Logan Machine Company
Sixty-year-old job shop Logan Machine Company is a turn-key systems specialist that has expanded capabilities and gained competitiveness with EDGECAM
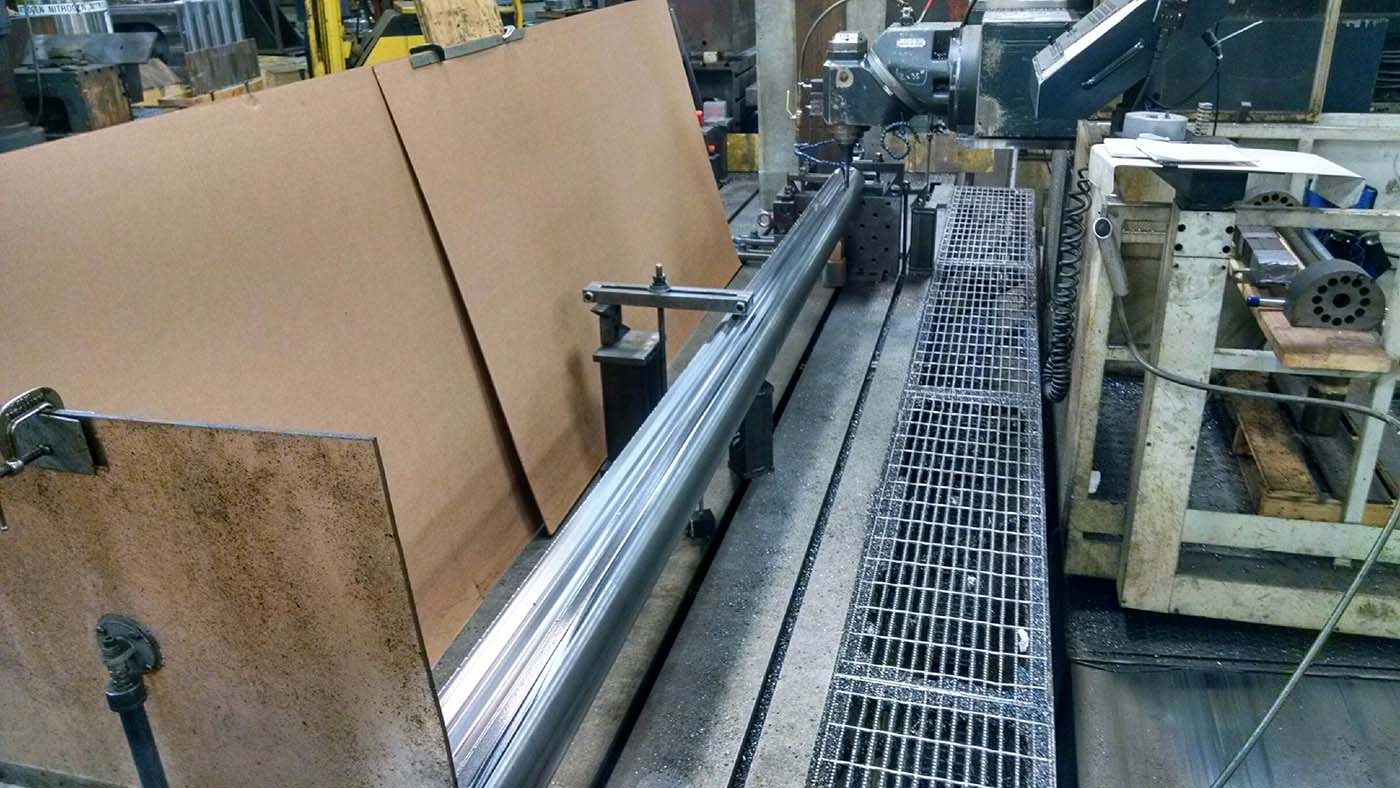
Succeeding as a job shop requires a combination of diverse machining capabilities and a willingness to take on new challenges, which is exactly how turn-key manufacturer Logan Machine Company has beaten the competition for 60 years.
Based in Akron, Ohio, Logan Machine Company is a family business with a long history of continuous growth, customer diversification, and fearless innovation. Today, the business serves a laundry list of industries, including aerospace, automotive, consumer, and defense. Among the products made using machinery built by Logan are tires, ladders, and tooling for rocket manufacturers.
