À propos des palpeurs de scanning laser
Le scanning laser crée un modèle tridimensionnel pour une surface qui, en raison de sa haute densité (souvent des millions de points), est appelé « nuage de points ».
Contactez-nous
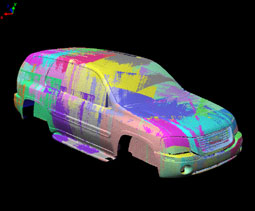
Le scanning laser crée un modèle tridimensionnel pour une surface qui, en raison de sa haute densité (souvent des millions de points), est appelé « nuage de points ». L’image montre un jeu de nuage de points volumineux représentant un véhicule complet. Les différentes couleurs marquent différents cycles de scanning de la pièce.
Inspection et validation en sous-traitance
Le nuage de points 3D créé par le bras de mesure Absolute Arm 7 axes, combiné au logiciel PC-DMIS, peut s'utiliser pour une inspection dimensionnelle ou GD&T, et il est possible de comparer les résultats avec les valeurs CAO nominales. La comparaison nuage-CAO permet de superposer de grands nuages de points sur le modèle CAO pour un examen rapide des divergences (parfois appelée « carte météo » ou carte en couleur). On peut aussi appliquer le scanning laser pour une inspection classique (non CAO) sur la base de la construction et du dimensionnement d'éléments.
Exemple d'applications d'inspection et de validation :
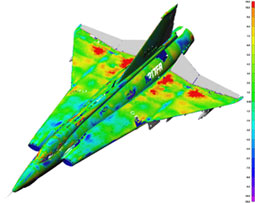
- Vérification de la conformité d’une pièce par rapport au modèle CAO dans le cadre de l’inspection initiale, de l’inspection pendant la fabrication ou de la validation finale.
- Vérification des dimensions des outils et du moule pour déterminer l’usure, évaluer les réparations ou contrôler les modifications.
- Inspection du premier article.
- Mesure de contour, comparaison de pièces par rapport modèles CAO correspondants, coupes 2D ou cartographie topographique 3D.
- Ajustement en fin de la chaîne de fabrication ou de l’assemblage.
- Inspection de l'ajustement de deux pièces.
La rétroconception revient à prendre une pièce physique, à la mesurer pour déterminer ses caractéristiques et à traiter les données pour créer un modèle CAO. On utilise souvent cette méthode dans les cas où le processus de conception de produit implique un haut degré de travail manuel, comme pour la conception automobile. Malgré les progrès réalisés en CAO, de nombreuses conceptions débutent toujours et encore par un modèle physique qu’il faut ensuite convertir sous forme électronique.
Les nuages de points générés par le scanning laser sont traités de différentes façons pour les préparer à la transformation en CAO. On emploie un logiciel de rétroconception comme PC-DMIS Reshaper pour créer ou importer le nuage de points numérisé, le traiter, le lisser d'un point de vue mathématique et combiner les données scannées de façon à obtenir un modèle de surface représentatif.
Exemples d'applications de rétroconception :
- Création d'un modèle 3D pour une conception ou une adaptation CAO.
- Caractérisation d'une surface d'ajustement de façon à pouvoir y raccorder ou fixer une autre pièce.
- Création d’une pièce de référence lorsqu’aucun modèle CAO ou plan de pièce n’existe.
- Établissement d'un modèle d'outil en l’état pour comparer l’usure au fil du temps.
- Analyse concurrentielle de pièce/produit.
- Conservation d’objets à des fins d’archive ou d’historiques en vue de créer un enregistrement 3D ou une copie.
- Fraisage de reproduction/mise à échelle et prototypage rapide
Exemples d'applications :
- Préservation du patrimoine historique ou culturel, avec scanning d’objets pour observer l’usure ou la détérioration.
- Prototypage rapide de modèles réalisés à la main.
- Mise à échelle d'un modèle scanné physique.
- Scanning de modèles à des fins électroniques, tels que les films et les jeux vidéo.
- Renseignez-vous sur nos solutions de scanning laser.
La vitesse du scanning dépend largement du capteur et du champ visuel de ce dernier. Sur les capteurs laser en général, on voit les points collectés sur « écran » en temps réel. On appelle parfois cette opération « peindre la pièce ». Effectuer des scans sous différents angles pour garantir l’acquisition de toute la géométrie aboutit souvent à un nuage de points comme celui de Liberty Bell, sur la figure 3, où on a l’impression que quelqu’un s’est amusé avec de la peinture.
