EDGECAM manages the right strategy for taking the brakes off
AIcon Components - UK
Contact us
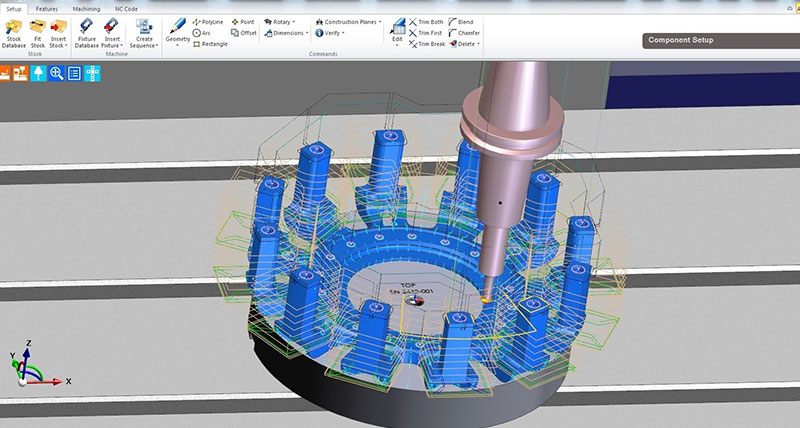
Automating much of its CAM programming for specialised motorsport braking pistons, means Alcon Components can create CNC toolpaths for hundreds of variants in two minutes.
“If we didn’t use EDGECAM’s Strategy Manager system, our more complex pistons would take around four hours to program,” says Production Engineer Warren Knight.
Alcon has a long history of supplying innovative race-winning brake and clutch technology to F1, Touring and NASCAR cars; and World Rally Championship teams, including helping Sébastien Loeb take seven successive driver’s titles for Citroën.
Marketing Manager Emeline Wilson explains that as well as pistons and the aluminium and cast iron calipers they fit into, Alcon also produces brake discs, master cylinders and brake pedal boxes, brake pad solutions and high performance sintered and carbon clutches.
And as an OEM tier 1 supplier for road car companies, key customers include Jaguar-Land Rover and Bentley. The company also supplies braking systems for military vehicles and armoured cars, both of which have heavy armoured panels and need more substantial brakes.
The pistons inside Alcon Components’ brake calipers come in many different sizes, and Warren Knight states as their typical batch size is relatively small and most parts are designed for a specific application, it would be impractical to spend several hours on programming. “We use Strategy Manager to automate a considerable number of EDGECAM’s machining applications on the pistons. Individual features change considerably – such as being longer, shorter, having a smaller diameter, a larger diameter, smaller bore and longer bore, and also include mill slots, undercuts, holes and chamfers, amongst others.
“We simply load a piston into EDGECAM, insert the Strategy Manager files we need, and within two minutes we’ve got a program coming out for each variant. It not only looks at sizes and features, but also changes speeds and feeds for different materials such as titanium, aluminium and stainless steel.”
Warren Knight uses Strategy Manager to build flexible strategies, utilising his own extensive knowledge of Alcon’s requirements, in a simple flow chart format which defines the rules governing how the part will be machined, creating consistent, repeatable G-code.
Having used EDGECAM at a previous employer since the turn of the Century, he was largely responsible for Alcon installing it in 2015. He says coupling EDGECAM and Strategy Manager with a new Doosan Lynx 220 for manufacturing the pistons has completely revolutionised the way they work. “The piston programs are all for mill-turn applications, and include sub-spindle pick-up, transfer and machining. Previously we were making pistons in two operations – either on two separate machines, or on one machine but with a second set-up between operations.”
With pistons going into all Alcon’s calipers, it means they are used in around 80 per cent of the company’s products. Production Engineering Manager Brian Cutler says: “We’re always adding to our range, with new brake discs or calipers, and if a caliper contains two, four or six pistons they can each be a different size, so the short set-up and programming times that Strategy Manager gives us are proving to be a real asset for the business.
“Seeing the toolpaths on the computer in the office means they will also be perfect at the machine when we start to cut metal.”
EDGECAM has also reduced the cycle times on the more complex pistons from around half an hour to ten minutes. “Using EDGECAM and Strategy Manager means we can get products to market faster and respond to customer requests quicker. Overall it makes us even more efficient as a company.”
While EDGECAM drives a further five CNC machines producing Alcon’s full product range, the Doosan Lynx is the only machine currently driven with programs involving Strategy Manager. However, Warren Knight has conducted research on using both EDGECAM and Strategy Manager for manufacturing discs, too, and is looking for this operation to go live before the end of 2016. “As discs are also a major part of our business, this will be another big time-saving for us.”
