Voller Schub dank Messen an Werkzeugmaschinen
Kontakt

Das Messen von Werkstücken noch in der Aufspannung auf der Maschine ist mittlerweile auch Stand der Technik in der Serienfertigung. Die Firma RUAG stellt große Bläserringe von Jet-Triebwerken mithilfe von 3D Form Inspect und Messtastern von m&h her.
Das Schweizer Werk Emmen der Firma RUAG hat sich auf die Fertigung von komplexen Teilen aus Aluminium spezialisiert, die in der Luft- und Raumfahrt, sowie in Verteidigungsgeräten zum Einsatz kommen.
“Wir konzentrieren uns darauf, kritische Teile hoher Komplexität mit möglichst hoher Wirtschaftlichkeit und Prozesssicherheit zu fertigen.” schildert Markus Graber, Teamleader Machining bei RUAG. Hier fertigt man auch das große Bläsergehäuse für das Jet-Triebwerk CF34-10E von General Electric mit Abmessungen von etwa 1500 mm Durchmesser und einer Höhe von ca. 600 mm.
“Anfangs konnten wir die Teile gar nicht auf der Mess- maschine messen. Da war das Messen auf der Maschine mit 3D Form Inspect von m&h der einzig gangbare Weg,” sagt Markus Graber. Auf zwei DMG-Bearbeitungszentren vom Typ DMC 200 FD mit Palettenwechslern wird gefräst und gedreht. Die Maschinen verfügen über Siemens 840D Steuerungen für eine effektive 5-Achsbearbeitung. Beide Maschinen tragen im Spindelkopf einen kleinen Infrarotempfänger von m&h, der die Signale der m&h Messtastern an die Steuerung weitergibt. Programmiert werden die Antastungen über die Software 3D Form Inspect von m&h.
Rückwärtige Einstiche und Nuten, tief im Werkstück liegende Konturen, unterschiedlichste Geometrien sowie 2-fach gekrümmte, nach innen fallende Flächen erfordern nicht nur das Messen mit allen 5 Achsen, sondern eben auch verschiedene Tasterlängen und Durchmesser von Tastkugeln, um alle Geometrien überhaupt zu erreichen und messen zu können. Deshalb verwendet RUAG modulare Messtaster vom Typ 25.41-HDR von m&h in 4 verschiedenen Längen und mit verschiedenen Taststiften und Kugeldurchmessern. Diese Taster sind mit Standardverlängerungen versehen, die in den Tasterkörper eingeschraubt werden.
Diese Standardmodule mit einem Durchmesser von nur 25 mm können nahezu beliebig aufeinander gesetzt werden. Am Ende dieser Verlängerungen, also möglichst nahe an der zu messenden
Stelle, wird das m&h-Messwerk aufgesetzt. So erreicht man bestes Antastverhalten und höchste Genauigkeit. RUAG misst mit Tastern bis 500 mm Länge und mit verschiedenen Tastkreuzen. Das Antastsignal des Messwerkes wird im Inneren der Verlängerungsmodule von Modul zu Modul weitergegeben und dann mit den Infrarotdioden im Tasterkörper gesendet.
Die Software 3D Form Inspect von m&h berücksichtigt die unterschiedlichen Ausführungen aller Messtaster. Mit einfachem Mausklick am Bildschirm mit der Werkstückdarstellung werden die zu messenden Punkte festgelegt und mit der gewünschten Messfunktion versehen. Die Messaufgaben werden wiederum den jeweiligen Messtastern zugeordnet, die mit ihren Dimensionen in der Software hinterlegt sind. Alles weitere rechnet die Software und generiert selbstständig das Messprogramm für die Maschine inklusive Kalibrierung der verwendeten Taster. Alle Verfahrwege werden automatisch ermittelt und gleichzeitig eine Kollisionskontrolle mit den Teilekonturen durchgeführt.
Die Software 3D Form Inspect vergleicht die Daten der CAD-Zeichnung mit den auf der Maschine gemessenen Werten. Die Maschinenbediener können jederzeit messen und gewinnen Sicherheit über ihr Tun. Das Werkstück kann jederzeit protokolliert werden. So kann noch in der Aufspannung reagiert werden. Das spart Zeit und bringt deutlich höhere Genauigkeiten.
Die auf der Werkzeugmaschine erzielten Messergebnisse sind denen von der Messmaschine vergleichbar. Ausschlaggebend dafür ist die ausgeklügelte Kalibrierungsstrategie von m&h, die zum Patent angemeldet wurde. Besonders wichtig ist dies bei den langen Tastern, da hier kleine Fehlweisungen im Aufnahmekonus der Maschinenspindel schon große Fehlstellungen der Tastkugel an den verlängerten Tastern bedeuten. Die Software generiert selbständig die Kalibrierzyklen für jeden Taster, sodass diese Fehlweisungen automatisch kompensiert werden. Das gleiche gilt für die 4. und 5. Achse der Maschinen. Die Schwenkfehler der Achsen werden mit der Kalibrierung erfasst und automatisch kompensiert.
