Matthew Marsden's error-free and speedy process with CABINET VISION
Matthew Marsden - UK
Contact us

“CABINET VISION speeds up our process and has completely eliminated errors from it.”
Those are the words of Matthew Marsden, whose company, Matthew Marsden Furniture, only began using the software in 2016, and quickly became advanced users at a high level. Along with manufacturing quality kitchens, bedrooms and studies, they are also known for boot rooms, gun rooms and wine rooms, working directly with end-users, and one trade outlet.
While they have supplied kitchens all over the world, including Moscow, Switzerland, Germany and Spain, most customers are close to their Lancashire base.
Everything is designed in Cabinet Vision Solid Ultimate from Vero Software, and the NC code sent to an Andi Stratos CNC router with its Screen-To-Machine module. “We can be totally confident that what we design in Cabinet Vision will be faithfully reproduced when it’s cut. As long as we draw it correctly, the finished component is going to be perfect.”
And he says they have never found anything that cannot be drawn up in the software. “For example, we’ve done complex circular butcher’s blocks with revolving shelves and curved doors with no difficulty. And it’s ideal for showing customers exactly what their finished room will look like.”
That latter point was the main reason he decided to invest in Cabinet Vision. “Previously we drew up our designs in another CAD system, which was only 2D and our customers struggled to picture how it would look in their homes. We often needed to go through several redraws with them, and even then it was still hard for them to visualise it from the 2D.
“But now, with Cabinet Vision’s full colour 3D renders they can see realistically what it will look like in situ straight away, and saves us having to do numerous redraws.” As well as showing customers the entire layout on a giant TV screen in the showroom, they also highlight specific cabinets and units. “We can pick out a large pantry cabinet, spin it round to show it from all angles, and adapt it there and then with the number of shelves and drawers the customer wants.”
Any engraving that is required – including words on drawer fronts – is incorporated through another Vero product, Alphacam.
Once Matthew and a colleague have created all the panels and completed the full design, the file is sent to Project Manager Steven Millington, who double checks all the drawings and then creates the cutting lists…which is another benefit of using Cabinet Vision.
“Previously the cutting lists and nesting were done manually, which was time consuming and there was a lot of scope for error. With nesting, I’d draw an 8 x 4 sheet and individually import each panel. Then the completed panel would be imported into another CAM system for the toolpaths and drill holes to be added, and finally sent to the machine.
“The whole process used to take days. Now, it’s just hours. I create the cutting lists and include any additional information that the shopfloor may need if it’s a particularly complex cabinet, and print off the drawings, passing everything to the workshop. Then I send the NC code to the router. So it speeds up our workflow considerably, while eliminating errors.”
As well as using the Cabinet Vision support portal occasionally, Steven finds the customer forums can normally answer any queries. In addition, he says YouTube videos are a good source of information showing various ways of achieving what he needs to do.
Matthew Marsden says it is vital that their components are high precision so everything fits perfectly on site. “The cabinets, drawer boxes, doors, frames and shelves are all cut at the same time,
so we can’t afford any hiccups during final assembly.
“Spending an additional fifteen minutes at the design stage making sure each cabinet is perfect may save an hour or more further down the process. We have total confidence that the Cabinet Vision designs will be accurately reproduced in the NC code and cut exactly as required.
“It means that once we’ve finished designing a cabinet we can forget about it, knowing full details will be in the cutting list, and that the shopfloor drawings will show the workshop manager and machine operator everything they need to know.”
The Marsden family have been running businesses, including a DIY store, on the site now housing the showroom, offices and workshop, in Leyland, Preston, since 1929. “My grandfather started as a builder, then my father took over, and I started working for him as a joiner,” explains Matthew. “I really enjoyed doing the kitchens and staircases, and when I was 21 I took a loan from my father to put some kitchen displays in the shop here, and my business grew from that, now employing 14 people.”
Those are the words of Matthew Marsden, whose company, Matthew Marsden Furniture, only began using the software in 2016, and quickly became advanced users at a high level. Along with manufacturing quality kitchens, bedrooms and studies, they are also known for boot rooms, gun rooms and wine rooms, working directly with end-users, and one trade outlet.
