CMM을 어떻게 선택할 것인가
좋은 CMM은 측정 운영에서 모든 차이를 보입니다.
문의하기

현대적 생산 운영에서 공정 관리 및 품질 보증은, 3차원 측정기(CMMs)의 성능에 크게 의존합니다. 지난 20년 동안, CMMs은 게이지나 고정 설비를 사용했던 전통적인 검사 방법을 대체하면서 품질 관리 운영에 필요한 시간과 인력을 크게 줄였습니다.
CMMs은 표준 기하학적 치수를 검사하는 기능을 제공할 뿐 아니라 기어, 캠축, 에어포일 형상 및 기타 여러 가지 특수 기능도 제공합니다. 전통적인 제작 환경에서는 이 모든 특수 검사를 하기 위해 해당 목적의 테스트 장비가 각각 필요했습니다.
제품의 품질은 제작에 사용된 기계 장비의 품질에 따라 달라질 뿐 아니라 측정의 정확도와 반복성, 그리고 검사 장비에 따라 달라지기도 합니다. 값싸고 저 성능 머시닝 센터가 고 정밀 CMM과 결합되어 제품의 품질을 보증할 수 있는 것은, 오차 한도 내의 부품만이 CMM 검사를 통과할 수 있기 때문입니다. 반대로, 값 비싼 고 품질 머시닝 센터가 값싸고 정확도가 낮은 측정 기기와 결합되면 제품 품질을 보증할 수 없습니다. 일정 비율의 오차를 벗어난 부품이 항상 정확도가 낮은 CMM 검사를 통과하기도 하고, 일정 비율의 오차 내 제품이 불합격되기도 하기 때문입니다. 결과적으로 올바른 CMM의 선택이 중요한 결정입니다. 이 기사의 목적은 정확도와 적용 요건을 충족하는 CMM을 선택하도록 여러분을 돕기 위한 것입니다.
첫 번째 중요한 기준은 CMM의 최소 측정 범위 요건에 대한 판단입니다. 이 범위는 대개 측정될 부품의 치수에 따라 다르지만, 대개는 그보다 더 복잡합니다. 예를 들면, 부품의 구성과 검사 루틴이 프로브 익스텐션과 고정구의 사용이 요구되는 경우, 실제 최소 측정 범위 요건은 측정 물체의 치수보다 훨씬 클 수 있습니다.
CMM의 크기를 적절하게 판단하기 위한 기준으로서, 기계의 X, Y, Z 측정 범위가 측정하고자 하는 가장 큰 부품의 넓이, 길이, 높이의 두 배인 기계를 선택할 것을 고려하도록 합니다.
두 번째 선택 기준은 최소 불 확실성 요건입니다. 불확실성과 CMMs의 테스트 절차는 ISO 10360-2에 설명되어 있습니다. 일부 CMM 제조사는 ISO 10360-2를 충족하지 못하고 CMMA, VDI/VDE 2617, B89 및JIS같은 다른 성능 표준을 사용합니다(CMM 성능 표준 이해하기 참조, 6페이지). 그러나 다른 제조사와 CMMs을 비교하기 위해서는 반드시 사양서를 비교해야 합니다. 대부분의 CMM 제조사들은, 해외 고객을 지원하기 위해, 이미 자신들의 사양을 다양한 포맷으로 제공하고 있습니다. 또 여러분이 글로벌 제조사라면 ISO 10360-2 포맷으로 CMM 사양서를 요청하는 것은 신중히 할 필요가 있습니다. 그것은 세계 표준이기 때문입니다. 본 기사는 경쟁사들과 비교하도록 도울 뿐 아니라, 전 세계에 이미 설치되어 있는 기존 기계와 새 기계를 비교할 수 있도록 도와줄 것입니다.
1994년부터 시행되고 있는 ISO 10360-2는 용적 길이 측정 불확실성(E)과 용적 프로빙 불확실성(R) 이라는 두 개의 불확실성을 명시하고 있습니다.