Die vielen Messfunktionen und die problemlose Funktion mit vielen Steuerungstypen auf unterschiedlichsten Maschinen machen die Software 3D Form Inspect nicht nur zu einer zukunftssicheren Investition, sondern auch zu einem unentbehrlichen Werkzeug in jeder modernen Werkstatt. Hinzu kommt die unmittelbare Unterstützung durch die Applikationsingenieure von m&h, die den Kunden mit Rat und Tat zur Seite stehen und auch vor Ort kommen. Installationen und Einweisungen erfolgen immer am realen Werkstück in den Werkstätten der Anwender. “Das alles ist auch Neuland für uns und wir sind dem Ganzen entsprechend skeptisch be- gegnet,” berichtet Markus Graber. “Die Anwendung ist einfach, das System selbst ist einfach.” Das will etwas heißen bei den vielfältigen Anforderungen mit über 1000 Antastungen an einem Werkstück.
Das Schweizer Werk Emmen der Firma RUAG hat sich auf die Fertigung von komplexen Teilen aus Aluminium spezialisiert, die in der Luft- und Raumfahrt, sowie in Verteidigungsgeräten zum Einsatz kommen.
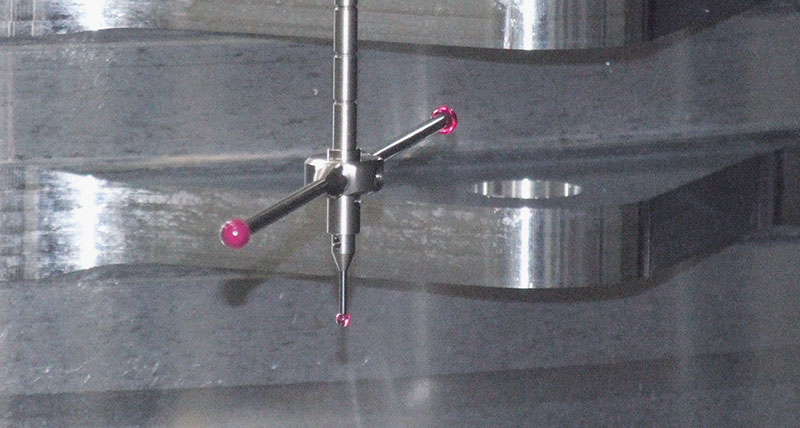
“Anfangs konnten wir die Teile gar nicht auf der Mess- maschine messen. Da war das Messen auf der Maschine mit 3D Form Inspect von m&h der einzig gangbare Weg,” sagt Markus Graber. Auf zwei DMG-Bearbeitungszentren vom Typ DMC 200 FD mit Palettenwechslern wird gefräst und gedreht. Die Maschinen verfügen über Siemens 840D Steuerungen für eine effektive 5-Achsbearbeitung. Beide Maschinen tragen im Spindelkopf einen kleinen Infrarotempfänger von m&h, der die Signale der m&h Messtastern an die Steuerung weitergibt. Programmiert werden die Antastungen über die Software 3D Form Inspect von m&h.
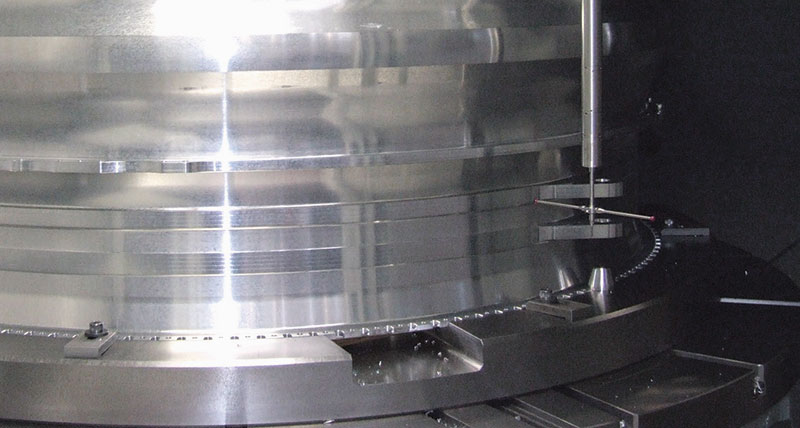
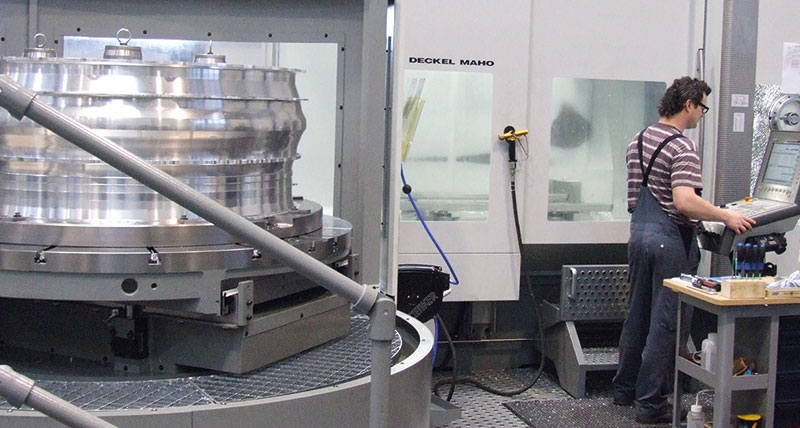
Die Software 3D Form Inspect von m&h berücksichtigt die unterschiedlichen Ausführungen aller Messtaster. Mit einfachem Mausklick am Bildschirm mit der Werkstückdarstellung werden die zu messenden Punkte festgelegt und mit der gewünschten Messfunktion versehen. Die Messaufgaben werden wiederum den jeweiligen Messtastern zugeordnet, die mit ihren Dimensionen in der Software hinterlegt sind. Alles weitere rechnet die Software und generiert selbstständig das Messprogramm für die Maschine inklusive Kalibrierung der verwendeten Taster. Alle Verfahrwege werden automatisch ermittelt und gleichzeitig eine Kollisionskontrolle mit den Teilekonturen durchgeführt.
