Como selecionar uma MMC
A MMC certa faz toda a diferença nas operações de medição.
Contato

As proporcionam a capacidade para inspecionar dimensões geométricas padrão, mas também peças com características especiais, como engrenagens, eixos de comando, formas de aerofólio, e muitos outros. Em um ambiente de produção tradicional, cada uma dessas inspeções especiais exigiria uma máquina de teste de único propósito.
A qualidade do produto não depende apenas da qualidade das máquinas-ferramenta utilizadas para a fabricação; ele também depende da precisão e repetibilidade de dispositivos de medição e inspeção. Um centro de usinagem de baixo custo e baixo desempenho em combinação com uma MMC de alta precisão ainda pode garantir a qualidade do produto, porque somente as peças dentro da tolerância pode passar na inspeção da MMC. Por outro lado, um caro, centro de usinagem de alta qualidade em combinação com um baixo custo, dispositivo de medição de baixa precisão não pode garantir produtos de qualidade. Uma certa percentagem de peças fora de tolerância será sempre passar a inspeção MMC baixa precisão, e da mesma forma, uma certa percentagem de peças dentro da faixa de tolerância será rejeitada. Por conseguinte, a seleção da MMC direito é uma decisão crítica. O objetivo deste artigo é ajudá-lo a escolher um MMC que atenda às suas exigências de precisão e de aplicações específicas.
O primeiro critério de seleção importante é a determinação da faixa de medição mínimo exigido da MMC. Esta gama geralmente depende das dimensões da peça a ser medido, mas é muitas vezes mais complexo do que isso. Por exemplo, se a configuração da peça e da rotina de inspeção requerem o uso de extensões de sondas e acessórios, o mínimo exigido faixa de medição real poderia ser consideravelmente maior do que as dimensões da peça.
Como orientação para o dimensionamento correto da MMC, considere a escolha de uma máquina cujo X, Y e Z faixas de medição são o dobro da largura, comprimento e altura da maior parte que você precisa para medir.
O segundo critério de seleção é a incerteza mínima exigida. As incertezas e procedimentos de ensaio para MMCs são descritos na norma ISO 10360-2. Alguns fabricantes de MMCs não estão em conformidade com a norma ISO 10360-2, mas utilizar outros padrões de desempenho, tais como CMMA, VDI / VDE 2617, B89, e JIS (Consulte Entendendo CMM padrões de desempenho, página 6). No entanto, a fim de comparar as MMCs de diferentes fabricantes, certifique-se comparar como especificações. A maioria dos fabricantes de MMC já oferece as suas especificações em uma variedade de formatos para apoiar a sua base de clientes internacionais. Além disso, se você é um fabricante internacional, pode ser prudente para solicitar as especificações do MMC no formato ISO 10360-2, uma vez que está se tornando um padrão mundial. Isto irá permitir-lhe não só comparar entre concorrentes, mas para comparar a nova máquina com suas máquinas existentes instaladas em todo o mundo.
ISO 10360-2, em vigor desde 1994, especifica duas incertezas, incerteza de medição do comprimento (E) e volumétrica de sondagem incerteza (R).
Para verificar volumétrica incerteza de medição do comprimento de um CMM, uma série de blocos de medição ou um medidor de passo são usados. O usuário seleciona sete locais diferentes (posição e direção) dentro volume de medição da CMM para o teste.
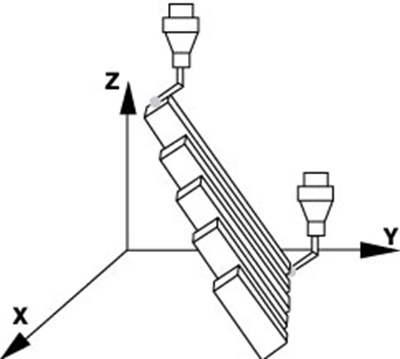
Para cada uma das sete localizações, cinco padrões materiais (comprimentos) são medidos três vezes cada para um total de 105 medições. Todos os resultados de medição 105, 100 por cento, deve estar dentro da tolerância declarada especificado pelo fabricante.