CMM의 용적 길이 측정 불확실성을 검증하기 위해, 일련의 게이지 블록이나 스텝 게이지가 사용됩니다. 사용자는 테스트를 위해 CMM의 측정 용적 내에서 일곱 개의 다른 위치(위치와 방향)를 선택합니다.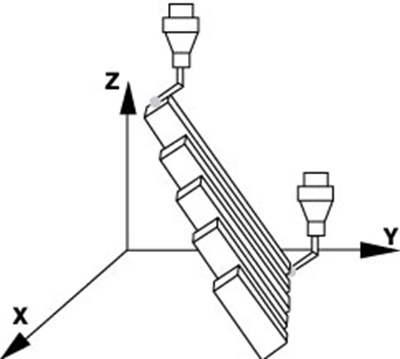
일곱 개의 위치별로 각각 다섯 가지 중요한 표준(길이)가 세 번 측정되므로, 측정은 총 105회 시행됩니다. 105회 측정 결과가 100% 모두, 제조사가 명시한 오차 범위 이내에 들어와야 합니다.
형식과 직경 인증서가 있는 10 mm와 50 mm 사이의 정밀구(球)가 CMM의 프로빙 불 확실성을 검증하기 위해 사용됩니다. 이 테스트는 구 위에 동일 간격의 점 25개를 측정하는 것으로 구성됩니다. 방사형으로부터 최소와 최대 편차의 절대값을 더해서 R을 계산합니다. 결과는 마이크로미터(µm) 단위로 보고되며, 25개의 프로빙이 계산에 모두 사용되어야 합니다.
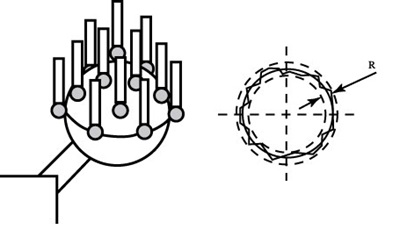
이 테스트는 정의와 실행 두 측면에서 매우 구체적입니다. 실제 운영조건 하에서 CMM의 불확실성은, 프로브 익스텐션의 사용, 길고 얇은 프로브, rotary table, probe 헤드의 회전, 온도 변화, 공장에서의 공기 내 오염 물질 등 때문에, 제조사의 사양서에 설명된 것보다는 더 크다는 것을 기억하는 것이 중요합니다.
예를 들면, 명시된 E와 R에서는, 익스텐션이나 회전 없이 프로브 헤드에 직접 고정된 하나의 스타일러스에 의해 결정됩니다. 그러나 대부분의 작업물은E와 R이 명시되지 않은 복잡한 프로브 구성을 요구합니다. 시험 대상 물체는 몇 개의 프로브 핀, 익스텐션, 프로브 헤드의 회전, 그리고 검사 프로그램 과정 도중의 프로브의 변화 등이 될 수 있습니다.
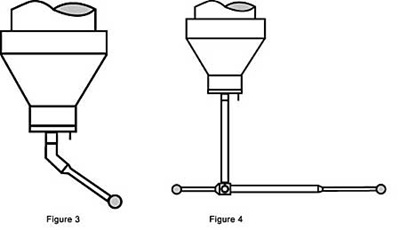
이러한 차이 때문에, 일반적으로 요구된 CMM 사양을 계산할 때 오차에 불확실성 비율을 적용하는 것입니다. 이 비율은 위에 설명한 요인들, 측정 작업의 복잡성, 그리고 그 과정 자체에 따라 크게 변할 수 있습니다. 전형적인 비율은 대개 1:3에서 1:20인데 1:5와 1:10이 가장 일반적입니다. 부품 오차에 대한 불 확실성의 비율을 1:5로 유지하기 위해서는 CMM 데이터 시트 사양서가 계산되는 오차보다 5배 이상 정확해야 합니다.
거의 모든 작업물에 대해, CMM은 세 그룹의 피쳐 직경과 거리, 위치 오차 및 모양 오차를 검사 해야합니다. 필요한 불확실성의 분석은 각 그룹별로 수행되어야 합니다.
직경과 거리 오차는, 부품 도면을 참고해서 가장 적은 오차를 가진 거리에 대한 직경을 찾습니다. 체적 불 확실성의 길이 의존도 때문에, 길이가 길고 오차가 더 큰 물체가 길이가 작고 오차가 빠듯한 물체보다 어려울 수 있습니다. 기계의 용적 길이 측정 불확실성을 계산하는 방법을 보여줍니다.
