Il Laser Tracker corregge la posizione esatta dei robot utilizzati per l’assemblaggio degli aeroplani
Premium Aerotec, Germania
Contattateci

L’A350 è un aereo diverso dagli altri. Ogni fusoliera di aereo contiene i profili, i cosiddetti correntini, con funzione di rinforzo. Fino ad ora erano per lo più in alluminio. In generale sono posizionati a mano sopra i fori creati con una fresatrice. Con l’A350, costruito essenzialmente con materiali plastici rinforzati in fibra di carbonio (CFP), questo tipo di assemblaggio non è applicabile. Il materiale indurisce in un’autoclave, un forno a pressione, sicchè non può essere forato. “I correntini, che sono anch’essi di CFP, devono aderire al guscio” spiega Tim Lewerenz, il responsabile alla Premium Aerotec per il progetto che si concentra sull’integrazione ottimizzata di questi componenti strutturali.
Come fornitore di aerostrutture, Premium Aerotec fornisce grandi componenti per la nuova generazione di aerei Airbus per le lunghe distanze, il cui viaggio inaugurale è previsto per la metà di quest’anno. Questo comprende l’intera fusoliera anteriore. “I correntini devono essere fissati in modo preciso per evitare successivi cali di qualità. Il posizionamento manuale qui è antieconomico poiché alla fine verranno costruiti fino a 13 aerei di questo tipo al mese. Il nostro obiettivo è quello di automatizzare anche il montaggio dell’aereo con i robot. L’esigenza tuttavia è che il robot lavori in modo preciso come una fresatrice.”
Più precisamente, per non mettere a repentaglio i successivi processi di produzione e montaggio, i correntini per l’A350 XWB (che possono essere lunghi anche 18 metri) devono essere messi in posizione nella direzione circonferenziale con una tolleranza di +/- 0,3 mm e in direzione longitudinale con una tolleranza di +/- 1 mm. Dopo i primi esperimenti, a Nordenham si è diffusa la delusione. Il primo robot doveva muoversi di 3.000 mm e invece si è fermato dopo 2.997 mm. Il secondo invece si muoveva sempre di oltre 1,5 mm. “Una differenza dello 0,1 per cento all’inizio sembra marginale, ma con una lunghezza di correntino di 18 m, si accumula. Questo era per noi inaccettabile” afferma Lewerenz.
Il costruttore del robot non ne aveva colpa, tuttavia, poiché i valori rientravano nelle specifiche. Questo significa che i robot lavorano in modo meno preciso delle fresatrici perché rispondono a cambiamenti di peso e di forza che portano a delle deviazioni. L’industria automobilistica risolve questo problema con l’apprendimento dei robot, ma Lewerenz scartò questa possibilità: “La tecnologia del sistema è progettata per 800 aerei in tutto. Componenti campione per l’apprendimento non sono quindi praticabili dal punto di vista economico. Questo è il motivo per cui noi alla Premium Aerotec dobbiamo partire dal presupposto che le macchine sono programmate in modo completamente offline così che tutto sia corretto durante la produzione.”
Il fornitore dell’industria aeronautica iniziò così a cercare una possibilità di portare i robot nella posizione corretta senza apprendimento. Era necessario un sistema che potesse essere collocato sulla testa del robot. Con il Leica Absolute Tracker e una videocamera (la cosiddetta Leica T-Cam), e un sensore Leica T-Mac a bordo del robot, si possono rilevare simultaneamente le coordinate 3D di un punto e il suo orientamento nello spazio (i, j, k o roll, pitch e yaw). Questo è importante perché è necessario un monitoraggio 6D del robot (sei gradi di libertà). Si può monitorare cioè non solo la posizione della testa del robot ma anche il suo orientamento.
Se come nell’applicazione in questione sono necessari i tre orientamenti nello spazio (roll, pitch e yaw), questi sono determinati per mezzo del controllo del T-Mac, solidale alla testa del robot, da parte della T-Cam. Lo zoom di cui dispone la T-Cam permette una precisione quasi indipendente dalla distanza di questi valori di misura determinati fotogrammetricamente entro il volume di lavoro.
utilizzati dal sistema di correzione del posizionamento ed eventualmente dare la precedenza a un risultato accettabile. Resta poi da vedere in che misura questo sia importante per noi, poiché i componenti devono essere ancora misurati e poi controllati. Usiamo l’Absolute Tracker anche per questo scopo.” Nella prima cella di produzione, due robot, uno montato a pavimento e l’altro montato sul binario che sostiene la testa dell’utensile, prende le due estremità di un correntino e lo colloca su di una sezione della fusoliera.
