Zintegrowana technologia pomiarowa dla uzyskania maksymalnej jakości
Schmehmann Rohrverformungstechnik Gmbh - Niemcy
Kontakt
.jpg?h=428&iar=0&w=800&hash=6336A528C4CDDA6426C0065C9AFE164A)
AICON TubeInspect - pełne rozwiązanie do kontroli i produkcji dla wiodącego niemieckiego producenta elementów rur
Elektrownia gdzieś w Europie, działająca od wielu lat, a nawet dziesięcioleci. Element gięty palnika został uszkodzony i musi zostać wymieniony możliwie jak najszybciej. Natychmiast potrzebna jest część zamienna, ponieważ przestój jest kosztowny. Firma Schmehmann Rohrverformungstechnik GmbH oferuje rozwiązanie tej kłopotliwiej sytuacji.Usługi świadczone dla sektora energetycznego to jeden z najważniejszych aspektów działalności przedsiębiorstwa Schmehmann Rohrverformungstechnik GmbH z siedzibą w niemieckiej miejscowości Bad Marienberg. Istnieje wiele budynków elektrowni posiadających elementy, które nie mają już rysunków lub danych CAD. W przypadku uszkodzenia, gdy dany element musi zostać wymieniony, szybkość oraz dokładność wymiarowa stanowi najważniejszą kwestię.
Dzięki tej przełomowej i pionierskiej technologii zyskaliśmy obecnie dostęp do zamówień, których w przeszłości nie bylibyśmy w stanie zrealizowaćPrzedsiębiorstwo otrzymuje wstępne informacje z pierwszymi kluczowymi danymi od operatora elektrowni bądź dostawcy usług, na podstawie których może przygotować surowiec oraz maszynę. Klient usuwa wadliwy element i przywozi go do firmy Schmehmann, gdzie jest następnie mierzony zaledwie w kilka sekund za pomocą systemu AICON TubeInspect. Dane dotyczące geometrii dla programu gięcia wyznaczane są dzięki zastosowaniu oprogramowania BendingStudio. Następnie tworzony jest pełen arkusz danych.
W kolejnej fazie następuje natychmiastowa produkcja części zamiennej, która po raz kolejny jest mierzona za pomocą systemu TubeInspect i porównywana z danymi nominalnymi. Ponieważ cały proces trwa zaledwie około dwóch godzin, kierowca ciężarówki może poczekać na miejscu i odjechać z parkingu zakładów do elektrowni z nową częścią zamienną, gdy tylko będzie ona gotowa. Szybka akcja jest istotna, ponieważ przestój w pracy elektrowni generuje wysokie koszty. Jeśli zapewniony jest szybki powrót do pracy, przestój ograniczony jest do minimum.

Komunikacja Maszyn - Idea "Industry 4.0" (Przemysł 4.0) w Praktyce
Proces w fabryce Bad Marienberg stanowi świetny przykład w jaki sposób technologia pomiarowa może zostać bezpośrednio zastosowana w procesie produkcji i w jaki sposób maszyny mogą zostać połączone w celu uzyskania większej wydajności. Firma należy do grupy Menk-Schmehmann, która posiada siedem zakładów w czterech krajach. Grupa przedsiębiorstw produkuje m.in. radiatory chłodzące, wielkogabarytowe kotły oraz konstrukcje spawane, a także oferuje wszystkie możliwości tworzenia rur wraz z technologią spawania z pojedynczego źródła.Firma zatrudnia około 60 pracowników i specjalistów w dziedzinie gięcia rur, cewek płaskich oraz technologii elektrowni. Elementy posiadają średnicę od 6 do 219 milimetrów, a wielkość partii wynosi od 1 do 5000 części. Ponieważ zakłady wytwarzają swoje własne narzędzia, elastycznie reagują i odpowiadają na indywidualne wygania klientów. Klienci działają w różnych sektorach przemysłu, takich jak energetyka, przemysł stoczniowy, inżynieria mechaniczna, petrochemikalia, produkcja kotłów, budowa aparatury chemicznej, technologia grzewcza i chłodnicza, a także przemysł spożywczy oraz rozrywkowy.
Komunikacja między ludźmi, maszynami i produktami -inteligentna, połączona fabryka - stanowi trzon idei Przemysłu 4.0. W zakładach Schmeh-mann system AICON TubeInspe został bezpośrednio wdrożony do procesów produkcji i połączony z giętarkami różnych producentów. Platforma oprogramowania BendingStudio kontroluje pomiary i przekazuje dane procesu gięcia oraz dane korekcyjne bezpośrednio do giętarek.