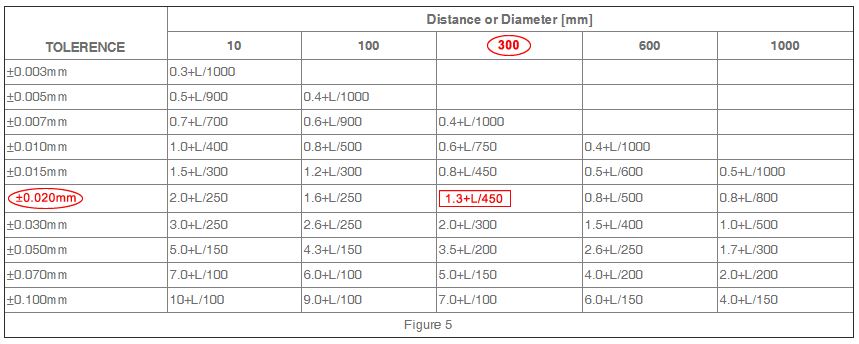
위치 오차는 대개 허용 오차 직경을 결정하기 때문에, 노미널 중심으로부터의 편차를 알아보기 위해서는 반지름만 사용됩니다. 요구된 장비의 불확실성을 계산하기 위해 사용된 방법을 보여줍니다.
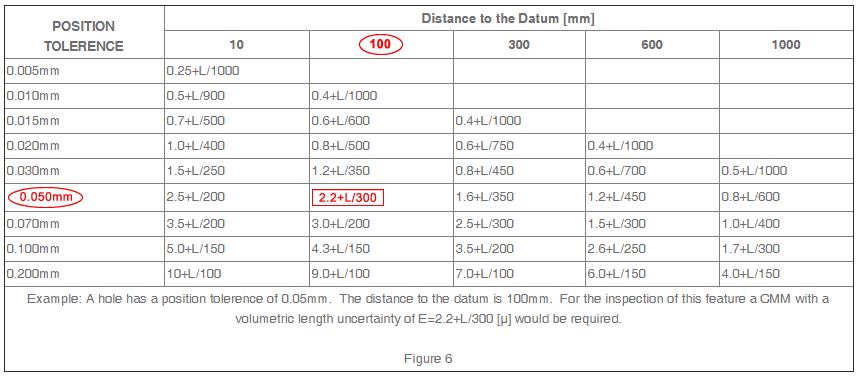
모양 오차에는 원형도, 평탄도, 직선도, 원통도, 프로파일 모양 등에 대한 호출(call outs)이 포함됩니다.
CMMs은 표준 기하학적 치수를 검사하는 기능을 제공할 뿐 아니라 기어, 캠축, 에어포일 형상 및 기타 여러 가지 특수 기능도 제공합니다. 전통적인 제작 환경에서는 이 모든 특수 검사를 하기 위해 해당 목적의 테스트 장비가 각각 필요했습니다.
제품의 품질은 제작에 사용된 기계 장비의 품질에 따라 달라질 뿐 아니라 측정의 정확도와 반복성, 그리고 검사 장비에 따라 달라지기도 합니다. 값싸고 저 성능 머시닝 센터가 고 정밀 CMM과 결합되어 제품의 품질을 보증할 수 있는 것은, 오차 한도 내의 부품만이 CMM 검사를 통과할 수 있기 때문입니다. 반대로, 값 비싼 고 품질 머시닝 센터가 값싸고 정확도가 낮은 측정 기기와 결합되면 제품 품질을 보증할 수 없습니다. 일정 비율의 오차를 벗어난 부품이 항상 정확도가 낮은 CMM 검사를 통과하기도 하고, 일정 비율의 오차 내 제품이 불합격되기도 하기 때문입니다. 결과적으로 올바른 CMM의 선택이 중요한 결정입니다. 이 기사의 목적은 정확도와 적용 요건을 충족하는 CMM을 선택하도록 여러분을 돕기 위한 것입니다.
첫 번째 중요한 기준은 CMM의 최소 측정 범위 요건에 대한 판단입니다. 이 범위는 대개 측정될 부품의 치수에 따라 다르지만, 대개는 그보다 더 복잡합니다. 예를 들면, 부품의 구성과 검사 루틴이 프로브 익스텐션과 고정구의 사용이 요구되는 경우, 실제 최소 측정 범위 요건은 측정 물체의 치수보다 훨씬 클 수 있습니다.
