RADAN means ups, and no downs, for lift component manufacturing
Pawle & Company Ltd - UK
Contact us

RADAN CAD/CAM software ensures the design and production process of a lift component manufacturer only has ups…and no downs.
Pawle & Company Ltd began using RADAN at around the turn of the century, and it played a key role in doubling turnover to £1.25m after current owners Ray Ashby and his wife Joelle took over the company in 2011.
They temporarily switched back to using proprietary software to drive their Amada machine tools – an LCG 3015 3.5kw laser and AE 2510NTpunch press – but Ray Ashby says they returned to RADAN for the two main benefits it brings them: sheet utilisation and speed.
While their business has been built principally on supplying the lift trade with components such as doors and architraves, machine bed plates, car frames, landing stations, car operating panes and guide alignment tools, they have diversified into the construction industry and sheet metal fabrication.
“It’s absolutely critical that the parts we produce are high precision,” says Ray Ashby. “Our tolerances are normally within + or – 0.5 mm, but some are as tight as + or – 0.1 mm. With the rising cost of raw materials and customers demanding ever faster lead times, RADAN ensures perfectly punched and profiled parts are nested in the most efficient way to keep scrap to a minimum, and time savings of at least 30 percent.
“RADAN has reduced the time taken from inputting a DXF file to cutting metal, down to just minutes. And where we’ve got offcuts we can simply pull a program up and change the sheet size at the touch of a button.”
His team are able to modify programs easily – for instance turning a component through 90 degrees and retooling it.
Since buying the company from his late Father’s estate and sleeping business partner, Ray Ashby has invested heavily in CNC cutting machinery and an Amada MP250 automatic conveyor at the 10,000 square foot factory in Essex.
“It allows us to run 24 hours a day, seven days a week when we need to, and RADAN gives us the best nests for each type of material and thickness.” On regular, repeat work, RADAN utilises as much of the sheet as possible by creating nests just for the one job. For example, if they are making CCTV boxes there will be one program for the boxes and one for the lids – with a separate nest for each.
The company, which has 18 employees, also operates as a jobshop, and finds RADAN's Project Nesting invaluable in nesting different components from different customers on the same sheet.
Draughtsman and CAD Technician Roy Haynes takes customer drawings, or carries out his own designs in SolidWorks, then flattens them and processes them into RADAN using the software’s powerful DXF and DWX translators. “Time is my biggest challenge – we’re always looking at ways of reducing the time taken from getting the job to the machine, produced, and shipped.”
And he says RADAN ensures substantial time savings at the front end, enabling him to pass the files on to CNC Programmer/Operator Darren Callander as soon as the design has been approved.
Darren says: “Once I receive the files I import them into RADAN – and if it’s already a RADAN file I go straight to the nesting function to create the programs.” Which is a simple task, as the files show him the best way to utilise the sheet, how the program cuts, and the cutting order.
“It’s easy to get maximum sheet utilisation with the way it assembles the parts on the nest. And we can manually input our own sizes, too, to use offcuts.”
With Roy and Darren working together closely, RADAN's simple process of manipulating any design and program means the procedure for switching a job from punch to laser and vice versa when necessary, is seamless and quick. “We just pull up the symbol, retool it as a laser, and nest it. It really is that quick.”
In conclusion, Ray Ashby says: “Whether we’re making lift components in 1.0 – 20 mm mild steel, or 1.0 – 8.0 mm aluminium parts for the construction industry, RADAN is an integral part of our arsenal of design and manufacturing CAD/CAM tools, meaning that we can offer our customers extremely competitive prices.”
Pawle & Company Ltd began using RADAN at around the turn of the century, and it played a key role in doubling turnover to £1.25m after current owners Ray Ashby and his wife Joelle took over the company in 2011.
They temporarily switched back to using proprietary software to drive their Amada machine tools – an LCG 3015 3.5kw laser and AE 2510NTpunch press – but Ray Ashby says they returned to RADAN for the two main benefits it brings them: sheet utilisation and speed.