Program BendingStudio łączy również przygotowanie do pracy oraz stanowiska robocze we wszystkich fazach produkcji aż do etapu kontroli jakości. Wszystkie dane przechowywane są na serwerze głównym i mogą być edytowane z różnych stanowisk roboczych. Po otrzymaniu zamówienia dotyczącego produkcji nowego elementu podczas fazy przygotowania do pracy w oprogramowaniu BendingStudio tworzone są nowe elementy i - na podstawie najbardziej analogowych rysunków - generowane dane wymagane do programu gięcia. Dzięki serwerowi, po akceptacji programu gięcia, personel odpowiedzialny za produkcję otrzymuje do niego bezpośredni dostęp i rozpoczyna produkcję, zapewniając bezproblemowy oraz gładki proces produkcji.
"Włóż część, naciśnij przycisk i gotowe"
System AICON TubeInspect stosowany jest w zakładach w Bad Marienberg od 2014 roku. Optyczny system pomiarowy rur i przewodów pełni trzy główne funkcje w procesie produkcji - mierzy prototypy do produkcji części zamiennych (inżynieria odwrotna); testuje elementy seryjne (100 procentowe testowanie), a także wprowadza korektę ustawień giętarek.System został specjalnie opracowany z myślą o efektywnej kontroli jakości giętych rur i przewodów. Dzięki zastosowaniu wysokiej rozdzielczości kamer cyfrowych, część może zostać zmierzona zaledwie w kilka sekund. Benjamin Schmidt, Dyrektor Działu Planowania Procesu w firmie Schmehmann, w kilku słowach podsumowuje proces pomiarowy: "Włóż część, naciśnij przycisk i gotowe". Ponieważ system TubeInspect jest szybki i współdziała z giętarkami, pozwala na sporą oszczędność czasu podczas codziennej pracy.
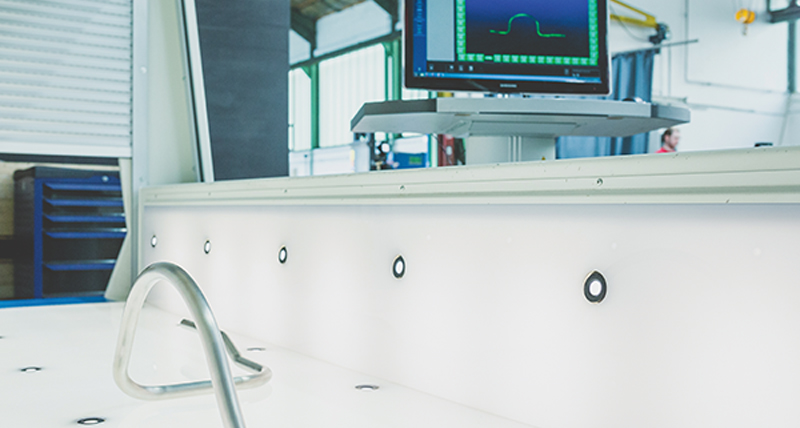
i przetworzyć. Dział produkcji musiał zrozumieć i zaakceptować nowe procedury" - dodaje Schmidt.
Dzięki wprowadzeniu nowego systemu pomiarowego możliwa stałą się realizacja specjalnych potrzeb i wymagań klientów. Obecnie firma otrzymuje zamówienia dotyczące produkcji elementów giętarek z maksymalną dozwoloną odchyłką geometryczną wielkości 0,2 milimetrów. Takie elementy muszą zostać poddane 100% kontroli. Każdy element posiada kod QR (kod szybkiej odpowiedzi), dzięki któremu klient otrzymuje dostęp do wszystkich danych pomiarowych i wgląd do danych produkcyjnych w dowolnym czasie.
Dzięki zastosowaniu TubeInspect możliwa stała się również kontrola form o dowolnych kształtach lub geometrii typu "bend-in bend" (gięcie po gięciu). Automatyczne przekazywanie wartości korekcji do giętarek oraz inżynieria odwrotna stanowią wartościowe innowacje, które oferuje system TubeInspect. Dodatkowo szczegółowa dokumentacja systemu zapewnia klientowi dodatkowe zabezpieczenie. Równolegle procesy robocze niemal całkowicie zostały zaprojektowane i dostosowane do procesu pomiarowego 3D.