Automatisierung in der industriellen Messtechnik – keine Zukunftsmusik, sondern längst Realität
Kontakt
Industrieroboter gehören für uns schon seit geraumer Zeit zum Alltag. Einer 2013 veröffentlichten Studie der International Federation of Robotics (IFR) zufolge, wurde 2012 die zweithöchste Anzahl an binnen eines Jahres weltweit abgesetzten Robotern erzielt. Von den 159.346 verkauften Robotern gingen fast 70 % in die Vereinigten Staaten, nach Japan, Deutschland, China oder Korea. In der Automobil-, Lebensmittel-, Chemikalien-, Gummi- und Kunststoffindustrie wurden ungewöhnlich hohe Bestellmengen verzeichnet, während der Bedarf in der Metall- und Maschinenbaubranche leicht rückläufig war.
Die IFR hat zudem in den USA einen interessanten Trend festgestellt: Die Anzahl der ausgelieferten Roboter stieg 2012 anteilsmäßig auf einen neuen Spitzenwert von 22.414 Stück im Vergleich zum Vorjahr, obwohl die Verkaufszahlen schon in den Jahren 2010 und 2011 deutlich zugenommen hatten. Laut Studie zeigten die Absatzzahlen der ersten drei Quartale 2013 zudem bezogen auf den Vergleichszeitraum des Vorjahres einen weiteren Anstieg.
Auch oder gerade für diejenigen unter uns, die nicht täglich mit Robotern zu tun haben, gehen diese zuverlässigen, fleißigen Gesellen stillschweigend im Hintergrund ihrer Arbeit nach. Sie haben beim Bau des Autos geholfen, das Sie fahren, waren an der Erzeugung des Mobiltelefons beteiligt, das Sie immer bei sich tragen, und haben den Computer hergestellt, den Sie täglich verwenden. Es ist praktisch unmöglich, einen Tag lang in unserer modernen Gesellschaft zu leben, ohne in Kontakt mit einem von einer dieser vielseitigen Maschinen hergestellten Produkt zu kommen. Angesichts der Tatsache, dass ein solcher Automatisierungsgrad in der Fertigung noch bis vor kurzer Zeit als vollkommen illusorisch galt, ist der weltweite Siegeszug des Industrieroboters geradezu verblüffend. Infolge ihrer zunehmenden Genauigkeit und Intelligenz können Roboter immer mehr Aufgaben übernehmen, sodass sich ihr Einsatzbereich auf neue Branchen und Anwendungen ausweitet.
Schon seit den frühesten Anfängen dieser elektromechanischen Helferlein in der Fertigungsautomatisierung besteht der dringende Wunsch nach höherer Präzision. In den 1970er und 1980er Jahren wurden Roboter auf breiter Basis in der Automobilindustrie eingesetzt, während sie im Flugzeugbau nur selten anzutreffen waren, da ihre Genauigkeit für solche Anwendungen einfach noch nicht ausreichte. In den späten 1980ern und frühen 1990ern begannen die Roboterhersteller, Lösungen für dieses Problem zu finden.
Industrieroboter weisen naturgemäß eine hohe Wiederhol- aber eine geringe absolute Genauigkeit auf. Ist im Programm hinterlegt, dass sich der Endeffektor eines Roboters 30 Zentimeter in Y-Richtung bewegen soll, kann es sein, dass er sich stattdessen 30,5 Zentimeter in Y-Richtung bewegt. Ist dies der Fall, bewegt er sich dann allerdings auch zuverlässig jedes Mal 30,5 Zentimeter in Y-Richtung. Aufgrund dieser Wiederholbarkeit ließ sich die Ungenauigkeit der Roboter kompensieren, um ein gewisses Maß an absoluter Genauigkeit zu erzielen. Durch die exakte Vermessung des Roboters in unterschiedlichen Stellungen konnten anhand der Gliedlängen, Torsionswinkel, Nullpositionen der Gelenke, Versatzwerte der Glieder und Steifigkeitsparameter spezifische Korrekturen für das Robotermodell berechnet werden.
