Sobre sondas de escaneamento a laser
A saída de escâner a laser cria um modelo tridimensional de uma superfície, o qual, devido à sua elevada densidade (geralmente milhões de pontos) é chamado de "ponto de nuvem" ou "nuvem de pontos".
Contato
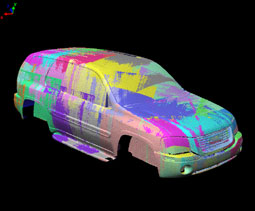
A saída de escâner a laser cria um modelo tridimensional de uma superfície, o qual, devido à sua elevada densidade (geralmente milhões de pontos) é chamado de "ponto nuvem" ou "nuvem de pontos". Mostra um conjunto de nuvem de pontos grandes representando um veículo inteiro. As diversas cores representam diferentes passes de escaneamento individual na peça.
Inspeção-Alvo e Validação
A nuvem de pontos 3D criada pelo 7 axis Absolute Arm combinado com o PC-DMIS pode ser usada para a inspeção dimensional ou GD&T, e os resultados comparados com valores CAD nominais. Com a comparação Cloud-to-CAD, grandes nuvens de pontos podem ser sobrepostas no modelo CAD para inspeção visual rápida de desvios (às vezes chamado de "Weathermap" ou "mapa de cores"). O escaneamento a laser também pode ser usado para a inspeção tradicional (não-CAD) usando o recurso de construção e dimensionamento.
Exemplo de inspeção e validação de aplicações:
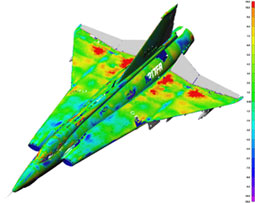
- Verificação se uma peça cumpre CAD, para a inspeção de recebimento, inspeção em processo ou validação final.
- Verificação de dimensões de Tool & Die para determinar o desgaste, avaliar o reparo ou verificar modificações
- Inspeção do primeiro artigo
- Medir o Contorno, comparando peças para modelos CAD, seções transversais 2D ou mapeamento topográfico 3D correspondente.
- Refinamento da linha de produção ou processo de montagem
- Inspeção da combinação de duas peças.
Engenharia reversa é o processo de tomar uma peça física, medi-la para determinar as suas características e o processamento dos dados para a criação de um modelo CAD. Isto é geralmente usado nos casos em que o processo de design de produto tem operação manual significativa, como design automotivo. Apesar dos avanços em CAD, muitos projetos ainda começam como um modelo físico, que precisa então ser transformado em formato eletrônico.
Nuvens de pontos gerados por escaneamento a laser são processadas de várias maneiras para deixá-las prontos para a conversão para CAD. O software de engenharia reversa, como PC-DMIS Reshaper é usado para criar ou importar a nuvem de pontos escaneada, manipular, matematicamente atenuar e combinar os dados escaneados para que um modelo de superfície representante possa ser criado.
Exemplo de aplicações de engenharia reversa:
- Criar um modelo 3D para desenho CAD ou adaptação posterior.
- Caracterização de uma superfície de de modo que uma outra peça possa estar associada a ele.
- Criar um "legado" ou peça "de ouro" onde não existe CAD ou design da peça.
- Criar um modelo "as-built" de uma ferramenta para que o desgaste ao longo do tempo possa ser comparado
- Análise de peça / produto da concorrência
- Arquivamento ou preservação histórica de artefatos para criar um registro 3D ou cópia.
Fresagem de Cópia / Escala Prototipagem Rápida
Réplicas únicas podem não exigir a criação de um modelo de CAD completo. Modelos de litografia estéreos ou moagem à base de CAD, em muitos casos podem ser feitos diretamente a partir dos dados de escaneamento ponto de nuvem ou no modelo de malha. O redimensionamento básico e dimensionamento do modelo podem ser possíveis. O software CAM é usado para ler os dados em nuvem de escaneamento e produzir instruções de usinagem para máquinas-ferramentas CNC.
Exemplos de aplicação:
- Preservação de herança histórica ou cultural do patrimônio, quando artefatos são digitalizados para observar o desgaste ou deterioração
- Prototipagem rápida de modelos artesanais
- Redimensionamento de um modelo de física digitalizada
- Verificação de modelos para efeitos eletrônicos, tais como filmes e videogames
Pergunte-nos sobre as nossas soluções de escaneamento a laser.
Qual é a velocidade de escaneamento?
