Blue and white metrology under Bavaria’s skies
Aircraft Philipp - Germany
Contact us

Aircraft Philipp makes structural components in Übersee, Bavaria for every conceivable type of passenger and military aircraft. One such plane is the Airbus A320, the world‘s best-selling medium-range airliner. So that these silver birds climb safely into white and blue skies all over the world, quality assurance at Aircraft Philipp is firmly grounded on a coordinate measurement system from Hexagon Manufacturing Intelligence.
Aircraft Philipp has been active in this industry for over 45 years. Structural and engine components leave the assembly lines in three locations in Germany for dispatch to almost all renowned aircraft manufacturers. The Übersee factory produces a wide range of machined aluminium or the more costly titanium structural components with dimensions up to 2 metres for incorporation into airframes. Small batches but enormous diversity of parts are the order of the day for the Bavarii.
Even after decades in the business, Toni Liedl, Quality Manager at Aircraft Philipp, is still fascinated by the engineering that makes aircraft construction possible. “I am still filled with enthusiasm when everything fits together at the end, just as it should. Especially when you consider the multitude of parts, with regular shapes, straight lines, various angles etc., which go into each plane.“
The company has made its mark in particular with its competence in numerical control (NC) programming. But it is not just milling and turning machines that are fed with CAD data from CATIA V5. The data is also essential for metrology. The metrology technicians use a DEA GLOBAL series coordinate measuring machine (CMM) with a measurement range of 1200 x 3000 x 1000 mm and PC-DMIS CAD++ CMM software. The software integrates CAD models simply and easily.
In addition to initial sample testing, coordinate measuring systems are used in the metrology laboratory for checking current series production – whether by 100% checks or random sampling – and for inspecting parts after modifications to machining programs. Metrology technician Andreas Laumer loads the part on the coordinate measuring machine and starts the measuring program. In normal circumstances Laumer can say within 30 to 60 minutes whether the component complies with the reference model.
And this teamwork also works beyond the borders of Bavaria. All departments in the corporate group use PC-DMIS CAD++ CMM software. When the need arises at Karlsruhe, the engineers there simply send the CAD model and the necessary information about probes, fixturing systems and X-Y-Z axes to Übersee. On his off-line station Andreas Laumer creates the measuring program and makes it available to his colleagues in Karlsruhe.
Member of the PC-DMIS fan club Andreas Laumer enthuses about the features of the measuring software: “I am a real PC-DMIS fan,“ he affirms. “The beauty of PC-DMIS is that there are different ways to achieve your goal when programming. Thus there are always alternative solutions.
And the traceability of the evaluation is perfect. For example, if I had to examine a diameter and assess its circularity and for some reason the part was already with the customer, then I could still carry out the assessment in spite of this – using the previously measured values.“ Furthermore, he is able to do the programming very quickly, thanks to the shortcuts and the good graphical capabilities of the system. The excellent training from Hexagon Manufacturing is bound to have helped too. And the support from the Hexagon Manufacturing Intelligence application engineers is worth its weight in gold, maintains Laumer.
Just as diverse as the palette of parts produced at Aircraft Philipp are the standards that the parts have to fulfil and the tolerances on their various features, which may be anything from a few microns to several hundredths of a millimetre. A universal measuring solution was therefore a must. Aircraft Philipp has backed a winner with the DEA GLOBAL coordinate measuring machine in combination with the flexible PC-DMIS CAD++ software.
Aircraft Philipp has been active in this industry for over 45 years. Structural and engine components leave the assembly lines in three locations in Germany for dispatch to almost all renowned aircraft manufacturers. The Übersee factory produces a wide range of machined aluminium or the more costly titanium structural components with dimensions up to 2 metres for incorporation into airframes. Small batches but enormous diversity of parts are the order of the day for the Bavarii.