Lewerenz: “Für den Laser Tracker spricht auch, dass die Non appena il robot ha posizionato il correntino in un punto, il sistema di misura si attiva automaticamente. Il robot lo informa della sua posizione e il sistema di misura sollecita il robot a fare eventuali correzioni. Oggi nelle esecuzioni di prova, questo richiede circa 20 secondi, ma quando il circuito di controllo sarà ottimizzato, il tempo si ridurrà a soli pochi secondi. In seguito, il collegamento viene interrotto. Il correntino viene incollato e contemporaneamente il tracker può correggere il prossimo posizionamento del robot.
In ogni caso, Lewerenz considera un grande vantaggio il fatto che la Premium Aerotec abbia già esperienza con il laser tracker. Questo significa che il metodo di funzionamento, le caratteristiche del sistema e la loro affidabilità sono note e non è assolutamente indispensabile acquistare nuovi sistemi, se i sistemi laser tracker esistenti sono disponibili. E non sono necessari neppure costi di formazione.
La cella di test è stata intenzionalmente progettata in modo aperto con un software centralizzato in modo che qualunque sistema di misura 3D possa realizzare la massima flessibilità nella serie. Il sistema di misura esterno esclude qui i sistemi di misura interni dei robot, secondo Lewerenz. “Ciò che è importante per noi è la separazione di macchina e sistema di misura. Secondo noi questa concezione ha un grande potenziale futuro perché siamo in grado di combinare un ottimo sistema di misura con un’ottima macchina.”
“Questo ci affascina perché sostanzialmente siamo in grado di fare a meno di una costosa macchina speciale, e questo va oltre il posizionamento dei correntini” racconta il project manager. Alla Premium Aerotec infatti un aspetto ancora più importante è quello di ridurre i tempi ciclo nella produzione e nel montaggio. Oggi questo richiede molto lavoro manuale e attrezzature di montaggio permanenti, come i gantry. Il problema è realizzare un assemblaggio flessibile, cioè il montaggio di prodotti diversi in un’unica linea. “Inoltre i prodotti cambiano nel corso del loro ciclo di vita e noi dobbiamo essere in grado di rispondere in modo rapido a questi cambiamenti. Molto raramente due aerei sono esattamente uguali. Anche se si tratta solo di una toilette collocata in un posto diverso, l’aerostruttura ha bisogno di essere adattata di conseguenza. Questo è in sostanza il motivo per cui ogni guscio ha un aspetto diverso” spiega Lewerenz.
Robot e sistemi portatili di misura sono dunque il futuro per lui. Potrebbero rendere possibile un cambiamento copernicano nell’ingegneria meccanica. Ecco perché spera che i partner nel progetto, compreso il fornitore del sistema FFT-Edag, sviluppino e offrano una soluzione chiavi in mano. “Noi vogliamo acquistare un prodotto finito che funzioni. E se qualcosa un giorno non dovesse funzionare, ci sarebbe un solo partner da contattare” afferma Lewerenz.
Ha anche una richiesta da fare a Hexagon Manufacturing Intelligence. Il Leica Absolute Tracker funziona internamente a 3.000 Hz con una produttività di 1.000 valori di misura al secondo. Queste 1.000 serie di dati, tuttavia, sono state prodotte ad una velocità massima di 10 Hz. “Ci servono 100 Hz perché i robot funzionano internamente a circa 100 Hz e noi vogliamo essere in grado di correggre ogni singolo ciclo di calcolo del robot. Questo è il motivo per cui la nuova interfaccia real time (Ethercat), che consente l’output di dati a 1.000 Hz, è un passo importante nella giusta direzione.”
Il concetto di produzione: si devono usare sei o otto robot a seconda della dimensione dell’aereo. Il correntino viene sostenuto da tre o quattro robot su ciascun lato. Due serie di robot e due tracker devono operare in modo indipendente tra loro.