"Es gibt einfach viel mehr Sicherheit in der Produktion, und es macht sich bezahlt."
Eine Bildschirmsimulation des Messens garantiert höchste Bediensicherheit. Ein wichtiger Aspekt und eine große Erleichterung, vor allem wenn mehr als 1.000 Dimensionen mit bis zu 4 Antastungen geprüft werden müssen. Ein später auf der Messmaschine gefundener Fehler wäre fatal und würde ein teures Werkstück zum Ausschuss machen. “Bei diesem Werkstück haben wir keine Chance das Teil jemals wieder in die Ausgangslage zu bringen, wenn wir auf der Messmaschine einen Fehler entdecken,” erklärt Markus Graber.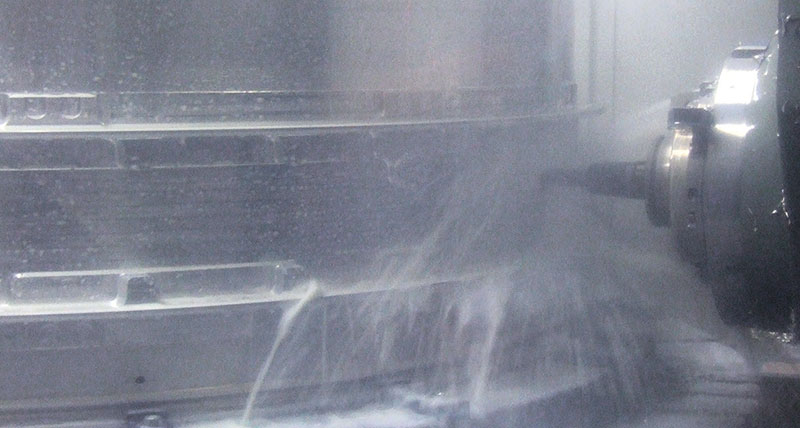
Die auf der Werkzeugmaschine erzielten Messergebnisse sind denen von der Messmaschine vergleichbar. Ausschlaggebend dafür ist die ausgeklügelte Kalibrierungsstrategie von m&h, die zum Patent angemeldet wurde. Besonders wichtig ist dies bei den langen Tastern, da hier kleine Fehlweisungen im Aufnahmekonus der Maschinenspindel schon große Fehlstellungen der Tastkugel an den verlängerten Tastern bedeuten. Die Software generiert selbständig die Kalibrierzyklen für jeden Taster, sodass diese Fehlweisungen automatisch kompensiert werden. Das gleiche gilt für die 4. und 5. Achse der Maschinen. Die Schwenkfehler der Achsen werden mit der Kalibrierung erfasst und automatisch kompensiert.
Die vielen Messfunktionen und die problemlose Funktion mit vielen Steuerungstypen auf unterschiedlichsten Maschinen machen die Software 3D Form Inspect nicht nur zu einer zukunftssicheren Investition, sondern auch zu einem unentbehrlichen Werkzeug in jeder modernen Werkstatt. Hinzu kommt die unmittelbare Unterstützung durch die Applikationsingenieure von m&h, die den Kunden mit Rat und Tat zur Seite stehen und auch vor Ort kommen. Installationen und Einweisungen erfolgen immer am realen Werkstück in den Werkstätten der Anwender. “Das alles ist auch Neuland für uns und wir sind dem Ganzen entsprechend skeptisch be- gegnet,” berichtet Markus Graber. “Die Anwendung ist einfach, das System selbst ist einfach.” Das will etwas heißen bei den vielfältigen Anforderungen mit über 1000 Antastungen an einem Werkstück.