Die Hauptschwierigkeit dabei war die Vermessung des Roboters in allen Stellungen innerhalb unterschiedlicher Temperaturbereiche, um aus den Messdaten ein möglichst zuverlässiges Modell zu generieren. Zu dieser Zeit war das Laserinterferometer das Hilfsmittel der Wahl, wenn es um die präzise Distanz- und sogar Winkelmessung ging. Das Problem bei Laserinterferometern bestand jedoch darin, dass sie einer exakten Führung mit einem Retroreflektor bedurften, um Unterbrechungen des Laserstrahls zu vermeiden. Während der Bewegung des Reflektors in Abstimmung mit dem Laserstrahl werden die Bewegungsrichtung und die Anzahl der Wellenberge erfasst. Auf dieser Basis lässt sich die exakte Änderung der Distanz durch Multiplikation mit der halben Wellenlänge des Lasers berechnen. Wird der Zählvorgang jedoch zu irgendeinem Zeitpunkt gestört (z. B. durch eine Strahlunterbrechung), muss der gesamte Prozess ausgehend von der exakten ursprünglichen Reflektorposition neu begonnen werden. Allein aus diesem Grund setzten sich Laserinterferometer für die Roboterkompensation nie wirklich durch. Mit anderen frühen Lösungen wie Lasertriangulation und optischen Potenziometern wurde experimentiert, doch keine bot die erforderliche Benutzerfreundlichkeit und Genauigkeit.
In den frühen 1980er Jahren taten sich einige Einrichtungen zusammen, um die Probleme des Laserinterferometers bei der präzisen Strahlverfolgung durch verschiedene sogenannte Trackingsysteme zu lösen. Fachleute des damaligen National Bureau of Standards (NBS) – des heutigen NIST –, der University of Surrey in England und der FhG Karlsruhe arbeiteten gemeinsam an Projekten zur Integration von Laserinterferometer und Trackingsystem. Ziel war es, ein Interferometer zu entwickeln, das zur selbständigen Verfolgung eines Lasers in der Lage war. Gegen Ende dieses Jahrzehnts begannen Unternehmen in den USA und Europa mit der Konzeption eines Laser Trackers für industrielle Messanwendungen, wobei dieses System außerhalb des Messlabors in einer Fertigungsumgebung einsetzbar sein sollte. Das Ergebnis war der Leica Geosystems Smart 310 Laser Tracker, der der Fachwelt auf der Branchenmesse „Quality“ 1990 in Chicago vorgestellt wurde.
Damit begannen die Laser Tracker von Leica Anfang bis Mitte der 1990er Jahre in der Roboterkalibrierung Fuß zu fassen. Dazu wurde eine Kalibriersoftware entwickelt, die dem Roboter befahl, sich zu bestimmten Koordinaten innerhalb eines Arbeitsbereichs zu bewegen, und dann die tatsächlichen vom Laser Tracker gemessenen Positionen erfasste. Mittels Abgleich von Soll- und Istpositionen konnte die Software anschließend Kompensationsparameter zur Korrektur der Positionierung und damit der Bewegungen des Roboters berechnen. Diese Parameter berücksichtigten sowohl die mechanischen Mängel im Bewegungsablauf als auch die Biegung und Verformung unter Last. Durch diese Kalibrierung der Absolutgenauigkeit konnte die Messunsicherheit eines Roboters erheblich von acht bis 15 Millimeter auf ca. einen halben Millimeter reduziert werden.
Damals boten die meisten großen Roboterhersteller auf diese Art kompensierte Roboter an. Allerdings ging jeder Hersteller dabei unterschiedlich vor, und Kunden mit Robotern unterschiedlicher Hersteller hatten keinerlei Möglichkeit zur Vereinheitlichung von Kalibriervorgängen und -plattformen. Deshalb brachten einige Unternehmen Softwarepakete zur Roboterkalibrierung auf den Markt. Mithilfe dieser Softwaremodule ließen sich Roboter aller Hersteller sowohl extrinsisch (innerhalb des Arbeitsbereichs) als auch intrinsisch (Gliedlängen, Torsionswinkel usw.) kalibrieren. Ein Beispiel für eine solche Software ist das von New River Kinematics entwickelte Modul SA Machine. Es diente außerdem zur Kompensation von Temperaturveränderungen des Roboters.
Beispielsweise dehnt sich ein Roboter, der sich zuvor im Ruhemodus befand, bei der Verwendung infolge der thermischen Expansion seiner Glieder physikalisch aus. Diese Größenänderung während des Aufwärmens des Roboters kann 0,5 Millimeter und mehr betragen, was sich erheblich auf die Wiederholbarkeit der Messungen auswirken kann. Die Kalibriersoftware kann diese Thermoeffekte jedoch berechnen und die Messwerte entsprechend bereinigen, um so eine hohe Wiederholgenauigkeit zu erzielen (0,10 Millimeter 6 Sigma typisch).
