Zintegrowane rozwiązanie dla szybszej linii produkcyjnej
GKN Driveline - Sweden
Kontakt

GKN Driveline jest jednym z wiodących dostawców elementów i systemów układu napędowego. Oferuje szeroką gamę elementów układu napędowego stosowanych zarówno w najmniejszych i niezwykle ekonomicznych samochodach, jak i najbardziej wyrafinowanych pojazdach najwyższej jakości, które wymagają najbardziej złożonej dynamiki jazdy. Jako przedsiębiorstwo o globalnym zasięgu, GKN współpracuje z największymi światowymi producentami. Dlatego ta szwedzka firma musiała znaleźć partnera metrologicznego, który pomógłby jej wyjść na przeciw coraz większym oczekiwaniom dotyczącym zwiększenia produkcji i dokładności. Hexagon Manufacturing Intelligence podziela wizję GKN Driveline dotyczącą optymalizacja procesu pomiarowego w celu zwiększenia szybkości, jednak bez utraty dokładności. Właśnie dlatego wybrano nas na partnera.
GKN wychodzi myślą na przód, gdy chodzi o planowanie produkcji. Zakłady w szwedzkim mieście Koping opracowują, produkują i montują najważniejsze elementy napędu na cztery koła dla większości dzisiejszych samochodów. Jan Engström pracuje jako Inżynier Produkcji w jakże ważnym dziale produkcji kół. Odpowiedzialny jest za 34 maszyny obróbkowe, które działają 24 godziny na dobę. Wraz z firmą Hexagon, Engström brał udział w realizacji projektu, który zmieni procesy pomiaru części stosowane w GKN.
“W przeszłości używaliśmy sprawdzianów do przeprowadzenia pomiarów naszych produktów” - tłumaczy Engström. "Jednak wadą tego urządzenia było to, że do pomiaru każdego nowego detalu, który wyprodukowaliśmy, musieliśmy zakupić nowy, pasujący sprawdzian. Gdy otrzymaliśmy zlecenia dotyczące realizacji kilku nowych produktów, potrzebowaliśmy bardziej elastycznego rozwiązania" - tłumaczy inżynier.
Elastyczność także stanowiła ważny czynnik dla GKN Driveline w momencie wyboru właściwej współrzędnościowej maszyny pomiarowej, ponieważ firma musiała szybko mierzyć różne części dla różnych klientów. Wszechstronne rozwiązanie Hexagon umożliwiło realizację tego zadania, a także wielu innych, ponieważ nowe części obecnie mogą być kontrolowane w celi pomiarowej. Wymiana części do pomiaru przebiega szybciej, dlatego że zrezygnowano z kilku zbędnych procesów, dzięki czemu czas kontroli ograniczono do wymiany uchwytów i programowania.
“Wszystko opiera się na długoterminowym planowaniu” - mówi Engström. "W porównaniu ze sprawdzianami, współrzędnościowa maszyna pomiarowa stanowi elastyczne rozwiązanie, ponieważ może mierzyć wszystko, co położymy na stole pomiarowym. Dzięki temu możemy teraz od razu rozpocząć produkcję wszystkich nowych produktów. Oszczędziliśmy czas w laboratorium pomiarowym, ponieważ maszyny mogą przeprowadzić dodatkowe kontrole, czego nie mógł zrobić sprawdzian" - dodaje inżynier.
GKN obecnie posiada dziesięć współrzędnościowych maszyn pomiarowych Hexagon. Pracownicy firmy pokładają w nich duże zaufanie. Właśnie zaufanie było jednym z głównych powodów wyboru GLOBAL Shop Floor do integracji w celi pomiarowej.
Zastosowanie współrzędnościowej maszyny pomiarowej na linii produkcyjnej przyniosło wiele korzyści - jedną z nich jest szybsza produkcja dzięki nowemu systemowi kontroli jakości. A jakość faktycznie zwiększa wydajność.
“Dane dotyczące jakości, które obecnie pozyskujemy, są nadzwyczajne w porównaniu z danymi, które otrzymywaliśmy wcześniej” - mówi Lider Zespołu - Johan Bäckström.
