Volvo Bus Corporation standardises on MSC Nastran for all their structural analysis needs
By Anders Winkler, Director Solutions Marketing, Hexagon’s Manufacturing Intelligence division
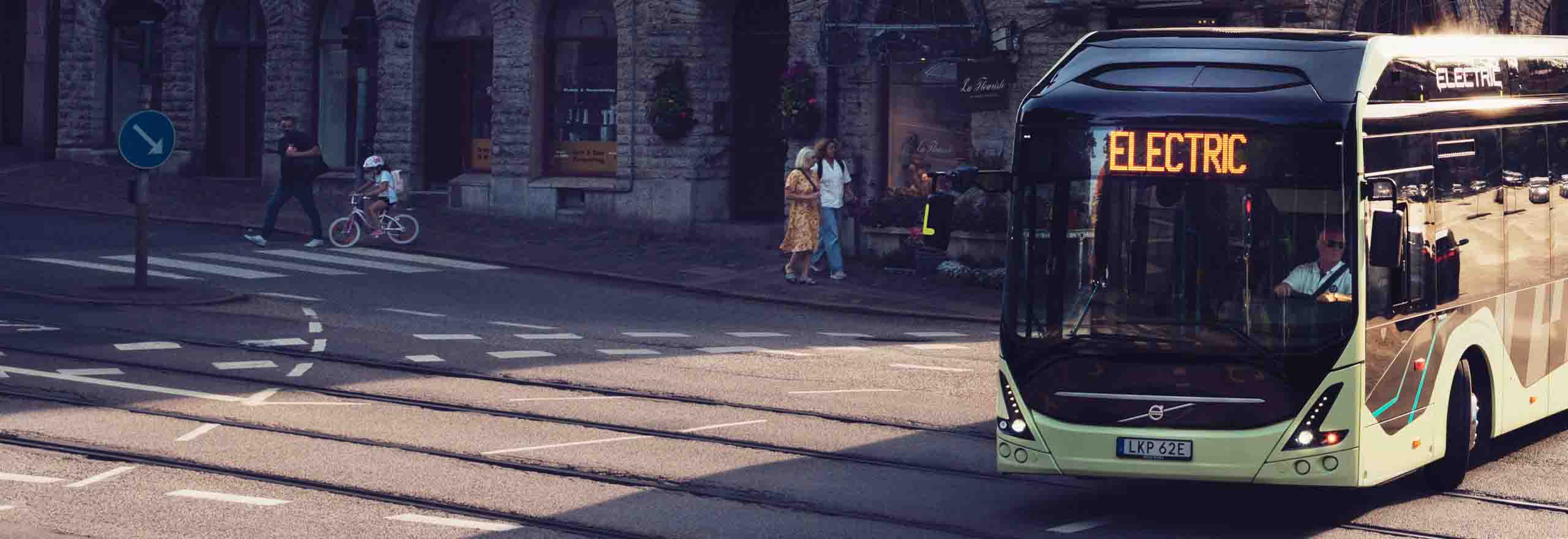
Engineering Reality 2024 volume 1
Accelerate Smart Manufacturing
Simulation is an essential tool in the design of modern buses, as it enables engineers to model and evaluate different strategies and scenarios before physically building a prototype. Engineers use simulation software and techniques to assess a vehicle’s performance under various conditions, such as high speeds, terrain, or weather conditions. This saves time and money by reducing the need for physical testing and redesign.
Simulation optimises the vehicle’s performance, such as improving fuel efficiency or reducing emissions. Engineers can find the best solutions for achieving their performance goals by modelling different scenarios and testing various design options.
Simulation can be used in various stages of the vehicle design process, from the initial concept phase to final testing before production. Using simulation in the initial concept phase informs engineers about high-level design decisions. Using simulation at the final verification stage validates our designs, predicts problems we may find in production and may even indicate the need for a higher level of CAE fidelity.
When asked what the most significant challenge was to overcome when using simulation in design, David responded: “Finding and accepting a sufficient level of detail. As a CAE engineer, diving deep into a problem is easy, modelling every little part to the finest resolution possible using the most advanced solver available.
However, we are constantly challenged with time and costs in our projects. We must be efficient in everything we do and incorporate the correct level of detail in our model using the appropriate solver for these complex problems.”
Figure 1. SOL 101 solution for the Bus BIW.
"Focusing on one solver enables us to concentrate our methodology on developing in-house processes and guidelines on more advanced simulations, exploring available features in MSC Nastran and extending the number of MSC Nastran solution sequences used by VBC. So yes, we definitely see the benefits of the decision."
Simulation with MSC Nastran
MSC Nastran is a collection of many simulation solution sequences that allow engineers to solve a large variety of problems. For example, the solution sequence SOL 101 is used to measure structures’ static stiffness. Bus design engineers would use it to measure the body’s overall stiffness and visualise portions of the Body in White (BIW) structure that might experience high compression or tension.
Bus design engineers would utilise SOL 400 to visualise the highly non-linear behaviour of components in contact, such as pre-tensioned bolts.
The comprehensive nature of the solution sequences in MSC Nastran allows Volvo Buses to select it as its standard structural solver. David continues: “Today, we have a model library almost exclusively consisting of models built for MSC Nastran. We perform simulations with various MSC Nastran solution sequences supporting multiple features such as durability, NVH and composite. Since we focus on one software environment, we have time to dive deeper into new features like CAE Fatigue/NEF and adopt new developments such as Multifrontal Parallel Direct Solver (MUMPS), which reduces the solution time by about 50%.”
Figure 2. SOL 400 solution for nonlinear contact analysis.
MSC Nastran is part of the Multiphysics Suite
When asked, “Has there been a surprising secondary/ proximal benefit from using Hexagon’s MSC Software or MSC Nastran?” David responded, “Maybe if we hadn’t used MSC Nastran to the extent that we do today, we might not have started the introduction of Hexagon’s Actran acoustic simulation into our process.”
Actran and MSC Nastran are both included in Hexagon’s Multiphysics Suite and interoperate, enabling structural analysis to extend to acoustical analysis for the prediction of noise levels in the interior and exterior of the bus.
About Volvo Bus Corporation
About Hexagon’s Multiphysics Suite
All physics simulations in one place
Create reliable and accurate digital twins with a complete suite of physics simulation software products, including structural simulation analysis solutions, fatigue, computational fluid dynamics, acoustic and NVH simulation and multiphysics co-simulation.