an operative is off ill – we can simply move a Works Order to another centre at the touch of a button, reset it and run Scheduling again.”
He feels Shop Floor Data Capture is at the heart of their Javelin operation. “We have around 30 people in the machine shop working on a number of machines at different times, and they scan each operation. We can then see exactly where each component is, who’s working on it, and what stage it’s at. It also shows the time and costs of a job, comparing it to the Sales Order and the original Purchase Order.”
Information is collected on around 35 different machining possibilities from 33 work stations. “And with anything up to 500 Works Orders going through the shop floor at any one time we need to be able to see at a glance where everything is. Some jobs may have a lead in time through the shop of a couple of weeks, and then remain static for two or three days. SFDC allows us to map where all these products are, and enables us to print the works tool list for that particular week.”
“There are so many opportunities to attach and link documents, drawings, certificates and results at the click of a key. All documentation aspects are linked to each PO and saved for future reference underneath the Sales Order and Purchase Order, which we couldn’t do with the old system. To have an efficient electronic data library of every detail we need from all jobs we’ve worked on is a huge benefit.”
Al-Met’s sophisticated machine shop predominantly manufactures components for flow control valves, and assembling carbide parts onto Inconel or super duplex, thanks to a range of machine tools, including a recently-acquired 5-axis machining centre and 5-axis lathe, both programmed with Edgecam, from Vero Software.
The Javelin production control system, also part of the Vero suite, now ensures full traceability of those high precision components, as demanded by the two highly disciplined industries.
While the machine shop comprises both conventional and CNC lathes, mills and grinders, and a radial arm, it is their 5-axis capability that is helping the company take the next step.
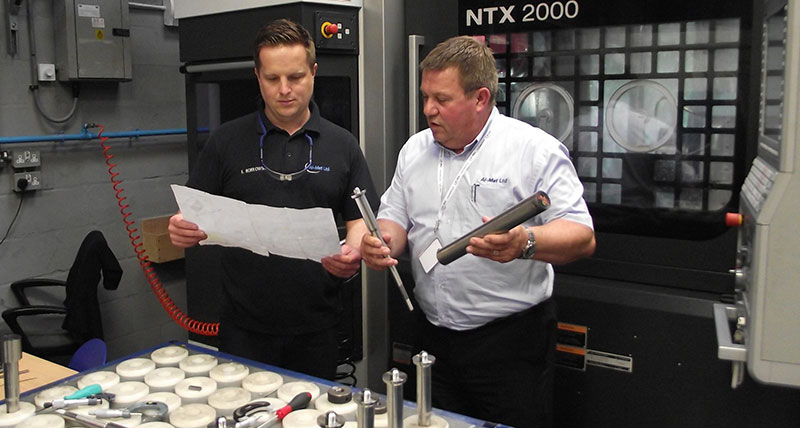
“But one particular job that used to take four or five days is now fully processed in just under two hours. It’s a massive time saving, and means we’ll be looking at increasing our 5-axis capability when we invest in further machinery.”
However, with over 2,000 parts on their system, and 500 Works Orders going through the shop floor each month, Al-Met knew that improvements were needed in their production control.
“As a certified material environment we have a lot of certification and drawing packs to go with our materials…and in some cases we’re actually using them on a manual tandem basis with our planning system, so with our old system there was always the risk of error. But we knew Javelin incorporates everything we need. We visited a number a local companies who were using it, and the Board of Directors agreed that Javelin was the way forward for us.”
The long-term strategy is that once Javelin is fully implemented at Al-Met’s 22,000sqft factory in Wales, it will also be installed at the other two manufacturing plants in the Group – at Glasgow and Rotherham.
“We’re working with up to 200 line items on the shop floor every day – mainly components for equipment used in controlling the flow of oil and gas after drilling – and each line has a different route card and different order of operations. Javelin fully controls that, and gives us full visibility of where every job is and what stage it’s at. It also shows how many hours each job takes, so we can capture all the costings as well.”
A major benefit for Operations Manager Craig Coomer is that Javelin has led to each user improving their productivity. “No matter which part of the system they’re on, it’s so quick and easy for them to drill up and down to find the information they need about everything from material origin to costings. Starting with the Sales Order screen they can drill through the Works Order right down to the subcontractor requirements, and back the other way to see where the order came from – even to the initial enquiry and quotation.”
Phil Harmer says Javelin contains all the functionality they need, both now and in the future with no bolt-ons required, which means it will grow with them as they expand and diversify. And he says it is extremely simple to use. “For example, it’s so easy to enter information into the Scheduling function and maintain it. Colour coding makes the whole system easily visible at a glance, and schedules can be readily moved around. If there’s an issue with a particular work centre – maybe because of a breakdown, or an operative is off ill – we can simply move a Works Order to another centre at the touch of a button, reset it and run Scheduling again.”
He feels Shop Floor Data Capture is at the heart of their Javelin operation. “We have around 30 people in the machine shop working on a number of machines at different times, and they scan each operation. We can then see exactly where each component is, who’s working on it, and what stage it’s at. It also shows the time and costs of a job, comparing it to the Sales Order and the original Purchase Order.”
Information is collected on around 35 different machining possibilities from 33 work stations. “And with anything up to 500 Works Orders going through the shop floor at any one time we need to be able to see at a glance where everything is. Some jobs may have a lead in time through the shop of a couple of weeks, and then remain static for two or three days. SFDC allows us to map where all these products are, and enables us to print the works tool list for that particular week.”
“There are so many opportunities to attach and link documents, drawings, certificates and results at the click of a key. All documentation aspects are linked to each PO and saved for future reference underneath the Sales Order and Purchase Order, which we couldn’t do with the old system. To have an efficient electronic data library of every detail we need from all jobs we’ve worked on is a huge benefit.”