A velocidade de escaneamento depende significativamente da sonda e campo de visão da sonda. Em sondas a laser em geral, você será capaz de ver os pontos coletados "na tela" em tempo real. Às vezes isso é referido como "pintar a peça". Escanear em diversos ângulos para garantir que toda a geometria relevante seja capturada, muitas vezes resulta em uma nuvem de pontos como a capturada no Sino da Liberdade na figura 3, onde parece que alguém enlouqueceu com tinta spray.
Também relevante para a velocidade total é a competência do número de pontos do escâner por segundo, a largura do caminho do escaneamento, e a densidade de pontos por linha. A animação abaixo compara a diferença entre dois escâneres diferentes, um com uma faixa estreita e um com uma faixa larga, capturando uma placa plana de 1 metro quadrado em um campo de meados de vista. O escâner com uma (105 milímetros) largura de linha mais ampla em visão de meio de campo, capta a superfície em menos de 3 minutos, em que o escâner com a largura da linha mais estreita levaria mais de 13 minutos na mesma peça.
O aplicativo pode ser um fator que contribui para a escolha do escâner. Aplicações onde a velocidade e cobertura são extremamente importantes, mas pequenos detalhes não, podem exigir um escâner com uma velocidade maior. Outras aplicações com peças menores e mais complexas, podem funcionar melhor com uma largura de banda menor. Alguns escâneres, como o HP-L-20.8 permitem que o usuário selecione uma largura de banda que melhor corresponde ao aplicativo.
Escâner com Largura Estreita | Escâner com Largura Ampla |
Largura da linha 44 milímetros na visão de meio do campo | Largura da linha 105 milímetros na visão de meio do campo |
23 passes para pintar a chapa | 10 passes para pintar a chapa |
Espaçamento de 1 milímetro de linha, 13 min, 2 segundos | Espaçamento entre linhas 1 milímetro, 2 min 50 segundos |
Isso depende, em parte, de como você pretende usar os dados. Superfícies que são extremamente complexas com muita curvatura irão se beneficiar com o escaneamento de maior densidade. Superfícies mais achatadas, nem tanto. Extração de recursos de características tais como buracos, compartimentos, cilindros e outras formas prismáticas e também bordas irão se beneficiar de dados de alta densidade também. Considere as duas imagens abaixo, que são cópias idênticas de um buraco de 15 milímetros. A cópia à esquerda foi criada com uma sonda de escaneamento de baixa densidade, e a da direita com uma sonda V5 top de linha. A extração e formação da medição do buraco no lado direito tende a ser mais precisa com os dados de maior densidade. Dados de maior densidade irão capturar texturas de forma mais eficaz, se isso for importante para você.
Pergunte-nos sobre as nossas soluções de escaneamento a laser.
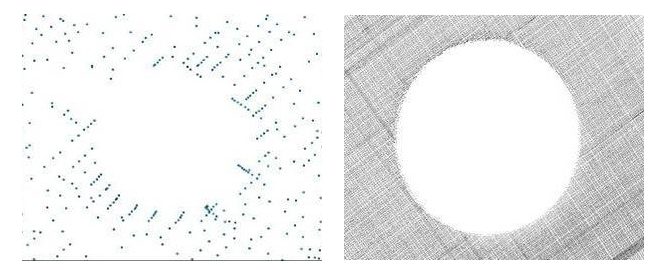
A luz ambiente afeta o sensor?
Muitas vezes, vários tipos de iluminação em um laboratório, estúdio e ambientes fabris podem ter um efeito adverso sobre um dispositivo óptico. Enquanto alguns tipos de dispositivos de escaneamento devem ter um ambiente de luz controlada, este não é o caso de sondas utilizadas nos braços Romer. Braços Romer equipados com escâneres a laser empregam uma variedade de técnicas para superar os efeitos da luz ambiente, incluindo filtros ópticos e controles de exposição, que são projetados para ignorar comprimentos de onda da luz exceto aqueles perto do laser a ser utilizado. O efeito final é que luzes de lâmpadas incandescentes, de vapor de mercúrio, halogênio e outros sistemas de iluminação populares são rejeitadas e não afetam o sensor.
As condições da superfície afetam o sensor a laser?
Tradicionalmente a precisão da medição foi afetada por acabamentos de superfície. Superficies de cromo altamente polido e pretas brilhantes foram as mais difíceis de escanear. Superfícies multi-coloridas ou superfícies em que a transição na refletividade também pode causar problemas para muitos escâneres. Braços Romer equipados com escâneres a laser e empregam ferramentas para lidar com estas situações, permitindo que a maioria das superfícies e as cores a sejam verificadas com sucesso. O nosso sensor premium HP-L-20.8 emprega controle automático de exposição e a tecnologia flying dot que permite que ele se ajuste automaticamente e em tempo real às mudanças na cor do material e refletividade, tornando mais fácil e possível o escaneamento de quase qualquer objeto. Na foto à direita, uma peça com três cores diferentes e acabamentos de superfície e diferentes graus de refletividade é facilmente verificada com o HP-L-20.8.
