A automação da metrologia é aqui e agora
Mesmo se você não vir ou usar estes robôs diariamente, eles estão trabalhando nos bastidores. Eles ajudaram a construir o automóvel que você dirige, o celular que está sempre em sua mão e o computador do qual depende.
Contato
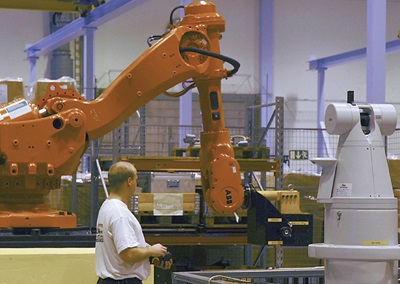
A IFR também relatou outra tendência interessante para os EUA – as encomendas de robôs subiram novamente por % para um novo nível de pico de 22.414 unidades em 2012, em comparação com o ano anterior, enquanto as vendas já haviam subido substancialmente em 2010 e 2011. O relatório do presidente da IFR corroborou os dados de mercado para os três primeiros trimestres de 2013 que mostrou um aumento em comparação com o mesmo período do ano passado.
Mesmo se você não vir ou usar estes robôs diariamente, eles estão trabalhando nos bastidores. Eles ajudaram a construir o automóvel que você dirige, o celular que está sempre em sua mão e o computador do qual depende. Seria quase impossível passar um dia inteiro e não entrar em contato com algo criado por essas máquinas. O progresso tem sido incrível considerando que este nível de automação de fábrica era apenas um sonho não muito tempo atrás. Como os robôs se tornam mais precisos e inteligentes, mais tarefas eles podem executar, aumentando o seu uso ainda mais em novas indústrias e aplicações.
Há um grande desejo de tornar essas máquinas eletromecânicas mais precisas, desde a introdução de robôs industriais para automação industrial. Nas décadas de 1970 e 80, os robôs foram amplamente integrados na fabricação de automóveis, mas raramente usados na fabricação aeroespacial. Eles simplesmente não eram suficientemente precisos para realizar as tarefas necessárias. Nos anos 80 e início dos anos 90, muitos dos fabricantes de robôs começaram a encontrar maneiras de abordar esta questão.
Por natureza, os robôs industriais são bastante repetitivos, mas sua exatidão absoluta é muito fraca. Por exemplo, se um programa instrui o instrumento terminal efetivo de um robô para mover 30 polegadas na direção "Y", ele pode mover 31 polegadas, em vez de as 30 polegadas programadas. No entanto, ele iria mover as mesmas 31 polegadas toda vez. Porque suas ações são repetíveis, os robôs poderiam ser compensados com um nível de precisão absoluta. Ao medir o robô em um determinado número de poses, comprimentos de ligação, ângulos de torção, zeros de articulação, offsets de link e parâmetros de rigidez podem ser intrinsecamente calculados para corrigir o modelo de robô.
A principal dificuldade foi como medir o robô através de todas estas poses nas mais variadas faixas de temperatura com uma precisão alta o suficiente para criar um modelo de valor. Neste ponto no tempo, o dispositivo mais procurado para distâncias de precisão e mesmo medição da angularidade era o interferômetro a laser. O problema com interferômetros a laser era que exigiam orientação precisa de um refletor para evitar a interrupção do feixe de laser. À medida que o refletor é movido em linha com o feixe de laser, a direção do movimento e uma contagem dos picos de onda são registradas. O grau de alteração da distância pode, em seguida, ser calculado quando multiplicado por metade do comprimento de onda do laser. No entanto, se este processo de contagem é interrompido a qualquer momento (isto é, através da interrupção do feixe), todo o processo tem de recomeçar do início e da posição inicial exata do refletor. Esta limitação foi suficiente para evitar que os interferômetros a laser fossem amplamente aplicados para a compensação do robô. Outras soluções precoces, como triangulação a laser e caixas de cordas ópticas foram estudadas e testadas, mas nada viabilizava a facilidade de uso e precisão necessárias.
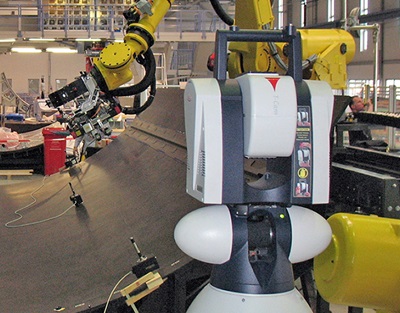
No início de 1980, algumas organizações se uniram para tentar resolver as limitações de orientação de precisão do interferômetro a laser através de vários sistemas de "rastreamento". Especialistas do National Bureau of Standards (NBS), agora conhecido como NIST, da Universidade de Surrey, na Inglaterra, e a FhG Karlsruhe na Alemanha trabalharam em projetos com base na integração de um interferômetro a laser com um sistema de rastreamento para criar um interferômetro de rastreamento a laser. Perto do final da década, as empresas nos EUA e Europa comeaçram a trabalhar no conceito de um rastreador a laser para aplicações de medição industriais, um sistema que pudesse ser utilizado num ambiente de produção fora de um laboratório. Em 1990, o rastreador a laser 310 Leica Geosystems inteligente, um rastreador que poderia ser usado em um ambiente de produção fora do laboratório, foi apresentado ao mundo na feira de Qualidade em 1990, em Chicago.
