Sélection d'une MMT
Une bonne MMT fait toute la différence dans les tâches de mesure.
Contactez-nous

Dans la fabrication moderne, le contrôle des processus et l’assurance qualité s'appuient de plus en plus sur la performance des machines à mesurer tridimensionnelles (MMT). Durant les 20 dernières années, les MMT se sont substituées aux méthodes d’inspection traditionnelles accomplies au moyen de calibres et de bridages. Elles ont réduit le temps de traitement et les interventions humaines nécessaires, pour l’assurance qualité.
Les MMT peuvent aussi bien inspecter des dimensions géométriques standard que des pièces à profil spécial, comme les engrenages, les arbres à cames, les formes d’airfoil et bien d’autres encore. Dans un environnement de production classique, chacun de ces examens exigerait une machine de test spécifique.
La qualité des produits ne dépend pas seulement de la qualité des machines-outils utilisées pour la fabrication. Elle est également tributaire de la précision et de la répétabilité des systèmes de mesure et d'inspection. Associé à une MMT de haute précision, un centre d’usinage pas cher et aux performances faibles peut tout de même garantir la qualité des produits parce que seules les pièces respectant les tolérances passent le test avec la MMT. En revanche, un centre d’usinage de haute qualité, onéreux, ne peut pas garantir la qualité s’il est associé à un système de mesure bon marché à faible précision. Un certain pourcentage de pièces hors tolérance passera toujours le test avec cette MMT. D’autre part, un certain pourcentage de pièces respectant la tolérance seront rejetées. Par conséquent, la sélection de la bonne MMT est cruciale. Cet article a pour but d'aider à choisir une MMT conforme aux exigences de précision et d'application spécifiques.
Le premier critère de sélection important est la détermination de la plage de mesure minimale exigée sur la MMT. Cette plage dépend en général des dimensions de la pièce à mesurer, mais est souvent beaucoup plus complexe que cela. Par exemple, si la configuration de la pièce et le programme d’inspection imposent l’utilisation de rallonges de stylet et de bridages, la plage de mesure minimale requise peut être nettement plus grande que les dimensions de la pièce.
Comme règle de base concernant les dimensions adaptées de la MMT, veillez à choisir une machine dont les plages de mesure, sur les axes X, Y et Z, représentent le double de la largeur, de la longueur et de la hauteur de la plus grande pièce que vous devez mesurer.
Le deuxième critère de sélection est l’incertitude minimale requise. Les incertitudes et les procédures de test pour les MMT sont décrites dans la norme ISO 10360:-2. Certains fabricants de MMT ne se conforment pas à ISO 10360-2, mais s'appuient sur d'autres normes, telles que CMMA, VDI/VDE 2617, B89 et JIS (Voir le chapitre Comprendre les standards de performance des MMT, page 6). Cependant, pour comparer des MMT de différents fabricants, assurez-vous de comparer des spécifications similaires. La plupart des fabricants de MMT proposent déjà des spécifications dans différents formats pour répondre aux besoins de la clientèle. En plus, si vous êtes un fabricant international, il peut s'avérer prudent de demander les spécifications des MMT dans le format ISO 10360-2, puisque cette norme devient un standard mondial. Cela vous permettra non seulement de comparer les produits concurrents, mais aussi de comparer la nouvelle machine avec les systèmes existants que vous avez installés à travers le monde.
ISO 10360-2, en vigueur depuis 1994, spécifie deux incertitudes, l’incertitude de mesure de longueur volumétrique (E) et l’incertitude de palpage volumétrique (R).
Pour vérifier l’incertitude de mesure de longueur volumétrique d’une MMT, on utilise diverses cales-étalons ou un calibre en escalier. L’utilisateur choisit sept emplacements (position et direction) dans le volume de mesure MMT pour le test.
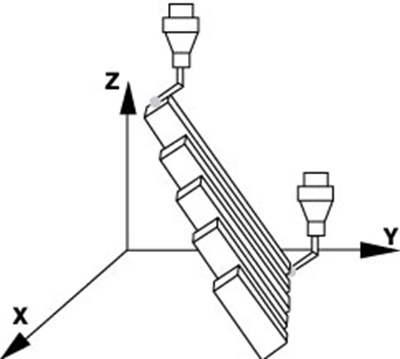
Pour chacun des sept emplacements, cinq standards matériels (longueurs) sont mesurés trois fois, chacun pour 105 mesures au total. Les 105 résultats de mesure, soit 100 pour cent, doivent se situer dans la tolérance spécifiée par le fabricant.