Você precisa pulverizar as peças?
Em todas, menos as superfícies mais transparentes, a resposta é não. A preparação de superfície por pulverização com um pó (para reduzir a refletividade e criar uma superfície uniforme) é indesejável por várias razões, que vão desde o tempo extra necessário para preparar a superfície, até o acréscimo da variabilidade da medição do próprio pó (estudos mostram este pode ter até 100 mícrons / 0,004" de variabilidade de medição). Enquanto as peças precisavam ser pulverizadas antigamente, hoje isso não é mais necessário.
A temperatura e o ambiente afetam o sensor?
Ambientes fabris e lojas de máquina tradicionais são aceitáveis para o funcionamento dos braços Romer com escâneres a laser. Os sensores não são adequados para ambientes de pulverização de água ou óleo diretos, pois eles podem aderir ao laser e às lentes da câmera. A temperatura deve normalmente estar entre 15 e 35°C e a umidade entre 0 e 90% sem condensação. Ambientes onde a sujeira, óleo ou outros contaminantes estão presentes que podem aderir ao sensor devem ser evitados, pois isso pode influenciar o desempenho da medição. Estes sensores podem funcionar 24 horas/7 dias por semana em ambientes fabris durante muitos anos.
Dados filtrados vs. Não filtrados ... Qual é a verdadeira diferença?
Dados filtrados são dados do sensor que foram "filtrados" ou "processados" enquanto a nuvem de pontos está sendo gerada. Isto é geralmente feito pelos pacotes de software de terceiros enquanto os dados do sensor estão sendo lidos no software. Os dados do sensor brutos são comprometidos, porque estão sendo filtrados, “enquanto capturados” e, assim, a qualidade dos dados é desconhecida.
Dados não filtrados são dados do sensor em seu estado bruto, incluindo todos os dados discrepantes, independente de sua causa. Os dados originais podem ser avaliados de forma independente. Usar dados não filtrados proporciona a verdadeira competência da capacidade dos sensores de verificar com precisão; para comparar os dados verdadeiros aos dados nominais (impressão ou CAD).
A capacidade de capturar dados brutos, não filtrados de escaneamento independente de qualquer software de terceiros é preferível, simplesmente porque ele permite que você decida o que faz e não quer incluir em seu conjunto de dados. Muitas vezes, os dados não são lidos devido ao baixo desempenho do escâner, de modo que um escâner melhor é capaz de captar a verdadeira superfície e não ser "enganado" por fatores externos, tais como iluminação, cor e refletividade da superfície, e você tem mais confiança nos resultados. A maioria dos pacotes de nuvens de pontos ou pacotes de inspeção têm ferramentas para remover ou ignorar os dados discrepantes ao seu critério.
Quando eu escanear uma peça, eu obtenho um modelo CAD quando terminar?
Este é talvez o aspecto mais amplamente mal compreendido de escaneamento a laser. O braço e o escâner capturam a geometria da peça em um formato de ponto de nuvem 3D. Isto é simplesmente um arquivo dos pontos em relação ao outro, não é um arquivo CAD. Para obter um arquivo CAD, você precisa primeiro criar algum tipo de modelo de polígono a partir de nuvens de pontos e, em seguida, trabalhar para caracterizar as superfícies e recursos como um modelo CAD, muitas vezes em um sistema CAD. Estes são processos off-line que ocorrem uma vez que a coleta e verificação de dados for concluída, e é realmente a parte mais demorada de se trabalhar com dados de escaneamento 3D. A imagem à esquerda é nuvem de pontos, mais uma vez, mostrando as diversas áreas digitalizadas como diferentes manchas de cor, o modelo do lado direito são os mesmos dados convertido em um modelo de malha de polígono, apenas o primeiro passo em direção a uma conversão CAD completa.
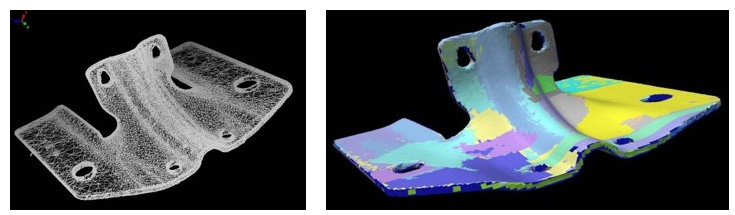