L'automatisation de la métrologie est d’actualité
Même si vous ne voyez ou n’utilisez pas de robots quotidiennement, ils travaillent dans les coulisses. Ils ont aidé à construire le véhicule que vous conduisez, le téléphone qui se trouve en permanence à votre portée et l’ordinateur que vous utilisez.
Contactez-nous
Les robots sont devenus un élément de notre vie courante. Selon un rapport publié en 2013 par l’Association internationale de la robotique (IFR), 2012 s’est soldé par la vente du deuxième plus grand nombre de robots en une année. Parmi les 159 346 unités vendues, près de 70 % étaient destinés aux États-Unis, au Japon, à l’ Allemagne, à la Chine et à la Corée. La construction automobile, l'agroalimentaire, l’industrie chimique, du caoutchouc et du plastique ont enregistré une forte hausse des commandes de robots. Dans le secteur métallurgique et de l’équipement, par contre, la distribution les commandes ont légèrement reculé.
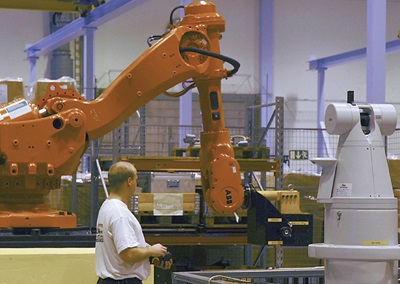
Augmenter la précision de ces machines électromécaniques a constitué un objectif principal depuis l’introduction des robots industriels pour automatiser les usines. Durant les années 1970 et 1980, les robots étaient largement intégrés dans la construction automobile, mais peu utilisés dans l'aéronautique. Ils n’étaient tout simplement pas assez précis pour accomplir les tâches requises. Vers la fin des années 1980 et le début des années 1990, de nombreux fabricants de robots ont commencé à chercher de nouvelles voies pour résoudre ce problème.
Par principe, les robots industriels sont assez répétables, mais leur précision absolue est très faible. Par exemple, si un programme ordonne à l’effecteur d’un robot de se déplacer d’un mètre dans la direction « Y », il pourra accomplir un mouvement d’un peu plus d’un mètre. Par contre, l'amplitude de ce mouvement sera constante. Comme leurs actions sont répétables, les robots pourraient faire l’objet d’une compensation pour atteindre une précision absolue. En mesurant le robot dans une série de poses, on pourrait calculer intrinsèquement les longueurs de liaison, les angles de torsion, les origines des articulations, les décalages d'articulation et les paramètres de raideur pour corriger le modèle de robot.
La difficulté principale consistait à mesurer le robot dans toutes ces poses sur différentes plages de température avec une précision assez élevée pour créer un modèle acceptable. À ce moment, le système adéquat pour la mesure de précision de distances et d'angles était l’interféromètre laser. Le problème avec les interféromètres laser est qu'ils nécessitaient le guidage précis d'un rétroréflecteur pour éviter une interruption du faisceau laser. Lorsque le réflecteur est déplacé sur la même ligne que le faisceau laser, la direction du mouvement et la valeur des pics d’onde sont enregistrées. Il est alors possible de calculer la variation précise de la distance en la multipliant par la demi-longueur d’onde du laser. Mais si ce processus de comptage est interrompu à un moment quelconque (par l’interruption du faisceau), il faut redémarrer le processus au début et à partir de la position initiale précise du réflecteur. Cette limite à elle seule a empêché l'utilisation des interféromètres laser pour la compensation des robots. D'autres solutions précoces, comme la triangulation laser et les potentiomètres optiques à câble, ont fait l’objet de recherches et de tests, mais rien de bien faisable n’a abouti pour la facilité d’emploi et la précision requises.
Au début des années 1980, quelques organisations se sont regroupées pour essayer de résoudre le problème des limites du guidage de précision de l’interféromètre laser à travers différents systèmes de poursuite. Les experts du Bureau national des normes (NBS), devenu entre temps le NIST, l’université de Surrey en Angleterre et le FhG de Karlsruhe, en Allemagne, ont travaillé sur des projets basés sur l'intégration d’un interféromètre laser dans un système de poursuite pour créer un interféromètre de poursuite laser. Vers la fin de la décennie, des entreprises aux États-Unis et en Europe ont commencé à se pencher sur le concept d’un laser tracker pour les applications de mesure industrielles, un système convenant à l’environnement de production, en dehors du laboratoire. En 1990, le salon Qualité à Chicago a dévoilé le laser tracker Leica Geosystems Smart 310, un tracker utilisable dans un environnement de production à l’extérieur du laboratoire.