Heute sind diese Prozesse längst etabliert und werden praktisch täglich eingesetzt. Das bedeutet jedoch nicht, dass keine weiteren Verbesserungen möglich sind! Während des vergangenen Jahrzehnts wurden die Leica Laser Tracker kontinuierlich weiterentwickelt – mit teils spektakulären Ergebnissen. Einer der wichtigsten Fortschritte ist die Fähigkeit der Leica Laser Tracker zur Messung in allen sechs Freiheitsgraden (6DoF). Diese Fähigkeit ermöglicht es Roboterherstellern zum einen, den Endeffektor des Roboters in einem kürzeren Kalibrierzyklus zu kompensieren, der weniger Positionen erfordert. Zum anderen eröffnen sich dadurch aber auch völlig neue Möglichkeiten. In der Vergangenheit mussten bei der Verwendung eines herkömmlichen dreidimensionalen Laser Trackers zur Berechnung des Werkzeugarbeitspunkts (TCP) im 6D-Raum mehrere Positionen gemessen werden. Durch den Einsatz des Laser Tracker AT901 mit sechs Freiheitsgraden ist nun die exakte Position des Endeffektors im 6D-Raum in Echtzeit bekannt. Die logische Konsequenz dieser Innovation ist der völlige Verzicht auf die Roboterkalibrierung, da der Laser Tracker die Position des Endeffektors jederzeit in Echtzeit überwachen und korrigieren kann, sodass Thermoeffekte und anderweitige Veränderungen der Einzelteile des Roboters überhaupt nicht mehr von Interesse sind.
Diese moderne Technologie wurde beispielsweise von Premium Aerotec, in der deutschen Stadt Nordenham, zur Automatisierung der Montage von Stringern im Rumpf des Airbus A350 XWB genutzt. Da die Länge der Stringer bis zu 18 Meter betrug, reichte die spezifizierte Absolutgenauigkeit der verwendeten Roboter zur korrekten Positionierung nicht aus. Dem Team gelang es jedoch, die strengen Genauigkeitsanforderungen durch Echtzeitkorrekturen der Roboter auf der Grundlage von Messungen mit dem Leica Absolute Tracker mit sechs Freiheitsgraden zu erfüllen.
Automatisierte Fertigungszellen auf der Basis von Robotern und mobilen Messsystemen sind nicht mehr länger Zukunftsmusik, sondern verzeichnen überall auf der Welt ein eindrucksvolles Wachstum. Hexagon Manufacturing Intelligence hat weltweit bereits mehr als 60 solcher automatisierten Fertigungszellen umgesetzt. Die dabei gesammelten Erfahrungen versetzen Fertigungsbetriebe und Branchen in die Lage, ihre Prozesse in einem neuen Licht zu betrachten und kritisch zu prüfen, wodurch präzise Messungen und die Automatisierung von Inspektionsvorgängen Mehrwerte erzielt werden können. So werden wir Zeugen eines spannenden Paradigmenwechsels, der sich direkt vor unseren Augen vollzieht.
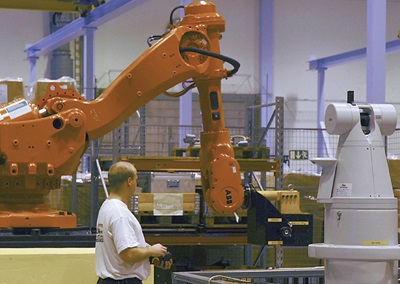
Auch oder gerade für diejenigen unter uns, die nicht täglich mit Robotern zu tun haben, gehen diese zuverlässigen, fleißigen Gesellen stillschweigend im Hintergrund ihrer Arbeit nach. Sie haben beim Bau des Autos geholfen, das Sie fahren, waren an der Erzeugung des Mobiltelefons beteiligt, das Sie immer bei sich tragen, und haben den Computer hergestellt, den Sie täglich verwenden. Es ist praktisch unmöglich, einen Tag lang in unserer modernen Gesellschaft zu leben, ohne in Kontakt mit einem von einer dieser vielseitigen Maschinen hergestellten Produkt zu kommen. Angesichts der Tatsache, dass ein solcher Automatisierungsgrad in der Fertigung noch bis vor kurzer Zeit als vollkommen illusorisch galt, ist der weltweite Siegeszug des Industrieroboters geradezu verblüffend. Infolge ihrer zunehmenden Genauigkeit und Intelligenz können Roboter immer mehr Aufgaben übernehmen, sodass sich ihr Einsatzbereich auf neue Branchen und Anwendungen ausweitet.
