Greenfield shows Radan power to tomorrow’s engineers
Greenfield Engineering - UK
Contact us

Specialist CAD/CAM and logistics software from Radan is helping the largest sheet metal subcontractor in the South West of England to compete effectively with manufacturers in Eastern Europe and the Far East.
Based at Holsworthy, near the North Devon coast, Greenfield Engineering have the latest machine tools and state-of-the-art software to utilise them to the fullest capability. Currently operating out of two sites, combining 45,000 square feet, they are in the process of taking an additional 6,000 square foot factory as part of their latest £1m investment programme.
A recently installed Amada EM 3610ZRB punch press and buffet turret is fully automated with load/unload and part picking, enabling them to take advantage of opportunities of additional work from existing and new customers.
This brings their CNC machine tool tally to three punches and an Amada EML 3610NT 4kw punch/laser combi. The punch/laser is equipped with a ten-pallet stockyard for part removal and component stacking, giving them true lights out 24-hour production capabilities, and means they have full manufacturing flexibility.
Their EM3610NT punch also has a ten-pallet tower, capable of holding 27 tonnes of steel, and three-table part picker, along with an external tooling carousel holding ready-for-use 220-tool and 440-die options.
Their market sectors include office furniture, electronic enclosures, point of sale, lighting, and vending, for a number of well-known names including Herman Miller Office Furniture and Bisley Filing Cabinets. Contracts range from producing basic individual components, right through to fully assembled and packaged finished products.
With five seats of Radan’s 3D and 2D design solutions, and Radnest, Radpunch and Radcombi, he says all components go through the software. “The nesting module is absolutely crucial in ensuring, first of all, that the products are designed and manufactured correctly, and then that we have the highest material utilisation and lowest run times. Steel prices are extremely volatile at the moment, so every little percentage that we can save is passed on to our customers.” Four employees currently use Radan for 3D design and development, with two full-time programmers, and third programmer on the night shift.
Greenfield operate an impressive apprenticeship scheme, which saw Gary Burnard rise through the ranks himself from apprentice to Managing Director. They currently have 16 apprentices, mainly working towards Level-3, with some at Level-2, and they recruit more at each summer intake. “As manufacturing is not a major sector in Devon, it’s hard to find people with the skills we need, so we train them ourselves to become the engineers of the future.”
Apprentices are rotated through the entire business during their first two years, and are introduced to Radan while learning design and programming. “They pick it up so easily – it’s very intuitive, easy to learn and easy to remember.”
Greenfield are also pioneering the use of Radan’s logistics suite in the UK. “It allows us to take the raw demand from our ERP/MRP system and manage it in a number of ways,” says Gary Burnard. “The Order Manager and Material Manager functions help us interpret what’s needed to be done in the factory in a more efficient way.”
They first saw the logistics package, all of which is currently not readily available in the UK, at the Euroblech exhibition. “I hadn’t seen anything like it before – developed specifically for sheet metal equipment and recognising exactly what sheet metal manufacturing companies need.”
The logistics suite was supplied by Radan’s Dutch subsidiary Radan BV, and provides the ability to organise components and procedures purely from a planning and manufacturing aspect. Radan BV have been supplying Logistics products for many years. It is with that experience that Radan are currently in the process of utilising this expertise to provide a global solution.
Gary Burnard says: “We can take a number of components and put them together for a particular machining process, paint colour, or just a target date, rather than reasons of them simply being from single job. It increases our ability to plan and improve that particular function, meaning we’re as agile, flexible and competitive as possible.”
And he says project nesting complements the logistics suite perfectly, by allowing them to select parts from different jobs and different customers, and nest them together for best sheet utilisation.
The company have used Radan since the arrival of their first CNC machine. “Then, as now, it was the market leader in sheet metal CAD/CAM software in the UK, and was the obvious choice for us. The 3D facilities were the best we’d ever seen for sheet metal, and the CNC programming was so simple and easy to pick up.”
In conclusion, Gary Burnard says: “Radan is clearly a forward thinking company with products ensuring that manufacturers become considerably more efficient and competitive. Most CNC software is designed simply to drive machines, but Radan is much more business-focused and looks at the bigger picture.”
