Jak wybrać właściwą współrzędnościową maszynę pomiarową (CMM)
Odpowiednia maszyna CMM stanowi istotę czynności pomiarowych
Kontakt

Kontrola procesu pomiarowego i zapewnienie jakości w nowoczesnej produkcji w dużej mierze zależy od wydajności współrzędnościowych maszyn pomiarowych (CMM). Ponad 20 lat temu maszyny CMM zajęły miejsce tradycyjnych metod pomiarowych wykorzystujących sprawdziany oraz instrumenty pomiarowe, skracając czas oraz zmniejszając wysiłek ludzki wymagany w procesie kontroli jakości.
Współrzędnościowe maszyny pomiarowe nie tylko umożliwiają kontrolę standardowych wymiarów geometrycznych, ale również specjalnych cech, takich jak koła zębate, wały korbowe, kształty profili lotniczych i wiele innych. W tradycyjnym środowisku przemysłowym każda z tych specjalnych kontroli wymagałaby osobnej maszyny pomiarowej do realizacji poszczególnych zadań metrologicznych.
Jakość produktu nie zależy jedynie od jakości obrabiarek wykorzystywanych w produkcji – zależna jest również od dokładności i powtarzalności pomiarowej urządzeń metrologicznych. Tanie i mało wydajne centrum obróbki w połączeniu z bardzo precyzyjną maszyną CMM wciąż może gwarantować wysoką jakość produktu, ponieważ jedynie części mieszczące się w granicach tolerancji mogą przejść pozytywnie kontrolę przeprowadzaną za pomocą współrzędnościowej maszyny pomiarowej. Odwrotnie jest w przypadku drogiego, wysokojakościowego centrum obróbki, które w połączeniu z tanim, mało precyzyjnym urządzeniem pomiarowym nie może zagwarantować jakości produktów. Pewien odsetek części poza zakresem tolerancji zawsze pozytywie przejdzie kontrolę przeprowadzaną za pomocą mało dokładnej maszyny CMM. I odwrotnie - pewien procent części w granicach tolerancji zostanie odrzuconych. A zatem wybór odpowiedniej współrzędnościowej maszyny pomiarowej ma naprawdę zasadnicze znaczenie. Opracowanie to ma pomóc naszym klientom w wyborze odpowiedniej maszyny CMM, która spełnia indywidualne wymagania dotyczące dokładności pomiarowych i zastosowań.
Pierwszym ważnym kryterium klasyfikacji jest minimalny zakres pomiarowy współrzędnościowej maszyny pomiarowej. Zakres ten zazwyczaj zależy od wymiarów mierzonej części, ale nie tylko. Na przykład, jeśli konfiguracja części oraz czynności kontrolnych wymaga wykorzystania przedłużek sondy oraz specjalnych uchwytów, rzeczywisty minimalny wymagany zakres pomiarowy może być znacznie większy niż wymiary części.
Wybór właściwego rozmiaru maszyny CMM opiera się na następującej zasadzie: należy wybrać maszynę, której zakres pomiarowy osi X, Y, Z stanowi dwukrotność szerokości, długości i wysokości największej mierzonej części.
Drugim kryterium jest minimalna wymagana niepewność pomiarowa. Niepewności oraz procedury kontrolne dla maszyn CMM określa norma ISO 10360-2. Niektórzy producenci maszyn CMM nie stosują normy ISO 10360-2, ale działają zgodnie z międzynarodowymi normami CMMA, VDI/VDE 2617, B89 oraz JIS (Patrz: Normy działania maszyn CMM, strona 6). Jednak przy porównaniu współrzędnościowych maszyn pomiarowych rożnych producentów, pod uwagę należy wziąć również specyfikacje. Większość producentów CMM oferuje swoje specyfikacje w różnorodnych formatach, aby wyjść na przeciw potrzebom swoich klientów z całego świata. Jeśli jesteś wytwórcą działającym na rynku międzynarodowym, domagaj się specyfikacji maszyny CMM zgodnych z normą ISO 10360-2. Norma ta niebawem będzie powszechnie stosowana na całym świecie. Dzięki temu nie tylko wybierzesz odpowiedniego producenta, ale również porównasz nową maszynę z urządzeniami używanymi obecnie na świecie.
Obowiązująca od 1994 roku norma ISO 10360 określa dwie niepewności - błąd pomiaru długości (E) oraz błąd układu przejmowania punktów (głowicy)(R).
Aby wyznaczyć błąd pomiaru długości maszyny CMM stosowane są wzorce stopniowe lub zestawy płytek wzorcowych. Użytkownik ustawia wzorzec długości w 7 różnych pozycjach (pozycja i kierunek) w przestrzeni pomiarowej maszyny CMM.
