Antriebe für Elektrofahrzeuge
Gewährleistung der effektiven Leistungsübertragung bei hohen Drehmomenten mit Fertigungslösungen speziell für die Anforderungen von E-Fahrzeug-Antriebssystemen
Kontakt
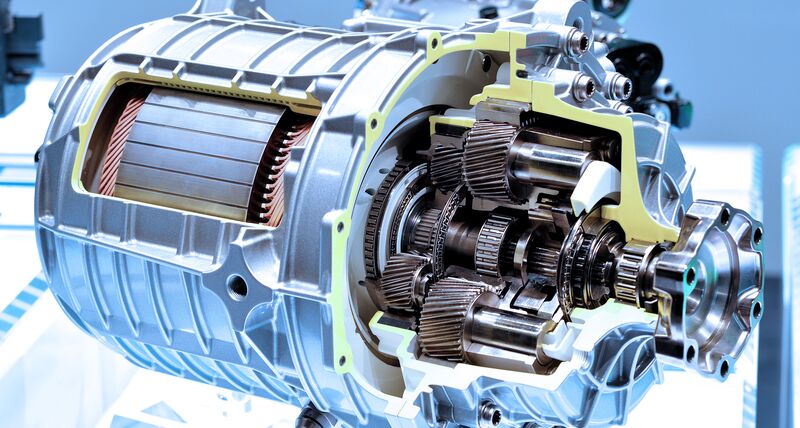
Im Vergleich zur Entwicklung traditioneller Fahrzeuge mit Verbrennungsmotor verändert die E-Mobilität grundlegend das Design des Antriebsstrangs. Wo in der Vergangenheit eine manuelle 6-Gang-Schaltung oder ein 8-Gang-Automatikgetriebe den Standard im Automobilbau darstellten, verfügen modernste Elektrofahrzeuge heute über unterschiedlichste Automatikgetriebe wie 2-stufige Stirnradantriebe, integrierte gestufte Planetengetriebe oder stufenlose Getriebe (CVT) für optimale Betriebseffizienz.
Häufig teilen sich Elektromotor, Leistungselektronik und Antriebseinheit ein Gehäuse. Das reduziert die Anzahl von Einzelkomponenten im Antriebsstrang und verringert so das Gesamtgewicht des Systems. Bei batterieelektrischen Fahrzeugen (BEVs) kann diese integrierte Einheit direkt ein kombiniertes elektrisches Achsgetriebe antreiben. Bei Hybridfahrzeugen sind unterschiedliche Getriebekonfigurationen möglich, je nachdem wie der Hersteller die Interaktion zwischen Elektro- und Verbrennungsmotor vorsieht.
Während sich viele Funktionsprinzipien für E-Fahrzeug-Antriebe von denen für Verbrennungsmotoren unterscheiden, gibt es auf der Komponentenebene tatsächlich viele Gemeinsamkeiten bei den erforderlichen Konstruktions- und Fertigungsprozessen. Schlüsselkomponenten wie gerad- und schrägverzahnte Getriebe oder Gehäuse sind beiden Arten von Antriebssträngen gemeinsam. Die größte Herausforderung bei der Anpassung dieser Komponenten für den elektrifizierten Antriebsstrang liegen in der Bewältigung des größeren Drehmoments und der höheren Drehzahlen, die sich mit Elektromotoren erzielen lassen. Die Toleranzen für die präzisionsbearbeiteten Bauteile für gerad- und schrägverzahnte Zahnräder oder Planetengetriebe sind für Elektrofahrzeugkomponenten in aller Regel enger. Zudem gewinnt die Oberflächenbeschaffenheit von Zahnrädern einen neuen Stellenwert, da die Geräuschemission des Antriebs aufgrund der leisen Elektromotoren bei E-Fahrzeugen eine wesentliche Rolle spielt.
