Digimat-MF
Predict and analyse multiphase and composite material properties in a fast, efficient and accurate way
Digimat-MF
From constituents to macroscopic behavior by mean-field homogenisation

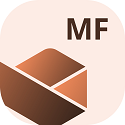
Digimat-MF computes the macroscopic properties of multiphase materials based on a mean field homogenization approach that provides fast and accurate results.
Exploring material designs with our Digital Materials Laboratory
The materials of tomorrow need to be designed with optimized properties tailored to the application and industry of interest. Digimat-MF brings the essence of a physical lab to your digital workspace. It enables you to define the constituent materials, design the microstructure, and apply the loading conditions in a click of a button, saving time and reducing material waste to explore new materials.
A large array of material models covering diverse analysis types and levels of richness enables a seamless setup of the most complex systems. The underlying mean-field homogenisation allows users to rapidly obtain composite responses with a high level of confidence, across various performances such as failure, creep, fatigue, as well as thermal and electrical conductivity among other multiphysics.
Value & benefits:
- Get insights of macroscopic properties of multiphase composite materials
- Quantify the material sensitivity to the underlying microstructure, constituents, defects, etc.
- Optimise properties to match specific requirements
- Assess average per-phase properties leveraging multiscale simulation.
Key features:
-
A wide variety of material models to cover different needs and applications
-
Multiphase and multilayered microstructures
-
Damage, failure and fatigue modelling
-
Loadings for virtual testing
-
Fast and accurate results