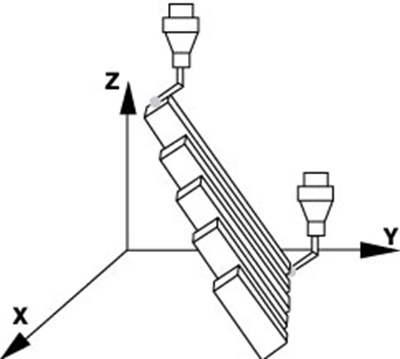
Sprawdzenie głowic pomiarowych (wyznaczenie niepewności pomiarowej CMM)polega na zmierzeniu wzorca sferycznego o średnicy nie mniejszej niż 10 mm i nie większej niż 50 mm. Test polega na kontroli 25 równomiernie rozłożonych punktów pomiarowych wzorca sferycznego. Dla każdego z punktów pomiarowych należy wyznaczyć promień od środka elementu skojarzonego i z uzyskanych wyników obliczyć wartość R (poprzez dodanie wartości bezwzględnych minimalnej i maksymalnej odchyłki). Wynik podawany jest w mikrometrach (µm). Błąd wyznaczany jest z wszystkich 25 punktów.
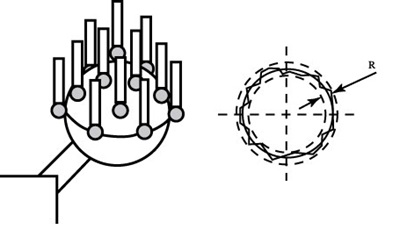
Na przykład niepewność E oraz R jest wyznaczana za pomocą jednego trzpienia przymocowanego bezpośrednio do głowicy pomiarowej, bez przedłużek oraz bez możliwości obracania. Jednak większość części wymaga złożonych konfiguracji sond, dla których niepewność E oraz R nie została określona. Mierzona część może wymagać zastosowania kilku końcówek pomiarowych, przedłużek, obrotowej głowicy pomiarowej, a być może również wymiany sondy podczas realizacji programu kontroli.
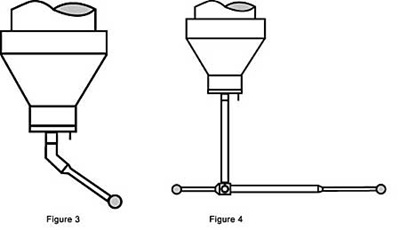
W przypadku niemal wszystkich części, współrzędnościowe maszyny pomiarowe muszą zmierzyć trzy grupy cech - średnice oraz odległości, tolerancje położenia i kształtu. Dla każdej grupy należy przeprowadzić analizę wymaganej niepewności.
W przypadku tolerancji średnicy i odległości należy odnieść się do rysunku części i odnaleźć średnicę dla odległości w granicach najbardziej ścisłych tolerancji. Z powodu zależności niepewności pomiaru od długości, większe tolerancje na bardzo długim elemencie mogą sprawiać więcej trudności niż najbardziej ścisłe tolerancje małego elementu. Poniżej przedstawiamy jak można obliczyć wymagany błąd pomiaru długości.
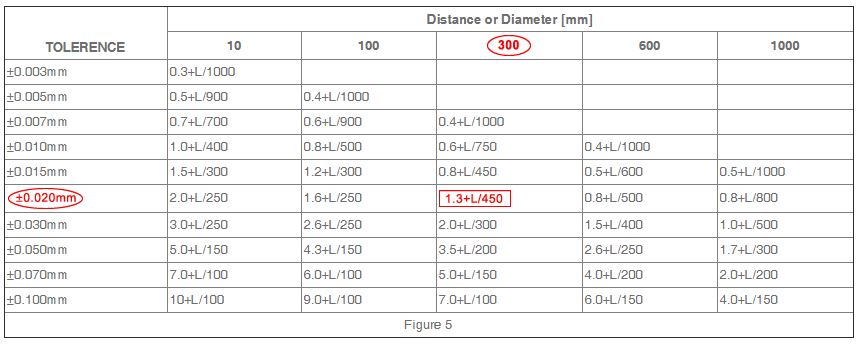
Ponieważ tolerancje położenia zazwyczaj definiują tolerancję średnicy, odchyłkę od środka nominalnego określamy jedynie na podstawie promienia. Poniżej przedstawiamy jak można obliczyć wymaganą niepewność maszyny.