No início e meados dos anos 90, os rastreadores a laser Leica começaram a encontrar espaço na calibração de robô. O software de calibração foi desenvolvido para instruir um robô a se mover para coordenar posições em uma área de trabalho, em seguida, registrar as posições reais, medidas pelo rastreador. Ao comparar as posições teóricas e reais, o software iria criar um conjunto de parâmetros de compensação que iria corrigir o posicionamento do robô e, assim, os seus movimentos. Os parâmetros levariam em conta tanto as imperfeições mecânicas no padrão dos movimentos e as distorções de flexão reduzidas causados pelas cargas. Esta calibração de precisão absoluta seria capaz de corrigir um robô com a variabilidade entre 8 a 15 mm, até cerca de 0,5 mm.
A maioria dos fabricantes de robôs grandes ofereceu robôs compensados semelhantes ao longo deste período. No entanto, cada fabricante tinha seu próprio processo proprietário e os clientes com tipos de robôs de fabricantes diferentes foram deixados sem uma forma de harmonizar os processos de calibração e plataformas. Este dilema levou várias empresas a oferecerem pacotes de calibração de robôs para estes casos. Estes módulos de software podem permitir que um robô de qualquer fabricante seja calibrado ambos extrinsecamente (localizado na área de trabalho) e intrinsecamente (comprimentos de ligação, ângulos de torção, etc.). Um exemplo de tal software é o módulo da máquina SA desenvolvido pela New River Kinematics. Além disso, também compensar os efeitos da variação térmica do robô.
Por exemplo, quando você usa um robô que estava ocioso, ele irá expandir fisicamente ao passo que ele aquece a partir da expansão térmica de suas ligações. Como um robô continua a aquecer, a mudança pode ser tão grande como 0,5 mm (0,020 polegadas) ou mais, o que pode afetar significativamente a repetibilidade das medições. No entanto, o software de calibração pode calcular e remover esses efeitos térmicos a partir das medições para que eles sejam consistentemente repetíveis (normalmente dentro de 0,10 mm ou 0,004 polegadas 6 sigma).
Hoje, esses processos estão bem estabelecidos e utilizados quase diariamente. Mas isso não significa que não há espaço para mais avanços. Na última década, os rastreadores a laser Leica têm melhorado muito em termos de funcionalidade. Uma das melhorias mais significativas é a capacidade do rastreador a laser Leica para medir, em um total de seis graus de liberdade, ou 6DOF. Esta capacidade permite que os fabricantes de robôs possam corrigir o instrumento terminal do robô durante um ciclo de calibração com menos poses, mas também abriu novas possibilidades. No passado, quando se utiliza um rastreador a laser tradicional 3D, várias posições teve de ser medido para calcular o ponto central ferramental (TCP) no espaço 6D. Agora, utilizando o rastreador a laser 6DOF AT901, é possível conhecer a localização exata do efetor final no espaço 6D em tempo real. Esta inovação elimina a necessidade de calibração robô completamente quanto o rastreador pode monitorar e corrigir a posição do instrumento terminal em tempo real sem a necessidade de se preocupar com o que o robô está fazendo no "espaço comum".
Esta tecnologia avançada foi recentemente aplicado na Premium Aerotec (Nordenahm, Alemanha) para automatizar o processo de colocação de longarinas para a seção de fuselagem do novo Airbus A350XWB. Porque as longarinas tinham até 18 metros de comprimento, a precisão absoluta especificada dos robôs sendo utilizados ainda não precisa o suficiente para instalá-las adequadamente. A equipe só foi capaz de satisfazer as suas exigências de precisão rigorosas corrigindo os robôs em tempo real com base no feedback do rastreador a laser 6DoF Absolut.
As células automatizadas, baseadas em robôs e sistemas de medição móveis não são mais vistas como futuristas, e essas implementações têm crescido substancialmente em escala mundial. Em todo o mundo, a Hexagon Manufacturing Intelligence implementou mais de 60 células automatizadas baseadas em robôs e sistemas de medição móveis. Como resultado dessa inteligência, uma variedade de fabricantes e indústrias está investigando seus processos com um olhar inovador, voltando suas atenções a áreas onde a medição e inspeção de automação podem desempenhar um papel vital. No meio de uma mudança de paradigma, a história de fabricação está mudando diante de nossos olhos.
Automated cells based on robots and mobile measurement systems are no longer viewed as futuristic, and these implementations have grown substantially in a worldwide scale. Worldwide, Hexagon Manufacturing Intelligence has implemented more than 60 automated cells based on robots and mobile measurement systems. As a result of this intelligence, a variety of manufacturers and industries are investigating their processes with fresh eyes, setting their sights on areas where measurement and inspection automation can play a vital role. In the midst of a paradigm shift, manufacturing history is changing right before our eyes.