Romax Spin
Part of the Romax toolset, Romax Spin offers advanced simulation of rolling element bearings as part of a full electro-mechanical system. With Spin, bearing designers and application engineers can get the independent insights they need to design, select, analyse and optimise bearings and predict their performance in a variety of applications.
Want to learn more?
Romax: Integrated powertrain simulation
Romax Spin is part of the Romax portfolio, an integrated toolset for ePowertrain engineering from concept exploration to virtual product sign-off.
The challenge
Whether selecting appropriate bearings for a concept design, designing a custom bearing for a specific application, or performing root cause analysis of a bearing failure, engineers need reliable prediction of bearing performance to make decisions. In addition, bearing suppliers and OEMs must be able to collaborate and share data with each other, while being independent and preserving valuable IP.
The solution
To get the insight required to design and select bearings for optimum performance and durability, bearing specialists require independent tools that provide access to a wide range of catalog bearings and enable advanced bearing simulation as part of a whole system. Romax software is founded on bearing expertise, and Romax Spin embodies the latest in world-leading bearing technology.
Overview
Romax Spin features detailed modelling of rolling bearings, fast and intuitive modelling of full drive systems, and advanced contact algorithms accurately capturing the non-linear behaviour of bearings. Users can calculate load and stress distributions, film thickness, standard ratings such as ISO 281 and ISO/TS 16281 and run dynamic simulations to study phenomena such as skidding and cage dynamics.
Rapid design
Build parametric models of any full drive system rapidly (in minutes), with an easy-to-use drag-and-drop 2D modelling interface and a live reflection of the model in a 3D visualisation. Models (starting with basic shaft, gear, bearing arrangements) can be created from scratch, imported from other Romax products, from CAD geometry, or via a number of other interfaces such as REXS.
Romax offers multi-fidelity component models across the full system:
- Model helical, spur and planetary gears as loading (ratio only), concept (teeth/module defined), detailed (macro/micro geometry)
- Model bearings as linear stiffnesses, rolling bearings from manufacturer catalogs or custom bearings with full details including micro-geometry profiles
- Import/create and condense FE components (or import from FEA), and model flexible FE bearings and gear blanks
Models can then be converted to MBD, CAD, CFD and other formats to save time on data re-entry.
Full system structural analysis: utilizing state of the art gear and bearing contact models for fast, parallelised static analysis of the full driveline, including deflections, loads, stresses and misalignments.
Combining state of the art gear and bearing contact models with the latest standards and stress-based life calculations, Romax offers fast, accurate prediction of component performance and system structural deformations. Romax’ holistic approach to system simulation considers the cumulative effect of the complex interactions between all components:
- shaft deflections
- gear misalignments and shifting contacts
- housing flexibility
- non-linear, load-dependent bearing stiffness
Analyses are appropriate to the model fidelity, ranging from fast approximations when evaluating design concepts to longer, more detailed analyses during virtual testing and design for manufacture. And crucially, Romax is able to provide this analysis very quickly, thanks to its hybrid approach of FE, analytical and empirical methods. The most computationally-efficient and accurate method is used for each part, and combined into a fully-coupled system simulation that provides the optimal blend of speed and accuracy, specifically designed for powertrain simulation.
Model highly detailed bearings, and analyse their performance within the context of a full transmission, considering all system loads, deflections, and misalignments to get unrivalled insight into their performance within a particular application.
- Design bearings for optimal system performance
- Model fully customisable, parametric bearings of all ball and roller types, including all external, internal dimensions and micro-geometry, for easy design space exploration
- Flexible model fidelity from single bearing to complex systems with flexible bearing rings and other structures
- Specify ring flexibility, clearance and press fits, preload, internal clearance, mounting distortion, temperatures and other assembly and operating properties
- Create, share, and use proprietary bearing databases protecting the IP of the creator
- Access the same shared bearing database within your organisation

Select and analyse bearings quickly, accurately and with confidence, to deliver the perfect bearing arrangement and accurate results for the application.
- Search up-to-date supplier catalogs directly and choose from more than 60,000 bearings from SKF, Schaeffler, Timken, JTEKT and Nachi
- Quickly and accurately predict element and raceway load and stress distribution, rib contact, edge stress, and contact truncation
- Enhanced bearing contact analysis featuring a coupled strip model accurately capturing roller edge stresses, end effects, material yield, rib contact, and truncation
- Evaluate optimum preload/clearance settings and how they are affected by thermal and structural conditions
- Accurate bearing stress including micro geometry means you get the most accurate results from ISO 281, ISO/TS16281 and other life prediction methods
- All calculations are based on a fully-coupled flexible system simulation optimised for speed and accuracy and underpinned by a sophisticated non-linear bearing stiffness model
- Obtain results directly from SKF’s cloud calculation service without leaving Romax Spin
With the rise of electric vehicles, bearings are operating under increasingly high speeds. Combined with low load conditions, this can lead to a dynamic phenomenon known as bearing skidding. In certain circumstances, bearing skidding can generate excessive frictional heat and high surface shear stress, and subsequently result in efficiency issues or premature bearing failure.