CMM의 크기를 적절하게 판단하기 위한 기준으로서, 기계의 X, Y, Z 측정 범위가 측정하고자 하는 가장 큰 부품의 넓이, 길이, 높이의 두 배인 기계를 선택할 것을 고려하도록 합니다.
두 번째 선택 기준은 최소 불 확실성 요건입니다. 불확실성과 CMMs의 테스트 절차는 ISO 10360-2에 설명되어 있습니다. 일부 CMM 제조사는 ISO 10360-2를 충족하지 못하고 CMMA, VDI/VDE 2617, B89 및JIS같은 다른 성능 표준을 사용합니다(CMM 성능 표준 이해하기 참조, 6페이지). 그러나 다른 제조사와 CMMs을 비교하기 위해서는 반드시 사양서를 비교해야 합니다. 대부분의 CMM 제조사들은, 해외 고객을 지원하기 위해, 이미 자신들의 사양을 다양한 포맷으로 제공하고 있습니다. 또 여러분이 글로벌 제조사라면 ISO 10360-2 포맷으로 CMM 사양서를 요청하는 것은 신중히 할 필요가 있습니다. 그것은 세계 표준이기 때문입니다. 본 기사는 경쟁사들과 비교하도록 도울 뿐 아니라, 전 세계에 이미 설치되어 있는 기존 기계와 새 기계를 비교할 수 있도록 도와줄 것입니다.
1994년부터 시행되고 있는 ISO 10360-2는 용적 길이 측정 불확실성(E)과 용적 프로빙 불확실성(R) 이라는 두 개의 불확실성을 명시하고 있습니다.
CMM의 용적 길이 측정 불확실성을 검증하기 위해, 일련의 게이지 블록이나 스텝 게이지가 사용됩니다. 사용자는 테스트를 위해 CMM의 측정 용적 내에서 일곱 개의 다른 위치(위치와 방향)를 선택합니다.
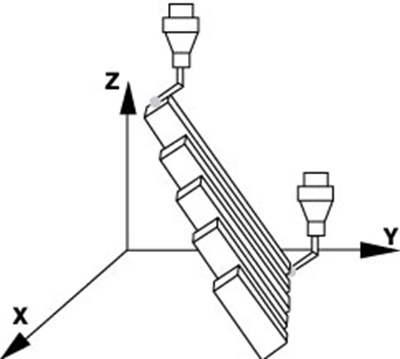
일곱 개의 위치별로 각각 다섯 가지 중요한 표준(길이)가 세 번 측정되므로, 측정은 총 105회 시행됩니다. 105회 측정 결과가 100% 모두, 제조사가 명시한 오차 범위 이내에 들어와야 합니다.
형식과 직경 인증서가 있는 10 mm와 50 mm 사이의 정밀구(球)가 CMM의 프로빙 불 확실성을 검증하기 위해 사용됩니다. 이 테스트는 구 위에 동일 간격의 점 25개를 측정하는 것으로 구성됩니다. 방사형으로부터 최소와 최대 편차의 절대값을 더해서 R을 계산합니다. 결과는 마이크로미터(µm) 단위로 보고되며, 25개의 프로빙이 계산에 모두 사용되어야 합니다.
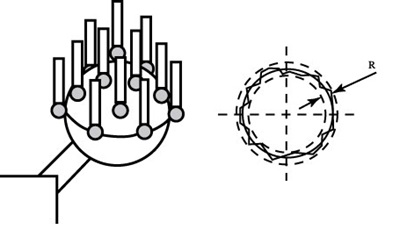
이 테스트는 정의와 실행 두 측면에서 매우 구체적입니다. 실제 운영조건 하에서 CMM의 불확실성은, 프로브 익스텐션의 사용, 길고 얇은 프로브, rotary table, probe 헤드의 회전, 온도 변화, 공장에서의 공기 내 오염 물질 등 때문에, 제조사의 사양서에 설명된 것보다는 더 크다는 것을 기억하는 것이 중요합니다.
예를 들면, 명시된 E와 R에서는, 익스텐션이나 회전 없이 프로브 헤드에 직접 고정된 하나의 스타일러스에 의해 결정됩니다. 그러나 대부분의 작업물은E와 R이 명시되지 않은 복잡한 프로브 구성을 요구합니다. 시험 대상 물체는 몇 개의 프로브 핀, 익스텐션, 프로브 헤드의 회전, 그리고 검사 프로그램 과정 도중의 프로브의 변화 등이 될 수 있습니다.