Uma esfera de precisão entre 10 mm e 50 mm, com forma e certificação de diâmetro é utilizado para verificar a incerteza de sondagem de um MMC. O teste consiste em medir 25 pontos igualmente espaçados sobre a esfera. R é calculado pela soma dos valores absolutos do desvio mínimo e máximo a partir da forma radial. O resultado é apresentado em micrómetros (µm), e todos os 25 sondagens deve ser utilizado no cálculo.
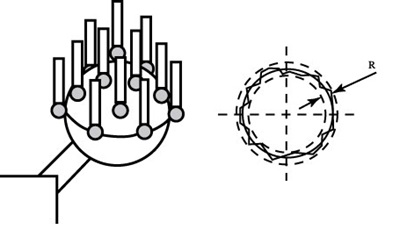
Estes testes são muito específicos tanto na definição e execução. É importante lembrar que a incerteza de um MMC em condições reais de operação pode ser maior do que o indicado nas especificações do fabricante por causa do uso de extensões de sondas, sondas longas ou delgadas, mesas giratórias, girando cabeças de sonda, mudanças de temperatura e contaminantes do ar na fábrica.
Por exemplo, em E e R são tal como se especifica determinada por um pontas fixadas diretamente na cabeça de sonda sem extensões e sem rotação. No entanto, a maioria das peças de trabalho requerem configurações de sondas complexas para as quais E e R não são especificados. A peça de trabalho pode exigir a combinação de vários pinos de sonda, extensões rotação da cabeça da sonda, e talvez uma mudança sonda durante o curso do programa de inspeção.
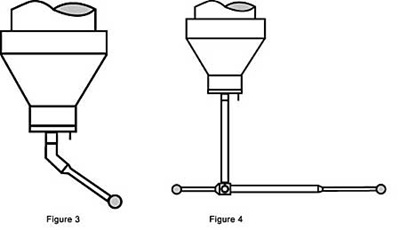
Devido a essas diferenças, a prática geralmente aceite consiste em aplicar uma relação de incerteza de tolerância ao calcular uma especificação MMC necessária. Esta razão pode variar amplamente dependendo dos fatores acima descritos, a complexidade da tarefa de medição e do próprio processo. As proporções típicas variam de 1: 3 a 1:20 com 1: 5 e 1:10, sendo o mais comum. A fim de manter uma relação de 1: 5 de incerteza à tolerância parte, a folha de dados de especificação MMC deve ser cinco vezes mais preciso do que a tolerância a ser inspecionado.
Em quase todas as partes do trabalho, as MMCs devem inspecionar três grupos de características-diâmetros e distâncias, tolerâncias de posição e tolerâncias de forma. Uma análise da incerteza necessária deve ser realizada para cada grupo.
Para tolerâncias de diâmetro e distância, consulte o desenho da peça e localize o diâmetro para distâncias com as tolerâncias mais estreitas. Por causa da dependência de comprimento de incerteza volumétrica, uma tolerância maior em uma característica muito grande pode apresentar mais dificuldade do que uma tolerância muito rígida em uma característica pequena. Isso ilustra como calcular a incerteza da medição do comprimento volumétrico necessário para a máquina.