Schon seit den frühesten Anfängen dieser elektromechanischen Helferlein in der Fertigungsautomatisierung besteht der dringende Wunsch nach höherer Präzision. In den 1970er und 1980er Jahren wurden Roboter auf breiter Basis in der Automobilindustrie eingesetzt, während sie im Flugzeugbau nur selten anzutreffen waren, da ihre Genauigkeit für solche Anwendungen einfach noch nicht ausreichte. In den späten 1980ern und frühen 1990ern begannen die Roboterhersteller, Lösungen für dieses Problem zu finden.
Industrieroboter weisen naturgemäß eine hohe Wiederhol- aber eine geringe absolute Genauigkeit auf. Ist im Programm hinterlegt, dass sich der Endeffektor eines Roboters 30 Zentimeter in Y-Richtung bewegen soll, kann es sein, dass er sich stattdessen 30,5 Zentimeter in Y-Richtung bewegt. Ist dies der Fall, bewegt er sich dann allerdings auch zuverlässig jedes Mal 30,5 Zentimeter in Y-Richtung. Aufgrund dieser Wiederholbarkeit ließ sich die Ungenauigkeit der Roboter kompensieren, um ein gewisses Maß an absoluter Genauigkeit zu erzielen. Durch die exakte Vermessung des Roboters in unterschiedlichen Stellungen konnten anhand der Gliedlängen, Torsionswinkel, Nullpositionen der Gelenke, Versatzwerte der Glieder und Steifigkeitsparameter spezifische Korrekturen für das Robotermodell berechnet werden.
Die Hauptschwierigkeit dabei war die Vermessung des Roboters in allen Stellungen innerhalb unterschiedlicher Temperaturbereiche, um aus den Messdaten ein möglichst zuverlässiges Modell zu generieren. Zu dieser Zeit war das Laserinterferometer das Hilfsmittel der Wahl, wenn es um die präzise Distanz- und sogar Winkelmessung ging. Das Problem bei Laserinterferometern bestand jedoch darin, dass sie einer exakten Führung mit einem Retroreflektor bedurften, um Unterbrechungen des Laserstrahls zu vermeiden. Während der Bewegung des Reflektors in Abstimmung mit dem Laserstrahl werden die Bewegungsrichtung und die Anzahl der Wellenberge erfasst. Auf dieser Basis lässt sich die exakte Änderung der Distanz durch Multiplikation mit der halben Wellenlänge des Lasers berechnen. Wird der Zählvorgang jedoch zu irgendeinem Zeitpunkt gestört (z. B. durch eine Strahlunterbrechung), muss der gesamte Prozess ausgehend von der exakten ursprünglichen Reflektorposition neu begonnen werden. Allein aus diesem Grund setzten sich Laserinterferometer für die Roboterkompensation nie wirklich durch. Mit anderen frühen Lösungen wie Lasertriangulation und optischen Potenziometern wurde experimentiert, doch keine bot die erforderliche Benutzerfreundlichkeit und Genauigkeit.
In den frühen 1980er Jahren taten sich einige Einrichtungen zusammen, um die Probleme des Laserinterferometers bei der präzisen Strahlverfolgung durch verschiedene sogenannte Trackingsysteme zu lösen. Fachleute des damaligen National Bureau of Standards (NBS) – des heutigen NIST –, der University of Surrey in England und der FhG Karlsruhe arbeiteten gemeinsam an Projekten zur Integration von Laserinterferometer und Trackingsystem. Ziel war es, ein Interferometer zu entwickeln, das zur selbständigen Verfolgung eines Lasers in der Lage war. Gegen Ende dieses Jahrzehnts begannen Unternehmen in den USA und Europa mit der Konzeption eines Laser Trackers für industrielle Messanwendungen, wobei dieses System außerhalb des Messlabors in einer Fertigungsumgebung einsetzbar sein sollte. Das Ergebnis war der Leica Geosystems Smart 310 Laser Tracker, der der Fachwelt auf der Branchenmesse „Quality“ 1990 in Chicago vorgestellt wurde.