On utilise une sphère de précision entre 10 et 50 mm, avec une certification de forme et de précision, pour vérifier l’incertitude de palpage d'une MMT. Le test consiste à mesurer 25 points de la sphère, espacés régulièrement. R est calculé en additionnant les valeurs absolues de l’écart minimum et maximum par rapport à la forme radiale. Le résultat est exprimé en micromètres (µm), et il faut tenir compte des 25 palpages dans le calcul.
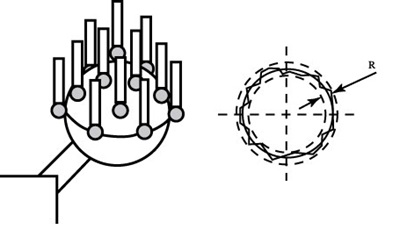
Ces tests sont très spécifiques au niveau de la définition et de l’exécution. Il est important de se rappeler qu’une incertitude de MMT établie dans les conditions d’utilisation réelles peut être supérieure à celle spécifiée par le fabricant en raison de l’utilisation de rallonges de palpeur, de palpeurs longs ou fins, de plateaux tournants, de têtes de mesure rotatives, de la présence de variations de température et de contaminants contenus dans l’air de l’atelier.
Par exemple, si E et R sont déterminés avec un stylet fixé directement dans la tête de mesure, sans rallonge et sans rotation. Mais la plupart des pièces exigent des configurations de palpage complexes pour lesquelles E et R ne sont pas spécifiés. Une pièce peut imposer la combinaison de différentes tiges de palpage, de rallonges, la rotation de la tête de mesure et peut-être un changement de palpeur pendant l’exécution du programme d’inspection.
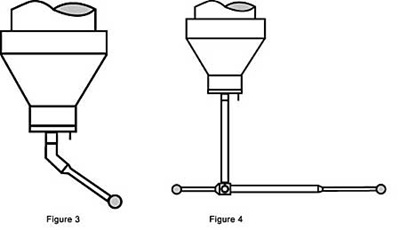
En raison de ces différences, la pratique généralement acceptée consiste à appliquer un rapport d’incertitude à la tolérance lorsque l’on détermine la spécification requise d’une MMT. Ce rapport peut varier considérablement en fonction des facteurs décrits ci-dessus, de la complexité de la tâche de mesure et du processus lui-même. Les rapports habituels vont de 1:3 à 1:20, les rapports 1:5 et 1:10 étant les plus courants. Afin de maintenir un rapport d’incertitude de 1:5 pour la tolérance de la pièce, les spécifications de la fiche technique de la MMT doivent être cinq fois plus précises que la tolérance inspectée.
Sur presque toutes les pièces usinées, les MMT doivent inspecter trois groupes de caractéristiques, des diamètres et des distances, les tolérances de position et les tolérances de forme. Il faut analyser l’incertitude requise pour chaque groupe.
Pour les tolérances de diamètre et de distance, se référer au plan de la pièce et repérer le diamètre pour les distances ayant les tolérances les plus serrées. Compte tenu de la dépendance à la longueur de l’incertitude volumétrique, une plus grande tolérance sur un élément très long peut présenter plus de difficultés qu'une tolérance étroite sur un petit élément. La figure 5 montren comment calculer l’incertitude de mesure de longueur volumétrique requise.
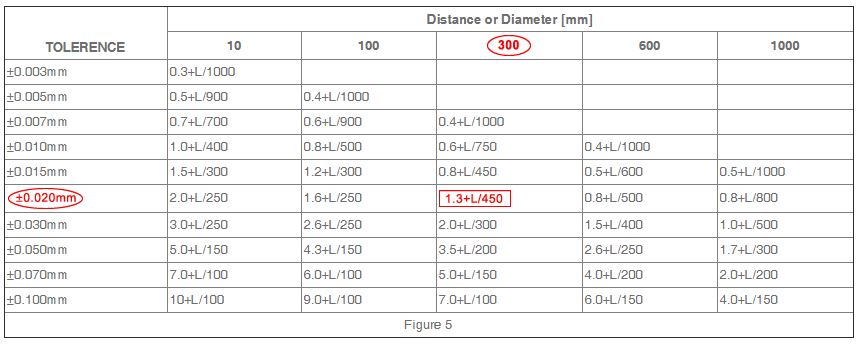
Comme les tolérances de position définissent en général un diamètre de tolérance, seul le rayon est utilisé pour déterminer l’écart par rapport au centre nominal. La figure 6 montre la méthode utilisée pour calculer l’incertitude requise sur la machine.