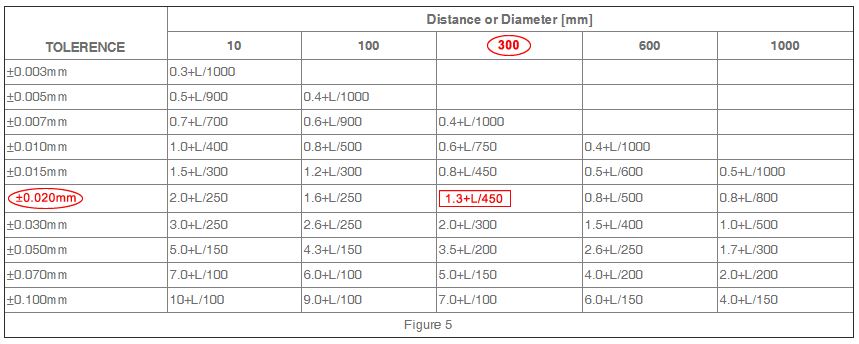
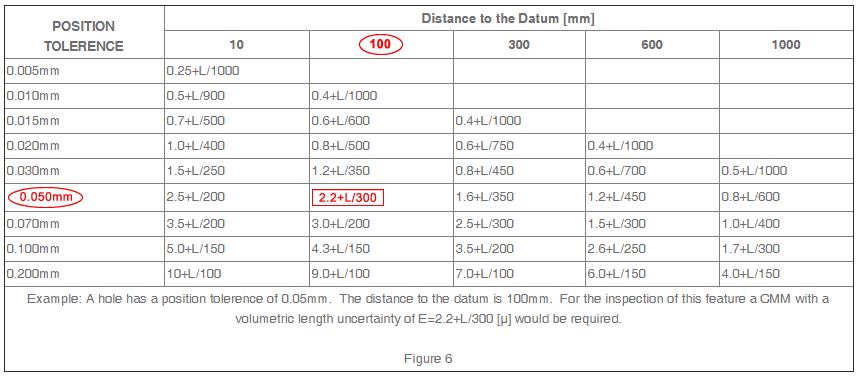
Tolerâncias de forma incluem saídas de chamada para circularidade, nivelamento, linearidade, cilindricidade e forma de perfil.
Ilustra o cálculo da incerteza de medição máquina para tolerâncias de forma.
Exemplo: um diâmetro de 20mm possui tolerância de circularidade de 0,007mm. Para inspeção dessa característica, uma MMC com incerteza de sondagem volumétrica de R=0,7 µm é necessária. Observe que R é especificado para áreas relativamente pequenas (até 30mm).
A incerteza de cada MMC depende em grande parte das condições ambientais. Por consequência, os fabricantes de MMC geralmente especificam a gama de temperatura, variação de temperatura por hora, a variação da temperatura por dia, e a variação da temperatura por metro dentro da qual uma determinada MMC alcança as suas especificações de desempenho. Essas variáveis devem ser consideradas na escolha de uma MMC adequada.Além disso, o nível de vibração no chão é importante para a otimização do desempenho da MMC. A maioria dos fabricantes fornece a vibração máxima que a máquina pode aguentar e ainda atender às especificações estabelecidas. Sistemas de amortecimento de vibração ativos e passivos opcionais também podem ser adquiridos e permitem que a máquina possa ser instalada em ambientes menos adequados e funcionar de acordo com as especificações. É importante conduzir um estudo de vibração sísmica completo realizado no local de instalação preferido se você acha que a vibração pode ser um problema.
Todos os fabricantes de MMC fornecem software para rotinas de medição básicas. Alguns também oferecem software para peças com geometrias mais complexas, tais como engrenagens, impulsores, compressores de parafuso, e cortadores de placa para citar alguns. Certifique-se de compreender a complexidade da rotina de medição necessária para inspecionar suas peças e selecione o pacote de software que irá executar as tarefas de medição necessárias.
Os requisitos de processamento também são uma consideração. Quanto mais peças a MMC puder inspecionar por dia, menor será o custo de inspeção por peça. Aceleração e o número de pontos de sondagem por minuto são os fatores que determinam a taxa de transferência geral. O rendimento também pode ser aumentado por arranjos de acessórios especiais, tais como a inspeção de palete de peças.
A seleção da MMC mais adequada para a sua aplicação requer alguma pesquisa, mas você não tem que fazer isso sozinho. Fabricantes de MMC como a Hexagon Manufacturing Intelligence oferecem especialistas que irão trabalhar com você para ajudá-lo a escolher a MMC mais adequada às suas necessidades.