L'automazione della misura è già qui
Anche se non li vediamo e non li impieghiamo ogni giorno, questi robot lavorano dietro le quinte. Hanno contribuito a costruire l'auto che guidiamo, il telefono costantemente a portata di mano, il computer da cui dipendiamo.
Contattateci
I robot industriali sono diventati parte della nostra vita quotidiana. In un rapporto del 2013 della International Federation of Robotics (IFR), l'anno 2012 ha registrato il secondo posto per vendite di robot nell'arco di un anno. Delle 159.346 unità vendute, circa il 70% è andato a Stati Uniti, Giappone, Germania, Cina e Corea. I settori automotive, alimentare, chimico, gomma e plastica hanno visto un'impennata negli ordini di robot mentre nel settore metalmeccanico c'è stato un leggero calo.
L'IFR ha riportato anche un'altra interessante tendenza per gli USA: le consegne di robot sono aumentate nuovamente del 9% rispetto all'anno precedente, salendo al nuovo massimo di 22.414 unità nel 2012, mentre le vendite erano già notevolmente aumentate nel 2010 e nel 2011.
L'IFR President’s Report affermava che i dati di mercato per i primi tre trimestri del 2013 hanno rivelato un ulteriore aumento rispetto allo stesso periodo dell’anno precedente.
Anche se non li vediamo e non li impieghiamo ogni giorno, questi robot lavorano dietro le quinte. Hanno contribuito a costruire l'auto che guidiamo, il telefono costantemente a portata di mano, il computer da cui dipendiamo. Sarebbe quasi impossibile trascorrere un intero giorno senza entrare in contatto con qualcosa di creato con l'ausilio di queste macchine straordinarie.
Il progresso compiuto à stato incredibile se si considera che il livello di automazione in fabbrica era solo una chimera non molto tempo fa. Man mano che i robot diventano più precisi e intelligenti, sono in grado di eseguire più operazioni, e il loro uso si diffonde così in nuovi settori dell'industria e in nuove applicazioni.
C'è stato un forte desiderio di rendere più precise queste macchine elettromeccaniche, a partire dall'introduzione dei robot industriali per l'automazione della fabbrica. Negli anni '70 e '80 i robot erano ampiamente integrati nella produzione automobilistica ma venivano raramente usati nella produzione aerospaziale. Semplicemente non erano abbastanza precisi per svolgere le operazioni necessarie. Alla fine degli anni '80 e inizio anni '90, molti costruttori di robot hanno iniziato a trovare dei modi per affrontare questo problema.
I robot industriali sono piuttosto ripetibili per natura ma la loro precisione assoluta è molto scarsa. Ad esempio, se un programma istruisce l'elemento terminale di un manipolatore a eseguire un movimento di 30 pollici in direzione Y, questo può magari muoversi invece di 31 pollici. Il movimento sarà tuttavia costantemente di 31 pollici.
Poiché le loro azioni sono ripetibili, i robot potrebbero essere quindi compensati per raggiungere un livello di precisione più elevato. Misurando il robot in un numero definito di posizioni, le lunghezze degli snodi, gli angoli di torsione, gli zeri comuni, gli offset degli snodi e i parametri di rigidità potrebbero essere calcolati intrinsecamente per correggere il modello del robot.
La difficoltà principale fu quella di misurare il robot in tutte queste posizioni in varie fasce di temperatura con una precisione abbastanza elevata da creare un modello proficuo. A questo punto, il dispositivo di riferimento per le distanze di precisione e persino la misura dell'angolarità era l'interferometro laser. Il problema degli interferometri laser era che richiedevano la guida precisa di un retroriflettore per evitare l'interruzione del raggio laser. Poiché il riflettore viene spostato in asse con il raggio laser, si registrano la direzione di movimento e il conteggio dei picchi d'onda. La variazione esatta della distanza può essere poi calcolata quando viene moltiplicata per la metà della lunghezza d'onda del laser. Se questo processo di conteggio, tuttavia, viene interrotto in qualunque momento (cioè con l'interruzione del raggio), l'intero processo deve ricominciare dall'inizio e dalla posizione iniziale esatta del riflettore. Questa limitazione da sola fu sufficiente a impedire un'applicazione diffusa della compensazione del robot. Altre soluzioni iniziali, come la triangolazione laser e i trasduttori ottici, furono studiate e testate ma nulla forniva in modo praticabile la facilità d'uso e la precisione necessarie.
