Un laser tracker corrige la position exacte de robots dans l’industrie aéronautique
Premium Aerotec, Allemagne
Contact

Avec l’A350, c’est une autre paire de manches. Chaque fuselage est fourni avec des profilés, plus précisément des raidisseurs lisses, pour le renforcement. Jusqu’ici, ces éléments étaient principalement constitués d’aluminium. En général, on les positionne manuellement au‑dessus des trous pratiqués par une fraiseuse. Avec l’A350, principalement constitué de plastique renforcé de fibre de carbone (CFP), cette méthode est inapplicable. Comme le matériau durcit à l’autoclave, dans un four sous pression, un perçage est impossible.
En tant que fournisseur d’aérostructures, l’avionneur livre de grandes pièces pour la nouvelle génération de long-courriers Airbus, dont le baptême de feu est prévu pour la mi-2013. Cette fourniture englobe tout le fuselage avant. “Les raidisseurs doivent être fixés avec précision pour exclure une dégradation ultérieure de la qualité. Un positionnement manuel s’avère peu rentable, étant donné qu’on sera amené à construire jusqu’à 13 avions de ce type par mois. Notre objectif est d’automatiser aussi l’assemblage de l’avion à l’aide de robots. Pour cela, il est cependant nécessaire que le robot travaille avec la même précision qu’une fraiseuse”, précise Lewerenz.
En d’autres termes, pour ne pas compromettre les processus de fabrication et d’assemblage consécutifs, la mise en place des raidisseurs pour l’A350 XWB (qui peuvent avoir 18 m de long) doit s’effectuer avec une tolérance de ± 0,3 mm dans l’axe circonférentiel et avec une tolérance de ± 1 mm dans l’axe longitudinal. Après les premières expériences, le désenchantement a régné à Nordeham. Le premier robot était supposé se déplacer sur 3 000 mm, mais s’arrêtait au bout de 2 997 mm. Le deuxième effectuait toujours un déplacement excessif de 1,5 mm. “Une différence de 0,1 % semble minime à première vue, mais l’imprécision augmente avec la longueur du raidisseur, qui est de 18 m. C’était inacceptable”, explique Lewerenz.
Le fabricant de robots Fanuc n’en était cependant pas responsable, car les valeurs obtenues correspondaient aux spécifications des robots. Cela signifie que les robots travaillent avec une moins grande précision que les fraiseuses car ils réagissent aux changements de poids et de force, ce qui conduit à des écarts. L’industrie automobile a recours à l’apprentissage pour amener les robots à exécuter les mouvements, mais Lewerenz a écarté cette possibilité : “La technologie système est prévue pour 800 avions en tout. Réaliser des modèles pour l’apprentissage est impossible du point de vue économique. C’est pourquoi Premium Aerotec part du principe que les machines sont entièrement programmées hors ligne pour que tout fonctionne bien pendant la fabrication.”
L’équipementier aérospatial a commencé à chercher une solution pour placer les robots à la position correcte sans phase d’apprentissage, après quelques mesures correctives. Il fallait un système qui pouvait être monté monte sur la tête du robot. Avec le Leica Absolute Tracker, une caméra (la Leica T-Cam) et un Leica T-Mac, il est possible d’acquérir simultanément les coordonnées 3D d’un point et son orientation dans l’espace (i, j, k; c’est-à-dire roulis, tangage et lacet). Ceci est important parce qu’une surveillance 6D du robot est nécessaire (il a six degrés de liberté). Il faut donc non seulement surveiller la position de la tête du robot, mais aussi son orientation.
Si les trois orientations spatiales (roulis, tangage et lacet) sont nécessaires, comme dans la présente application, elles sont déterminées avec la Leica T-Cam, utilisée pour la disposition des LED d’un Leica T-Mac. Le zoom vario permet d’obtenir une précision pratiquement indépendante de la distance pour ces valeurs déterminées par photogrammétrie dans le volume de travail.
Selon Lewerenz : “Un autre avantage du laser tracker est la possibilité d’y charger des résultats de mesure. On peut ainsi retrouver un résultat accepté. Reste à déterminer à quel point cette fonction nous sera utile, car dans un premier temps il faut mesurer les composants. Le contrôle s’effectue ultérieurement. Nous utilisons aussi le Leica Absolute Tracker pour cette tâche.” Dans la première unité de production, deux robots, l’un monté sur le sol et l’autre sur un axe transversal et tenant la tête de l’outil, saisissent les deux extrémités d’un raidisseur et placent celui-ci sur la section du fuselage.
