Come scegliere una CMM
La giusta CMM è fondamentale per le operazioni di misura.
Contattateci

Il controllo di processo e l'assicurazione qualità nelle moderne aziende manifatturiere dipendono in misura crescente dalle prestazioni delle macchine di misura a coordinate (CMM). Nel corso degli ultimi 20 anni le CMM hanno sostituito i tradizionali metodi di verifica basati su calibri e attrezzi, riducendo il tempo e la manodopera necessaria alle attività di controllo qualità.
Le CMM offrono non solo la capacità di verificare elementi geometrici comuni ma anche geometrie complesse come dentature, alberi a camme, profili e molti altri. In un ambiente produttivo tradizionale, ciascuna di queste verifiche speciali richiederebbe una macchina dedicata.
La qualità del prodotto non dipende solo dalla qualità delle macchine utensili usate per la produzione; dipende anche dalla precisione e ripetibilità dei dispositivi di misura e verifica. Un centro di lavoro di basso costo e prestazioni ridotte unito a una CMM di alta precisione può comunque garantire la qualità del prodotto perché saranno solo i componenti in tolleranza a passare la verifica della CMM. Viceversa, un centro di lavoro costoso e di qualità elevata unito a un apparecchio di misura di basso costo e bassa precisione non può garantire prodotti di qualità. Una certa percentuale di componenti fuori tolleranza passerà sempre la verifica della CMM di bassa precisione e analogamente una certa percentuale di componenti entro la fascia di tolleranza verrà scartata. Ne consegue che la scelta della giusta CMM è una decisione molto importante. Lo scopo di questo articolo è quello di fornire un aiuto per la scelta di una CMM che soddisfi le specifiche esigenze applicative e di precisione.
Il primo importante criterio di scelta è la determinazione della corsa di misura minima della CMM. Questa corsa generalmente dipende dalle dimensioni del componente da misurare ma spesso è una definizione più complessa. Se ad esempio la configurazione del pezzo e la procedura di verifica richiedono l'impiego di prolunghe del sensore e di attrezzaggi, la corsa effettiva necessaria potrebbe essere notevolmente maggiore delle dimensioni del pezzo.
A titolo indicativo, per stabilire correttamente le dimensioni della vostra CMM, considerate corse X, Y e Z di larghezza doppia e di altezza pari al pezzo più grande che dovete misurare.
Il secondo criterio di scelta è l'incertezza minima richiesta. Le incertezze e le procedure di verifica per le CMM sono descritte nella ISO 10360-2. Alcuni costruttori di CMM non sono conformi alla ISO 10360-2 ma impiegano norme sulle prestazioni come la CMMA, VDI/VDE 2617, B89, e JIS (Vedi Understanding CMM Performance Standards, a pagina 6). Se si confrontano CMM di costruttori diversi, tuttavia, si deve esser certi che le specifiche siano identiche. La maggior parte dei produttori offre già le proprie specifiche in svariati formati per supportare la propria base clienti internazionale. Inoltre se siete un produttore internazionale può essere opportuno richiedere le specifiche della CMM in formato ISO 10360-2, dato che questo sta diventando lo standard mondiale. Questo vi permetterà non solo di confrontarvi con i vostri concorrenti ma anche di confrontare la nuova macchina con le vostre macchine installate in varie parti del mondo.
La ISO 10360-2, in vigore dal 1994, specifica due incertezze: l'incertezza di misura longitudinale volumetrica (E) e l'incertezza di rilevamento volumetrica (R).
Per verificare l'incertezza di misura longitudinale volumetrica di una CMM, viene impiegata una serie di blocchetti pianparalleli o uno step gage. Per la verifica, l'utente sceglierà sette posizioni diverse (posizione e direzione) all'interno del volume di misura della CMM.
Per ciascuna delle sette posizioni, si misurano cinque campioni dimensionali (lunghezze) tre volte ciascuno per un totale di 105 misure. Tutti i 105 risultati di misura, il 100%, devono risultare all'interno della tolleranza specificata dal costruttore.
Per verificare l'incertezza di rilevamento di una CMM, si impiega una sfera di precisione di 10 - 50 mm con forma e diametro certificati. Il test consiste nella misura di 25 punti a uguale distanza sulla sfera. R viene calcolato sommando i valori assoluti dello scostamento minimo e massimo dalla forma radiale. Il risultato viene riportato in micron (µm), e tutti i 25 rilevamenti dovranno essere considerati nel calcolo.
