Bir CMM Nasıl Seçilir
Ölçüm İşlemlerindeki Tüm Fark Doğru CMM Seçiminden geçer.
Bize ulaşın

Modern üretim faaliyetlerinde süreç kontrol ve kalite güvence, giderek artan bir şekilde koordinat ölçüm cihazlarının (CMM'ler) performansına bağlı olmaktadır. CMM'ler, son 20 yılda mastar ve fikstürlere dayalı geleneksel denetim yöntemlerinin yerini almış ve kalite kontrol işlemlerinde gerekli olan zaman ve işçiliği azaltmıştır.
CMM'ler yalnızca standart geometrik boyutları ölçmekle kalmaz, dişliler, kam milleri ve diğer farklı özellikleri olan parçaları denetlemek için gerekli yeteneği de sağlar. Geleneksel bir üretim ortamında ise bu özel ölçümlerin her biri için tek amaçlı farklı test makinesi gerekmektedir.
Ürün kalitesi üretim için kullanılan takım tezgahının kalitesine bağlı olmakla kalmaz, aynı zamanda ölçüm ve denetim cihazlarının doğruluğuna ve tekrarlanabilirliğine dayanır. Düşük maliyetli ve düşük performanslı bir makineyle işleme merkeziyle birlikte yüksek hassasiyete sahip bir CMM yine de ürün kalitesini garanti edebilir, çünkü yalnızca tolerans içindeki parçalar CMM'nin denetimini geçebilmektedir. Bunun aksine, pahalı, yüksek kaliteli bir makineyle işleme merkeziyle birlikte düşük maliyetli, düşük doğruluğa sahip bir ölçüm cihazı, ürünlerin kalitesini garanti edemez. Tolerans dışında olan parçaların belirli bir yüzdesi, düşük doğruluğa sahip CMM denetiminden daima geçebilecektir ve benzer şekilde, tolerans aralığındaki parçaların belirli bir yüzdesi de reddedilecektir. Bu nedenle, doğru CMM seçimi kritik bir karardır. Bu yazının amacı, özel doğruluk ve uygulama gereksinimlerinizi karşılayan bir CMM seçmenize yardımcı olmaktır.
İlk önemli seçim kriteri, CMM'in minimum gerekli ölçüm aralığının belirlenmesidir. Bu aralık genellikle ölçülecek parçanın boyutlarına bağlıdır, ancak çoğu durumda bundan daha karmaşıktır. Örneğin, parçanın ve ölçüm rutininin konfigürasyonu, prob uzantılarının ve fikstürlerinin kullanımını gerektiriyorsa, gerekli minimum fiili ölçüm aralığı, iş parçasının boyutlarından bir hayli büyük olabilir.
CMM'nizi düzgün bir şekilde boyutlandırmak için bir rehber olarak, X, Y ve Z ölçüm aralıkları ölçmeniz gereken en büyük parçadan iki katı genişliğe, uzunluğa ve yüksekliğe sahip bir makine seçmeyi düşünün.
İkinci seçim kriteri, gerekli minimum belirsizliktir. CMM'ler için belirsizlikler ve test prosedürleri ISO 10360-2'de tarif edilmiştir. Bazı CMM üreticileri ISO 10360-2'ye uymamakta, ancak CMMA, VDI/VDE 2617, B89, ve JIS (Bkz. CMM Performans Standartlarını Anlamak, sayfa 6) gibi diğer performans standartlarını kullanmaktadır. Ancak farklı üreticilerin CMM'lerini karşılaştırabilmek için, benzer özellikleri değerlendirdiğinizden emin olun. Çoğu CMM üreticisi, uluslararası müşteri tabanlarını desteklemek için özelliklerini zaten değişik formatlarda sunmaktadır. Ek olarak, uluslararası bir üreticiyseniz, tedbirli olmak için CMM'in özelliklerini ISO 10360-2 formatında istemeniz iyi olabilir, çünkü bu format bir dünya standardı haline gelmektedir. Bu, rakipler arasında karşılaştırma yapmanızı sağlamakla kalmaz, aynı zamanda yeni makinenizi dünya çapında kurulu bulunan mevcut makinelerinizle karşılaştırmanızı sağlar.
1994 yılından beri yürürlükte olan ISO 10360-2 iki belirsizlik tarif eder: hacimsel uzunluk ölçüm belirsizliği (E) ve hacimsel problama belirsizliği (R).