Come fornitore di aerostrutture, Premium Aerotec fornisce grandi componenti per la nuova generazione di aerei Airbus per le lunghe distanze, il cui viaggio inaugurale è previsto per la metà di quest’anno. Questo comprende l’intera fusoliera anteriore. “I correntini devono essere fissati in modo preciso per evitare successivi cali di qualità. Il posizionamento manuale qui è antieconomico poiché alla fine verranno costruiti fino a 13 aerei di questo tipo al mese. Il nostro obiettivo è quello di automatizzare anche il montaggio dell’aereo con i robot. L’esigenza tuttavia è che il robot lavori in modo preciso come una fresatrice.”
Più precisamente, per non mettere a repentaglio i successivi processi di produzione e montaggio, i correntini per l’A350 XWB (che possono essere lunghi anche 18 metri) devono essere messi in posizione nella direzione circonferenziale con una tolleranza di +/- 0,3 mm e in direzione longitudinale con una tolleranza di +/- 1 mm. Dopo i primi esperimenti, a Nordenham si è diffusa la delusione. Il primo robot doveva muoversi di 3.000 mm e invece si è fermato dopo 2.997 mm. Il secondo invece si muoveva sempre di oltre 1,5 mm. “Una differenza dello 0,1 per cento all’inizio sembra marginale, ma con una lunghezza di correntino di 18 m, si accumula. Questo era per noi inaccettabile” afferma Lewerenz.
Il costruttore del robot non ne aveva colpa, tuttavia, poiché i valori rientravano nelle specifiche. Questo significa che i robot lavorano in modo meno preciso delle fresatrici perché rispondono a cambiamenti di peso e di forza che portano a delle deviazioni. L’industria automobilistica risolve questo problema con l’apprendimento dei robot, ma Lewerenz scartò questa possibilità: “La tecnologia del sistema è progettata per 800 aerei in tutto. Componenti campione per l’apprendimento non sono quindi praticabili dal punto di vista economico. Questo è il motivo per cui noi alla Premium Aerotec dobbiamo partire dal presupposto che le macchine sono programmate in modo completamente offline così che tutto sia corretto durante la produzione.”
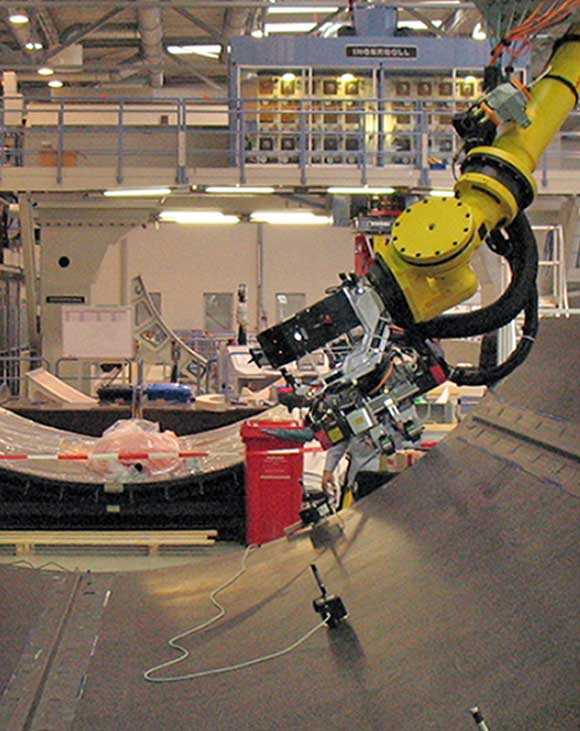
Se come nell’applicazione in questione sono necessari i tre orientamenti nello spazio (roll, pitch e yaw), questi sono determinati per mezzo del controllo del T-Mac, solidale alla testa del robot, da parte della T-Cam. Lo zoom di cui dispone la T-Cam permette una precisione quasi indipendente dalla distanza di questi valori di misura determinati fotogrammetricamente entro il volume di lavoro.
utilizzati dal sistema di correzione del posizionamento ed eventualmente dare la precedenza a un risultato accettabile. Resta poi da vedere in che misura questo sia importante per noi, poiché i componenti devono essere ancora misurati e poi controllati. Usiamo l’Absolute Tracker anche per questo scopo.” Nella prima cella di produzione, due robot, uno montato a pavimento e l’altro montato sul binario che sostiene la testa dell’utensile, prende le due estremità di un correntino e lo colloca su di una sezione della fusoliera.