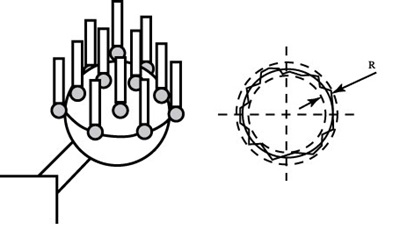
Questi test sono molto specifici sia nella definizione sia nello svolgimento. È importante ricordare che l'incertezza di una CMM nelle condizioni operative effettive può essere maggiore di quando indicato nelle specifiche del produttore a causa dell'impiego di prolunghe del sensore, sensori lunghi o sottili, tavole rotanti, teste di misura orientabili, variazioni di temperatura e inquinanti atmosferici in officina.
Ad esempio, E ed R come specificati sono determinati da uno stilo fissato direttamente sulla testa di misura senza prolunghe né rotazione. Molti pezzi tuttavia richiedono complesse configurazioni del sensore per le quali E ed R non vengono specificati. Un pezzo potrebbe richiedere la combinazione di diverse punte, prolunghe, rotazione della testa di misura e magari un cambio tastatore nel corso del programma di misura.
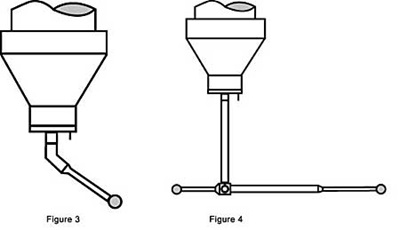
A causa di queste differenze, la prassi generalmente accettata è quella di applicare un quoziente di incertezza alla tolleranza nel calcolare le specifiche di una CMM. Questo quoziente può variare ampiamente a seconda dei fattori appena descritti, della complessità dell'operazione di misura e del processo stesso. I quozienti tipici vanno da 1:3 a 1:20, mentre i più comuni sono 1:5 e 1:10. Allo scopo di mantenere un rapporto di incertezza di 1:5 per la tolleranza del pezzo, le specifiche della CMM dovrebbero essere cinque volte più precise della tolleranza che si sta verificando.
Su quasi tutti i pezzi le CMM devono verificare tre gruppi di elementi-diametri e distanze, tolleranze di posizione e tolleranze di forma. L'analisi dell'incertezza richiesta dev'essere eseguita per ogni gruppo.
Per le tolleranze di diametro e distanza, fate riferimento al disegno del pezzo e identificate il diametro per le distanze con le tolleranze più strette. A causa della dipendenza della lunghezza dall'incertezza volumetrica, una tolleranza maggiore su di un elemento geometrico molto lungo può rivelarsi più difficile di una tolleranza molto stretta su di un elemento piccolo. La Figura 5 illustra come calcolare l'incertezza di misura longitudinale volumetrica della macchina.
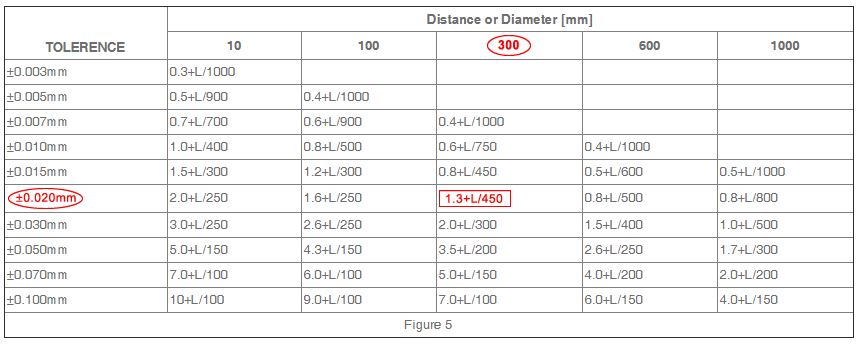
Poiché le tolleranze di posizione definiscono generalmente una tolleranza del diametro, si impiega solo il raggio per determinare lo scostamento dal centro teorico. La Figura 6 illustra il metodo impiegato per calcolare l'incertezza della macchina.