Un autre critère important pour la vitesse globale est le nombre de points par seconde que le scanner peut recueillir, la largeur de la trajectoire de scanning et la densité de points par ligne. L'animation ci-dessous compare la différence des résultats obtenus avec deux scanners dans le relevé d’une plaque plate carrée d'un mètre carré, l’un travaillant dans une bande étroite et l'autre dans une bande large avec un champ de vision moyen. Le scanner doté d’une plus grande largeur de balayage (105 mm) avec un champ visuel moyen acquiert la surface en moins de 3 minutes, alors que le scanner de plus petite largeur a besoin de 13 minutes pour la même pièce.
L'application peut déterminer le choix du scanner. Les tâches imposant une vitesse élevée et une grande couverture, dans lesquelles les détails fins ont une moindre importance, peuvent exiger un scanner à plus haute vitesse. D'autres applications en relation avec de plus petites pièces, plus complexes, peuvent donner de meilleurs résultats avec une plus petite largeur de bande. Certains scanners, comme le HP-L-20.8, permettent à l’utilisateur de sélectionner la largeur de balayage la mieux adaptée à l’application.
Scanner à largeur de balayage étroite | Scanner à grande largeur de balayage |
Largeur de balayage de 44 mm avec un champ visuel moyen | Largeur de balayage de 105 mm avec un champ visuel moyen |
23 cycles pour peindre la plaque | 10 cycles pour peindre la plaque |
Espacement de ligne de 1 mm, 13 min 2 s | Espacement de ligne de 1 mm, 2 min 50 s |
Est-il mieux de recueillir plus de points ?
Cela dépend en partie de la finalité des données. Un scanning de plus haute densité est avantageux pour relever des surfaces extrêmement complexes comportant de nombreuses courbures. Des surfaces moins sinueuses n'ont pas les mêmes exigences. Les données de plus haute densité sont également préférables pour l’extraction d’entités telles que des orifices, des fentes, des cylindres et autres formes prismatiques, ainsi que des bords. Étudiez les deux images ci-dessous obtenues à partir de scans identiques d'un orifice de 15 mm. Le scan de gauche a été créé avec un capteur de scanning de faible densité, celui de droite avec un capteur V5 de hautes performances. L’extraction et la mesure de la forme de l’orifice sur le côté droit tendent à être plus précises avec les données à plus haute densité. Les données à plus haute densité reproduisent mieux les textures, si cela est important pour vous.
Renseignez-vous sur nos solutions de scanning laser.
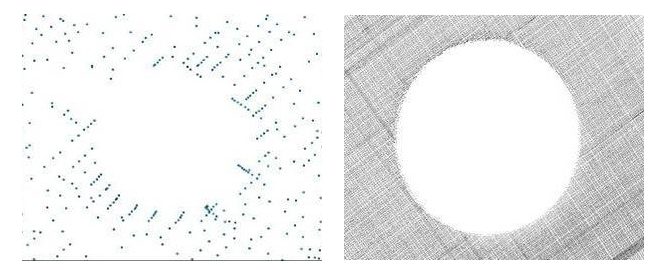
La lumière ambiante affecte-t-elle le capteur ?
Souvent, différents types d'éclairage dans un laboratoire, un studio et une usine peuvent avoir des effets négatifs sur un appareil optique. Alors que certains types d'appareils de scanning doivent disposer d’un environnement à lumière contrôlée, ce n’est pas le cas des capteurs utilisés sur les bras de mesure ROMER. Les bras de mesure ROMER équipés de scanners laser appliquent différentes techniques pour surmonter les effets de la lumière ambiante, y compris des filtres optiques et des commandes d'exposition, conçus pour ignorer certaines longueurs d’onde de la lumière, sauf celles proches du laser utilisé. Il en résulte un rejet de la lumière produite par les systèmes d'éclairage incandescents, aux vapeurs de mercure, halogènes et d'autres systèmes répandus, et l’absence d’effets sur le capteur.
Les conditions de surface affectent-elles le capteur laser ?
Traditionnellement, la précision de la mesure était influencée par l’état de surface. Les surfaces chromées ultra polies et les surfaces noires brillantes étaient plus difficiles à scanner. Les surfaces à plusieurs couleurs ou les surfaces réfléchissantes peuvent aussi causer des problèmes à de nombreux scanners. Les bras de mesure ROMER équipés de scanners laser utilisent des outils pour maîtriser ces situations et permettent de réussir le scanning de la plupart des états de surface et des couleurs. Notre capteur de pointe HP-L-20.8 emploie un système de contrôle d’exposition automatique et une technologie à virgule flottante pour autoriser un ajustement automatique, en temps réel, aux variations de couleur et de réflexion du matériau. Il facilite aussi le scanning de presque tous les objets. Dans l’image de droite, une pièce comportant trois couleurs et des états de surface différents, ainsi que différents niveaux de réflexion, est facilement scannée avec le HP-L-20.8.