“As a job shop, we pretty much try to do whatever our equipment allows us to do,” says CNC Area Supervisor Jeff Bohaychyck, who has been with Logan Machine Company for 40 years.
“Our forte is building all kinds of machines from start to finish. We do very well with weldments, frame weldments, conveyors, PLCs (programmable logic controllers), and all the mechanisms that make something run.”
As a long-time employee, Bohaychyck has taken part in the company’s process evolution from paper-tape machines to CNC equipment, and has seen parts become ever more complex even as lead times shrink. “Machining has gotten a lot more competitive in the US.,” he says. “The manufacturers that are still surviving are fiercely competing against each other.”
To stay ahead of the competition, Logan Machine expanded its machining capabilities by implementing the EDGECAM computer-aided-manufacturing (CAM) solution, by Vero Software, in 1998.

“We got an opportunity to run parts for an airplane and didn’t have the ability to generate the complex toolpath for it,” Bohaychyck says of switching to EDGECAM from the company’s former, less robust, system. “We got EDGECAM specifically to open our shop to new customers and to start getting regular work from them. We needed software that was sophisticated enough to do what we needed it to do, and this just enables you to do so much more.”
Today, the shop — which employs a staff of about 60 — machines in up to four axes with rotary capabilities, and each CNC machine tool is equipped with a tool changer for even greater efficiency.

While an in-house engineering team handles the company’s design work, Bohaychyck is adept at handling everything from solid models to paper drawings. To do so, he takes advantage of EDGECAM’s ability to seamlessly load the native computer-aided-design (CAD) files without translation, which ensures that CAD data remains intact.
Bohaychyck has seen EDGECAM evolve throughout two decades and has continuously applied new technologies as they’ve become available. Among the newer technologies he utilizes is the EDGECAM Workflow interface, which takes programmers through a five-step process that covers job requirements from start to finish in a realistic manufacturing environment. Designed to assist users with organization and job planning to quickly produce G-code, Workflow covers files, set-up, part features, machining strategies, and code generation.

Because users can choose to operate EDGECAM in one of three modes — manual, semi-automatic and fully automatic, all of which can be used interchangeably — Bohaychyck is able to customize programming methods to suit personal preferences and the needs of the job. For instance, he typically identifies part features manually, but utilizes the system’s automatic feature finder for parts that have multiple holes.