Even after decades in the business, Toni Liedl, Quality Manager at Aircraft Philipp, is still fascinated by the engineering that makes aircraft construction possible. “I am still filled with enthusiasm when everything fits together at the end, just as it should. Especially when you consider the multitude of parts, with regular shapes, straight lines, various angles etc., which go into each plane.“
True versatility: DEA GLOBAL and PC-DMIS
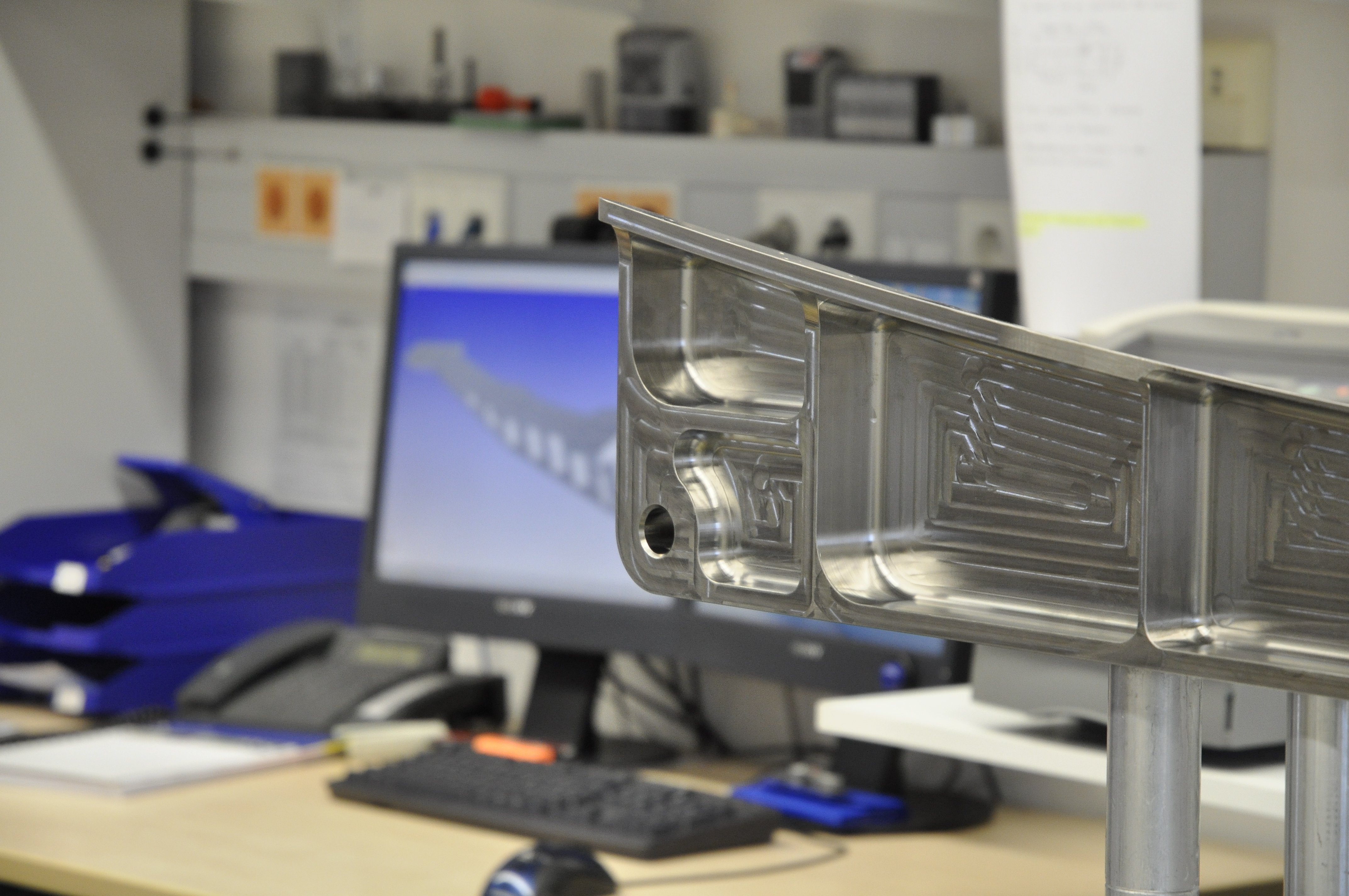
In addition to initial sample testing, coordinate measuring systems are used in the metrology laboratory for checking current series production – whether by 100% checks or random sampling – and for inspecting parts after modifications to machining programs. Metrology technician Andreas Laumer loads the part on the coordinate measuring machine and starts the measuring program. In normal circumstances Laumer can say within 30 to 60 minutes whether the component complies with the reference model.
