ALPHACAM macros provide a step up for Stairplan
Stairplan - U.K.
Contact us

Purpose-written macros in Alphacam software have slashed programming time of bespoke projects from a day down to an hour, for a staircase specialist.
“Every staircase we make is individual,” says Stairplan Managing Director Graham Thomas. “And Alphacam takes the awkward machining we need to do, in its stride.”
The Telford-based company averages around 100 staircases a week, from space-savers through recessed, to high-end £60,000 staircases. “We never make two the same, and we don’t produce the same type in any order. But whatever we need to manufacture, we can do it with Alphacam. Without it, we simply couldn’t provide the service we do.”
Many of their products have a standard core which is designed with specialist staircase software, but Alphacam is used to add the bespoke elements, and the macros enable them to produce items extremely quickly.
“For example, when we make bolted treads, a macro creates all the drilling, where everything has to line up with the strings. And another macro manages our special fixings. The latest macro means we get drawings and toolpaths with just one click. It cuts the programming time by 90 per cent. Programming the internal aspect of a staircase used to take a day – now it takes an hour.
“We import a DXF file of the core staircase into Alphacam and the macros apply all the alterations with one click. It puts in all the connections, the drilling, the dowels, and the toolpaths.”
He says automating their processes in this way with Alphacam…part of the Vero Software suite…makes long, laborious tasks, very simple, and enables them to adhere rigidly to their maximum ten-day turnaround promise, even on the most complex shapes and curved handrails.
Graham Thomas began his career as a carpenter and joiner with a five-year apprenticeship, then decided his future lay in making the parts, and he focused on staircases and roofs. He started manufacturing in his garage before moving into a workshop, and then his first factory. Expansion followed, eventually moving into his current 30,000 square foot factory – which has room for further growth – where he now employs around 30 people.
Customers include joiners and both domestic and commercial sectors with developers, high-end builders, and the general public including self-build. “Our biggest single market are joiners, who appreciate the high quality we’re able to provide.”
Describing Stairplan as ‘engineers in wood,’ they use all the main species of timber, including pine, oak, beech, ash and walnut. Everything is now manufactured on their CNC machine tools: five 5-axis Makas and three twin-headed 5-axis and 4-axis Homags with automatic tables.
“We went down the automatic table route because of the time it saves with loading, and the accuracy. It now takes us literally 20 seconds to set up a table, and it’s far more reliable. Pre-automation it could take up to 15 minutes to position the pods, and then they weren’t always in the right place.”
Another aid to accuracy is the SL-Laser system that they use on all their CNC machine tools where every setup is simplified using laser projection for the exact positioning and alignment of machines and workpieces.
Once the components come off the machines they are thoroughly checked and assembled before being despatched around the world. “We send staircases to a wide variety of countries, including Sierra Leone, Australia, Gibraltar, France, Cyprus, and the USA.”
In conclusion, Graham Thomas says: “We can now make difficult components very quickly, and that’s because Alphacam’s engineers looked at what we needed to know and produced a bespoke automated solution for us. It’s tailored machining.”
“Every staircase we make is individual,” says Stairplan Managing Director Graham Thomas. “And Alphacam takes the awkward machining we need to do, in its stride.”
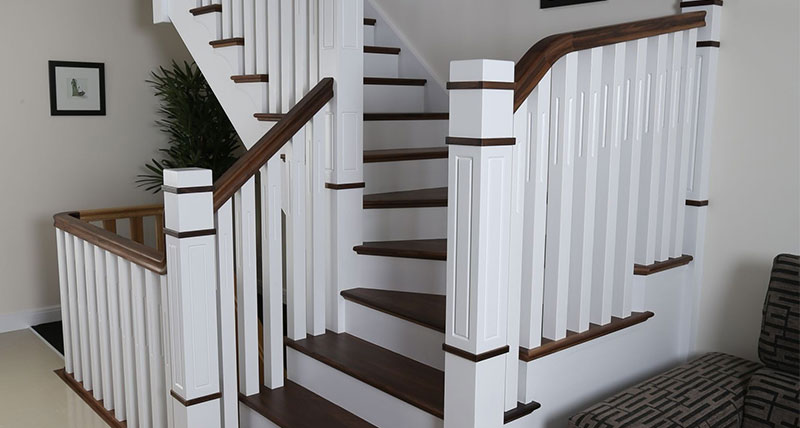
Many of their products have a standard core which is designed with specialist staircase software, but Alphacam is used to add the bespoke elements, and the macros enable them to produce items extremely quickly.
“For example, when we make bolted treads, a macro creates all the drilling, where everything has to line up with the strings. And another macro manages our special fixings. The latest macro means we get drawings and toolpaths with just one click. It cuts the programming time by 90 per cent. Programming the internal aspect of a staircase used to take a day – now it takes an hour.
“We import a DXF file of the core staircase into Alphacam and the macros apply all the alterations with one click. It puts in all the connections, the drilling, the dowels, and the toolpaths.”
He says automating their processes in this way with Alphacam…part of the Vero Software suite…makes long, laborious tasks, very simple, and enables them to adhere rigidly to their maximum ten-day turnaround promise, even on the most complex shapes and curved handrails.
Graham Thomas began his career as a carpenter and joiner with a five-year apprenticeship, then decided his future lay in making the parts, and he focused on staircases and roofs. He started manufacturing in his garage before moving into a workshop, and then his first factory. Expansion followed, eventually moving into his current 30,000 square foot factory – which has room for further growth – where he now employs around 30 people.
Customers include joiners and both domestic and commercial sectors with developers, high-end builders, and the general public including self-build. “Our biggest single market are joiners, who appreciate the high quality we’re able to provide.”
Describing Stairplan as ‘engineers in wood,’ they use all the main species of timber, including pine, oak, beech, ash and walnut. Everything is now manufactured on their CNC machine tools: five 5-axis Makas and three twin-headed 5-axis and 4-axis Homags with automatic tables.
“We went down the automatic table route because of the time it saves with loading, and the accuracy. It now takes us literally 20 seconds to set up a table, and it’s far more reliable. Pre-automation it could take up to 15 minutes to position the pods, and then they weren’t always in the right place.”
Another aid to accuracy is the SL-Laser system that they use on all their CNC machine tools where every setup is simplified using laser projection for the exact positioning and alignment of machines and workpieces.
Once the components come off the machines they are thoroughly checked and assembled before being despatched around the world. “We send staircases to a wide variety of countries, including Sierra Leone, Australia, Gibraltar, France, Cyprus, and the USA.”
In conclusion, Graham Thomas says: “We can now make difficult components very quickly, and that’s because Alphacam’s engineers looked at what we needed to know and produced a bespoke automated solution for us. It’s tailored machining.”