Laserscanning-Sensoren
Die Messdaten von Laserscannern dienen zur Erstellung eines dreidimensionalen Modells einer Oberfläche, das aufgrund seiner hohen Dichte (häufig Millionen von Punkten) als Punktwolke bezeichnet wird.
Kontakt
In der industriellen Messtechnik kann Laserscanning für unterschiedliche Aufgaben eingesetzt werden. Der ROMER Absolute Arms SI mit sieben Achsen und integriertem 3D-Laserscanner erfüllt all diese Aufgaben in Kombination mit der PC-DMIS Software als Komplettsystem. Die Absolutdrehgeber des Messarms kennen seine exakte Position zu jedem Zeitpunkt, wodurch Referenzierungsvorgänge entfallen. Das ergonomische Zero-G Gegengewicht lässt den Messarm in der Hand des Bedieners gleichsam schweben.
Die Messdaten von Laserscannern dienen zur Erstellung eines dreidimensionalen Modells einer Oberfläche, das aufgrund seiner hohen Dichte (häufig Millionen von Punkten) als Punktwolke bezeichnet wird. Die Abbildung zeigt eine große Punktwolke, die ein komplettes Fahrzeug darstellt. Die unterschiedlichen Farben stehen für verschiedene Scanvorgänge bei der Erfassung des Objekts.
Die mit dem Absolute Arm mit sieben Achsen erfassten 3D-Punktwolkendaten können mithilfe von PC-DMIS für dreidimensionale Maßprüfungen oder zur Kontrolle von Form- und Lagetoleranzen verwendet werden, wobei die Messergebnisse mit den CAD-Sollwerten abgeglichen werden. Für eine rasche visuelle Inspektion von Abweichungen können die Punktwolkendaten über das CAD-Modell gelegt werden. Die entstehende Darstellung wird als Farbprofil bezeichnet. Laserscanning kann darüber hinaus auch für herkömmliche Maßprüfungen (ohne CAD) von Merkmalen und Dimensionen eingesetzt werden.
Beispiele für Anwendungen in der Inspektion und Validierung
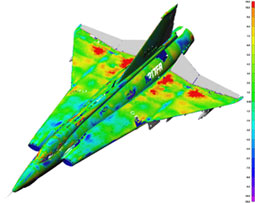
- Verifizierung, ob ein Werkstück den CAD-Vorgaben entspricht, oder Prüfungen beim Wareneingang, während der Fertigung oder zur Endabnahme
- Kontrolle der Maße von Werkzeugen und Formen zur Ermittlung von Verschleiß und Reparaturbedarf oder zur Überprüfung durchgeführter Modifikationen
- Erstmusterprüfung
- Messung von Konturen, Abgleich von Werkstücken mit CAD-Modellen, 2D-Querschnitte, topografische 3D-Kartierung
- Feinabstimmungen an der Fertigungslinie oder im Montageprozess
- Kontrollen beim Teilezusammenbau
Reverse Engineering
Als Reverse Engineering wird die Vermessung eines vorhandenen Werkstücks zur Ermittlung seiner Eigenschaften und die anschließende Verarbeitung der Messdaten zur Erstellung eines CAD-Modells bezeichnet. Diese Vorgehensweise wird besonders häufig dann angewendet, wenn die Produktentwicklung nennenswerte manuelle Teilschritte aufweist, wie beispielsweise im Fahrzeugdesign. Trotz unbestreitbarer Vorteile von CAD-Workflows gehen viele Designkonzepte bis heute von physischen Modellen aus, die digitalisiert werden müssen.
Mittels Laserscanning erzeugte Punktwolken werden für die Umwandlung in CAD-Daten unterschiedlich aufbereitet. Reverse-Engineering-Software wie PC-DMIS Reshaper dient zur Erstellung oder zum Import der gescannten Punktwolke. Die Scandaten werden bearbeitet, mathematisch geglättet und so kombiniert, dass sich ein repräsentatives Oberflächenmodell erstellen lässt.