Strong argument: off-line programming
“We chose to invest in the Hexagon Manufacturing Intelligence system because PC-DMIS is by far the best measuring software with respect to off-line programming,“ says Liedl. Since the introduction of off-line programming based on CAD data, the company‘s technicians have been able to create NC and measuring programs at the same time – without having the part physically in front of them and blocking the measuring machine. An enormous saving in time. “During periods of high economic growth, we have to process 500 initial samples per year, which equates to between five and seven approval processes per day.The NC and measuring programs must be created in parallel so that we can manage this workload in the short time available,“ says Toni Liedl. “While we program with the off-line licence, other parts are being inspected on the CMM using previously created programs.“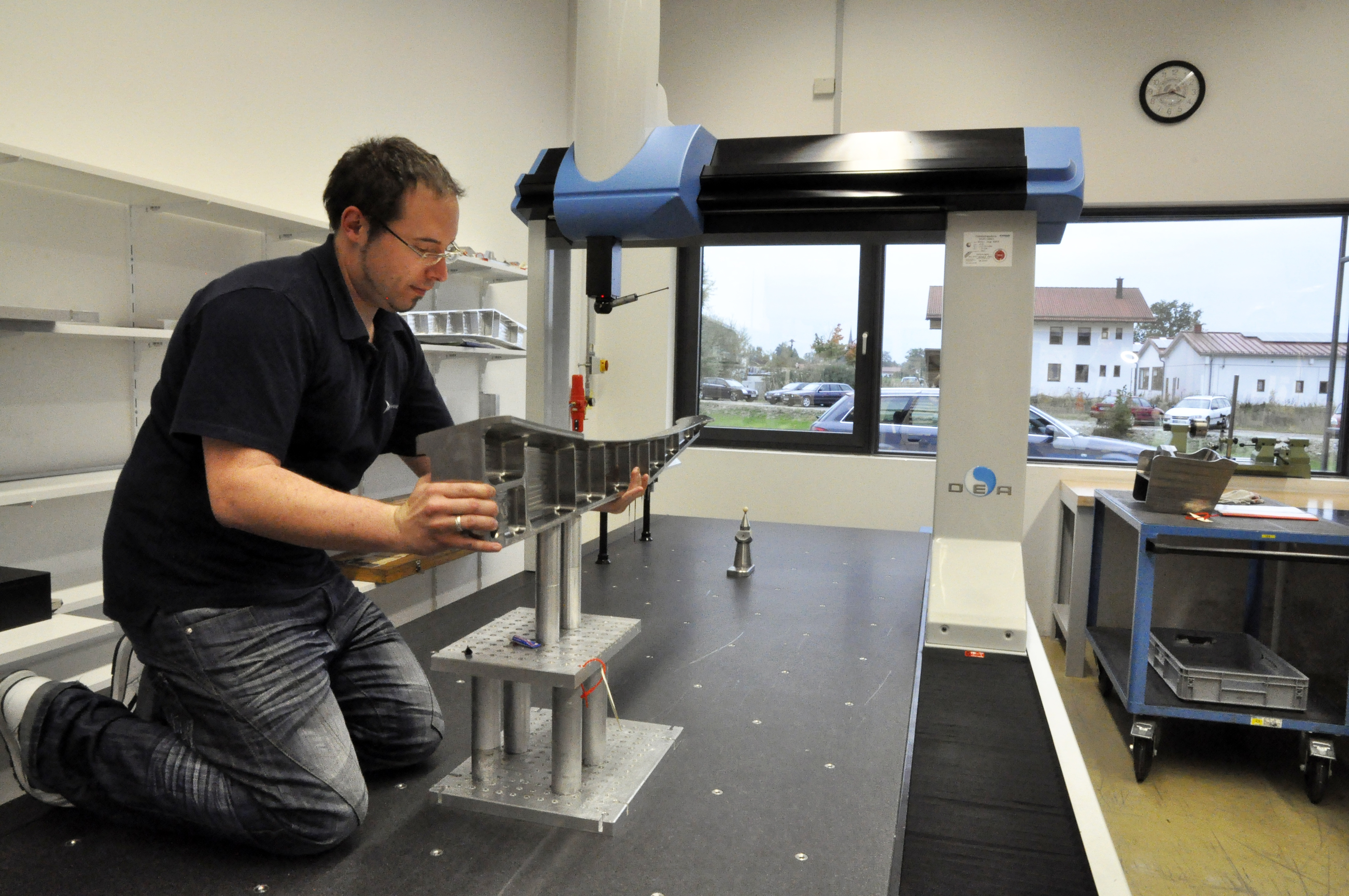
Member of the PC-DMIS fan club Andreas Laumer enthuses about the features of the measuring software: “I am a real PC-DMIS fan,“ he affirms. “The beauty of PC-DMIS is that there are different ways to achieve your goal when programming. Thus there are always alternative solutions.
And the traceability of the evaluation is perfect. For example, if I had to examine a diameter and assess its circularity and for some reason the part was already with the customer, then I could still carry out the assessment in spite of this – using the previously measured values.“ Furthermore, he is able to do the programming very quickly, thanks to the shortcuts and the good graphical capabilities of the system. The excellent training from Hexagon Manufacturing is bound to have helped too. And the support from the Hexagon Manufacturing Intelligence application engineers is worth its weight in gold, maintains Laumer.
Just as diverse as the palette of parts produced at Aircraft Philipp are the standards that the parts have to fulfil and the tolerances on their various features, which may be anything from a few microns to several hundredths of a millimetre. A universal measuring solution was therefore a must. Aircraft Philipp has backed a winner with the DEA GLOBAL coordinate measuring machine in combination with the flexible PC-DMIS CAD++ software.