Nopeampi tuotantolinja integroidun ratkaisun avulla
GKN Driveline - Ruotsi
Yhteystiedot

GKN:llä on nykyaikainen lähestymistapa tuotannon suunnitteluun. Sen Köpingin tehtaalla Ruotsissa kehitetään, valmistetaan ja kootaan monien teknisen kehityksen kärkeä edustavien autojen nelivetojärjestelmän tärkeimmät osat. Jan Engström työskentelee tuotantoinsinöörinä kruunurattaiden tuotanto-osastolla ja vastaa 34 vuorokauden ympäri käynnissä olevasta työstökoneesta. Yhteistyössä Hexagonin kanssa Engström on osallistunut projektiin, joka tulee muuttamaan GKN:n osien mittaukseen käyttämää prosessia.
”Aikaisemmin käytimme tuotteidemme tarkastusmittauksiin erilaisia mittareita”, sanoo Engström. ”Varjopuolena oli, että kunkin tuottamamme uuden yksityiskohdan myötä meidän oli hankittava uusi tarkoitukseen sopiva mittari. Kun aloimme saada tilauksia useille uusille tuotteille, tarvitsimme joustavamman ratkaisun.”
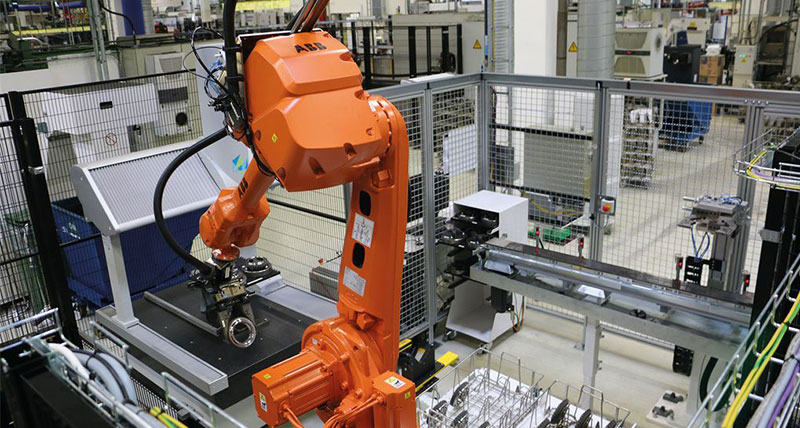
Sopiva ratkaisu yhteistyöllä
GKN oli tunnistanut tarpeensa laadukkaalle, joustavalle ja nopealle osien mittausjärjestelmälle, joka ei toimisi pullonkaulana tuotannossa. Projekti käynnistyi, kun Engström aloitti Hexagonin kanssa keskustelut oikean ratkaisun löytämisestä inline-mittausprosessiin. Osapuolet päätyivät automatisoidun ratkaisun asennukseen, jossa PC-DMIS-ohjelmistolla varustettu GLOBAL Shop Floor -koordinaattimittauskone integroitiin tuotantolinjaan. Tämä on ensimmäinen kerta, kun GKN yhdistää mittauskoneen tuotantosoluun. Aiemmin osat vietiin tuotantolinjalta erilliseen mittaushuoneeseen tarkastusta varten. Pitkä tarkastusprosessi aiheutti kalliita tuotantoviiveitä. Uudella järjestelmällä sama prosessi vie vain 90 sekuntia, mikä tuo arvokasta ajansäästöä.
Joustavuus oli GKN Drivelinelle myös tärkeä tekijä sopivan koordinaattimittauskoneen valinnassa, sillä yrityksen oli kyettävä mittaamaan nopeasti erilaisia osia eri asiakkaille. Hexagonin kattava ratkaisu on täyttänyt kaikki vaatimukset ja enemmänkin, sillä nyt uudet osat voidaan mitata solun sisällä. Työkappaleiden vaihdot käyvät nopeammin turhiksi jääneiden prosessien poistamisen myötä, joten odotusaika on supistunut kiinnitysten vaihtamiseen ja ohjelmointiin. ”Kyse on pitkän aikavälin suunnittelusta”, sanoo Engström. ”Mittareihin verrattuna koordinaattimittauskone on erittäin joustava vaihtoehto, koska se pystyy mittaamaan kaiken, minkä laskemme mittauspöydälle. Nyt voimme aloittaa kaikkien uusien tuotteiden tuotannon suoraan. Tämä myös vapauttaa aikaa mittaushuoneessa, koska mittauskone kykenee lisätarkastuksiin, joihin mittarit eivät pystyneet.”
GKN:llä on tällä hetkellä kymmenen Hexagonin koordinaattimittauskonetta tehtaassaan, mikä antaa yrityksen henkilökunnalle luottamusta koneisiin. Luottamus oli yksi pääsyistä, joiden ansiosta yritys päätyi yhdistämään GLOBAL Shop Floor -koordinaattimittauskoneen soluun.
Integraatio parantaa tehokkuutta
Koordinaattimittauskone on ensimmäinen GKN:n automatisoidun solun osaksi asentama sorviin ja robottiin liitetty järjestelmä. Jokainen yksityiskohta mitataan ja mittaustiedot lähetetään jatkuvasti mittauskoneesta sorviin, joka kompensoi toleranssien sisällä nimellisarvoon. On tärkeää mitata osat 100-prosenttisesti solun sisällä äärimmäisellä tarkkuudella.
Koordinaattimittauskoneen integroinnista tuotantolinjaan on seurannut useita etuja. Yhtenä etuna on, että tuotantoaika on lyhyempi uuden laadunvalvontajärjestelmän ansiosta. Laatu siis todellakin lisää tuottavuutta. ”Nykyiset laatua koskevat tiedot ovat huippuluokkaa verrattuna aiemmin käytössämme olleisiin tietoihin”, sanoo Team Leader Johan Bäckström.
Toisena etuna on nopeus, sillä GKN voi nyt mitata kaksi kappaletta kerrallaan, mikä tuplaa ajansäästön.
Tuotantoajan lyhennyttyä tuotantolinjaan integroidun koordinaattimittauskoneen myötä koko tuotannon nopeus on kasvanut.Hexagon loi myös räätälöidyn koulutusohjelman kyseistä tuotantolinjaa varten ja toteutti koulutuksen paikan päällä Köpingissä. Bäckströmin sanoin: ”Kone on helppokäyttöinen, ja saimme tarvitsemamme koulutuksen ja tuen. Hexagon saapui tehtaallemme ja perehdytti kaikki linjan työntekijät koordinaattimittauskoneen käyttöön.”
Etua kustannussäästöistä, helppokäyttöisyydestä ja teknisestä tuestaAjansäästöstä seuraa myös kustannussäästöjä, koska eri osien mittaaminen pelkästään ohjelmaa ja kiinnittimiä vaihtamalla on huomattavasti helpompaa kuin koko mittausprosessin vaihtaminen. Aiemmin jouduimme joka kerta investoimaan uuteen mittariin, ja kustannukset olivat noin 250 000 kruunua. Nyt säästöt ovat jokaisen uuden yksityiskohdan kohdalla yli 200 000 kruunua.
GKN:llä on monia uusia mittareita vaativia uusia projekteja, mutta se ei ole enää ongelma, sillä tämä uusi ja dynaaminen mittauskone tarjoaa mukautettavissa olevan, pitkäkestoisen ratkaisun.
Nykyiset laatua koskevat tiedot ovat huippuluokkaa verrattuna aiemmin käytössämme olleisiin tietoihin.