Beispiele für Reverse-Engineering-Anwendungen- Erstellung eines 3D-Modells für die Weiterentwicklung oder Adaptierung in einer CAD-Umgebung
- Erfassung der Eigenschaften einer Fügefläche, damit ein anderes Werkstück damit passend verbunden werden kann
- Erstellung einer Teilevorlage, für die weder CAD-Daten noch Zeichnungen existieren
- Erstellung eines Bestandsmodells eines Werkzeugs, sodass im Laufe der Zeit auftretende Verschleißerscheinungen analysiert werden können
- Untersuchung von Teilen oder Produkten der Mitbewerber
- Archivierung und historische Dokumentation von Kunstgegenständen und dergleichen in 3D
- Kopierfräsen, Kopierfräsen mit Größenänderung und Rapid Prototyping
Beispiele für Anwendungen
- Schutz von historischen Baudenkmälern und Kunstgegenständen durch Scanvorgänge zur Erfassung von Verschleiß- oder Alterserscheinungen
- Rapid Prototyping von handgefertigten Modellen
- Änderung der Größe eines gescannten physikalischen Modells
- Scannen von Modellen für die elektronische Weiterverarbeitung, beispielsweise in Filmen oder Videospielen
Wie lange dauert der Scanvorgang?
Die Scangeschwindigkeit ist in hohem Maße vom verwendeten Sensor und von dessen Sichtfeld abhängig. Beim Einsatz von Lasersensoren werden die erfassten Punkte in Echtzeit am Bildschirm angezeigt. Diesen Vorgang bezeichnet man auch als das „Malen“ des Werkstücks. Bei der Erfassung von Scans aus unterschiedlichen Winkeln, damit gewährleistet ist, dass alle erforderlichen Geometrien bekannt sind, ergeben sich oft farbenfrohe Punktwolken wie jene der Liberty Bell.
Ebenfalls relevant für die Geschwindigkeit ist die Punkterfassungskapazität des Scanners pro Sekunde, die Scanbreite und die Punktdichte pro Linie. Die Darstellung unten vergleicht zwei verschiedene Scanner – einen mit einer schmalen, einen mit einer breiten Scanlinie – bei der Erfassung einer ein Meter großen, flachen, quadratischen Platte bei mittlerem Sichtfeld. Der Scanner mit der größeren Scanbreite (105 mm) bei mittlerem Sichtfeld erfasst die Oberfläche in etwas weniger als 3 Minuten, während der Scanner mit der kleineren Scanbreite für dasselbe Werkstück über 13 Minuten benötigt.
Die Wahl des Scanners erfolgt in Abhängigkeit von der Anwendung. Für Anwendungen, bei denen Geschwindigkeit und Abdeckung von größerer Bedeutung sind als kleine Details, empfiehlt sich ein schnellerer Scanner. Bei anderen Anwendungen mit kleineren, komplexeren Komponenten funktioniert eine schmalere Scanlinie möglicherweise besser. Einige Scanner, wie der HP-L-20.8, erlauben die Auswahl der optimalen Breite der Scanlinie für die jeweilige Anwendung durch den Benutzer.
-
Scanner mit geringer Scanbreite Scanner mit hoher Scanbreite Scanbreite von 44 mm bei mittlerem Sichtfeld Scanbreite von 105 mm bei mittlerem Sichtfeld 23 Scanvorgänge zur Erfassung des Objekts 10 Scanvorgänge zur Erfassung des Objekts Linienabstand 1 mm, 13 min und 2 s Linienabstand 1 mm, 2 min und 50 s
Sind mehr Punkte besser?
Die Antwort auf diese Frage hängt teilweise davon ab, wofür die Daten benötigt werden. Auf extrem komplexe Oberflächen mit vielen Krümmungen wirkt sich eine höhere Datendichte günstig aus. Bei flacheren Oberflächen ist der Mehrwert dagegen geringer. Zur Extraktion von Elementen wie Langlöchern, Zylindern und anderen prismatischen Formen sowie Kanten sind dichtere Daten ebenfalls vorteilhaft. Bei den beiden Abbildungen unten handelt es sich um zwei identische Scans einer Bohrung mit 15 mm Durchmesser. Der Scan links wurde mit einem scannenden Sensor mit niedriger Dichte erstellt, der Scan rechts mit dem Topmodell V5. Die Extraktion und Messung der Form der Bohrung auf der rechten Abbildung kann mit Daten höherer Dichte genauer erfolgen. Daten mit höherer Dichte erfassen außerdem die Oberflächenbeschaffenheit von Werkstücken besser, sollte das für Ihre Anwendung von Bedeutung sein.