Bir CMM'in hacimsel uzunluk ölçüm belirsizliğini doğrulamak için bir dizi mastar veya step gage kullanılır. Kullanıcı, test için CMM'in ölçüm hacmi içinde yedi farklı yer (konum ve yön) seçer.
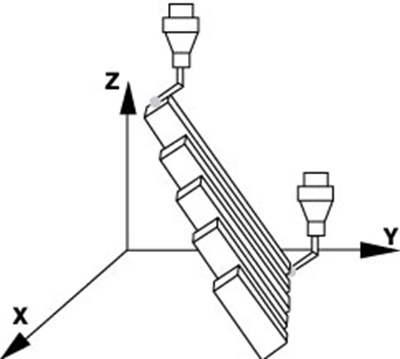
Bir CMM'in problama belirsizliğini doğrulamak için biçim ve çap sertifikasyonuna sahip 10 mm ile 50 mm arasındaki bir referans küresi kullanılır. Test, küre üzerinde aralarında eşit mesafe bulunan 25 noktanın ölçülmesinden oluşur. R, radyal biçimden minimum ve maksimum sapmaların mutlak değerlerinin toplanmasıyla hesaplanır. Sonuç mikrometre (µm) cinsinden rapor edilir ve hesaplamada 25 problamanın tamamı kullanılmalıdır.
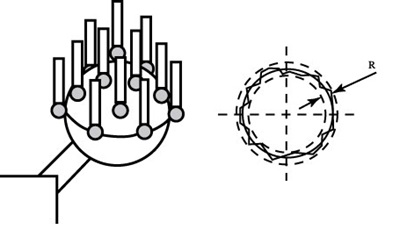
Örneğin belirtilen E ve R, hiçbir uzantı ve rotasyon olmaksızın doğrudan prob başına sabitlenen bir prob ucu tarafından belirlenir. Ancak çoğu iş parçası E ve R'nin belirtilmemiş olduğu karmaşık prob konfigürasyonları gerektirmektedir. Bir iş parçası, denetim programı sırasında birkaç prob ucu, uzatma, prob kafası rotasyonu ve belki de bir prob değişikliğinin bir kombinasyonunu gerektirebilir.
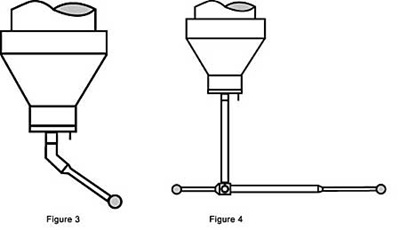
Hemen hemen tüm iş parçalarında, CMM'ler üç grup özellik-boyut ve mesafe, pozisyon toleransları ve biçim toleranslarını denetlemelidir. Her bir grup için istenen belirsizliğin analizi gerçekleştirilmelidir.
Çap ve mesafe toleransları için, parça çizimine bakın ve en katı toleranslara sahip mesafeler için olan çapları bulun. Hacimsel belirsizliğin uzunluk bağımlılığı nedeniyle, çok uzun bir özelliğin daha yüksek toleransı, küçük bir özellikteki daha katı bir toleranstan daha fazla zorluğa neden olabilir. Gerekli makine hacimsel uzunluk ölçüm belirsizliğinin nasıl hesaplanacağını gösterir.
TOLERANS Mesafe veya Çap [mm]
10 100 600 1000
±0,003mm 0,3+L/1000
±0,005mm 0,5+L/900 0,4+L/1000
±0,007mm 0,7+L/700 0,6+L/900 0,4+L/1000
±0,010mm 1,0+L/400 0,8+L/500 0,6+L/750 0,4+L/1000
±0,015mm 1,5+L/300 1,2+L/300 0,8+L/450 0,5+L/600 0,5+L/1000
±0,030mm 3,0+L/250 2,6+L/250 2,0+L/300 1,5+L/400 1,0+L/500
±0,050mm 5,0+L/150 4,3+L/150 3,5+L/200 2,6+L/250 1,7+L/300
±0,070mm 7,0+L/100 6,0+L/100 5,0+L/150 4,0+L/200 2,0+L/200
±0,100mm 10+L/100 9,0+L/100 7,0+L/100 6,0+L/150 4,0+L/150
Pozisyon toleransları genellikle bir tolerans çapını tanımladığı için, nominal merkezden sapmayı belirlemek için yalnızca yarıçap kullanılır. Gerekli makine belirsizliğini hesaplamak için kullanılan yöntemi gösterir.
