Una solución integrada para una línea de producción mas rápida
GKN Driveline - Suecia
Contacto

GKN ve más allá cuando se trata de planear la producción: su planta en Koping, Suecia, desarrolla, fabrica y ensambla las piezas más importantes de los sistemas de propulsión de cuatro ruedas de muchos de los automóviles actuales. Jan Engström trabaja como ingeniero de producción en el departamento de manufactura de rueda plana y es responsable de las 34 máquinas de procesamiento que trabajan las 24 horas. Junto con Hexagon, Engström ha estado involucrado en un proyecto que cambiará el proceso que usa GKN para medir las piezas.
Anteriormente usábamos juegos de calibres de medición para efectuar mediciones de control de nuestros productos,” explica Engström. “El problema era que con cada nuevo detalle que producíamos, era necesario adquirir los calibres adecuados. Cuando recibíamos pedidos de varios productos nuevos necesitábamos una solución más flexible.”
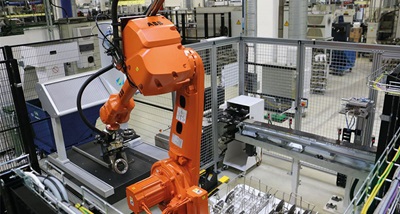
Trabajando juntos para encontrar la solución correcta
GKN ha detectado la necesidad de un sistema de alta calidad, flexible y rápido para la medición de piezas, que no provoque un cuello de botella en la producción. El proyecto inició cuando Engström se reunió con personal de Hexagon para encontrar la solución correcta para un proceso de medición en línea. El resultado final fue la instalación de una solución automatizada en la cual una máquina de medición por coordenadas (MMC) GLOBAL Shop Floor, equipada con el software PC-DMIS ha sido integrada a la línea de producción. Esta es la primera vez que GKN incorpora una máquina de medición en un módulo de producción; ya que anteriormente las piezas se tomaban de la línea de producción y se llevaban a un cuarto de medición para su análisis. El lento proceso de inspección provocaba costosos retrasos de producción, mientras que el nuevo sistema permite efectuar el mismo proceso en tan solo 90 segundos – un ahorro considerable de tiempo.
La flexibilidad también fue un factor importante para GKN Driveline al elegir la MMC correcta, ya que la empresa requería medir rápidamente diferentes piezas para diferentes clientes. La solución completa de Hexagon ha ofrecido esto y más, ya que las nuevas piezas se pueden medir directamente en el módulo de producción. Los cambios de las piezas son más rápidos gracias a la eliminación de algunos procesos innecesarios, por lo que el tiempo de espera se reduce a intercambiar elementos de fijación y programación.
“Se trata de una planificación a largo plazo,” explicó Engström. “Comparada con los calibres, la MMC es una opción muy flexible ya que es posible medir cualquier objeto que se coloque sobre la mesa. Ahora es posible comenzar a producir directamente todos los productos nuevos. Asimismo, se libera tiempo en la sala de medición, ya que la máquina de medición puede manejar controles adicionales que no sería posible usar con los calibres.”
Actualmente GKN cuenta con diez MMCs de Hexagon en de la fábrica, lo cual otorga a la empresa fiabilidad en el equipo humano y en las máquinas. Esta confianza fue una de las principales razones para decidir que la GLOBAL Shop Floor se incorporara al módulo de producción.
La integración mejora la eficiencia
La MMC es la primera que GKN ha instalado como parte de un módulo automatizado de producción, donde se conecta a un torno y a un robot. Cada detalle se mide y los datos de medición se envían continuamente de la máquina de medición al torno, después se compensa según los valores de tolerancia hacia el valor nominal. Es importante medir el 100% de las piezas dentro del módulo con alta precisión.Son varios los beneficios de incorporar la MMC en la línea de producción, uno de los cuales es que el tiempo de producción es menor gracias al nuevo sistema de control de calidad... y la calidad lleva a la productividad.
“Los datos de calidad con los que ahora contamos son sobresalientes, comparados con los datos que recibíamos antes,” comentó el líder del proyecto Johan Bäckströ.
Otro beneficio es la velocidad, ya que ahora en GKN es posible medir dos piezas simultáneamente, lo cual duplica el tiempo ahorrado. Ya que el tiempo de producción ha sido reducido con la incorporación de la MMC a la línea de producción, se ha incrementado la velocidad de la producción en su totalidad.
Hexagon también ha diseñado un programa de capacitación personalizado para esta línea de producción en particular y ha lo ha aplicado in situ en Koping.
Bäckström añade: “La máquina es muy fácil de usar y hemos recibido la capacitación y el soporte necesarios. Hexagon vino a nuestra fábrica y capacitó a todos los que trabajan en la línea para aprender el uso de la MMC.”
Los beneficios incluyen el ahorro de costos, la facilidad de uso y el soporte técnico
Al ahorrar tiempo también se ahorra en los costos, ya que es más fácil medir diferentes piezas con solo cambiar el programa y los elementos de sujeción y no todo el procesode medición. Anteriormente cada vez que se efectuaba una inversión en un nuevo calibre, el costo aproximado era de 250 000 SEK. Actualmente, el ahorro en cada nuevo detalle es de más de 200 000 SEK, ya que se hace un calibre de configuración a un costo mucho menor.
GKN tiene muchos proyectos nuevos que requieren nuevos calibres de medición, pero esto ya no representa un problema ya que esta máquina de medición dinámica proporciona una solución adaptable y de larga duración.