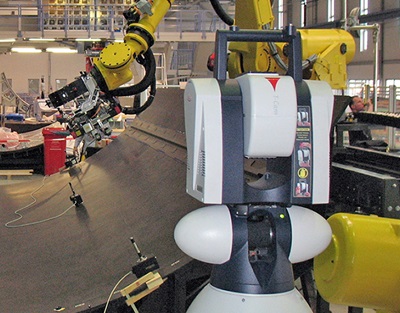
Damals boten die meisten großen Roboterhersteller auf diese Art kompensierte Roboter an. Allerdings ging jeder Hersteller dabei unterschiedlich vor, und Kunden mit Robotern unterschiedlicher Hersteller hatten keinerlei Möglichkeit zur Vereinheitlichung von Kalibriervorgängen und -plattformen. Deshalb brachten einige Unternehmen Softwarepakete zur Roboterkalibrierung auf den Markt. Mithilfe dieser Softwaremodule ließen sich Roboter aller Hersteller sowohl extrinsisch (innerhalb des Arbeitsbereichs) als auch intrinsisch (Gliedlängen, Torsionswinkel usw.) kalibrieren. Ein Beispiel für eine solche Software ist das von New River Kinematics entwickelte Modul SA Machine. Es diente außerdem zur Kompensation von Temperaturveränderungen des Roboters.
Beispielsweise dehnt sich ein Roboter, der sich zuvor im Ruhemodus befand, bei der Verwendung infolge der thermischen Expansion seiner Glieder physikalisch aus. Diese Größenänderung während des Aufwärmens des Roboters kann 0,5 Millimeter und mehr betragen, was sich erheblich auf die Wiederholbarkeit der Messungen auswirken kann. Die Kalibriersoftware kann diese Thermoeffekte jedoch berechnen und die Messwerte entsprechend bereinigen, um so eine hohe Wiederholgenauigkeit zu erzielen (0,10 Millimeter 6 Sigma typisch).
Heute sind diese Prozesse längst etabliert und werden praktisch täglich eingesetzt. Das bedeutet jedoch nicht, dass keine weiteren Verbesserungen möglich sind! Während des vergangenen Jahrzehnts wurden die Leica Laser Tracker kontinuierlich weiterentwickelt – mit teils spektakulären Ergebnissen. Einer der wichtigsten Fortschritte ist die Fähigkeit der Leica Laser Tracker zur Messung in allen sechs Freiheitsgraden (6DoF). Diese Fähigkeit ermöglicht es Roboterherstellern zum einen, den Endeffektor des Roboters in einem kürzeren Kalibrierzyklus zu kompensieren, der weniger Positionen erfordert. Zum anderen eröffnen sich dadurch aber auch völlig neue Möglichkeiten. In der Vergangenheit mussten bei der Verwendung eines herkömmlichen dreidimensionalen Laser Trackers zur Berechnung des Werkzeugarbeitspunkts (TCP) im 6D-Raum mehrere Positionen gemessen werden. Durch den Einsatz des Laser Tracker AT901 mit sechs Freiheitsgraden ist nun die exakte Position des Endeffektors im 6D-Raum in Echtzeit bekannt. Die logische Konsequenz dieser Innovation ist der völlige Verzicht auf die Roboterkalibrierung, da der Laser Tracker die Position des Endeffektors jederzeit in Echtzeit überwachen und korrigieren kann, sodass Thermoeffekte und anderweitige Veränderungen der Einzelteile des Roboters überhaupt nicht mehr von Interesse sind.
Diese moderne Technologie wurde beispielsweise von Premium Aerotec, in der deutschen Stadt Nordenham, zur Automatisierung der Montage von Stringern im Rumpf des Airbus A350 XWB genutzt. Da die Länge der Stringer bis zu 18 Meter betrug, reichte die spezifizierte Absolutgenauigkeit der verwendeten Roboter zur korrekten Positionierung nicht aus. Dem Team gelang es jedoch, die strengen Genauigkeitsanforderungen durch Echtzeitkorrekturen der Roboter auf der Grundlage von Messungen mit dem Leica Absolute Tracker mit sechs Freiheitsgraden zu erfüllen.
Automatisierte Fertigungszellen auf der Basis von Robotern und mobilen Messsystemen sind nicht mehr länger Zukunftsmusik, sondern verzeichnen überall auf der Welt ein eindrucksvolles Wachstum. Hexagon Manufacturing Intelligence hat weltweit bereits mehr als 60 solcher automatisierten Fertigungszellen umgesetzt. Die dabei gesammelten Erfahrungen versetzen Fertigungsbetriebe und Branchen in die Lage, ihre Prozesse in einem neuen Licht zu betrachten und kritisch zu prüfen, wodurch präzise Messungen und die Automatisierung von Inspektionsvorgängen Mehrwerte erzielt werden können. So werden wir Zeugen eines spannenden Paradigmenwechsels, der sich direkt vor unseren Augen vollzieht.