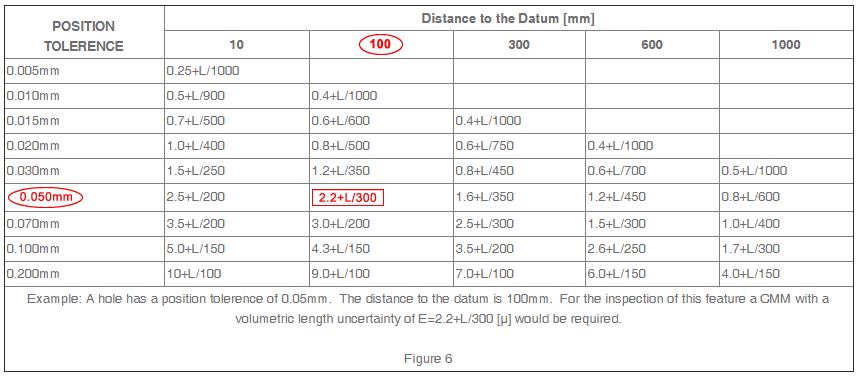
Esempio: Un foro ha tolleranza di posizione di 0.05 mm. La distanza dall'elemento di riferimento è di 100 mm. Per la verifica di questo elemento, sarebbe necessaria una CMM con incertezza longitudinale volumetrica di E=2.2+L/300 [µ].
Le tolleranze di forma comprendono label per rotondità, planarità, linearità, cilindricità e forma del profilo.
La Figura 7 illustra il calcolo dell'incertezza di misura della macchina per le tolleranze di forma.
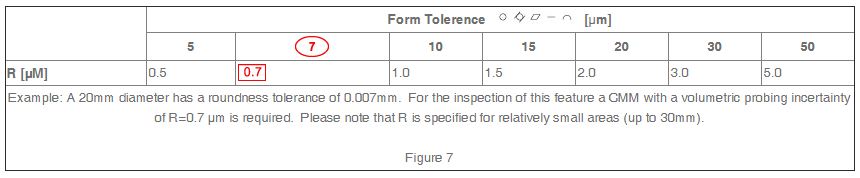
Esempio: Un diametro di 20 mm ha una tolleranza di rotondità di 0,007 mm. Per la verifica di questo elemento è necessaria una CMM con incertezza di rilevamento volumetrico di R=0.7 µm. Si noti che R viene specificato per aree relativamente ridotte (fino a 30 mm).
L'incertezza di ogni CMM dipende in gran parte dalle condizioni ambientali. Di conseguenza i costruttori di CMM generalmente indicano la fascia di temperatura, la variazione oraria di temperatura, la variazione giornaliera di temperatura e la variazione di temperatura per metro entro le quali una determinata CMM raggiunge le prestazioni specificate. È necessario considerare queste variabili per poter scegliere la giusta CMM.
Anche il livello di vibrazioni nel pavimento è importante per ottimizzare le prestazioni della CMM. La maggior parte dei costruttori indica il massimo livello di vibrazioni che la macchina può sopportare nel rispetto delle specifiche. Si possono anche acquistare sisitemi antivibranti attivi e passivi che permettono di installare la macchina in ambienti meno favorevoli, offrendo comunque le prestazioni indicate. È importante avere un'analisi completa delle vibrazioni sismiche, effettuata nel luogo di installazione scelto, se si ritiene che le vibrazioni possano essere un problema.
Tutti i costruttori di CMM forniscono software per le procedure di misura principali. Alcuni forniscono anche software per parti di geometria più complessa, come ruote coniche, giranti, compressori e creatori, per nominarne solo alcuni. È necessario capire la complessità della procedura di misura per scegliere il pacchetto software che eseguirà le operazioni di misura necessarie.
Anche la produttività richiesta va presa in considerazione. Maggiore il numero di pezzi che una CMM può verificare, minore sarà il costo di verifica per ciascun pezzo. L'accelerazione e il numero di punti di rilevamento al minuto sono i fattori che determinano la produttività generale. La produttività può essere aumentata anche con particolari misure di attrezzaggio, come la verifica di pezzi su pallet.
La scelta della CMM più adatta per la propria applicazione richiede riflessione e ricerca ma non è necessario farlo da soli. Costruttori di CMM come Hexagon Manufacturing Intelligence hanno esperti che vi aiuteranno a scegliere la CMM che meglio soddisfa le vostre esigenze.