All'inizio degli anni '80, alcune organizzazioni unirono le forze per cercare di risolvere i limiti della guida di precisione dell'interferometro laser attraverso vari sistemi di tracciamento. Esperti del National Bureau of Standards (NBS) che è ora il NIST, l'Università del Surrey in Inghilterra, e l'FhG Karlsruhe in Germania lavorarono a progetti basati sull'integrazione di un interferometro laser con un sistema di tracciamento per creare un interferometro di tracciamento laser. Verso la fine del decennio, aziende negli USA e in Europa cominciarono a lavorare a un laser tracker per applicazioni di misura industriali, un sistema che potesse essere impiegato in un ambiente di produzione, al di fuori di un laboratorio. Nel 1990, alla fiera Quality di Chicago, venne presentato il Leica Geosystems Smart 310, un laser tracker che poteva essere usato al di fuori del laboratorio, in un ambiente di produzione.
Dall'inizio a metà anni '90, i laser tracker Leica iniziarono a comparire nella calibrazione dei robot. Venne sviluppato un software di calibrazione per istruire il robot a muoversi verso posizioni coordinate in un'area di lavoro, e poi a registrare le posizioni reali misurate dal tracker. Confrontando posizioni reali ed effettive, il software creava una serie di parametri di compensazione che correggevano il posizionamento del robot e quindi i suoi movimenti. I parametri consideravano sia le imperfezioni meccaniche nella sequenza dei movimenti, sia le flessioni o distorsioni verso il basso dovute ai carichi. Questa calibrazione della precisione assoluta correggeva il robot con una variabilità tra gli 8 e i 15 mm, a circa 0,5 mm.
In questo periodo, la maggior parte dei grandi costruttori di robot offriva robot compensati in modo simile. Ma ogni costruttore aveva il proprio processo proprietario e gli utilizzatori di robot di costruttori diversi vennero lasciati senza un metodo per armonizzare processi e piattaforme di calibrazione. Questo problema indusse alcune aziende a offrire pacchetti di calibrazione dei robot per questi casi. Questi moduli software permettono di calibrare il robot di qualunque costruttore sia estrinsecamente (collocato nel luogo di lavoro) che intrinsecamente (lunghezze degli snodi, angoli di torsione, ecc.). Uno di questi software è il modulo SA Machine sviluppato dalla New River Kinematics che compensa anche gli effetti della variazione termica sul robot.
Quando ad esempio si usa un robot che è stato inattivo, questo si espande fisicamente poiché si riscalda a causa dell'espansione termica dei suoi snodi. Man mano che il robot continua a riscaldarsi, il cambiamento può essere di 0,5 mm o maggiore, il che può incidere in misura significativa sulla ripetibilità delle misure. Il software di calibrazione, tuttavia, può calcolare ed eliminare questi effetti termici dalle misure in modo che queste siano ripetibili in modo uniforme (tipicamente entro 0,10 mm o 0,004 pollici 6 sigma).
Oggi questi processi sono consolidati e impiegati quasi ogni giorno. Questo non significa però che non ci sia spazio per ulteriori perfezionamenti. Nell'ultimo decennio, i laser tracker Leica hanno migliorato molto la funzionalità. Uno dei miglioramenti più significativi è la capacità del Leica laser tracker di misurare nei Sei Gradi di Libertà o 6DoF. Questa capacità permette ai costruttori di correggere l'elemento terminale del manipolatore durante un ciclo di calibrazione con meno posizioni, ma ha anche aperto nuove possibilità. In passato quando si usava un laser tracker 3D tradizionale, si dovevano misurare più posizioni per calcolare il centro dell’attrezzo o dell’utensile (TCP) nello spazio 6D. Ora con l'uso del laser tracker AT901 6DoF è possibile conoscere la posizione esatta dell'elemento terminale nello spazio 6D in tempo reale. Grazie a questa novità non è più necessario calibrare il robot poiché il tracker è in grado di monitorare e correggere la posizione dell'elemento terminale in tempo reale, senza doversi preoccupare di ciò che succede al robot nello "spazio degli snodi".
Questa tecnologia avanzata è stata applicata recentemente alla Premium Aerotec (Nordenahm in Germania) per automatizzare il processo di posizionamento dei correntini della fusoliera del nuovo Airbus A350 XWB. I correntini arrivavano a 18 metri di lunghezza, sicché la precisione assoluta dei robot impiegati non era sufficiente per poterli collocare in modo corretto. Il team poté rispettare i severi requisiti di precisione correggendo i robot in tempo reale sulla base dei feedback ricevuti dall'Absolute laser tracker 6DoF.
