Integrating automated non-contact 3D inspection for welded structures
By Rodrigo Alfaia, Associate Director Laser Tracker, Hexagon’s Manufacturing Intelligence division
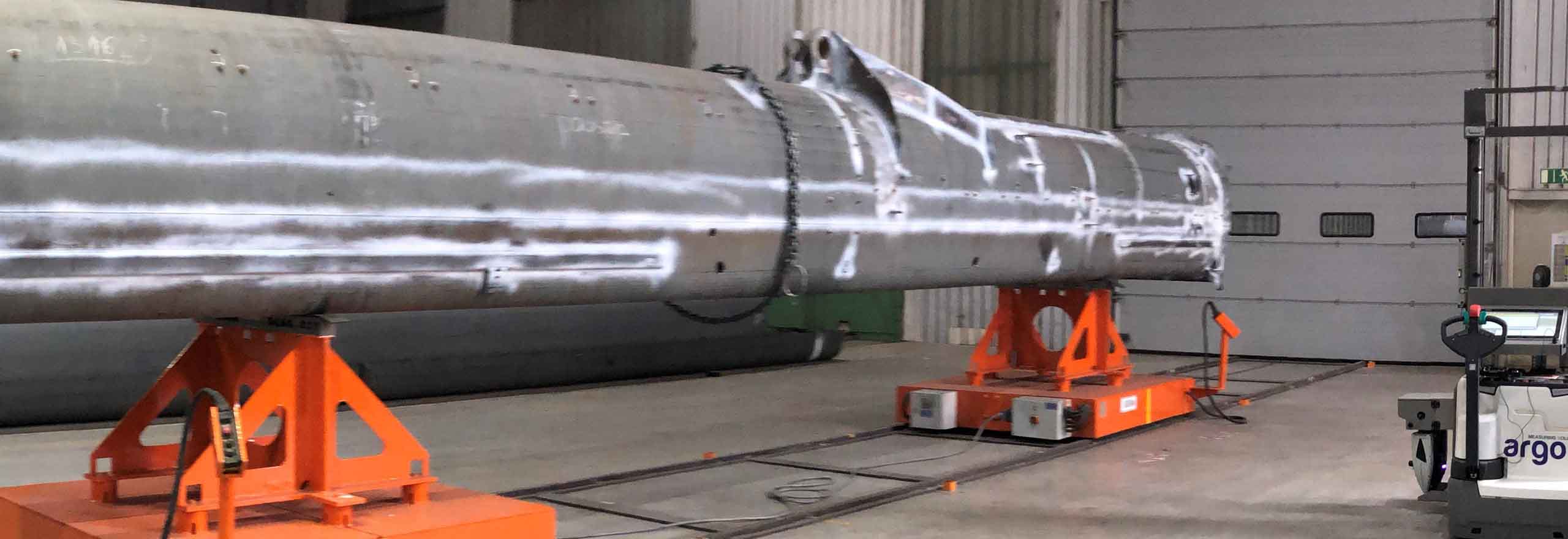
Engineering Reality 2024 volume 1
Accelerate Smart Manufacturing
To improve production efficiency and drive down costs, the Vlassenroot Group invested in a shop-floor measurement solution based on direct scanning laser tracker technology from Hexagon.
With production sites in Belgium, Germany and Poland, the Vlassenroot Group is a leading supplier of customised complex steel structures and components. Their competencies lie in cutting and bending, as well as in the welding, machining, assembly and painting of advanced steel components for various industries such as lifting, rail and energy. With their origins mainly in supplying bent half shells to the crane industry, the family-owned business has grown to supply completely welded telescopic booms, chassis and turntables according to customer needs.
A particular area in which Vlassenroot faces major challenges is in the production of telescopic booms. Booms with a length Volume XVII – Issue 1 | Manufacturing Intelligence hexagon.com | 65 of up to 16 metres need to seamlessly fit into each other to meet the high standards of crane manufacturers in terms of the telescope’s elastic behaviour and load-bearing capacity.
To increase production throughput and reduce tact times, Vlassenroot’s German facility engaged ARGON Measuring Solutions to work out a reliable 3D inspection solution that can be part and parcel of the production process.
The solution proposed by ARGON is built around the Leica Absolute Tracker ATS600 direct scanning laser tracker from Hexagon’s Manufacturing Intelligence division, mounted on a measurement trolley, a standard electric pallet stacker enhanced for metrology purposes.
Boom production poses major challenges
The production of long telescopic booms for the mobile crane industry passes through various stages. The main elements are the half shells of steel coming from the Belgian facility in Brussels that get joined by hybrid welding into a single tube that constitutes one of the elements of the telescopic boom.
“Despite the fact that our welders are experts in their job, we wanted to reinforce the inspection routine and make it less dependent on each individual operator’s accuracy,” explains Philippe Dudzik, Industrial Director at Vlassenroot. Details that need to be checked with accuracy include the quality of the weld seam and the influence of the induced heat on material deformations.
“We don’t understand the effects of these material deformations in detail yet, by which I mean, which parameters in the previous production steps influence the level of deformation,” explains Dudzik. “The digital data we now receive from the ATS600 across several production steps allows us to define important parameters and counteract deformations on the boom.”