While they have supplied kitchens all over the world, including Moscow, Switzerland, Germany and Spain, most customers are close to their Lancashire base.

And he says they have never found anything that cannot be drawn up in the software. “For example, we’ve done complex circular butcher’s blocks with revolving shelves and curved doors with no difficulty. And it’s ideal for showing customers exactly what their finished room will look like.”
That latter point was the main reason he decided to invest in Cabinet Vision. “Previously we drew up our designs in another CAD system, which was only 2D and our customers struggled to picture how it would look in their homes. We often needed to go through several redraws with them, and even then it was still hard for them to visualise it from the 2D.
“But now, with Cabinet Vision’s full colour 3D renders they can see realistically what it will look like in situ straight away, and saves us having to do numerous redraws.” As well as showing customers the entire layout on a giant TV screen in the showroom, they also highlight specific cabinets and units. “We can pick out a large pantry cabinet, spin it round to show it from all angles, and adapt it there and then with the number of shelves and drawers the customer wants.”
Any engraving that is required – including words on drawer fronts – is incorporated through another Vero product, Alphacam.
Once Matthew and a colleague have created all the panels and completed the full design, the file is sent to Project Manager Steven Millington, who double checks all the drawings and then creates the cutting lists…which is another benefit of using Cabinet Vision.
“Previously the cutting lists and nesting were done manually, which was time consuming and there was a lot of scope for error. With nesting, I’d draw an 8 x 4 sheet and individually import each panel. Then the completed panel would be imported into another CAM system for the toolpaths and drill holes to be added, and finally sent to the machine.
“The whole process used to take days. Now, it’s just hours. I create the cutting lists and include any additional information that the shopfloor may need if it’s a particularly complex cabinet, and print off the drawings, passing everything to the workshop. Then I send the NC code to the router. So it speeds up our workflow considerably, while eliminating errors.”
As well as using the Cabinet Vision support portal occasionally, Steven finds the customer forums can normally answer any queries. In addition, he says YouTube videos are a good source of information showing various ways of achieving what he needs to do.
Matthew Marsden says it is vital that their components are high precision so everything fits perfectly on site. “The cabinets, drawer boxes, doors, frames and shelves are all cut at the same time,
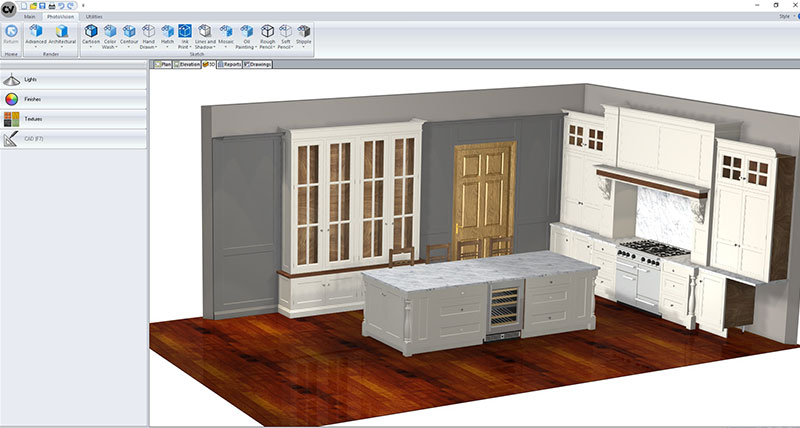
“Spending an additional fifteen minutes at the design stage making sure each cabinet is perfect may save an hour or more further down the process. We have total confidence that the Cabinet Vision designs will be accurately reproduced in the NC code and cut exactly as required.
“It means that once we’ve finished designing a cabinet we can forget about it, knowing full details will be in the cutting list, and that the shopfloor drawings will show the workshop manager and machine operator everything they need to know.”
The Marsden family have been running businesses, including a DIY store, on the site now housing the showroom, offices and workshop, in Leyland, Preston, since 1929. “My grandfather started as a builder, then my father took over, and I started working for him as a joiner,” explains Matthew. “I really enjoyed doing the kitchens and staircases, and when I was 21 I took a loan from my father to put some kitchen displays in the shop here, and my business grew from that, now employing 14 people.”