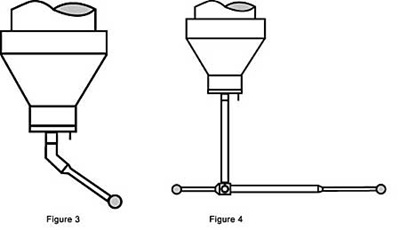
이러한 차이 때문에, 일반적으로 요구된 CMM 사양을 계산할 때 오차에 불확실성 비율을 적용하는 것입니다. 이 비율은 위에 설명한 요인들, 측정 작업의 복잡성, 그리고 그 과정 자체에 따라 크게 변할 수 있습니다. 전형적인 비율은 대개 1:3에서 1:20인데 1:5와 1:10이 가장 일반적입니다. 부품 오차에 대한 불 확실성의 비율을 1:5로 유지하기 위해서는 CMM 데이터 시트 사양서가 계산되는 오차보다 5배 이상 정확해야 합니다.
거의 모든 작업물에 대해, CMM은 세 그룹의 피쳐 직경과 거리, 위치 오차 및 모양 오차를 검사 해야합니다. 필요한 불확실성의 분석은 각 그룹별로 수행되어야 합니다.
직경과 거리 오차는, 부품 도면을 참고해서 가장 적은 오차를 가진 거리에 대한 직경을 찾습니다. 체적 불 확실성의 길이 의존도 때문에, 길이가 길고 오차가 더 큰 물체가 길이가 작고 오차가 빠듯한 물체보다 어려울 수 있습니다. 기계의 용적 길이 측정 불확실성을 계산하는 방법을 보여줍니다.
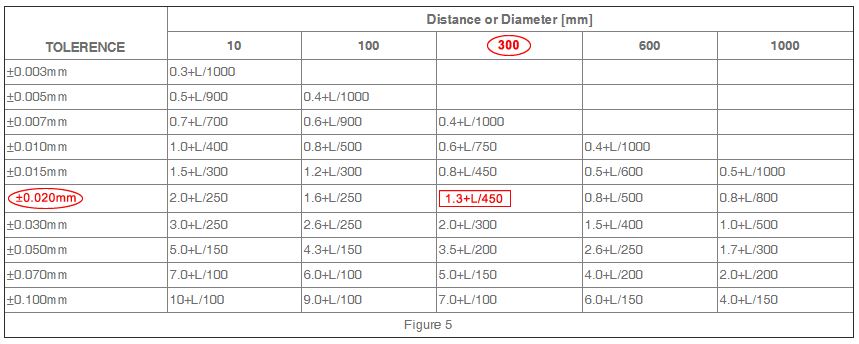
위치 오차는 대개 허용 오차 직경을 결정하기 때문에, 노미널 중심으로부터의 편차를 알아보기 위해서는 반지름만 사용됩니다. 요구된 장비의 불확실성을 계산하기 위해 사용된 방법을 보여줍니다.
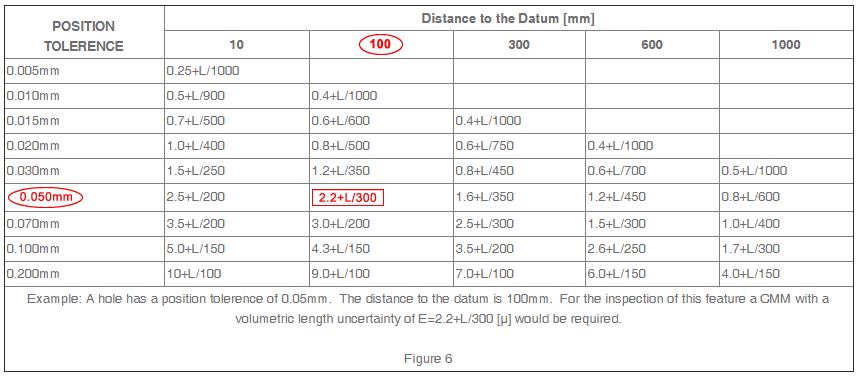
모양 오차에는 원형도, 평탄도, 직선도, 원통도, 프로파일 모양 등에 대한 호출(call outs)이 포함됩니다.