Lewerenz: “Für den Laser Tracker spricht auch, dass die Non appena il robot ha posizionato il correntino in un punto, il sistema di misura si attiva automaticamente. Il robot lo informa della sua posizione e il sistema di misura sollecita il robot a fare eventuali correzioni. Oggi nelle esecuzioni di prova, questo richiede circa 20 secondi, ma quando il circuito di controllo sarà ottimizzato, il tempo si ridurrà a soli pochi secondi. In seguito, il collegamento viene interrotto. Il correntino viene incollato e contemporaneamente il tracker può correggere il prossimo posizionamento del robot.
In ogni caso, Lewerenz considera un grande vantaggio il fatto che la Premium Aerotec abbia già esperienza con il laser tracker. Questo significa che il metodo di funzionamento, le caratteristiche del sistema e la loro affidabilità sono note e non è assolutamente indispensabile acquistare nuovi sistemi, se i sistemi laser tracker esistenti sono disponibili. E non sono necessari neppure costi di formazione.
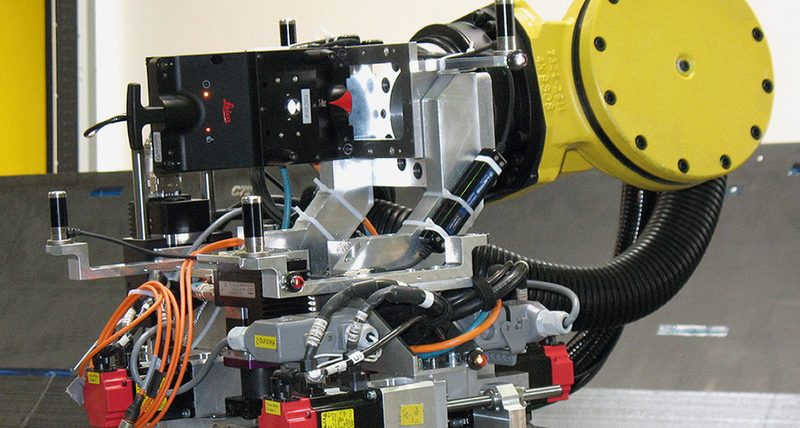
“Questo ci affascina perché sostanzialmente siamo in grado di fare a meno di una costosa macchina speciale, e questo va oltre il posizionamento dei correntini” racconta il project manager. Alla Premium Aerotec infatti un aspetto ancora più importante è quello di ridurre i tempi ciclo nella produzione e nel montaggio. Oggi questo richiede molto lavoro manuale e attrezzature di montaggio permanenti, come i gantry. Il problema è realizzare un assemblaggio flessibile, cioè il montaggio di prodotti diversi in un’unica linea. “Inoltre i prodotti cambiano nel corso del loro ciclo di vita e noi dobbiamo essere in grado di rispondere in modo rapido a questi cambiamenti. Molto raramente due aerei sono esattamente uguali. Anche se si tratta solo di una toilette collocata in un posto diverso, l’aerostruttura ha bisogno di essere adattata di conseguenza. Questo è in sostanza il motivo per cui ogni guscio ha un aspetto diverso” spiega Lewerenz.
Robot e sistemi portatili di misura sono dunque il futuro per lui. Potrebbero rendere possibile un cambiamento copernicano nell’ingegneria meccanica. Ecco perché spera che i partner nel progetto, compreso il fornitore del sistema FFT-Edag, sviluppino e offrano una soluzione chiavi in mano. “Noi vogliamo acquistare un prodotto finito che funzioni. E se qualcosa un giorno non dovesse funzionare, ci sarebbe un solo partner da contattare” afferma Lewerenz.
Ha anche una richiesta da fare a Hexagon Manufacturing Intelligence. Il Leica Absolute Tracker funziona internamente a 3.000 Hz con una produttività di 1.000 valori di misura al secondo. Queste 1.000 serie di dati, tuttavia, sono state prodotte ad una velocità massima di 10 Hz. “Ci servono 100 Hz perché i robot funzionano internamente a circa 100 Hz e noi vogliamo essere in grado di correggre ogni singolo ciclo di calcolo del robot. Questo è il motivo per cui la nuova interfaccia real time (Ethercat), che consente l’output di dati a 1.000 Hz, è un passo importante nella giusta direzione.”
Il concetto di produzione: si devono usare sei o otto robot a seconda della dimensione dell’aereo. Il correntino viene sostenuto da tre o quattro robot su ciascun lato. Due serie di robot e due tracker devono operare in modo indipendente tra loro.
Premium Aerotech Germany case study
Download