Inna korzyść to szybkość - teraz GKN może mierzyć dwa elementy na raz, podwójnie oszczędzając czas. Ponieważ zredukowano czas produkcji dzięki zastosowaniu współrzędnościowej maszyny pomiarowej na linii produkcyjnej, zwiększyła się szybkość całej produkcji. Firma Hexagon opracowała również dostosowany do potrzeb klienta program szkoleniowy, stworzony z myślą o tej szczególnej linii produkcyjnej. Szkolenie odbyło się w zakładach w Koping.
Bäckström komentuje: “Maszyna jest łatwa w użyciu. Do tego otrzymaliśmy szkolenie i wsparcie, którego potrzebowaliśmy. Firma Hexagon przyjechała do naszej fabryki i przeszkoliła każdą osobę pracującą na linii, jak należy obsługiwać współrzędnościową maszynę pomiarową" - wspomina inżynier.
GKN realizuje wiele nowych projektów, które wymagają zastosowania nowych sprawdzianów. Jednak nie jest to już problemem, ponieważ dynamiczna maszyna pomiarowa stanowi trwałe, dostosowane do realizowanych zadań rozwiązanie.
GKN wychodzi myślą na przód, gdy chodzi o planowanie produkcji. Zakłady w szwedzkim mieście Koping opracowują, produkują i montują najważniejsze elementy napędu na cztery koła dla większości dzisiejszych samochodów. Jan Engström pracuje jako Inżynier Produkcji w jakże ważnym dziale produkcji kół. Odpowiedzialny jest za 34 maszyny obróbkowe, które działają 24 godziny na dobę. Wraz z firmą Hexagon, Engström brał udział w realizacji projektu, który zmieni procesy pomiaru części stosowane w GKN.
“W przeszłości używaliśmy sprawdzianów do przeprowadzenia pomiarów naszych produktów” - tłumaczy Engström. "Jednak wadą tego urządzenia było to, że do pomiaru każdego nowego detalu, który wyprodukowaliśmy, musieliśmy zakupić nowy, pasujący sprawdzian. Gdy otrzymaliśmy zlecenia dotyczące realizacji kilku nowych produktów, potrzebowaliśmy bardziej elastycznego rozwiązania" - tłumaczy inżynier.
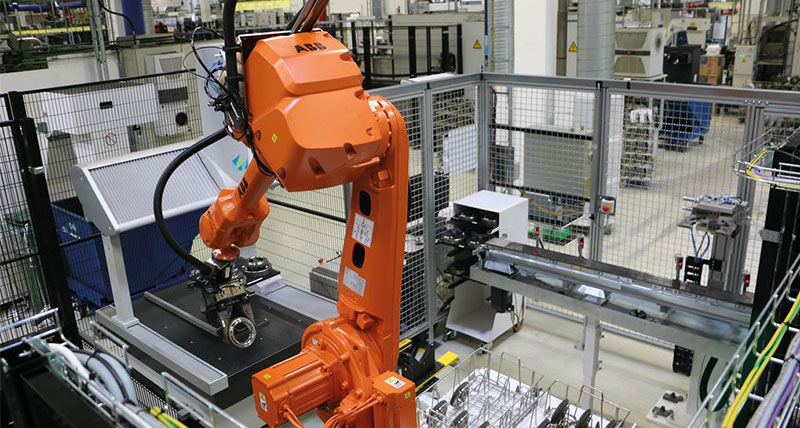
Współpraca w Celu znalezienia Właściwego Rozwiązania
Firma GKN potrzebowała wysokiej jakości, elastycznego i szybkiego systemu do pomiaru części, które nie spowalniałoby produkcji. Projekt ruszył, gdy Engström rozpoczął rozmowy z Hexagon odnośnie znalezienia właściwego rozwiązania do pomiaru na linii produkcyjnej. W rezultacie stworzono automatyczne rozwiązanie składające się ze współrzędnościowej maszyny pomiarowej GLOBAL Shop Floor oraz współdziałającego z nią oprogramowania PC-DMIS. System wprowadzono na linię produkcyjną. To wtedy firma GKN po raz pierwszy "osadziła" maszynę pomiarową w celi produkcyjnej - wcześniej części były przenoszone z linii produkcji do laboratorium pomiarowego, gdzie przeprowadzano kontrolę. Długotrwały proces pomiarowy powodował kosztowne opóźnienia w produkcji. Natomiast po zastosowaniu nowego systemu ten sam proces był przeprowadzany zaledwie w 90 sekund, co pozwoliło na znaczną i jakże cenną oszczędność czasu.Elastyczność także stanowiła ważny czynnik dla GKN Driveline w momencie wyboru właściwej współrzędnościowej maszyny pomiarowej, ponieważ firma musiała szybko mierzyć różne części dla różnych klientów. Wszechstronne rozwiązanie Hexagon umożliwiło realizację tego zadania, a także wielu innych, ponieważ nowe części obecnie mogą być kontrolowane w celi pomiarowej. Wymiana części do pomiaru przebiega szybciej, dlatego że zrezygnowano z kilku zbędnych procesów, dzięki czemu czas kontroli ograniczono do wymiany uchwytów i programowania.
