Hexagon helps Hendrick Motorsports toe the line while pushing the envelope
by Phillip Lewis and Dan Marinac, Hexagon’s Manufacturing Intelligence division

Engineering Reality 2023 volume 2 edition
Empowering Makers for an autonomous sustainable future
The team fields four full-time Chevrolet Camaro ZL1 entries in the NASCAR Cup Series with drivers Alex Bowman, William Byron, Chase Elliott, and Kyle Larson. Headquartered on over 100 acres in Concord, North Carolina, Hendrick Motorsports employs approximately 600 people.
Both for its own cars and components and the engines it builds for other teams, Hendrick Motorsports uses Hexagon equipment across its vehicle lab, fabrication shops and engine shops, as well as in the field.
Meeting NASCAR tolerances while maximising competitive edge
In NASCAR races, mere milliseconds can separate winners from losers, so gaining any possible competitive advantage is critical. But with the relatively recent introduction of NASCAR’s Next Gen car — where the chassis and vehicle structures for all cars are built by single source suppliers within extremely tight tolerances and stiffness specifications — the extent of customisation teams are permitted is extremely limited.
At a NASCAR race, each participating vehicle must undergo a quality check set to prove it is within tolerances. NASCAR uses optical scanning stations that quickly scan race cars producing a heatmap to indicate if anything is out of spec. Even a tiny area out of tolerance — like a spoiler bumped to the left by a quarter inch — is grounds for failing the car, forcing the team to bring it back to the garage for readjustment. If the readjustment falls short and the car fails inspection again, teams can face fines, lose track position, lose crew members, or even be assessed penalty laps.
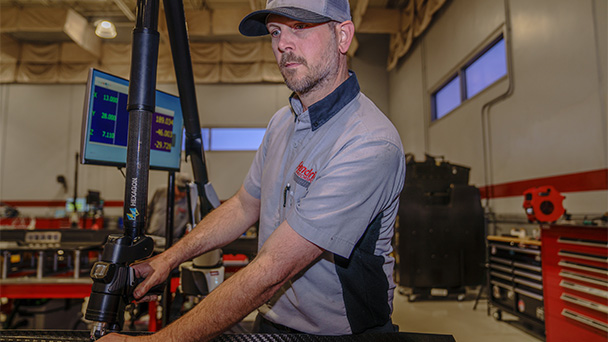
Figure 1. Bradley Johnson, Underwing Specialist with the Absolute Arm.
Figure 2. Bradley Johnson (Left) - Underwing Specialist working with an Absolute Arm with Roy Crump (Right) - Quality Control Supervisor.
Measurement data empowers Hendrick Motorsports to “bring better products to the racetrack”
During the off-season, the Hendrick team strategised ways to “be smarter, do better,” said Roy Crump, Quality Supervisor at Hendrick Motorsports. “We took all these components and started measuring every part to better understand what we were looking at — because the foundation is the chassis itself, and everything bolts to it. We quickly realised that measuring all the potential combinations of how the components could work together wasn’t realistic —we’d be measuring for months.
We knew we needed to determine a way to combine and measure parts virtually, and that’s where Hexagon came in. Hexagon has helped us bring better products to the racetrack.”
Hendrick Motorsports decided to build a new quality centre at its facility and partnered with Hexagon as the company’s sole provider of metrology solutions. The company currently uses multiple CMM machines, vision-based measurement systems, and Absolute Arm portable measuring arm systems with 3D laser scanners across its engine shop, vehicle lab, and fabrication shop, as well as in the field.
The measurement data that Hexagon tools provide has been vital to Hendrick’s ability to craft the best car. “Being able to assemble the best car based on what we see in the measurements of the parts has been key to our performance on the racetrack. Finding every single thousandth of a second here and there adds up on the racetrack for us. We use Hexagon tools to measure every component; it’s what we need to do to stay competitive,” said Crump.
Hendrick Motorsports knows they can count on Hexagon tools for highly accurate, precise measurements — something that’s critical in today’s racing environment. Tad Merriman, Engineering Manager, Engine Shop, Hendrick Motorsports shared, “In the past, we had several practice sessions, a qualifying session, and another practice session that provided opportunities to work on the car and engine. Today, we have events where we show up, unload the trailer, and the first lap on track is qualifying. There’s no opportunity to work on the car once it’s been unloaded, so it’s a competition of who can unload the best car off the trailer.”
Merriman continued, “The stakes are higher — whatever level of precision you implement in the shop is what you have when you get to the racetrack. This has impacted how we approach the vehicle build and what we send out the door.”
Optimising performance and maximising wins while staying within tolerance
Partnering with Hexagon, the Hendrick Motorsports team knows they’ve done everything possible to set their cars up for success — and wins.
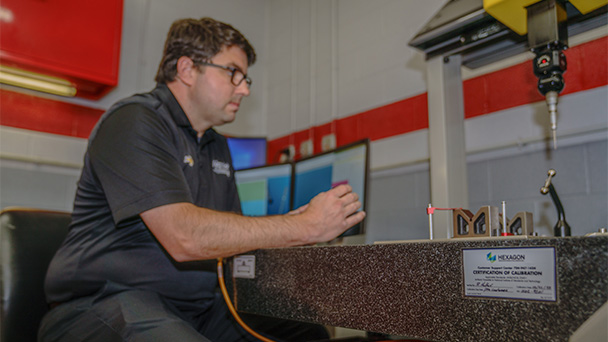
Figure 3. Tad Merriman - Engineering Manager, Engine Shop, Hendrick Motorsports at the stationary CMM.