Dès que le robot a placé le raidisseur en un point, le système de mesure s’allume automatiquement. Le robot l’informe de sa position, et le système de mesure ordonne au robot d’effectuer les corrections nécessaires. Durant la présente phase d’essai, cette opération prend 20 secondes, mais après l’optimisation du circuit de commande, elle se limitera à quelques secondes. Le raccordement est ensuite ajusté. Le raidisseur est fixé et le laser tracker peut corriger la prochaine tête de robot en même temps.
Quelle que soit l’issue, Lewerenz estime que l’expérience avec le laser tracker dans l’unité de production de Premium Aerotec s’avérera très utile. Le principe de fonctionnement, les caractéristiques du système et sa fiabilité sont connus. Et il n’est pas absolument nécessaire d’acquérir de nouveaux systèmes si les laser trackers existants sont disponibles (les frais de formation sont également négligeables).
La cellule d’essai présente une conception ouverte réalisée à l’appui d’un logiciel centralisé pour tout système de mesure 3D afin de procurer une flexibilité maximale dans la réalisation des séries. Le système de mesure externe prend le pas sur les systèmes de mesure internes des robots dans ce cas”, ajoute Lewerenz. “Il est important que le système de mesure et la machine soient séparés. A notre avis, ce concept a un grand avenir, car il nous permet de combiner un système de mesure optimal et une machine optimale.”
“Ce qui nous séduit aussi, c’est la possibilité de s’affranchir d’une machine spécialisée coûteuse, et cet aspect dépasse le cadre du positionnement des raidisseurs”, note le responsable du projet. Parce que Premium Aerotec attache une très grande importance à la réduction des temps de production et d’assemblage. Aujourd’hui, ces tâches exigent beaucoup de travail manuel et des supports permanents, tels que des portiques. Malheureusement, ces éléments rendent l’assemblage moins flexible et entravent le montage de différents produits sur la même chaîne. “En plus, les produits changent au cours de leur cycle de vie et nous devons être capables de nous y adapter avec souplesse.
Deux avions sont rarement exactement pareils. Même si la seule différence est l’emplacement des toilettes, il faut pouvoir adapter l’aérostructure. C’est essentiellement pour cette raison que chaque coque a une autre apparence”, explique Lewerenz.
Aussi, voit-il les robots et systèmes de mesure portables comme des solutions d’avenir. Ils pourraient introduire un changement paradigmatique dans l’ingénierie mécanique. C’est pourquoi il espère que les partenaires du projet, y compris le fournisseur FFT‑Edag, développeront une solution clé en main. “Nous souhaitons faire l’acquisition d’un produit fini qui fonctionne. Et si un problème devait apparaître, nous aurions un seul interlocuteur », observe Lewerenz.
Il a également adressé une demande à Hexagon Manufacturing Intelligence. Le Leica Absolute Tracker se caractérise par une fréquence de 3 000 Hz et un débit de 1 000 mesures par seconde. Durant les essais, ces 1 000 jeux de données étaient cependant fournis à une fréquence maximale de 10 Hz. “Nous avons besoin de 100 Hz parce que les robots fonctionnent avec une fréquence située autour de 100 Hz et nous souhaitons pouvoir corriger tout cycle de calcul du robot. Pour cette raison, la nouvelle interface temps réel (Ethercat), qui permet une sortie de données à 1 000 Hz est un pas important dans la bonne direction.”
Le principe de fabrication : selon la taille de l’avion, il faudra utiliser six ou huit robots et trois ou quatre robots placés de chaque côté pour tenir le raidisseur. Deux rangées de robots et deux laser trackers travailleront indépendamment l’un de l’autre.