“If I’ve got a million holes, I’ll let EDGECAM do the whole thing automatically,” he says. “It also lets me edit automated processes, so it is flexible in terms of letting me do things the way that I want to do them.”
When it comes to making chips, Bohaychyck chooses from among several of the system’s custom machining cycles, selecting strategies that suit the challenges and complexities specific to the job. For rapid-material removal, Bohaychyck sometimes opts for a specialized gouge-protected roughing cycle that uses a concentric or lacing pattern on 2D geometry. The cycle can be applied to surfaces, solids and STL models.
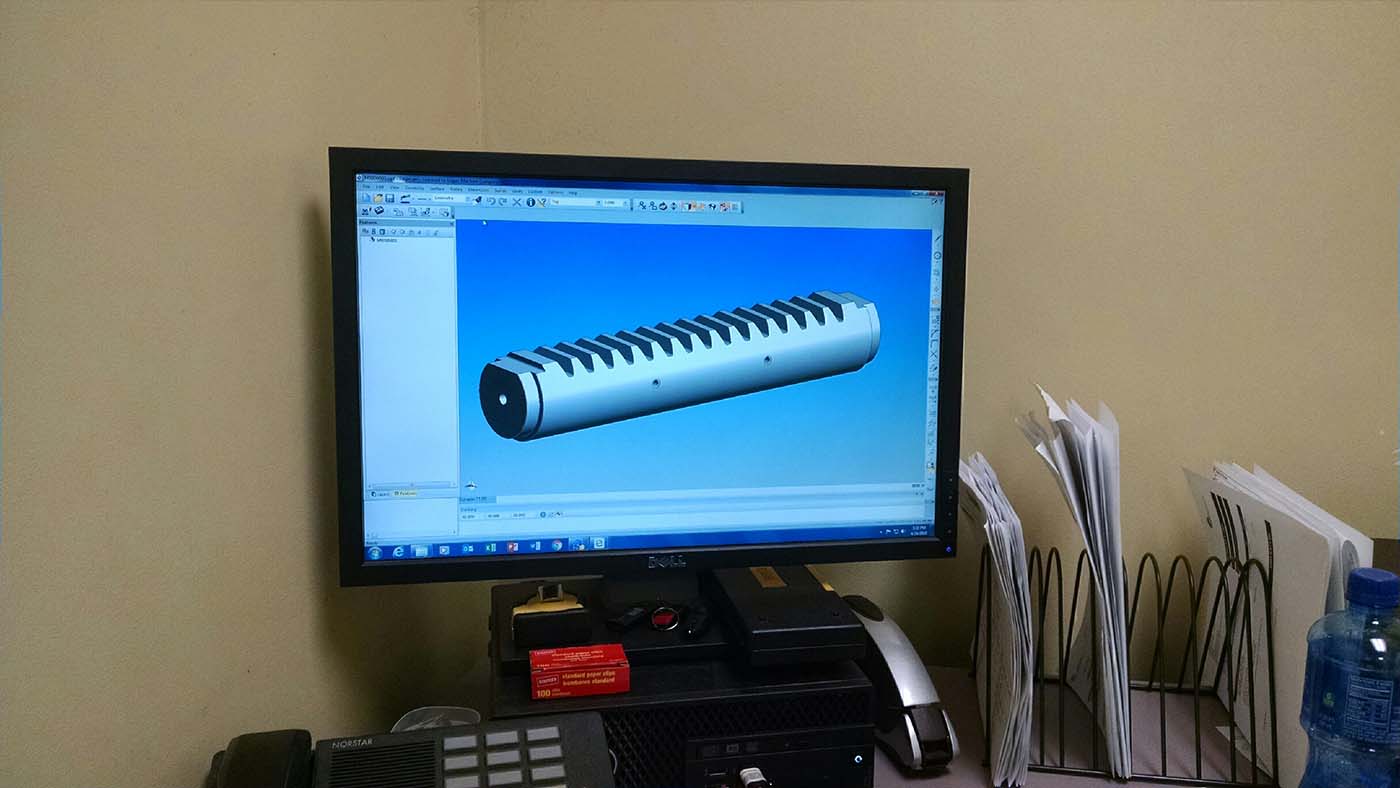
He also uses the EDGECAM Profile cycle to finish surfaces in a series of XY profiles down the Z-axis. This cycle can also be applied to surfaces, solids and STL models, and can be used to machine round wireframe profiles. “I use Profile for finishing after I’ve roughed the part. It will profile the surface and not all the roughing passes to get the material out.”
Bohaychyck takes advantage of the Constant Cusp finishing cycle to produce toolpath that can be defined from a curve or a boundary. The Constant Cusp cycle will collapse from the selected boundary or outer edge of selected surfaces, which generates an even surface finish over the entire model.

By consistently using the software’s customizable automation tools, Bohaychyck is able to “save hours” of programming time while maintaining company standards and best practices. Saving job processes allows him to reapply processes for previous jobs to new identical or similar jobs, after which he can edit new jobs as needed. Saving processes is especially helpful for programming families of parts.
“If you have a family of parts, you can bring a part into EDGECAM and maybe you’ll have two models where the holes are the same and the geometry is very close,” Bohaychyck explains. “You can save the process as another part and repost it in just a few minutes instead of taking a new part and starting from scratch. This is one way that you can really cut your time down.”
He also uses the system’s customizable tooling library, which helps him to quickly select available tooling and to rapidly define tools as they need to be added. “Being able to define tools on the fly saves so much time.”
At Logan Machine, the investment in EDGECAM helped the company to expand its capabilities and to ultimately gain a broader and more diverse customer base. “EDGECAM enables you to do things that you could never do without it. It has just opened up more opportunities and helps us to be successful in a very competitive business.”
About
Name: Logan Machine CompanyBusiness: Turn-key manufacturing solutions for a wide range of industries
Website: loganmachine.com
Benefits Achieved
- Greater ability to diversify and attract new business
- Customization of programming methods, including levels of automation
- Ability to generate complex G-code
- The use of specialized machining cycles designed to address specific challenges