Figure 1. The production of large steel components causes dust, dirt and vibrations, which means equipment in the Vlassenroot facility needs to be able to withstand a harsh production environment.
“This whole process requires a lot of time and experience from our employee,” says Dudzik. “Installing a quality process with well-defined quality gates will detect booms that do not need to go through the straightening process. For those that do, we will know immediately where to correct them. This will save us time and money. And by measuring faster and more reliably, we can understand the root causes of the deviations better and thus better anticipate and avoid them.”
Installing quality gates for efficiency gains
Together with ARGON, Vlassenroot established several quality gates during the production process. Based on this, ARGON developed a turnkey solution for Vlassenroot, proposing a system with a direct scanning Leica Absolute Tracker ATS600 mounted on an ARGON measurement trolley.
Figure 2. In the past, checking deviations on the boom was a purely manual
task — using gauges and callipers, an experienced employee captures shape
deviations along the boom.
Geert Creemers, CEO of ARGON Measuring Solutions, points out that “the combination of our shop-floor measurement solution, based on what we call our “coffee machine principle”, and the performance of the Leica Absolute Tracker ATS600, enables Vlassenroot to measure the parts quickly and reliably, wherever and at whatever stage they want.”
Through additional quality checks, Vlassenroot aims to drastically reduce the number of booms being reworked. Checking the quality of both half shells — the base for all booms — represents the first quality gate.
A new space, dedicated to the measurement procedures for booms in various production steps, has been set up in the production facility. Here, the trolley-mounted ATS600 can be positioned flexibly as needed, according to the large variety in part sizes.
In a second quality gate, the welded boom is checked to find out if the welding process has had any impact on the material and whether the heat caused any deformations, contributing to the previously mentioned material deformations.
Figure 3. With the ATS600 laser tracker mounted on its measurement trolley, ARGON created a highly mobile shop-floor solution for Vlassenroot.
Figure 4. Vlassenroot specialises in producing telescopic crane booms with lengths of up to 16 metres. Image: ©Argon
The third quality gate was installed right before the straightening process. “My intention right before the straightening was to receive the measuring results in a colour map that shows all deformations with detailed data,” says Dudzik. “We then use the data to design fixtures to avoid deformations during the welding process.”
After the straightening process, final assembly and painting take place. Here, during a fourth quality gate, the ATS600 inspects features such as the position of the attached locking disc and hydraulic stud attachments.
Dudzik and his team are already looking a step further ahead. “We plan to install more quality gates and find ways to make use of the data we collect. After checking the half shells, we can share that data with the Belgium facility, allowing them to adjust their bending machines and produce the booms more accurately. Our justification for the quality gates and therefore for our investment in the ATS600 shop-floor solution is to increase first-time-right production and avoid rework.”
The need for robust yet mobile measurement
Together with ARGON, Vlassenroot began the process of specifying their new system by evaluating measuring devices that were fast, accurate and, most importantly, resilient enough to deal with the production environment. “In our facilities we have to deal with dust and vibrations,” explains Dudzik. “We had our doubts about finding a device that can deal with this environment.”
Evaluation of other technologies capable of working on the shop floor uncovered unacceptable constraints, such as a time-intensive setup process or a time-consuming measurement and post-processing period of up to 90 minutes for a single boom. With the Leica Absolute Tracker ATS600, Vlassenroot found a solution that was not only resilient under the challenge of harsh conditions, but also flexible in its setup and integration and fast to produce usable results.
Compared to the past, measurements with the new ATS600- based shop-floor solution are simply much faster, with inspection time reduced by as much as 80 percent, and that with no measurement errors. “The results have been excellent,” says Dudzik. “And all this with minimal training required.”
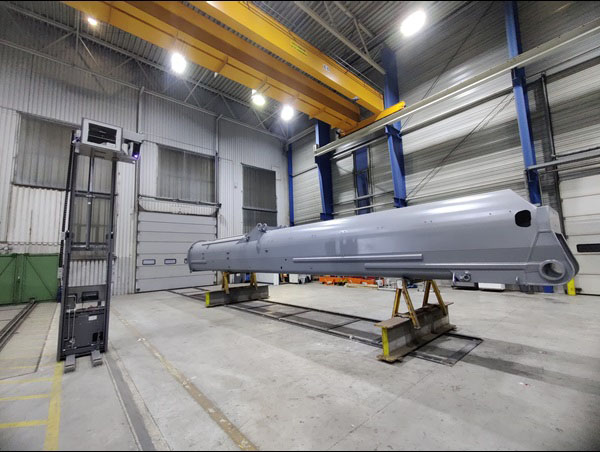
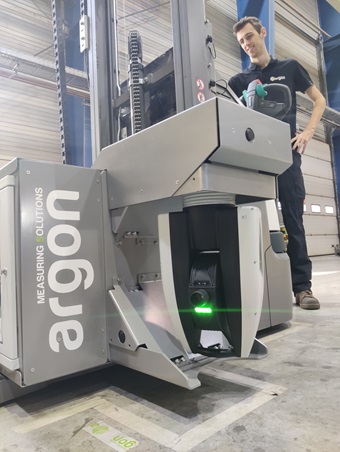