En tant que fournisseur d’aérostructures, l’avionneur livre de grandes pièces pour la nouvelle génération de long-courriers Airbus, dont le baptême de feu est prévu pour la mi-2013. Cette fourniture englobe tout le fuselage avant. “Les raidisseurs doivent être fixés avec précision pour exclure une dégradation ultérieure de la qualité. Un positionnement manuel s’avère peu rentable, étant donné qu’on sera amené à construire jusqu’à 13 avions de ce type par mois. Notre objectif est d’automatiser aussi l’assemblage de l’avion à l’aide de robots. Pour cela, il est cependant nécessaire que le robot travaille avec la même précision qu’une fraiseuse”, précise Lewerenz.
En d’autres termes, pour ne pas compromettre les processus de fabrication et d’assemblage consécutifs, la mise en place des raidisseurs pour l’A350 XWB (qui peuvent avoir 18 m de long) doit s’effectuer avec une tolérance de ± 0,3 mm dans l’axe circonférentiel et avec une tolérance de ± 1 mm dans l’axe longitudinal. Après les premières expériences, le désenchantement a régné à Nordeham. Le premier robot était supposé se déplacer sur 3 000 mm, mais s’arrêtait au bout de 2 997 mm. Le deuxième effectuait toujours un déplacement excessif de 1,5 mm. “Une différence de 0,1 % semble minime à première vue, mais l’imprécision augmente avec la longueur du raidisseur, qui est de 18 m. C’était inacceptable”, explique Lewerenz.
Le fabricant de robots Fanuc n’en était cependant pas responsable, car les valeurs obtenues correspondaient aux spécifications des robots. Cela signifie que les robots travaillent avec une moins grande précision que les fraiseuses car ils réagissent aux changements de poids et de force, ce qui conduit à des écarts. L’industrie automobile a recours à l’apprentissage pour amener les robots à exécuter les mouvements, mais Lewerenz a écarté cette possibilité : “La technologie système est prévue pour 800 avions en tout. Réaliser des modèles pour l’apprentissage est impossible du point de vue économique. C’est pourquoi Premium Aerotec part du principe que les machines sont entièrement programmées hors ligne pour que tout fonctionne bien pendant la fabrication.”
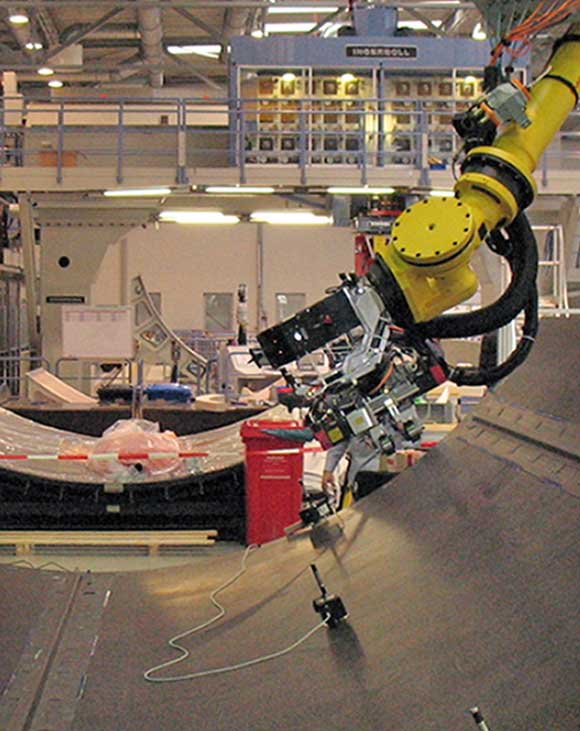
Si les trois orientations spatiales (roulis, tangage et lacet) sont nécessaires, comme dans la présente application, elles sont déterminées avec la Leica T-Cam, utilisée pour la disposition des LED d’un Leica T-Mac. Le zoom vario permet d’obtenir une précision pratiquement indépendante de la distance pour ces valeurs déterminées par photogrammétrie dans le volume de travail.
Selon Lewerenz : “Un autre avantage du laser tracker est la possibilité d’y charger des résultats de mesure. On peut ainsi retrouver un résultat accepté. Reste à déterminer à quel point cette fonction nous sera utile, car dans un premier temps il faut mesurer les composants. Le contrôle s’effectue ultérieurement. Nous utilisons aussi le Leica Absolute Tracker pour cette tâche.” Dans la première unité de production, deux robots, l’un monté sur le sol et l’autre sur un axe transversal et tenant la tête de l’outil, saisissent les deux extrémités d’un raidisseur et placent celui-ci sur la section du fuselage.
