Paving the way to repeatability and accuracy
Triumph Group - USA
Contact us
Every gear manufacturing company welcomes growth, but it comes with challenges. They include investing in new equipment to meet capacity, hiring skilled operators if necessary and even finding space to locate the machine.
For Triumph Gear Systems-Macomb, these challenges were easily overcome when it needed a bigger coordinate measuring machine (CMM) to handle the larger parts it was beginning to make. The increased revenue from the new work justified the investment, the PC-DMIS software was user friendly for beginners and popular enough for there to be plenty of programmers available on the market. In addition, the purchase came at a time when the company was tripling its workspace, so space wasn’t a problem.
Triumph discovered a host of benefits, including saving 20-24 hours per assembly of the large helicopter component the CMM was primarily purchased to measure, the ability to take on new work with more complex assemblies than before, and the elimination of a backlog in its inspection department.
To facilitate recent growth, the company set about searching for a CMM that would meet all of its criteria, beginning with a much larger workspace and high-precision measurement capabilities for increasingly complex parts. The measurement solution also needed to be versatile so that it could verify a range of parts. While the existing CMM was capable of inspecting Triumph’s newest component—a large gear casing for the transmission of a helicopter rotor system—it clearly needed more travel in the X-axis of the machine. Historically, to measure the part, the operator would lay it on one side, measure it, flip it 180 degrees about the Y axis, then measure the other side, causing a quality control bottleneck. In an attempt to speed things up, the inspection team began duplicating programs and part setup, actually causing further delays in output while their CNC machines sat idle.
The solution came in the form of a GLOBAL Advantage 15.30.10 from Hexagon Manufacturing Intelligence. This advanced CMM package met Triumph’s requirements for accuracy and speed, and
it included features such as thermal compensation, advanced software and a high-performance analog scanning probe. This specific model has the highest-performing drives of the entire product line, with top acceleration to 4.3 meters per second squared, for maximum measuring throughput.
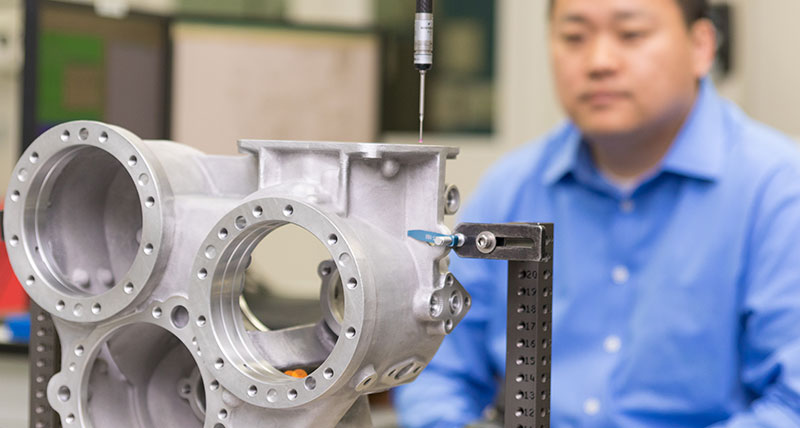
tight tolerance requirements of 0.001 inch. The complexity of the housings the company manufactures calls for more precise alignments due to the size increase of the gears and axles involved. He says that, of the roughly 500 different part numbers the company currently produces, about one third require quality inspection.
With less than 1 percent of parts returned to the metrology department, manufacturing intelligence is paving the way for precision manufacturing. “In order for us to maintain credibility with our customers, we need accuracy and repeatability. Efficiency is important, but not if it jeopardizes our quality,” Mr. Farr says. “We are very confident in the accuracy of our programs and our overall ability to inspect parts.”
Once the machine was installed, he began modifying the company’s existing program, reducing the handling time by roughly four hours per assembly. The helicopter gear casing no longer needed to be rotated, enabling faster setups, runtimes and change control times. The extra runtime also enabled the metrology department to keep up with internal demands. Overall, Triumph saved roughly 20-24 hours per assembly of its helicopter component with the new implementation.
No longer at maximum capacity, the company is able to take on additional work and more complex assemblies. “The new CMM and probe changers allow us to use multiple probe buildups while maintaining efficient runtimes,” Mr. Farr says. “We originally purchased the CMM to make inspection of the gear casing more efficient, but it also allowed us to run multiple jobs that required the larger inspection capability. In the past we had to schedule our larger jobs back-to-back. Today, we have doubled the overall capacity to inspect parts, which shows in our throughput.”
For Triumph Gear Systems-Macomb, these challenges were easily overcome when it needed a bigger coordinate measuring machine (CMM) to handle the larger parts it was beginning to make. The increased revenue from the new work justified the investment, the PC-DMIS software was user friendly for beginners and popular enough for there to be plenty of programmers available on the market. In addition, the purchase came at a time when the company was tripling its workspace, so space wasn’t a problem.
