Technologie de mesure intégrée pour une qualité maximale
Schmehmann Rohrverformungstechnik Gmbh - Allemagne
Contactez-nous
.jpg?h=428&iar=0&w=800&hash=6336A528C4CDDA6426C0065C9AFE164A)
AICON TubeInspect, la solution complète d’inspection et de production pour un fabricant leader dans la reproduction
d’éléments de tubesSituation de départ : une centrale électrique quelque part en Europe, exploitée depuis de nombreuses années, voire des décennies. Un composant, par exemple un coude de brûleur, a subi des dommages et doit être remplacé dans les plus brefs délais. La pièce de rechange doit être disponible immédiatement, puisque les arrêts sont très coûteux. Schmehmann Rohrverformungstechnik GmbH détient la solution.L’ingénierie dans le domaine des centrales électriques fait partie des activités clés de la société Schmehmann Rohrverformungstechnik GmbH, établie à Bad Marienberg, en Allemagne. De nombreuses centrales sont équipées de pièces pour lesquelles il n’existe plus de plans ou de données CAO. Si de tels composants subissent des dommages et doivent être remplacés, la rapidité et la précision dimensionnelle sont d’une importance capitale.
Avec cette technologie phare, nous pouvons aujourd’hui traiter des commandes que nous n’aurions pas pu honorer par le passé. L’entreprise reçoit les premières données clés de la part de l’opérateur de la centrale ou du fournisseur de services et peut préparer au moyen de ces informations la matière brute et la machine. Le client enlève la pièce défectueuse et l’apporte à Schmehmann, qui la mesure en l’espace de quelques secondes avec le système AICON TubeInspect. Le logiciel BendingStudio détermine les données géométriques pour le programme de cintrage et génère une fiche technique complète du composant.
L’entreprise fabrique immédiatement la pièce de rechange, la remesure avec le système TubeInspect et la compare aux données nominales. Comme l’ensemble du processus dure à peine deux heures, le chauffeur peut attendre et retourner à la centrale avec la nouvelle pièce dès que celle-ci est prête. La vitesse joue un rôle essentiel, car les temps d’arrêt dans une centrale électrique engendrent des coûts élevés et sont limités au maximum si l’exploitation peut se poursuivre rapidement.

Machines communicantes - l’industrie 4.0 dans la pratique
Le processus dans l’usine de Bad Marienberg montre à la perfection comment il est possible d’intégrer directement la technologie de mesure dans le processus de production et d’interconnecter des machines pour obtenir un gain d’efficacité. L’entreprise fait partie du groupe Menk- Schmehmann, qui possède sept usines dans quatre pays. Le fabricant réalise entre autres des radiateurs de refroidissement, des chauffe-eau de grandes dimensions et des structures soudées, en offrant toutes les techniques de formage de tubes et de soudage possibles.L’usine compte une soixantaine d’employés et est spécialisée dans le cintrage de tubes, les bobines plates et dans les technologies pour centrales électriques. Les composants ont un diamètre entre 6 et 219 millimètres, et les lots varient entre 1 et 5 000 pièces. Comme l’usine fabrique ses propres outils, elle peut répondre d’une manière flexible aux besoins particuliers des clients. Les utilisateurs sont issus de différents secteurs, notamment la production d’électricité, la construction navale et mécanique, l’industrie pétrochimique, la fabrication de chauffe-eau, la construction d’appareils chimiques, les techniques de chauffage et de refroidissement, l’agroalimentaire et l’industrie du divertissement.
La communication entre l’homme, la machine et le produit – en d’autres termes, l’usine connectée – est à la base de l’industrie 4.0. Schmehmann a intégré le système AICON TubeInspect directement dans ses processus de fabrication et l’a raccordé à ses cintreuses de tubes provenant de différents constructeurs. Le logiciel BendingStudio commande les mesures et transfère les données de cintrage et de correction directement aux cintreuses.
BendingStudio relie aussi la préparation du travail, les stations de fabrication et l’assurance qualité. Toutes les données sont enregistrées sur un serveur central et peuvent être éditées à partir de différentes stations. Lors de la réception d’un ordre de fabrication d’un nouveau composant, la préparation du travail dans BendingStudio crée le nouveau composant et génère les données nécessaires pour le programme de cintrage sur la base de plans en majorité analogiques. Grâce à la solution serveur, après la validation du programme de cintrage, l’équipe de fabrication peut y accéder directement et démarrer la production, ce qui rend le processus fluide.
« Insérer la pièce, appuyer sur le bouton. Terminé »
Le site de Bad Marienberg utilise le système AICON TubeInspect depuis fin 2014. Le système de mesure optique de tubes et de fils accomplit trois tâches principales dans l’unité de production : il relève des prototypes pour la fabrication de pièces de rechange (rétroconception), teste des composants de série (à 100 %), configure et corrige les cintreuses.Le système a été spécialement développé pour une assurance qualité efficace des tubes et fils cintrés. Au moyen de caméras numériques de haute résolution, il acquiert l’objet à mesurer en quelques secondes. Benjamin Schmidt, directeur de la planification du process chez Schmehmann, résume la procédure de mesure avec la phrase suivante : « Insérer la pièce, appuyer sur le bouton. Terminé ». Grâce à sa vitesse et à sa compatibilité avec les cintreuses, TubeInspect apporte un gain de temps considérable au quotidien.
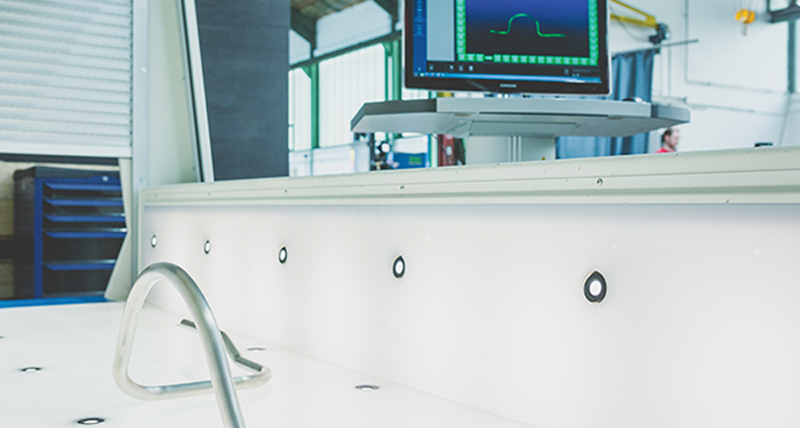
L’application du nouveau système de mesure a permis de tenir compte d’exigences spéciales des clients. Aujourd’hui, l’entreprise reçoit des commandes pour la fabrication de composants cintrés avec un écart géométrique toléré maximal de 0,2 millimètre qui doivent faire l’objet d’un contrôle intégral. À chaque composant est attribué un code QR à travers lequel le client a accès à toutes les données de mesure et peut visualiser les données de production à tout moment.
Depuis l’introduction de TubeInspect, il est possible de mesurer des composants de forme quelconque ou à cintrage multiple. La transmission automatique des valeurs de correction aux cintreuses, tout comme la rétroconception, sont également de précieuses innovations, devenues accessibles grâce à TubeInspect. Et la documentation détaillée établie par le système à l’intention du client renforce la sécurité des deux côtés. Entre-temps, les processus de travail sont presque complètement conçus pour la mesure 3D optique.