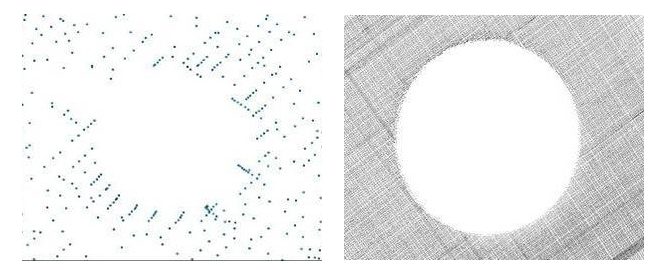
Wirkt sich die Umgebungsbeleuchtung auf den Sensor aus?
Oft wirken sich unterschiedliche Arten der Umgebungsbeleuchtung in einem Labor, Studio oder in einer Werksumgebung ungünstig auf die mit optischen Geräten erzielten Messergebnisse aus. Tatsächlich benötigen manche Scanner eine kontrollierte Umgebungsbeleuchtung, doch bei den Sensoren der ROMER Messarme ist dies nicht der Fall. Die mit Laserscannern ausgestatteten ROMER Messarme nutzen verschiedene Verfahren zum Ausgleich der Auswirkungen der Umgebungsbeleuchtung, darunter optische Filter und Belichtungssteuerungen, die so konzipiert sind, dass Lichtwellenlängen mit Ausnahme jener in der Nähe des verwendeten Lasers ausgeblendet werden. So kann sich von Glühlampen, Quecksilberdampflampen, Halogenlampen und anderen gängigen Beleuchtungssystemen abgestrahltes Licht nicht auf die Messergebnisse des Sensors auswirken.
Wirkt sich die Oberflächenbeschaffenheit auf den Sensor aus?
Früher war die Genauigkeit einer Messung von der Beschaffenheit der gemessenen Oberfläche abhängig. Am schwierigsten war das Scannen auf Hochglanz polierter Chromteile und schwarz glänzender Oberflächen. Auch mehrfarbige Oberflächen und Oberflächen mit unterschiedlichem Reflexionsvermögen verursachten bei vielen Scannern Probleme. ROMER Arme mit Laserscannern können mit solchen Situationen umgehen und lassen die erfolgreiche Erfassung von Objekten mit fast allen Oberflächenbeschaffenheiten und Farben zu. Der HP-L-20.8, unser Premiumsensor, ist mit einer automatischen Belichtungssteuerung und der Flying Dot-Technologie ausgestattet, die ihm die automatische Anpassung an Änderungen der Farbe und des Reflexionsvermögens der Oberfläche in Echtzeit erlaubt. So kann praktisch jedes Objekt erfolgreich gescannt werden. In der Abbildung rechts wird ein Werkstück mit drei verschiedenen Farben und unterschiedlichen Oberflächenbeschaffenheiten sowie Reflexionseigenschaften problemlos mit dem HP-L-20.8 gescannt.
Müssen die Werkstücke vor dem Scannen mit Puder vorbehandelt werden?
Dies ist fast nie der Fall. Nur bei hochgradig transparenten Oberflächen kann sich Pudern als sinnvoll erweisen. Generell ist die Vorbehandlung der Oberfläche mit Puder (um das Reflexionsvermögen zu reduzieren und eine einheitliche Oberfläche zu schaffen) aus verschiedensten Gründen nicht wünschenswert: Zum einen wird dadurch der Zeitaufwand erhöht, zum anderen wird die Genauigkeit der Messung durch die Puderschicht verfälscht (Studien zufolge können sich daraus Messungenauigkeiten von bis zu 100 Mikrometer ergeben). In der Vergangenheit mussten Werkstücke vor der Messung oft mit Pulver vorbehandelt werden, doch diese Zeiten sind nun vorbei.
Wirken sich Temperatur und Umgebungsbedingungen auf den Sensor aus?