Romax Bearing Dynamics uses a novel approach based on transient time-domain analysis to predict the occurrence of skidding in electric-vehicle bearings in a matter of minutes. The model considers structural, thermal and fluid domains, including the influence of centrifugal and gyroscopic effects on rolling element dynamics, heat generated by the lubricant and associated temperature rise, and rheology and traction behaviour of the lubricating oil.
This application helps design engineers and bearing analysts to avoid damaging failures by designing more reliable bearings and selecting better lubricants, through unique insight of the underlying skidding mechanism and bearing dynamics.
Integrated ePowertrain design
Romax Spin is part of the Romax portfolio, which means you can use the same model in common file formats for multi-attribute, multi-fidelity, full system design, simulation and optimization. Our product range starts with Romax Concept, the perfect platform for early stage investigation and design space exploration, and extends through Romax Enduro, Romax Spectrum and Romax Energy, for analysis and optimization of efficiency, durability and NVH within a single model. Romax Spin adds world-leading bearing design and analysis capabilities, while Romax Evolve provides the perfect tool for electric machine designers looking to investigate the structural and NVH performance of their motor.
Beyond Romax, we have interfaces with dozens of other tools in the Hexagon portfolio and beyond. So, whether you are wanting to take your Romax powertrain into a full vehicle MBD model in Adams, or import electromagnetic loss data to be considered in the efficiency prediction of your electric machine, Romax will sit at the heart of your workflow.
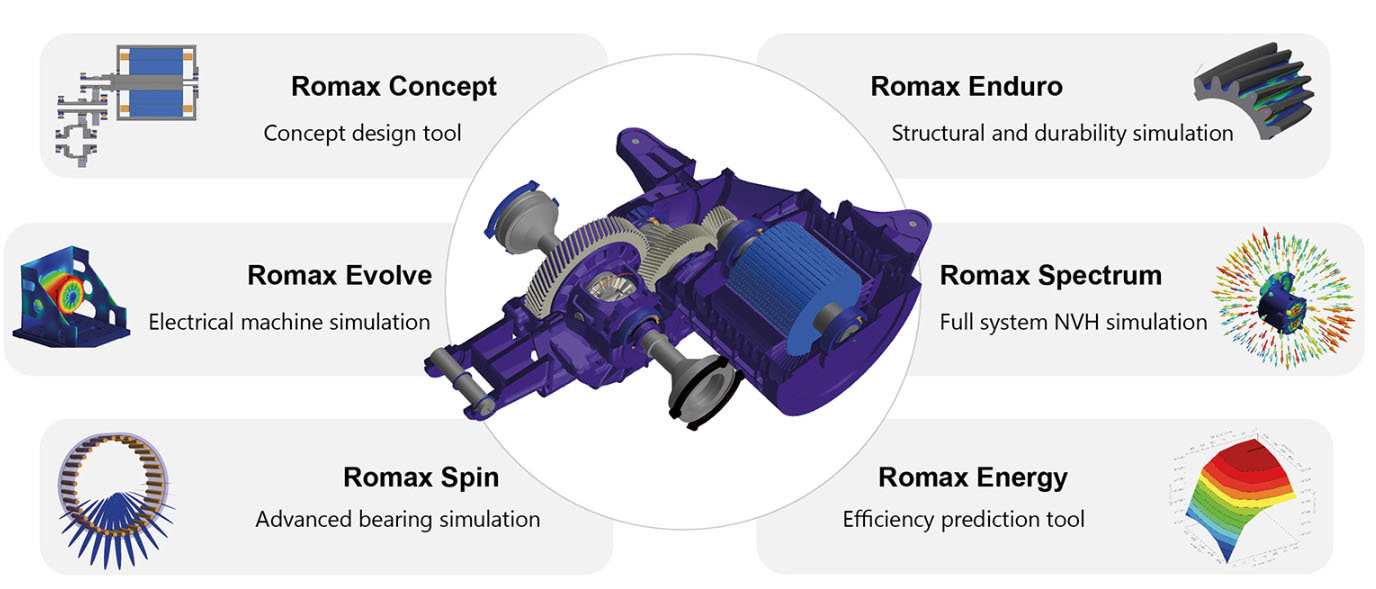
-
Case studies
-
Webinars
-
White papers