Figure 4. Several reliable Hexagon CMMs are installed across the Hendrick engine and fabrication shops and vehicle lab.
Figure 5. The Absolute Arm systems in use at Hendrick are capable of touch probing as well as 3D scanning measurement, allowing for increased accuracy when inspecting features.
Merriman explained, “wherever the line is, we’re going to toe it. If you put that line over there, we’re going to go over there and put our toes on it. Wherever it is, we’re going to find that limit and be on it. Hexagon’s tools give us the confidence to get as close to the line as possible but still stay within NASCAR’s parameters. It’s very imperative that we have these measurement tools because we must make sure that we’re maximising the tolerances that were provided, and we have to know and trust that what we have is accurate. So, when we push it to the bleeding edge, when we go to the racetrack, we know we’ll be okay.”
Hendrick also uses Hexagon tools to gather after-race data to help inform future race strategies. Bradley Johnson, Engineer for Underwing at Hendrick Motorsports, adds, “It’s crucial, after a race, we bring the car back to the shop and measure everything that may have changed during the race — we rescan the body, we rescan the underwing — just to see how things changed when it got hot. If your car’s out in the sun all day, panels are swelling or shrinking. Stuff moves, and we want to see where it moves in our favour. Are there certain panels that are already leaning in or leaning out? We need to know if a particular panel gets hot and moves, if it will move in a
hundredth or out a hundredth of an inch — because it will get rescanned, and we don’t want to be out of tolerance,” he shared.
Hexagon tools allow Hendrick Motorsports to choose the best combination of parts from all available. “The chassis comes in three subsections, and we can combine them however we want to. We measure each component separately and identify that this specific centre section is perfect for what we’re looking for. That clip is perfect for what we’re looking for — so if we use this combination of parts in a car for a particular track, we will do even better. Hexagon has helped us look at the parts we have and realise what’s good and what’s bad. It allows us to go to the racetrack a lot more confident that we have the best product possible,” Crump explained.
He continued, “NASCAR mandates that we have to use the parts as provided, but they don’t say where specifically we have to use them. So, we use Hexagon’s tools to find components best suited to our needs — for example, finding a part that performs well on road courses. We’re talking tiny orders of magnitude, but every little bit counts in our sport. There have been events where people win by one-thousandth of a second, so if we can assemble a car combination that’s even five-thousandths of a second a lap faster over 500 laps, it will add up. It may be a thousandth here and a thousandth there. But in the end, once you put it all together, it translates to time on the clock and position on the racetrack — and hopefully to wins and championships.”
Specifically, Hendrick Motorsports uses Hexagon’s Absolute Arm systems to help improve the car’s travel. “Travel of the car refers to the suspension travel from where the car sits in the garage to where it actually rides on the racetrack. The closer the car is to the ground, the more aerodynamically advantageous it is. It helps drag and downforce, and so we do everything possible to maximise those advantages,” adds Merriman.
“We use the Absolute Arm to measure every suspension component and chassis. Once we’re done measuring, we review the data and know that by looking at a particular component’s parameters, we’ll be able to travel the car more — and when we travel the car more, that’s more speed on the racetrack. Hexagon lets us go part-by-part: once we determine a chassis’ parameters are good, we can find the best lower control arms we’ve measured. We can find the best mounts. We can find the best uprights. After we put that all together, we use that measurement data directly in our simulation tools, which can confirm or deny whether that combination of parts we put together is better,” said Crump.
Hendrick Motorsports’ partnership with Hexagon has also helped the organisation ensure they are delivering high- quality engines to their customers. Merriman explained, “We’re in the business of partnerships. We live off of partnerships, and we can’t afford to have a situation where a team thinks we’re favouring one partner over another. So, the engines we deliver are randomly built — we don’t know what engine is going to what team until the final moment. And we build all engines to the same specs, as identical as they can be. Hendrick Motorsports not only makes engines for themselves but also supplies engines for other NASCAR teams. We enjoy the success of our partners. Their success is our success — we’re proud to say we have 494 engine wins over our entire history.”
In the future, Hendrick Motorsports plans to expand its use of Hexagon tools, measuring more parts more efficiently. “We’re moving forward with a focus on being more efficient with our time and know that Hexagon will help us make that happen. Our race teams envision a future where a part comes in, we can measure it immediately and have it on the car in the next hour. And with Hexagon’s tools constantly improving, I think we’ll be able to work more quickly and accurately measure more parts, making our cars even better,” he concluded.

Engineering Reality magazine Volume XVI – issue 2
“The stakes are higher — whatever level of precision you implement in the shop is what you have when you get to the racetrack. This has impacted how we approach the vehicle build and what we send out the door.”