Dès que le robot a placé le raidisseur en un point, le système de mesure s’allume automatiquement. Le robot l’informe de sa position, et le système de mesure ordonne au robot d’effectuer les corrections nécessaires. Durant la présente phase d’essai, cette opération prend 20 secondes, mais après l’optimisation du circuit de commande, elle se limitera à quelques secondes. Le raccordement est ensuite ajusté. Le raidisseur est fixé et le laser tracker peut corriger la prochaine tête de robot en même temps.
Quelle que soit l’issue, Lewerenz estime que l’expérience avec le laser tracker dans l’unité de production de Premium Aerotec s’avérera très utile. Le principe de fonctionnement, les caractéristiques du système et sa fiabilité sont connus. Et il n’est pas absolument nécessaire d’acquérir de nouveaux systèmes si les laser trackers existants sont disponibles (les frais de formation sont également négligeables).
La cellule d’essai présente une conception ouverte réalisée à l’appui d’un logiciel centralisé pour tout système de mesure 3D afin de procurer une flexibilité maximale dans la réalisation des séries. Le système de mesure externe prend le pas sur les systèmes de mesure internes des robots dans ce cas”, ajoute Lewerenz. “Il est important que le système de mesure et la machine soient séparés. A notre avis, ce concept a un grand avenir, car il nous permet de combiner un système de mesure optimal et une machine optimale.”
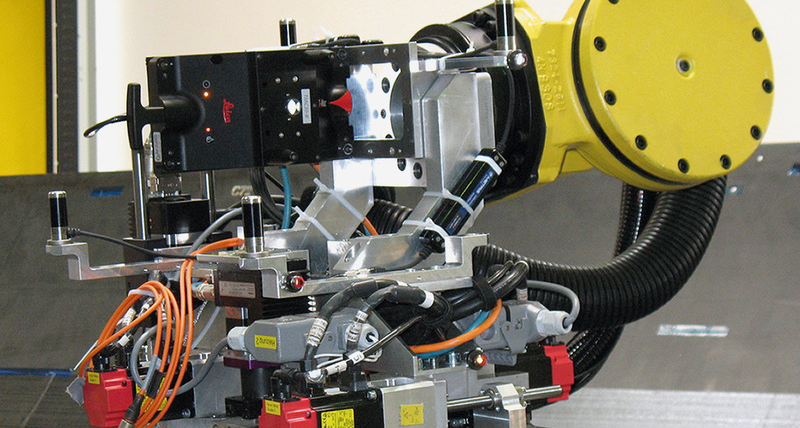
Deux avions sont rarement exactement pareils. Même si la seule différence est l’emplacement des toilettes, il faut pouvoir adapter l’aérostructure. C’est essentiellement pour cette raison que chaque coque a une autre apparence”, explique Lewerenz.
Aussi, voit-il les robots et systèmes de mesure portables comme des solutions d’avenir. Ils pourraient introduire un changement paradigmatique dans l’ingénierie mécanique. C’est pourquoi il espère que les partenaires du projet, y compris le fournisseur FFT‑Edag, développeront une solution clé en main. “Nous souhaitons faire l’acquisition d’un produit fini qui fonctionne. Et si un problème devait apparaître, nous aurions un seul interlocuteur », observe Lewerenz.
Il a également adressé une demande à Hexagon Manufacturing Intelligence. Le Leica Absolute Tracker se caractérise par une fréquence de 3 000 Hz et un débit de 1 000 mesures par seconde. Durant les essais, ces 1 000 jeux de données étaient cependant fournis à une fréquence maximale de 10 Hz. “Nous avons besoin de 100 Hz parce que les robots fonctionnent avec une fréquence située autour de 100 Hz et nous souhaitons pouvoir corriger tout cycle de calcul du robot. Pour cette raison, la nouvelle interface temps réel (Ethercat), qui permet une sortie de données à 1 000 Hz est un pas important dans la bonne direction.”
Le principe de fabrication : selon la taille de l’avion, il faudra utiliser six ou huit robots et trois ou quatre robots placés de chaque côté pour tenir le raidisseur. Deux rangées de robots et deux laser trackers travailleront indépendamment l’un de l’autre.
Premium Aerotech Germany case study
Download