“Wszystko opiera się na długoterminowym planowaniu” - mówi Engström. "W porównaniu ze sprawdzianami, współrzędnościowa maszyna pomiarowa stanowi elastyczne rozwiązanie, ponieważ może mierzyć wszystko, co położymy na stole pomiarowym. Dzięki temu możemy teraz od razu rozpocząć produkcję wszystkich nowych produktów. Oszczędziliśmy czas w laboratorium pomiarowym, ponieważ maszyny mogą przeprowadzić dodatkowe kontrole, czego nie mógł zrobić sprawdzian" - dodaje inżynier.
GKN obecnie posiada dziesięć współrzędnościowych maszyn pomiarowych Hexagon. Pracownicy firmy pokładają w nich duże zaufanie. Właśnie zaufanie było jednym z głównych powodów wyboru GLOBAL Shop Floor do integracji w celi pomiarowej.
Integracja Zwiększa Wydajność
Współrzędnościowa maszyn pomiarowa jest pierwszym urządzeniem zainstalowanym jako część automatycznej celi pomiarowej, w której została podłączona do tokarki i robota. Każdy detal jest mierzony, a dane pomiarowe stale przesyłane z maszyny pomiarowej do tokarki, która przeprowadza kompensację w granicach tolerancji do poziomu wartości nominalnej. Ważne jest, aby z dużą dokładnością zmierzyć 100% części w celi pomiarowej.Zastosowanie współrzędnościowej maszyny pomiarowej na linii produkcyjnej przyniosło wiele korzyści - jedną z nich jest szybsza produkcja dzięki nowemu systemowi kontroli jakości. A jakość faktycznie zwiększa wydajność.
“Dane dotyczące jakości, które obecnie pozyskujemy, są nadzwyczajne w porównaniu z danymi, które otrzymywaliśmy wcześniej” - mówi Lider Zespołu - Johan Bäckström.
Inna korzyść to szybkość - teraz GKN może mierzyć dwa elementy na raz, podwójnie oszczędzając czas. Ponieważ zredukowano czas produkcji dzięki zastosowaniu współrzędnościowej maszyny pomiarowej na linii produkcyjnej, zwiększyła się szybkość całej produkcji. Firma Hexagon opracowała również dostosowany do potrzeb klienta program szkoleniowy, stworzony z myślą o tej szczególnej linii produkcyjnej. Szkolenie odbyło się w zakładach w Koping.
Bäckström komentuje: “Maszyna jest łatwa w użyciu. Do tego otrzymaliśmy szkolenie i wsparcie, którego potrzebowaliśmy. Firma Hexagon przyjechała do naszej fabryki i przeszkoliła każdą osobę pracującą na linii, jak należy obsługiwać współrzędnościową maszynę pomiarową" - wspomina inżynier.
Korzyści Obejmują Oszczędność Kosztów, Łatwe Użytkowanie i Wsparcie Techniczne
Oszczędność czasu często wiąże się również z oszczędnością kosztów - łatwiej jest zmierzyć różne części jedynie zmieniając program i uchwyty niż cały proces pomiarowy. Wcześniej, gdy inwestowano w nowy sprawdzian, koszt ten wynosił około 250 000 SEK. Obecnie oszczędność na każdym nowym detalu wynosi ponad 200 000 SEK, ponieważ wzorzec nastawczy kosztuje znacznie mniej.GKN realizuje wiele nowych projektów, które wymagają zastosowania nowych sprawdzianów. Jednak nie jest to już problemem, ponieważ dynamiczna maszyna pomiarowa stanowi trwałe, dostosowane do realizowanych zadań rozwiązanie.