Based at Holsworthy, near the North Devon coast, Greenfield Engineering have the latest machine tools and state-of-the-art software to utilise them to the fullest capability. Currently operating out of two sites, combining 45,000 square feet, they are in the process of taking an additional 6,000 square foot factory as part of their latest £1m investment programme.
A recently installed Amada EM 3610ZRB punch press and buffet turret is fully automated with load/unload and part picking, enabling them to take advantage of opportunities of additional work from existing and new customers.
This brings their CNC machine tool tally to three punches and an Amada EML 3610NT 4kw punch/laser combi. The punch/laser is equipped with a ten-pallet stockyard for part removal and component stacking, giving them true lights out 24-hour production capabilities, and means they have full manufacturing flexibility.
Their EM3610NT punch also has a ten-pallet tower, capable of holding 27 tonnes of steel, and three-table part picker, along with an external tooling carousel holding ready-for-use 220-tool and 440-die options.
Their market sectors include office furniture, electronic enclosures, point of sale, lighting, and vending, for a number of well-known names including Herman Miller Office Furniture and Bisley Filing Cabinets. Contracts range from producing basic individual components, right through to fully assembled and packaged finished products.
With five seats of Radan’s 3D and 2D design solutions, and Radnest, Radpunch and Radcombi, he says all components go through the software. “The nesting module is absolutely crucial in ensuring, first of all, that the products are designed and manufactured correctly, and then that we have the highest material utilisation and lowest run times. Steel prices are extremely volatile at the moment, so every little percentage that we can save is passed on to our customers.” Four employees currently use Radan for 3D design and development, with two full-time programmers, and third programmer on the night shift.
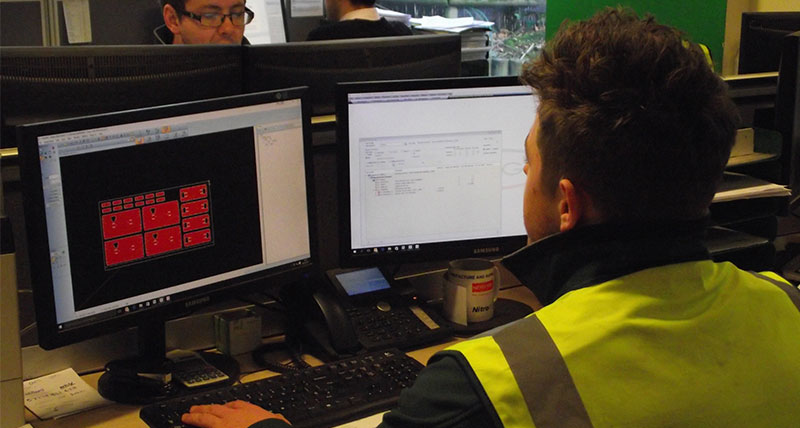
Apprentices are rotated through the entire business during their first two years, and are introduced to Radan while learning design and programming. “They pick it up so easily – it’s very intuitive, easy to learn and easy to remember.”
Greenfield are also pioneering the use of Radan’s logistics suite in the UK. “It allows us to take the raw demand from our ERP/MRP system and manage it in a number of ways,” says Gary Burnard. “The Order Manager and Material Manager functions help us interpret what’s needed to be done in the factory in a more efficient way.”
They first saw the logistics package, all of which is currently not readily available in the UK, at the Euroblech exhibition. “I hadn’t seen anything like it before – developed specifically for sheet metal equipment and recognising exactly what sheet metal manufacturing companies need.”
The logistics suite was supplied by Radan’s Dutch subsidiary Radan BV, and provides the ability to organise components and procedures purely from a planning and manufacturing aspect. Radan BV have been supplying Logistics products for many years. It is with that experience that Radan are currently in the process of utilising this expertise to provide a global solution.
And he says project nesting complements the logistics suite perfectly, by allowing them to select parts from different jobs and different customers, and nest them together for best sheet utilisation.
The company have used Radan since the arrival of their first CNC machine. “Then, as now, it was the market leader in sheet metal CAD/CAM software in the UK, and was the obvious choice for us. The 3D facilities were the best we’d ever seen for sheet metal, and the CNC programming was so simple and easy to pick up.”
In conclusion, Gary Burnard says: “Radan is clearly a forward thinking company with products ensuring that manufacturers become considerably more efficient and competitive. Most CNC software is designed simply to drive machines, but Radan is much more business-focused and looks at the bigger picture.”