Race Sports: Catch the Highest Performance with Lightweight Design
From Load Simulation via Generative Design to Manufacturing and Verification – Optimisation of a Wheel Carrier for FormulaStudent with Hexagon
Superior design for maximum performance
To maximise the output, the team used MSC Apex Generative Design to generate a super-lightweight, yet robust wheel carrier for their race car

Every year a team of young students from the UPBracing Team develops a FormulaStudent racing car to compete in international competitions. Two factors are essential for a successful racing car: light weight and strong components. In addition to the races in which drivers and racing cars prove their performance, there is also an extra rating for the lightweight construction of the racing car. Due to its fourfold use, the wheel carrier is ideal for saving weight while meeting high load-bearing requirements.
Smart Generative Design for tailored 3D Printing Structures
In previous years, the team had tried to design light weight wheel carriers with complex milling designs. The wheel carrier in 2012 with a traditional, already complex, milling design weighed 515g. It was milled from a 16 kg block of material thus producing 15.5 kg of aluminum waste. For the 2018 season, MSC Apex Generative Design technology was applied to create an optimal lightweight design. Design and non-design areas were defined in the model design and the complex load cases were added. The mesh was then automatically generated and optimized. The algorithm generated the finished smoothed result with a weight of 266 g - a reduction of 48% compared to the 2012 equivalent. There was also no significant waste of material because the part was produced by additive manufacturing. This contributed considerably to the overall weight reduction of the race car and gained a lot of attention and a very good rating within the design report, a special category in the overall competition.
Fill in the form and directly access this case story!
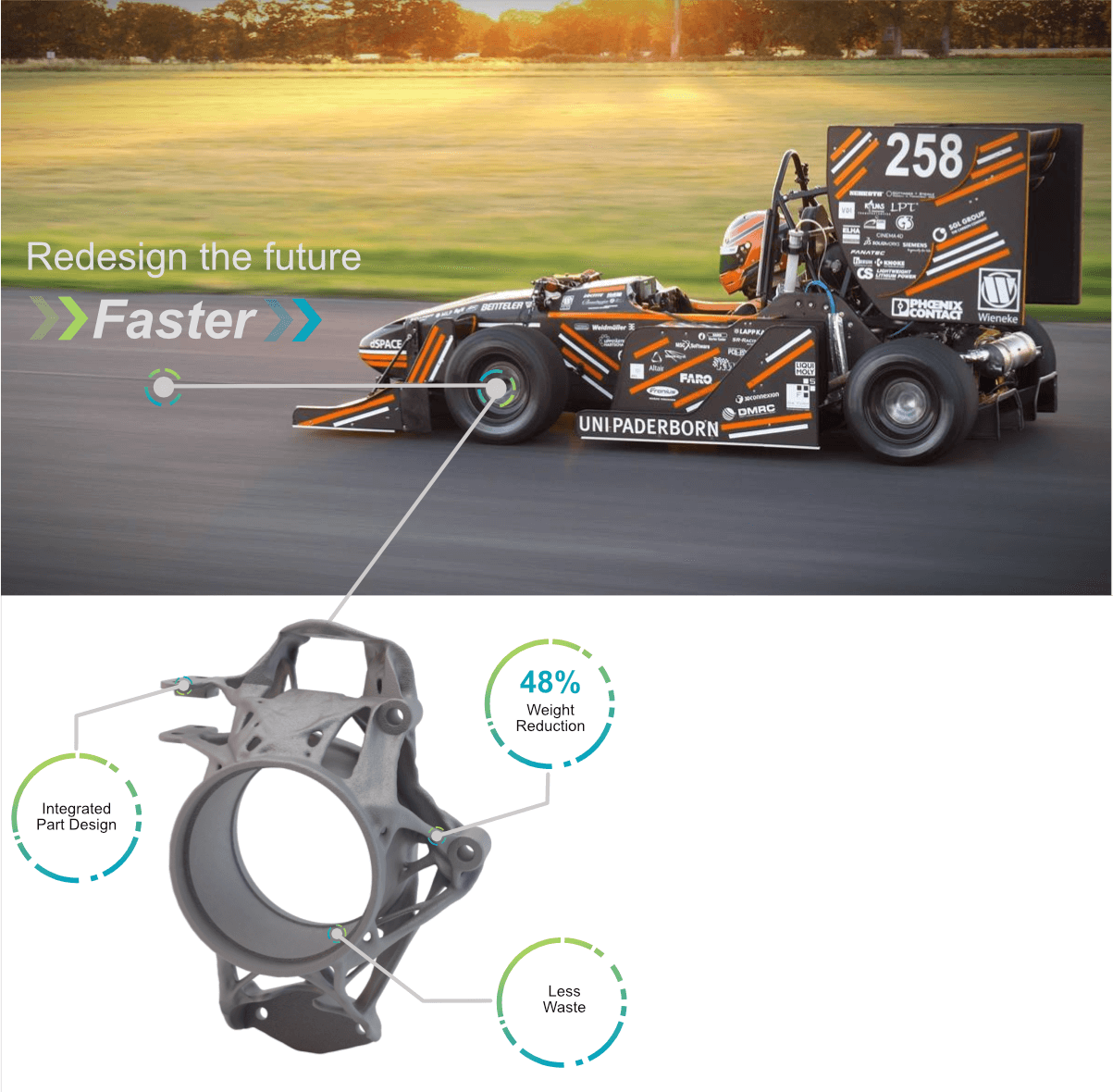