Le celle automatizzate basate su robot e sistemi di misura mobili non sono più considerate futuristiche, e queste realizzazioni hanno avuto una crescita notevole su scala mondiale. In varie parti del mondo Hexagon Manufacturing Intelligence ha implementato oltre 60 celle automatizzate basate su robot e sistemi di misura mobili. Come conseguenza di ciò, numerosi produttori e settori dell'industria stanno studiando i propri processi in un’ottica nuova, considerando aree in cui l'automazione di misura e verifica può svolgere un ruolo essenziale. La storia della produzione, al centro di una rivoluzione copernicana, sta cambiando davanti ai nostri occhi.
L'IFR ha riportato anche un'altra interessante tendenza per gli USA: le consegne di robot sono aumentate nuovamente del 9% rispetto all'anno precedente, salendo al nuovo massimo di 22.414 unità nel 2012, mentre le vendite erano già notevolmente aumentate nel 2010 e nel 2011.
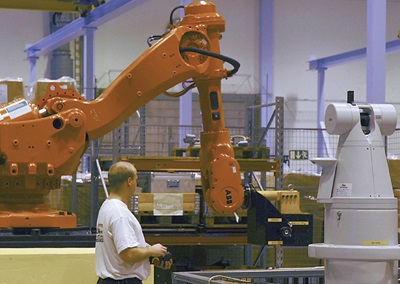
Anche se non li vediamo e non li impieghiamo ogni giorno, questi robot lavorano dietro le quinte. Hanno contribuito a costruire l'auto che guidiamo, il telefono costantemente a portata di mano, il computer da cui dipendiamo. Sarebbe quasi impossibile trascorrere un intero giorno senza entrare in contatto con qualcosa di creato con l'ausilio di queste macchine straordinarie.
Il progresso compiuto à stato incredibile se si considera che il livello di automazione in fabbrica era solo una chimera non molto tempo fa. Man mano che i robot diventano più precisi e intelligenti, sono in grado di eseguire più operazioni, e il loro uso si diffonde così in nuovi settori dell'industria e in nuove applicazioni.
C'è stato un forte desiderio di rendere più precise queste macchine elettromeccaniche, a partire dall'introduzione dei robot industriali per l'automazione della fabbrica. Negli anni '70 e '80 i robot erano ampiamente integrati nella produzione automobilistica ma venivano raramente usati nella produzione aerospaziale. Semplicemente non erano abbastanza precisi per svolgere le operazioni necessarie. Alla fine degli anni '80 e inizio anni '90, molti costruttori di robot hanno iniziato a trovare dei modi per affrontare questo problema.
I robot industriali sono piuttosto ripetibili per natura ma la loro precisione assoluta è molto scarsa. Ad esempio, se un programma istruisce l'elemento terminale di un manipolatore a eseguire un movimento di 30 pollici in direzione Y, questo può magari muoversi invece di 31 pollici. Il movimento sarà tuttavia costantemente di 31 pollici.
Poiché le loro azioni sono ripetibili, i robot potrebbero essere quindi compensati per raggiungere un livello di precisione più elevato. Misurando il robot in un numero definito di posizioni, le lunghezze degli snodi, gli angoli di torsione, gli zeri comuni, gli offset degli snodi e i parametri di rigidità potrebbero essere calcolati intrinsecamente per correggere il modello del robot.
La difficoltà principale fu quella di misurare il robot in tutte queste posizioni in varie fasce di temperatura con una precisione abbastanza elevata da creare un modello proficuo. A questo punto, il dispositivo di riferimento per le distanze di precisione e persino la misura dell'angolarità era l'interferometro laser. Il problema degli interferometri laser era che richiedevano la guida precisa di un retroriflettore per evitare l'interruzione del raggio laser. Poiché il riflettore viene spostato in asse con il raggio laser, si registrano la direzione di movimento e il conteggio dei picchi d'onda. La variazione esatta della distanza può essere poi calcolata quando viene moltiplicata per la metà della lunghezza d'onda del laser. Se questo processo di conteggio, tuttavia, viene interrotto in qualunque momento (cioè con l'interruzione del raggio), l'intero processo deve ricominciare dall'inizio e dalla posizione iniziale esatta del riflettore. Questa limitazione da sola fu sufficiente a impedire un'applicazione diffusa della compensazione del robot. Altre soluzioni iniziali, come la triangolazione laser e i trasduttori ottici, furono studiate e testate ma nulla forniva in modo praticabile la facilità d'uso e la precisione necessarie.