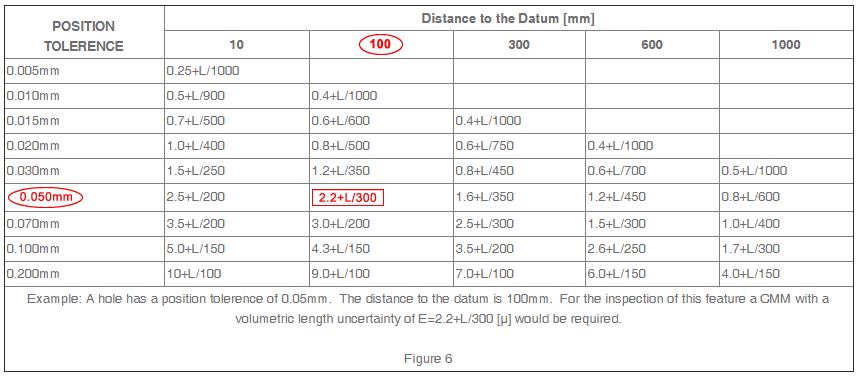
Les tolérances de forme incluent des spécifications de circularité, de planéité, de rectitude, de cylindricité et de profil.
La figure 7 montre le calcul de l’incertitude de mesure de machine pour les tolérances de forme.
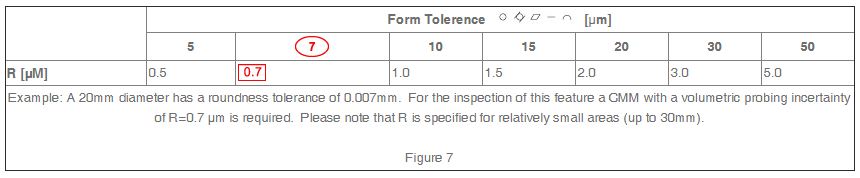
L'incertitude de chaque MMT dépend en grande partie des conditions environnementales. Par conséquent, les fabricants de MMT spécifient habituellement la plage de température, la variation de température par heure, la variation de température par jour et la variation de température par mètre dans lesquelles une MMT donnée atteint la performance spécifiée. Il faut tenir compte de ces variables lors de la sélection d'une MMT appropriée.
Par ailleurs, le niveau de vibration du sol est important pour optimiser la performance de la MMT. La plupart des fabricants fournissent l’amplitude maximale des vibrations que la machine peut supporter en respectant les spécifications définies. Vous pouvez aussi acheter des systèmes d’amortissement de vibrations passifs permettant à la machine d’être installée dans un environnement difficile et de se conformer aux spécifications établies. Il est important d’effectuer une étude complète des vibrations sismiques au lieu d’installation choisi, si vous pensez que les vibrations peuvent poser des problèmes.
Tous les fabricants de MMT proposent un logiciel pour des miniprogrammes de mesure de base. Certains fournissent aussi un logiciel pour des pièces présentant des géométries plus complexes, telles que des pignons coniques, des turbines, des compresseurs à vis et des fraises-mères, pour en citer quelques-unes. Assurez-vous de comprendre la complexité du miniprogramme de mesure nécessaire pour inspecter vos pièces et de sélectionner le package logiciel qui effectuera les tâches de mesure nécessaires.
Les caractéristiques de rendement sont également importantes. Plus une MMT peut inspecter de pièces par jour, plus les coûts d’examen par pièce sont bas. L’accélération et le nombre de points de palpage par minute sont les facteurs qui déterminent le rendement global. Vous pouvez aussi accroître le rendement au moyen de systèmes de bridage spéciaux, tels que les inspections de pièces sur palettes.
Le choix de la MMT la plus appropriée pour l’application exige une certaine réflexion et une certaine recherche, mais vous n’avez pas besoin de le faire tout seul. Les fabricants de MMT comme Hexagon emploient des spécialistes qui vous aideront à choisir la MMT la mieux adaptée à vos exigences.