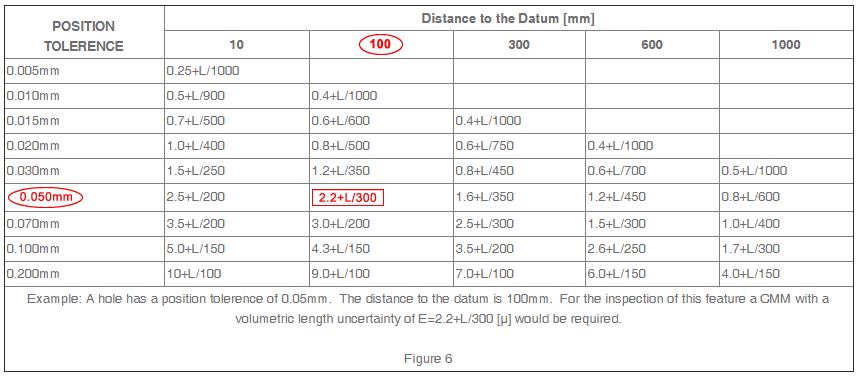
Przykład: Otwór ma tolerancję położenia 0.05mm. Odległość względem układu odniesienia wynosi 100mm. Dla zmierzenia tej cechy wymagana będzie maszyna CMM z błędem pomiaru długości E=2.2+L/300 [µ]
Tolerancje kształtu obejmują odwołania do okrągłości, płaskości, prostoliniowości, walcowatości oraz profilu.
Poniżej przedstawiamy jak można obliczyć wymaganą niepewność pomiarową maszyny dla tolerancji kształtu.
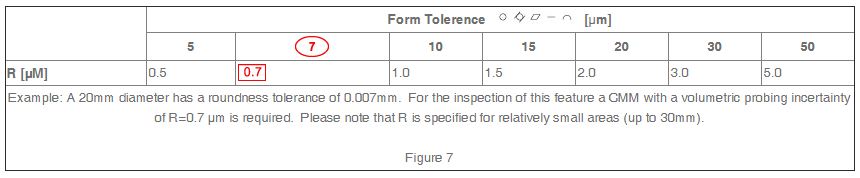
Przykład: 20 mm średnica posiada tolerancję okrągłości 0.007mm. Aby dokonać kontroli tej cechy wymagane będzie zastosowanie maszyny CMM z błędem układu przejmowania punktów (głowicy) R=0.7. Proszę wziąć pod uwagę, że błąd R został wyznaczony dla relatywnie małych obszarów (do 30 mm).
Niepewność każdej współrzędnościowej maszyny pomiarowej w dużej mierze zależy od warunków środowiskowych. Dlatego producenci maszyn CMM zazwyczaj określają zakres temperatur, wahania temperatury na godzinę, wahania temperatury na dzień, wahania temperatury na metr, w których dana współrzędnościowa maszyna pomiarowa osiąga swoje specyfikacje wydajnościowe (techniczne). Te wahania należy wziąć pod uwagę podczas wyboru odpowiedniej maszyny CMM.
Również poziom drgań posadzki jest ważny dla optymalnego działania współrzędnościowej maszyny pomiarowej. Większość producentów określa maksymalny poziom drgań, które maszyna jest w stanie znieść i wciąż spełniać określone specyfikacje. Opcjonalnie można nabyć aktywny i pasywny układ tłumiący drgania, który pozwala na instalację urządzenia w mniej przyjaznym środowisku. Dzięki niemu maszyna będzie działać zgodnie ze swoimi specyfikacjami. Ważne jest, aby przeprowadzić pełne badania dotyczące drgań sejsmicznych w preferowanym miejscu instalacji, jeśli uważamy, że drgania mogą stanowić problem.
Wszyscy producenci maszyn CMM dostarczają podstawowe oprogramowanie metrologiczne do przeprowadzania prostych czynności pomiarowych. Niektórzy oferują również program do kontroli bardziej skomplikowanych kształtów geometrycznych, takich jak m.in. stożkowe koła zębate, wirniki, sprężarki śrubowe oraz frez ślimakowy. Dowiedz się, jak bardzo skomplikowanych pomiarów potrzebujesz dla swoich części i wybierz właściwe oprogramowanie, które pomoże Ci zrealizować niezbędne zadania metrologiczne.
Należy wziąć pod uwagę także wymagania odnośnie wydajności. Im więcej elementów maszyna CMM może dziennie zmierzyć, tym niższy koszt kontroli jednej części. Przyspieszenie oraz ilość zbieranych punktów pomiarowych na minutę również mają wpływ na ogólną wydajność urządzenia. Wydajność można zwiększyć dzięki specjalnym funkcjom, takim jak kontrola części na paletach.
Wybór odpowiedniej współrzędnościowej maszyny pomiarowej, dzięki której możliwa będzie realizacja zadań pomiarowych, wymaga nie tylko zastanowienia, ale również zbadania rynku metrologicznego. Nie musisz robić tego sam. Producenci maszyn CMM, tacy jak firma Hexagon Manufacturing Intelligence, zatrudniają specjalistów, którzy pomogą Ci wybrać współrzędnościową maszynę pomiarową na miarę Twoich potrzeb.