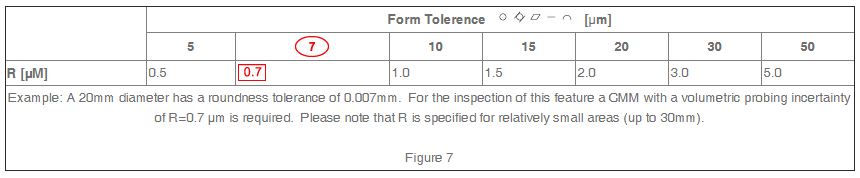
모든 CMM의 불확실성은 환경적 조건에 따라 크게 좌우됩니다. 따라서, CMM 제조사들은 일반적으로 온도 범위, 시간당 온도 변화, 하루 동안의 온도 변화, 그리고 각 미터 당 온도 변화를 성능을 명시하여 구체화 합니다. 적절한 CMM을 선택할 때에는 이런 변수들이 고려되어야 합니다.
또, CMM의 성능을 최적화하기 위해서는 바닥 진동 수준도 중요합니다. 대부분의 제조사들은 기계가 견딜 수 있고, 기술된 사양서를 충족할 수 있는 최대 진동을 공급합니다. 기계가 익숙하지 않은 환경에서도 설치되며, 사양서에 상응하는 성능으로 작동할 수 있도록 하는 능동 및 수동 진동 완충 시스템 (damping system)을 옵션으로 구입할 수 있습니다. 진동이 문제가 된다면, 원하는 설치 장소에서 심한 진동에 대한 연구를 수행하게 하는 것도 중요합니다.
모든 CMM 제조사들은 기본 측정 루틴을 위한 소프트웨어를 제공합니다. 베벨 기어, 임펠러(impeller), 스크류 컴프레셔, 홉 커터(hob cutter) 등과 같은 복잡한 기하학적 도형의 부품에 대한 소프트웨어를 제공하는 회사도 있습니다. 부품을 검사하기 위해 필요한 측정 루틴의 복잡성을 이해하고, 필요한 측정 작업을 수행할 소프트웨어 패키지를 선택하여야 합니다.
처리량 요건도 고려 사항입니다. CMM이 하루에 더 많은 부품을 검사할 수 있을수록, 부품 당 검사 비용은 절약 할 수 있습니다. 가속과 분당 프로브 포인트의 수는 전체적인 처리량을 판단하는 요인입니다. 처리량은 파트의 팔레트 검사 같은 특수 정렬된 고정구들을 부착시켜 늘어나게 할 수도 있습니다.
용도에 가장 적절한 CMM을 선택하는 것은 많은 생각과 조사가 필요합니다. 그러나 여러분이 혼자 할 필요는 없습니다. Hexagon Metrology 같은 CMM제조사들은 요건에 가장 적합한 CMM을 선택하는데 도와줄 전문가들을 보유하고 있습니다.
모든 CMM 제조사들은 기본 측정 루틴을 위한 소프트웨어를 제공합니다. 베벨 기어, 임펠러(impeller), 스크류 컴프레셔, 홉 커터(hob cutter) 등과 같은 복잡한 기하학적 도형의 부품에 대한 소프트웨어를 제공하는 회사도 있습니다. 부품을 검사하기 위해 필요한 측정 루틴의 복잡성을 이해하고, 필요한 측정 작업을 수행할 소프트웨어 패키지를 선택하여야 합니다.
처리량 요건도 고려 사항입니다. CMM이 하루에 더 많은 부품을 검사할 수 있을수록, 부품 당 검사 비용은 절약 할 수 있습니다. 가속과 분당 프로브 포인트의 수는 전체적인 처리량을 판단하는 요인입니다. 처리량은 파트의 팔레트 검사 같은 특수 정렬된 고정구들을 부착시켜 늘어나게 할 수도 있습니다.
용도에 가장 적절한 CMM을 선택하는 것은 많은 생각과 조사가 필요합니다. 그러나 여러분이 혼자 할 필요는 없습니다. Hexagon Metrology 같은 CMM제조사들은 요건에 가장 적합한 CMM을 선택하는데 도와줄 전문가들을 보유하고 있습니다.