Devez-vous poudrer les pièces ?
En général, la réponse est « non » sauf pour les surfaces les plus transparentes. La préparation des surfaces par poudrage (pour réduire la réflexion et créer une surface uniforme) est indésirable pour de nombreuses raisons, allant du temps nécessaire pour adapter la surface à la variabilité des mesures due à la poudre elle-même (des études montrent que celle-ci peut produire une variabilité de mesure jusqu'à 100 microns/0,004"). Alors qu’il était souvent nécessaire de poudrer les pièces par le passé, ce n’est plus le cas aujourd'hui.
La lumière et l’environnement affectent-ils le capteur ?
Les environnements de production et d'atelier habituels sont acceptables pour le fonctionnement des bras de mesure ROMER avec des scanners laser. Les capteurs ne conviennent pas à des environnements où un risque de contact avec l’eau ou l’huile existe, étant donné que ces fluides peuvent adhérer aux lentilles de laser et de caméra. La température doit se situer entre 15°C et 35 °C et l’humidité entre 0 et 90 % sans condensation. Il convient d'éviter des environnements comportant des salissures, de l’huile ou d'autres contaminants susceptibles d'adhérer au capteur, puisque cela peut influencer la performance de mesure. Ces capteurs peuvent fonctionner de façon fiable 24 h sur 24/7 jours sur 7 dans une usine pendant de nombreuses années.
Données filtrées / non filtrées... Quelle est la différence ?
Les données filtrées sont des données de capteur « filtrées » ou « traitées » lors de la génération du nuage de points. Cette opération est en général assurée par un package logiciel tiers lors de la lecture des données de capteur dans le logiciel. Les données de capteur brutes sont compromises parce qu'elles sont filtrées pendant l’acquisition et que la qualité des données est une entité non connue.
Les données non filtrées sont des données de capteur à l’état brut, incluant toutes les valeurs aberrantes. Les données originales peuvent faire l’objet d'une évaluation indépendante. L’utilisation de données non filtrées indique la capacité du capteur à effectuer un scan précis, en vue de comparer les données réelles et les données nominales (imprimées ou CAO).
L'aptitude à acquérir des données de scan brutes, non filtrées, indépendamment d’un logiciel tiers, est préférable, tout simplement parce qu’elle vous permet de déterminer ce que vous voulez inclure ou non dans votre jeu de données. Souvent, les données incompréhensibles sont le résultat d'une faible performance du scanner. Aussi, plus votre scanner pourra acquérir de surface effective sans se laisser « leurrer » par des facteurs externes comme l'éclairage, la couleur et le pouvoir de réflexion de la surface, plus les résultats seront fiables. La plupart des logiciels de nuages de points ou d’inspection intègrent des outils pour supprimer ou ignorer les données aberrantes comme vous le souhaitez.
Si je scanne une pièce, puis-je obtenir un modèle CAO à la fin ?
C’est peut-être l’aspect le plus mal connu du scanning laser. Le bras de mesure et le scanner acquièrent la géométrie de la pièce dans un format de nuage de points 3D. C’est tout simplement un fichier de points en relation entre eux. Ce n’est pas un fichier CAO. Pour obtenir un fichier CAO, vous devez d'abord créer une espèce de modèle basé sur les polygones à partir des nuages de points, puis caractériser les surfaces et les entités comme modèles CAO, souvent dans un système de CAO. Il s’agit de processus hors ligne qui ont lieu à la fin de collecte des données et ils représentent la partie la plus laborieuse du traitement des données scan 3D. L'image de gauche est un nuage de points qui montre les différentes surfaces scannées comme patchs colorés. Le modèle à droite représente les mêmes données converties en un modèle maillé polygonal, première étape pour obtenir une conversion CAO complète.
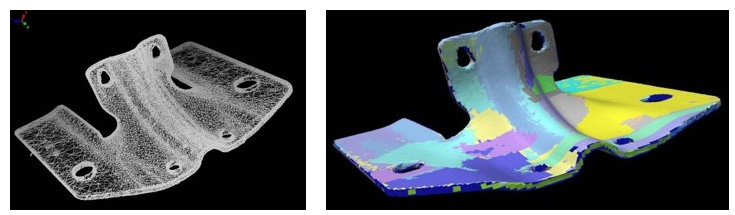