All'inizio degli anni '80, alcune organizzazioni unirono le forze per cercare di risolvere i limiti della guida di precisione dell'interferometro laser attraverso vari sistemi di tracciamento. Esperti del National Bureau of Standards (NBS) che è ora il NIST, l'Università del Surrey in Inghilterra, e l'FhG Karlsruhe in Germania lavorarono a progetti basati sull'integrazione di un interferometro laser con un sistema di tracciamento per creare un interferometro di tracciamento laser. Verso la fine del decennio, aziende negli USA e in Europa cominciarono a lavorare a un laser tracker per applicazioni di misura industriali, un sistema che potesse essere impiegato in un ambiente di produzione, al di fuori di un laboratorio. Nel 1990, alla fiera Quality di Chicago, venne presentato il Leica Geosystems Smart 310, un laser tracker che poteva essere usato al di fuori del laboratorio, in un ambiente di produzione.
Dall'inizio a metà anni '90, i laser tracker Leica iniziarono a comparire nella calibrazione dei robot. Venne sviluppato un software di calibrazione per istruire il robot a muoversi verso posizioni coordinate in un'area di lavoro, e poi a registrare le posizioni reali misurate dal tracker. Confrontando posizioni reali ed effettive, il software creava una serie di parametri di compensazione che correggevano il posizionamento del robot e quindi i suoi movimenti. I parametri consideravano sia le imperfezioni meccaniche nella sequenza dei movimenti, sia le flessioni o distorsioni verso il basso dovute ai carichi. Questa calibrazione della precisione assoluta correggeva il robot con una variabilità tra gli 8 e i 15 mm, a circa 0,5 mm.
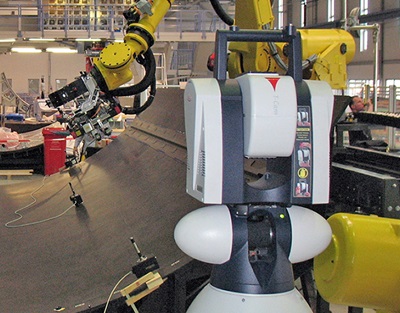
Quando ad esempio si usa un robot che è stato inattivo, questo si espande fisicamente poiché si riscalda a causa dell'espansione termica dei suoi snodi. Man mano che il robot continua a riscaldarsi, il cambiamento può essere di 0,5 mm o maggiore, il che può incidere in misura significativa sulla ripetibilità delle misure. Il software di calibrazione, tuttavia, può calcolare ed eliminare questi effetti termici dalle misure in modo che queste siano ripetibili in modo uniforme (tipicamente entro 0,10 mm o 0,004 pollici 6 sigma).
Oggi questi processi sono consolidati e impiegati quasi ogni giorno. Questo non significa però che non ci sia spazio per ulteriori perfezionamenti. Nell'ultimo decennio, i laser tracker Leica hanno migliorato molto la funzionalità. Uno dei miglioramenti più significativi è la capacità del Leica laser tracker di misurare nei Sei Gradi di Libertà o 6DoF. Questa capacità permette ai costruttori di correggere l'elemento terminale del manipolatore durante un ciclo di calibrazione con meno posizioni, ma ha anche aperto nuove possibilità. In passato quando si usava un laser tracker 3D tradizionale, si dovevano misurare più posizioni per calcolare il centro dell’attrezzo o dell’utensile (TCP) nello spazio 6D. Ora con l'uso del laser tracker AT901 6DoF è possibile conoscere la posizione esatta dell'elemento terminale nello spazio 6D in tempo reale. Grazie a questa novità non è più necessario calibrare il robot poiché il tracker è in grado di monitorare e correggere la posizione dell'elemento terminale in tempo reale, senza doversi preoccupare di ciò che succede al robot nello "spazio degli snodi".
Questa tecnologia avanzata è stata applicata recentemente alla Premium Aerotec (Nordenahm in Germania) per automatizzare il processo di posizionamento dei correntini della fusoliera del nuovo Airbus A350 XWB. I correntini arrivavano a 18 metri di lunghezza, sicché la precisione assoluta dei robot impiegati non era sufficiente per poterli collocare in modo corretto. Il team poté rispettare i severi requisiti di precisione correggendo i robot in tempo reale sulla base dei feedback ricevuti dall'Absolute laser tracker 6DoF.
Le celle automatizzate basate su robot e sistemi di misura mobili non sono più considerate futuristiche, e queste realizzazioni hanno avuto una crescita notevole su scala mondiale. In varie parti del mondo Hexagon Manufacturing Intelligence ha implementato oltre 60 celle automatizzate basate su robot e sistemi di misura mobili. Come conseguenza di ciò, numerosi produttori e settori dell'industria stanno studiando i propri processi in un’ottica nuova, considerando aree in cui l'automazione di misura e verifica può svolgere un ruolo essenziale. La storia della produzione, al centro di una rivoluzione copernicana, sta cambiando davanti ai nostri occhi.