La forma es lo importante
Hansa-Flex Hydraulic Solutions - Países Bajos
Contacto

Cuando un experto mundial en hidráulica requirió trasladar la producción de tubos a un sitio nuevo, el sistema de inspección de tubos de Hexagon fue parte fundamental para la solución perfecta.
Hansa-Flex es un experto mundial en hidráulica con filiales en todo el mundo. La empresa holandesa Hansa-Flex Hydraulic Solutions, opera en Deventer, y ofrece a sus clientes soluciones completas de tecnología de fluidos que abarcan desde la asesoría inicial hasta la producción e instalación de unidades completas de energía hidráulica.
Además de una amplia experiencia en diversas áreas técnicas como hidráulica, eléctrica y mecánica, HansaFlex tiene una extensa red de empresas asociadas con la capacidad de satisfacer una variada gama de requerimientos de los usuarios. Según Erik-Jan Klomps, Director técnico de Hansa-Flex Nederland BV, este enfoque, que permite tener un
solo punto de contacto para cada proyecto, es muy importante para los clientes finales.
Como parte de su actividad económica principal, Hansa-Flex Nederland BV debe proporcionar a sus clientes una gran variedad de tubos de miles de modelos diferentes. Entre las principales necesidades de los clientes de Hansa-Flex se encuentran una respuesta y plazo de entrega rápidos.
Anteriormente, estos tubos se fabricaban y revisaban en una fábrica de Hansa-Flex en Alemania, pero debido a que ha crecido el número de clientes que requieren tubos terminados en uno o dos días, en 2015 Hansa-Flex Nederland BV tomó la decisión de invertir en su propia máquina CNC de flexión de tubos para fabricarlos ellos mismos.
"La adaptabilidad de la solución de medición es vital para poder resolver las peticiones individuales de nuestros clientes."
Sin embargo, esta nueva operación de producción de tubos requería encontrar una forma de revisar los tubos terminados antes de entregarlos. Con el sistema de inspección de tubos de Hexagon Manufacturing Intelligence – un ROMER Absolute Arm asociado con palpadores especiales para tubos y el software TubeShaper – Hansa-Flex no solo pudo revisar sus rutinas de producción de tubos, sino también ampliar su servicio, ofreciendo ingeniería inversa de tubos y también mediciones in situ para sus clientes.
“Diversas características del ROMER Absolute Arm y del software TubeShaper hicieron que la selección fuera sencilla gracias a su portabilidad, el hardware plug-andplay,
el reconocimiento automático y repetible del palpador, los palpadores de tubo de fácil uso y la interfaz de flexión direct-CNC satisfacen todas nuestras necesidades”, comentó Klomps.
El feed-back de otros clientes de Hexagon también influyó en el proceso de evaluación de Hansa-Flex al buscar la mejor solución para la inspección de tubos.
“Nos pusimos en contacto con otros usuarios de ROMER Absolute Arm y de TubeShaper como referencia,” agregó Klomps. “El feed-back de los usuarios de Hexagon fue muy positivo, lo cual fue un punto determinante para nosotros.”“Los requerimientos individuales del usuario hacen que una solución de medición adaptable sea muy importante” explicó Klomps. Recientemente un usuario requería un tubo que se ajustara con precisión entre dos rebordes, con tolerancias críticas en cada extremo. Al usar el sistema de inspección de tubos, Hansa-Flex pudo digitalizar fácilmente los detalles de los rebordes y crear una nueva geometría de tubos que se ajuste a sus límites dimensionales.
Anteriormente este tipo de tareas generaba una cantidad considerable de desperdicio, ya que el tubo se fabricaba y se ajustaba hasta 20 veces antes de lograr un ajuste aceptable.
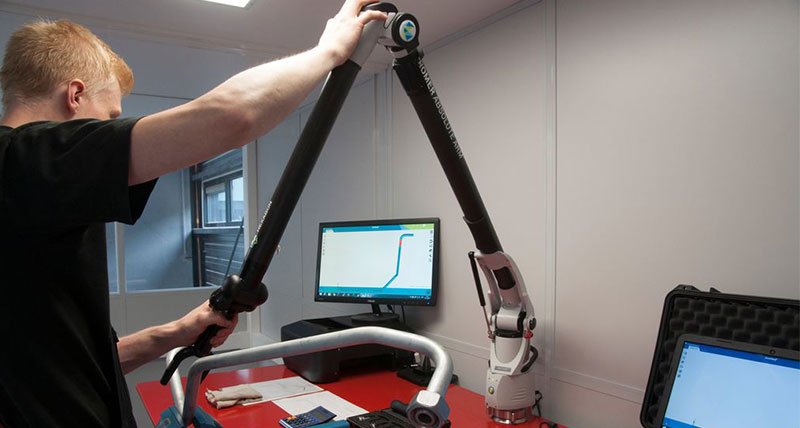
Las posibilidades del ROMER Absolute Arm y de TubeShaper no han pasado desapercibidas por Klomp y su equipo de trabajo en Deventer, y tienen planes para ir todavía más allá para aprovechar al máximo la tecnología. “Estamos a punto de incorporar la interfaz entre TubeShaper y la máquina de flexión. Esto ahorrará aún más tiempo y reducirá los errores humanos provocados por la entrada de datos incorrectos de flexión en la computadora”.