Hexagon verfügt über umfangreiche Erfahrung bei der Entwicklung von Antriebsstrangkomponenten sowohl im Automobilbau als auch in der Luft- und Raumfahrt und kann so die Gestaltung von Elektrofahrzeug-Antriebssträngen optimal unterstützen. Mit unseren Simulationslösungen verbessern Hersteller das Zahnrad- und Lagerdesign sowie die Langlebigkeit der Komponenten, simulieren die Schmierstoffeffizienz und beurteilen Geräuschemissionen noch bevor die Fahrzeuge in die Entwicklung gehen. Während unsere Produktionssoftwarelösungen Fertigungsprozesse validieren und die präzise Herstellung von Getriebeteilen mit engen Toleranzen gewährleisten, sind unsere ultra-hochgenauen Messsysteme speziell für die Prüfung und Qualitätssicherung kritischer Teile wie Zahnräder, Wellen und Gehäuse konzipiert.
Häufig teilen sich Elektromotor, Leistungselektronik und Antriebseinheit ein Gehäuse. Das reduziert die Anzahl von Einzelkomponenten im Antriebsstrang und verringert so das Gesamtgewicht des Systems. Bei batterieelektrischen Fahrzeugen (BEVs) kann diese integrierte Einheit direkt ein kombiniertes elektrisches Achsgetriebe antreiben. Bei Hybridfahrzeugen sind unterschiedliche Getriebekonfigurationen möglich, je nachdem wie der Hersteller die Interaktion zwischen Elektro- und Verbrennungsmotor vorsieht.
Während sich viele Funktionsprinzipien für E-Fahrzeug-Antriebe von denen für Verbrennungsmotoren unterscheiden, gibt es auf der Komponentenebene tatsächlich viele Gemeinsamkeiten bei den erforderlichen Konstruktions- und Fertigungsprozessen. Schlüsselkomponenten wie gerad- und schrägverzahnte Getriebe oder Gehäuse sind beiden Arten von Antriebssträngen gemeinsam. Die größte Herausforderung bei der Anpassung dieser Komponenten für den elektrifizierten Antriebsstrang liegen in der Bewältigung des größeren Drehmoments und der höheren Drehzahlen, die sich mit Elektromotoren erzielen lassen. Die Toleranzen für die präzisionsbearbeiteten Bauteile für gerad- und schrägverzahnte Zahnräder oder Planetengetriebe sind für Elektrofahrzeugkomponenten in aller Regel enger. Zudem gewinnt die Oberflächenbeschaffenheit von Zahnrädern einen neuen Stellenwert, da die Geräuschemission des Antriebs aufgrund der leisen Elektromotoren bei E-Fahrzeugen eine wesentliche Rolle spielt.
Hexagon verfügt über umfangreiche Erfahrung bei der Entwicklung von Antriebsstrangkomponenten sowohl im Automobilbau als auch in der Luft- und Raumfahrt und kann so die Gestaltung von Elektrofahrzeug-Antriebssträngen optimal unterstützen. Mit unseren Simulationslösungen verbessern Hersteller das Zahnrad- und Lagerdesign sowie die Langlebigkeit der Komponenten, simulieren die Schmierstoffeffizienz und beurteilen Geräuschemissionen noch bevor die Fahrzeuge in die Entwicklung gehen. Während unsere Produktionssoftwarelösungen Fertigungsprozesse validieren und die präzise Herstellung von Getriebeteilen mit engen Toleranzen gewährleisten, sind unsere ultra-hochgenauen Messsysteme speziell für die Prüfung und Qualitätssicherung kritischer Teile wie Zahnräder, Wellen und Gehäuse konzipiert.
-
Maßprüfung
Hochgenaue Zahnradprüfung für Elektrofahrzeuge
Obwohl der Antriebsstrang elektrischer Fahrzeuge in aller Regel auf anderen Funktionsprinzipien als ein Fahrzeug mit Verbrennungsmotor beruht, gibt es eine Vielzahl von...Dimensionale Prüfung von E-Antriebsgehäusen
Zahlreiche Elektrofahrzeugkonzepte integrieren heute den Elektromotor, die Leistungselektronik und Komponenten des Antriebsstrangs in nur einem Gehäuse. -
ePowertrain Engineering
From solving engineering issues like reducing gear whine noise, improving drivetrain efficiency, enhancing electric motor cooling, all the way to delivering turnkey.