Offering a full in-house R & D, design, machining and assembly service from its Staffordshire headquarters, Alcon also has a dedicated team in the United States.
One of Alcon’s latest products is a triple plate carbon clutch aimed at rallycross drivers, and designed to be one of the most competitive clutches on the market. This new 2016 clutch is approximately ten per cent lighter than its predecessor, offering 18 per cent reduction in inertia, as well as 38 per cent reduction in deflection.
“If we didn’t use EDGECAM’s Strategy Manager system, our more complex pistons would take around four hours to program,” says Production Engineer Warren Knight.
Alcon has a long history of supplying innovative race-winning brake and clutch technology to F1, Touring and NASCAR cars; and World Rally Championship teams, including helping Sébastien Loeb take seven successive driver’s titles for Citroën.
Marketing Manager Emeline Wilson explains that as well as pistons and the aluminium and cast iron calipers they fit into, Alcon also produces brake discs, master cylinders and brake pedal boxes, brake pad solutions and high performance sintered and carbon clutches.
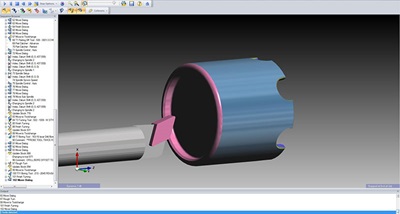
The pistons inside Alcon Components’ brake calipers come in many different sizes, and Warren Knight states as their typical batch size is relatively small and most parts are designed for a specific application, it would be impractical to spend several hours on programming. “We use Strategy Manager to automate a considerable number of EDGECAM’s machining applications on the pistons. Individual features change considerably – such as being longer, shorter, having a smaller diameter, a larger diameter, smaller bore and longer bore, and also include mill slots, undercuts, holes and chamfers, amongst others.
“We simply load a piston into EDGECAM, insert the Strategy Manager files we need, and within two minutes we’ve got a program coming out for each variant. It not only looks at sizes and features, but also changes speeds and feeds for different materials such as titanium, aluminium and stainless steel.”
Warren Knight uses Strategy Manager to build flexible strategies, utilising his own extensive knowledge of Alcon’s requirements, in a simple flow chart format which defines the rules governing how the part will be machined, creating consistent, repeatable G-code.
Having used EDGECAM at a previous employer since the turn of the Century, he was largely responsible for Alcon installing it in 2015. He says coupling EDGECAM and Strategy Manager with a new Doosan Lynx 220 for manufacturing the pistons has completely revolutionised the way they work. “The piston programs are all for mill-turn applications, and include sub-spindle pick-up, transfer and machining. Previously we were making pistons in two operations – either on two separate machines, or on one machine but with a second set-up between operations.”
With pistons going into all Alcon’s calipers, it means they are used in around 80 per cent of the company’s products. Production Engineering Manager Brian Cutler says: “We’re always adding to our range, with new brake discs or calipers, and if a caliper contains two, four or six pistons they can each be a different size, so the short set-up and programming times that Strategy Manager gives us are proving to be a real asset for the business.
“Seeing the toolpaths on the computer in the office means they will also be perfect at the machine when we start to cut metal.”
EDGECAM has also reduced the cycle times on the more complex pistons from around half an hour to ten minutes. “Using EDGECAM and Strategy Manager means we can get products to market faster and respond to customer requests quicker. Overall it makes us even more efficient as a company.”
While EDGECAM drives a further five CNC machines producing Alcon’s full product range, the Doosan Lynx is the only machine currently driven with programs involving Strategy Manager. However, Warren Knight has conducted research on using both EDGECAM and Strategy Manager for manufacturing discs, too, and is looking for this operation to go live before the end of 2016. “As discs are also a major part of our business, this will be another big time-saving for us.”
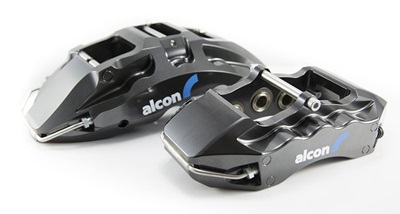
One of Alcon’s latest products is a triple plate carbon clutch aimed at rallycross drivers, and designed to be one of the most competitive clutches on the market. This new 2016 clutch is approximately ten per cent lighter than its predecessor, offering 18 per cent reduction in inertia, as well as 38 per cent reduction in deflection.