Entre le début et le milieu des années 1990, les laser trackers Leica ont commencé à s’établir dans la calibration des robots. On a développé un logiciel de calibration pour ordonner au robot d’exécuter des mouvements sur la base de coordonnées dans un espace de travail, puis d’enregistrer les positions actuelles comme elles sont mesurées par le tracker. En comparant les positions théorique et actuelle, le logiciel crée un jeu de paramètres de compensation capable de compenser le positionnement du robot et donc ses mouvements. Les paramètres tiennent compte à la fois des imperfections mécaniques dans les mouvements opérés et de la courbure ou des distorsions vers le bas sous l’effet des charges. Cette calibration de précision absolue corrige un robot présentant une variabilité de 8 à 15 mm à 0,5 mm.
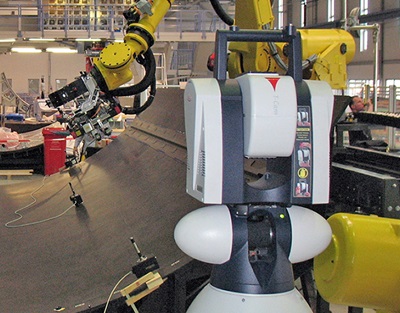
Par exemple, si vous utilisez un robot qui est resté au repos, il se dilatera au fur et à mesure de l'échauffement en raison de la dilatation thermique de ses liaisons. Durant la phase de mise en température, le changement peut atteindre 0,5 mm (0,020 pouce) ou plus, ce qui a un effet important sur la répétabilité des mesures. Mais, le logiciel de calibration peut calculer et supprimer ces effets thermiques des mesures de façon à ce qu’elles présentent une répétabilité cohérente (habituellement dans une plage de 0,10 mm ou 0,004 pouce 6 sigma).
Aujourd’hui, ces processus sont bien établis et appliqués presque quotidiennement. Mais cela ne signifie pas qu’il n’y ait pas de marge pour d'autres perfectionnements. Durant la dernière décennie, les laser trackers Leica ont enregistré une grande amélioration au niveau de la fonctionnalité. L’une des améliorations les plus significatives est la capacité du laser tracker Leica à réaliser des mesures avec six degrés de liberté (6 DoF). Cette aptitude permet aux fabricants de robots de corriger l’effecteur pendant un cycle de calibration avec moins de poses. Mais elle offre aussi de nouvelles possibilités. Par le passé, lors de l’utilisation d’un laser tracker 3D classique, il fallait mesurer de nombreuses positions pour calculer le centre de l’outil dans un espace 6D. Aujourd’hui, en utilisant un laser tracker AT901 6 DoF, il est possible de connaître l’emplacement précis de l’effecteur dans un espace 6D en temps réel. Cette innovation supprime complètement la nécessité d'une calibration de robot puisque le tracker peut surveiller et corriger la position de l’effecteur en temps réel, sans se soucier de ce que le robot fait dans « l’espace joint ».
Cette technologie avancée a récemment été appliquée chez Premium Aerotec (Nordenahm, Allemagne) pour automatiser le processus de pose des longerons pour la section du fuselage du nouvel Airbus A350 XWB. Comme les longerons faisaient jusqu’à 18 mètres de long, la précision absolue spécifiée des robots utilisés n'était pas assez élevée pour une mise en place correcte. L'équipe n’a pu respecter le haut niveau d’exigence de précision qu’en corrigeant les robots en temps réel sur la base du feedback de l’Absolute laser tracker 6 DoF.
Les cellules automatisées basées sur des robots et les systèmes de mesure mobiles ne sont plus considérés comme futuristes, et ces mises en œuvre se sont étendues à l’échelle mondiale. Aux quatre coins du monde, Hexagon Metrology a installé plus de 60 cellules automatisées basées sur des robots et des systèmes de mesure mobiles. Comme résultat de cette intelligence, différents fabricants et secteurs explorent leurs processus sous un nouvel angle, en se concentrant sur des domaines où l'automatisation des mesures et de l’inspection peuvent jouer un rôle primordial. Face à ce changement paradigmatique, l’histoire de la production évolue sous nos yeux.