POZİSYON
TOLERANS Referans noktasına olan Mesafe [mm]
10 image4.jpg 300 600 1000
0,005mm 0,25+L/1000
0,010mm 0,5+L/900 0,4+L/1000
0,015mm 0,7+L/500 0,6+L/600 0,4+L/1000
0,020mm 1,0+L/400 0,8+L/500 0,6+L/750 0,4+L/1000
0,030mm 1,5+L/250 1,2+L/350 0,8+L/450 0,6+L/700 0,5+L/1000
1,6+L/350 1,2+L/450 0,8+L/600
0,070mm 3,5+L/200 3,0+L/200 2,5+L/300 1,5+L/300 1,0+L/400
0,100mm 5,0+L/150 4,3+L/150 3,5+L/200 2,6+L/250 1,7+L/300
0,200mm 10+L/100 9,0+L/100 7,0+L/100 6,0+L/150 4,0+L/150
Örnek: Bir delik, 0,05mm'lik bir pozisyon toleransına sahiptir. Referans noktasına olan mesafe 100mm'dir. Bu özelliğin denetlenmesi için hacimsel uzunluk belirsizliği E= 2.2 + L/300 [µ] olan bir CMM gereklidir.
Form toleransları; dairesellik, düzlemsellik, doğruluk, silindirlik ve profil formu için çağrılar içerir.
Form toleransları için makine ölçüm belirsizliğinin hesaplanmasını gösterir.
Form Toleransı [µm]
10 15 20 30 50
R [µM] 1,0 1,5 2,0 3,0 5,0
Örnek: 20mm'lik bir çap, 0,007mm'lik bir dairesellik toleransına sahiptir. Bu özelliğin ölçülmesi için, hacimsel problama belirsizliği R=0,7 µm olan bir CMM gereklidir. R'nin göreli olarak küçük alanlar için belirtilmiş olduğunu lütfen unutmayın (30mm'ye kadar).
Her CMM'in belirsizliği büyük ölçüde çevresel koşullara bağladır. Bu nedenle, CMM üreticileri genellikle, belirli bir CMM'in performans özelliklerini yerine getirdiği sıcaklık aralığını, saat başına sıcaklık değişimini, gün başına sıcaklık değişimini ve metre başına sıcaklık değişimini belirtir. Uygun CMM seçilirken bu değişkenler hesaba katılmalıdır.
Ek olarak, CMM'in performansını optimize etmek için zemin titreşimi seviyesini hesaba katmak önemlidir. Çoğu üretici makinenin dayanabildiği ve belirtilen özelliklerini karşılamaya devam ettiği maksimum titreşimi belirtir. Makinenin zorlu ortamlarda da kurulmasını ve yayımlanan özelliklerini yerine getirmesini sağlayan opsiyonel aktif ve pasif titreşim damping sistemleri de satın alınabilir. Titreşimin bir sorun olduğunu düşünüyorsanız, tercih edilen kurulum yerinde tam bir sismik titreşim araştırmasının yapılması önemlidir.
Tüm CMM üreticileri temel ölçüm rutinleri için yazılım sunmaktadır. Bazıları, konik dişliler, kanatlar, vida kompresörleri ve freze çakıları gibi karmaşık geometrileri olan parçalar için de yazılım sunmaktadır. Parçalarınızı ölçmek için gerekli ölçüm rutininin karmaşıklığını anladığınızdan ve gerekli ölçüm görevlerini yerine getirecek yazılım paketini seçtiğinizden emin olun.
Verimlilik gereksinimleri de göz önünde bulundurulmalıdır. Bir CMM günde ne kadar çok parça denetleyebilirse, parça başına denetim maliyeti o kadar azalır. İvme ve dakikada problama noktası sayısı, genel verimliliği belirleyen faktörlerdir. Verimlilik aynı zamanda, parçaların palet denetlenmesi gibi özel fikstürleme düzenlemeleriyle de artırılabilir.
Uygulamanız için en uygun CMM'nin seçilmesi bir miktar üzerinde düşünme ve araştırma gerektirir, ancak hepsini tek başınıza yapmanız gerekmez. Hexagon Manufacturing Intelligence gibi CMM üreticileri, ihtiyaçlarınıza en uygun CMM'yi seçmenize yardımcı olmak için sizinle birlikte çalışacak uzmanlara sahiptir.