Pleine poussée grâce aux mesures sur machines-outils
Contact

L’usine suisse de l’entreprise RUAG à Emmen s’est spécialisé en fabrication des pièces complexes en aluminium pour l’aéronautique, le spatial et les appareils de défense.
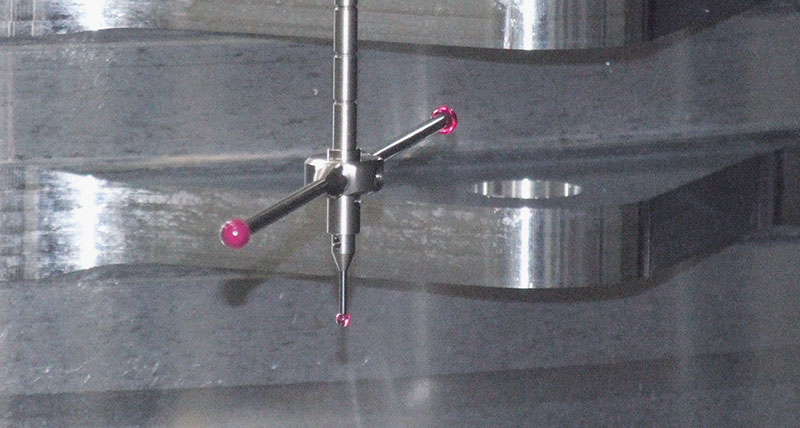
“Initialement, nous ne pouvions pas mesurer les pièces dans la machine à mesurer. En conséquence, mesurer sur la machine avec le 3D Form Inspect de m&h était la seule méthode praticable,” dit Markus Graber. Le fraisage et le tournage sont faits sur deux centres d’usinage DMG avec palettiseur. Les machines sont dotées des commandes Siemens 840D pour l’usinage en 5 axes. Les deux machines disposent d’un petit récepteur infrarouge m&h dans la tête de broche qui transmet les signaux des palpeurs de mesure m&h à la commande. Les palpages sont programmés par le logiciel 3D Form Inspect de m&h.
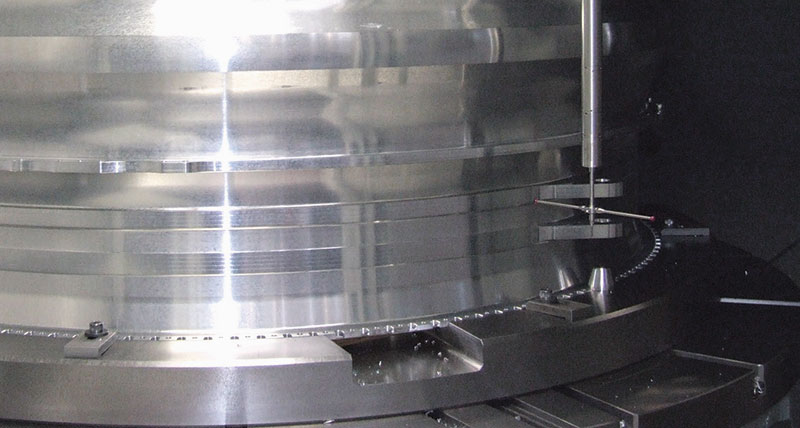
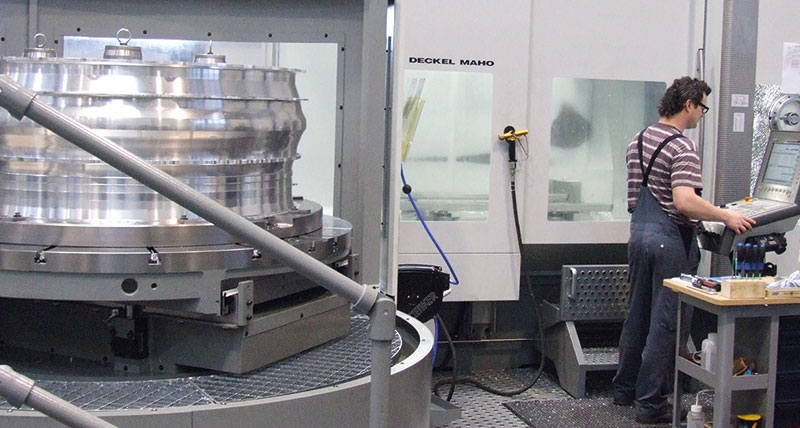
Le signal de palpage du système de mesure est transmis à l’intérieur des rallonges de module à module et ensuite transféré par les diodes infrarouges du palpeur. Le logiciel 3D Form Inspect de m&h prend en considération les types différents des palpeurs. Avec un simple clic de souris sur la représentation de la pièce sur l’écran, les endroits à mesurer sont définis et la fonction de mesure souhaitée y est attribuée. Les tâches de mesure sont attribuées aux palpeurs de mesure correspondants dont les caractéristiques comme la dimension sont sauvegardées par le logiciel. Le logiciel calcule tout le reste et génère automatiquement le programme de mesure pour la machine, y compris le calibrage des palpeurs utilisés.
Toutes les courses sont automatiquement déterminées et, en même temps, un contrôle de collision avec les contours des pièces est effectué. Une simulation de la mesure sur l’écran garantit un maniement sécurisé. C’est une tâche importante qui allège considérablement la vérification quand, comme ici, on mesure plus de 1.000 dimensions en faisant jusqu’à 4 palpages sur chacune. Une erreur détectée plus tard sur la machine à mesurer serait fatale – cette pièce coûteuse serait rebutée. “Avec, nous n’avons aucune chance de remettre cette pièce dans sa position initiale, si nous détectons une erreur sur la machine à mesurer,” explique Markus Graber. Le logiciel 3D Form Inspect compare les données du dessin CAO avec les valeurs mesurées sur la machine. Les opérateurs machine peuvent mesurer à tout moment et améliorent la fiabilité de leur tâche. Ils peuvent consigner la pièce à tout moment et, en procédant ainsi, réagir alors que la pièce est encore immobilisée dans la machine.
"Cela économise du temps et permet d’arriver à une précision considérablement plus élevée."
Les résultats de mesure obtenus sur la machine-outil sont comparables à ceux obtenus sur la machine à mesurer, la stratégie de calibrage brevetée de m&h étant décisive. C’est particulièrement important pour des palpeurs longs, parce que les petites déviations dans le cône porte-outil dans la broche de la machine génèrent de grands décalages de la bille du stylet au bout des palpeurs rallongés. Le logiciel génère automatiquement les cycles de calibrage pour chaque palpeur de sorte que ces déviations sont automatiquement compensées. Cela s’applique également aux 4ème et 5ème axes des machines. Les erreurs pivots des axes sont saisies pendant le calibrage et automatiquement compensées.
Les nombreuses fonctions de mesure et les différents fonctions de commande selon la machine rendent le logiciel 3D Form Inspect non seulement un investissement orienté vers l’avenir, mais aussi un outil indispensable dans chaque atelier moderne. S’y ajoute le support technique des ingénieurs d’application de m&h qui assistent les clients par tous les moyens, y compris par une visite sur site.
Les installations et les formations sont toujours effectuées en utilisant la pièce réelle dans les ateliers des utilisateurs “Tout cela était une aventure en terrain inconnu pour nous, et nous l’avons abordée avec une attitude sceptique,” rapporte Markus Graber. “La manutention est simple, le système lui-même est simple.” Ce n’est pas peu dire compte tenu de l’exigence de plus de 1000 palpages divers et variés sur une seule pièce.”