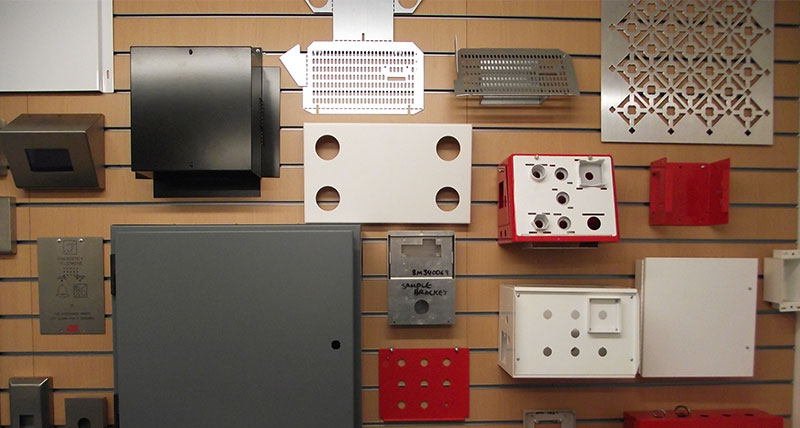
“It’s absolutely critical that the parts we produce are high precision,” says Ray Ashby. “Our tolerances are normally within + or – 0.5 mm, but some are as tight as + or – 0.1 mm. With the rising cost of raw materials and customers demanding ever faster lead times, RADAN ensures perfectly punched and profiled parts are nested in the most efficient way to keep scrap to a minimum, and time savings of at least 30 percent.
“RADAN has reduced the time taken from inputting a DXF file to cutting metal, down to just minutes. And where we’ve got offcuts we can simply pull a program up and change the sheet size at the touch of a button.”
His team are able to modify programs easily – for instance turning a component through 90 degrees and retooling it.
Since buying the company from his late Father’s estate and sleeping business partner, Ray Ashby has invested heavily in CNC cutting machinery and an Amada MP250 automatic conveyor at the 10,000 square foot factory in Essex.
“It allows us to run 24 hours a day, seven days a week when we need to, and RADAN gives us the best nests for each type of material and thickness.” On regular, repeat work, RADAN utilises as much of the sheet as possible by creating nests just for the one job. For example, if they are making CCTV boxes there will be one program for the boxes and one for the lids – with a separate nest for each.
The company, which has 18 employees, also operates as a jobshop, and finds RADAN's Project Nesting invaluable in nesting different components from different customers on the same sheet.
Draughtsman and CAD Technician Roy Haynes takes customer drawings, or carries out his own designs in SolidWorks, then flattens them and processes them into RADAN using the software’s powerful DXF and DWX translators. “Time is my biggest challenge – we’re always looking at ways of reducing the time taken from getting the job to the machine, produced, and shipped.”
And he says RADAN ensures substantial time savings at the front end, enabling him to pass the files on to CNC Programmer/Operator Darren Callander as soon as the design has been approved.
Darren says: “Once I receive the files I import them into RADAN – and if it’s already a RADAN file I go straight to the nesting function to create the programs.” Which is a simple task, as the files show him the best way to utilise the sheet, how the program cuts, and the cutting order.
“It’s easy to get maximum sheet utilisation with the way it assembles the parts on the nest. And we can manually input our own sizes, too, to use offcuts.”
With Roy and Darren working together closely, RADAN's simple process of manipulating any design and program means the procedure for switching a job from punch to laser and vice versa when necessary, is seamless and quick. “We just pull up the symbol, retool it as a laser, and nest it. It really is that quick.”
In conclusion, Ray Ashby says: “Whether we’re making lift components in 1.0 – 20 mm mild steel, or 1.0 – 8.0 mm aluminium parts for the construction industry, RADAN is an integral part of our arsenal of design and manufacturing CAD/CAM tools, meaning that we can offer our customers extremely competitive prices.”