ROMER Messarme mit Laserscannern können in üblichen Fertigungs- und Montageumgebungen ohne Schwierigkeiten betrieben werden. Für Arbeitsbereiche, in denen Wasser- oder Ölspritzer vorkommen können, sind die Systeme nicht geeignet, da Flüssigkeiten am Laser und an der Kameralinse anhaften können. Die Temperatur sollte zwischen 15 und 35 °C betragen, die Luftfeuchtigkeit sollte zwischen 0 und 90 % (nicht kondensierend) liegen. Umgebungen, in denen sich Schmutz, Öl oder andere Schadstoffe befinden, die am Sensor anhaften können, sind zu meiden, da dies die Messleistung beeinträchtigen kann. Die Sensoren können ohne Genauigkeitseinbußen über viele Jahre hinweg in einer Werksumgebung rund um die Uhr genutzt werden.
Gefilterte oder ungefilterte Daten ... Worin genau besteht eigentlich der Unterschied?
Gefilterte Daten sind Sensordaten, die im Zuge der Erstellung der Punktwolke bereits gefiltert oder bearbeitet wurden. Diese Bearbeitung erfolgt in der Regel mithilfe von Softwarepaketen von Drittanbietern, während die Sensordaten in die Software eingelesen werden. Die Qualität der Rohdaten des Sensors ist unklar, da die Daten während der Erfassung gefiltert werden.
Ungefilterte Daten sind die vom Sensor unmittelbar erfassten Rohdaten einschließlich Ausreißern, unabhängig von etwaigen Begründungen für diese Ausreißer. Diese Originaldaten können eigenständig ausgewertet werden. Die Nutzung ungefilterter Daten lässt Rückschlüsse auf die tatsächliche Scanleistung des Sensors zu, wenn diese mit den Solldaten (Zeichnungen oder CAD-Modellen) abgeglichen werden.
Die Möglichkeit zur Erfassung roher, ungefilterter Scandaten unabhängig von einer Drittanbieter-Software ist vorzuziehen, da Sie so die Wahl haben, welche Informationen in Ihrem Datensatz enthalten sein sollen und welche nicht. Häufig sind Ausreißer durch Fehler beim Scannen bedingt. Je besser Ihr Scanner also die tatsächliche Oberfläche erfasst und je weniger er sich durch externe Faktoren wie Beleuchtung, Farbe und Reflexionsvermögen ablenken lässt, umso mehr Vertrauen können Sie in die Ergebnisse haben. Die meisten Softwarepakete für die Verarbeitung von Punktwolken oder die Durchführung von Inspektionsaufgaben verfügen über Tools zur individuellen Verwaltung von Ausreißern.
Wenn ich ein Werkstück scanne, erhalte ich am Ende ein CAD-Modell?
Dies ist eines der verbreitetsten Missverständnisse im Bereich Laserscanning. Arm und Scanner erfassen die Geometrie eines Werkstücks im 3D-Punktwolkenformat. Dabei handelt es sich um eine Datei, die nur die einzelnen Punkte und ihre Beziehungen zueinander enthält, aber nicht um eine CAD-Datei. Um eine CAD-Datei zu erstellen, muss aus der Punktwolke ein auf einem Polygonnetz basierendes Modell erstellt werden, dessen Oberflächen und Elemente – häufig in einem CAD-System – als CAD-Modell definiert werden müssen. Dies sind Offlinevorgänge, die erst nach Abschluss der Erfassung der Scandaten stattfinden und den zeitaufwändigsten Teil der Arbeit mit den 3D-Scandaten darstellen. Bei der Abbildung links handelt es sich um eine Punktwolke, in der die Farben wieder die einzelnen Scanvorgänge darstellen, während dieselben Daten in der Abbildung rechts in ein Polygonnetzmodell konvertiert wurden. Dies ist der erste Schritt auf dem Weg zur Umwandlung einer Punktwolke in ein CAD-Modell.step toward a full CAD conversion.
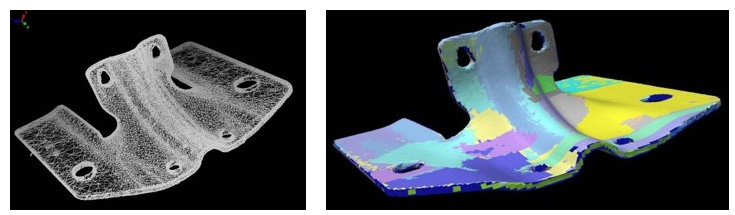