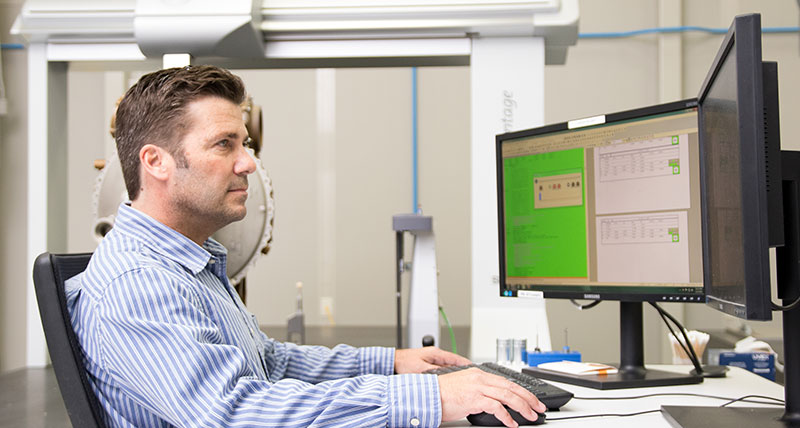
Measuring growth
Over the last 40 years, the Michigan-based company has built a solid reputation for its expertise in machining precision gears for the aerospace industry. In the past decade it has expanded the business to include much larger components such as housings and subassemblies. Today, Triumph Gear produces approximately 28,800 parts annually.To facilitate recent growth, the company set about searching for a CMM that would meet all of its criteria, beginning with a much larger workspace and high-precision measurement capabilities for increasingly complex parts. The measurement solution also needed to be versatile so that it could verify a range of parts. While the existing CMM was capable of inspecting Triumph’s newest component—a large gear casing for the transmission of a helicopter rotor system—it clearly needed more travel in the X-axis of the machine. Historically, to measure the part, the operator would lay it on one side, measure it, flip it 180 degrees about the Y axis, then measure the other side, causing a quality control bottleneck. In an attempt to speed things up, the inspection team began duplicating programs and part setup, actually causing further delays in output while their CNC machines sat idle.
The solution came in the form of a GLOBAL Advantage 15.30.10 from Hexagon Manufacturing Intelligence. This advanced CMM package met Triumph’s requirements for accuracy and speed, and
it included features such as thermal compensation, advanced software and a high-performance analog scanning probe. This specific model has the highest-performing drives of the entire product line, with top acceleration to 4.3 meters per second squared, for maximum measuring throughput.
Size matters
Robert Farr is the CMM manager at Triumph Gear. He points out that Triumph Gear’s need for accuracy and repeatability is essential to its success, notably because several parts have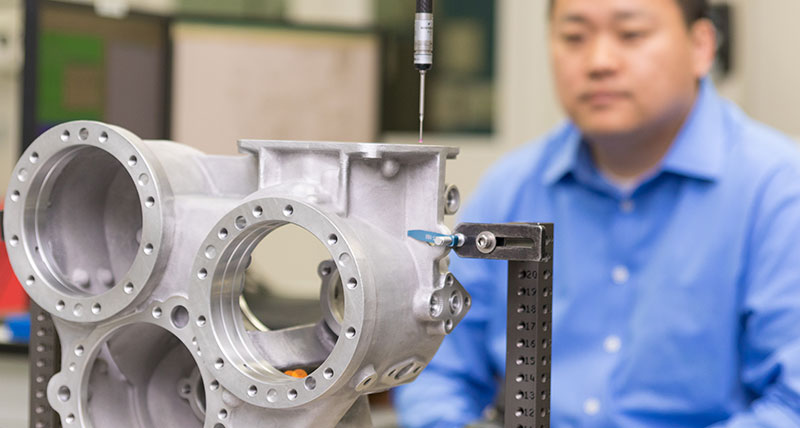
tight tolerance requirements of 0.001 inch. The complexity of the housings the company manufactures calls for more precise alignments due to the size increase of the gears and axles involved. He says that, of the roughly 500 different part numbers the company currently produces, about one third require quality inspection.
With less than 1 percent of parts returned to the metrology department, manufacturing intelligence is paving the way for precision manufacturing. “In order for us to maintain credibility with our customers, we need accuracy and repeatability. Efficiency is important, but not if it jeopardizes our quality,” Mr. Farr says. “We are very confident in the accuracy of our programs and our overall ability to inspect parts.”
Once the machine was installed, he began modifying the company’s existing program, reducing the handling time by roughly four hours per assembly. The helicopter gear casing no longer needed to be rotated, enabling faster setups, runtimes and change control times. The extra runtime also enabled the metrology department to keep up with internal demands. Overall, Triumph saved roughly 20-24 hours per assembly of its helicopter component with the new implementation.
No longer at maximum capacity, the company is able to take on additional work and more complex assemblies. “The new CMM and probe changers allow us to use multiple probe buildups while maintaining efficient runtimes,” Mr. Farr says. “We originally purchased the CMM to make inspection of the gear casing more efficient, but it also allowed us to run multiple jobs that required the larger inspection capability. In the past we had to schedule our larger jobs back-to-back. Today, we have doubled the overall capacity to inspect parts, which shows in our throughput.”