Full Thrust grazie alla misurazione su macchine utensili
Contattateci

Oggi la misura dei pezzi mentre sono ancora staffati sulle macchine utensile sta diventando sempre più attuale nella produzione in serie. Alla ditta RUAG fabbricano grandi anelli per le ventole dei motori dei jet utilizzando tastatori ed il software 3D Form Inspect di m&h.
In una divisione della RUAG ci è stato permesso di dare un’occhiata alla fabbricazione degli anelli delle ventole a parete sottile per i motori dei jet e di ascoltare le loro esperienze con la verifica dei pezzi mentre sono ancora staffati sulla macchina utensile. Nello stabilimento di Emmen, situato nel cuore della Svizzera, circa 1.000 dipendenti sono specializzati nella lavorazione di parti complesse fatte di alluminio e delle sue leghe, essenzialmente per aeroplani e sistemi di difesa.
“La strategia di RUAG consiste nel fabbricare parti critiche di grande complessità con processi affidabili e la massina efficienza,” afferma Markus Graber, Capogruppo del Reparto Lavorazioni alla RUAG. RUAG Emmen costruisce alloggiamenti delle ventole per il motore jet CF34-10E della General Electric, utilizzato nella ultimissima generazione di aerei tipo Embraer 190 / 195, per esempio. Questi pezzi quasi cilindrici hanno diametri di circa 1500 mm ed un’altezza di circa 600 mm, ma le loro pareti sono sottili.
“Il problema principale era regolare il “run out” su una macchina di misura. All’inizio non potevamo misurare i pezzi su una macchina di misura a coordinate. La misura per mezzo del 3D Form Inspect di m&h mentre i componenti erano ancora staffati sulla macchina utensile era l’unico modo di fare il lavoro,” spiega Markus Graber. La lavorazione degli alloggiamenti delle ventola è eseguita su due centri di lavoro, tipo DMC 200 FD, con sistemi di cambio pallet. Comandate da un controllo Siemens 840D le macchine sono equipaggiate con tastatori m&h con trasmissione a infrarossi per mezzo di un piccolo ricevitore montato vicino al naso mandrino. Il software 3D Form Inspect di m&h veniva utilizzato su questo tipo di macchine utensili DMG per la prima volta ma la combinazione è stata vincente sin dall’inizio.
Oltre alla grande necessità di estrema precisione, gli alloggiamenti delle ventole presentano molte geometrie complesse e superfici curvate in due direzioni, rientranze e scanalature e fori nascosti che diventano successivamente punti di fissaggio per azionamenti ed altri dispositivi del motore. Per riuscire a verificarli, sono utilizzati 4 tastatori differenti con lunghezze diverse e diametri differenti delle sfere di contatto come pure alcuni con stili a croce. m&h ha inventato i tastatori modulari con estensioni standard disponibili nelle lunghezze di 30, 50, 100 e 200 mm.
I moduli sono fatti di acciaio inossidabile con un diametro di soli 25 mm e possono essere avvitati l’uno sull’altro fino a raggiungere un contatto stretto e rigido sulle flange e a portare il sistema di misura al massimo. Alla RUAG utilizzano tastatori con estensioni fino ad una lunghezza totale di 500 mm.
Molti test per paragonare le prestazioni hanno dimostrato che i risultati di misura sulle macchine utensili generati dai sistemi m&h differiscono di appena qualche micron da quelli ottenuti su una macchina di misura a coordinate e che sono assolutamente ripetibili. “I risultati di misura forniti dal 3D Form Inspect consentono la decisione di continuare o fermare la lavorazione dei pezzi in qualunque momento nel corso del processo”, conferma Markus Graber. “All’inizio la MMC non era ancora pronta. Tutto era stato realizzato sulla macchina utensile. Questo è stato possibile grazie all’ingegnosa strategia di calibrazione di m&h”. Tutte le variazioni termiche della macchina sono automaticamente rilevate e compensate. Grazie al fatto che il 3D Form Inspect rileva scostamenti sul 4° e 5°h asse, anche tutti gli errori di orientamento di quegli assi sono compensati automaticamente.
Semplicemente in produzione ci dà le certezze di cui abbiamo bisogno. E si ripaga in breve tempo, assolutamente.he è molto importante con questi tastatori lunghi. Altrimenti, utilizzando tastatori così lunghi, un leggero scostamento di alcuni micron al cono mandrino può causare una grossa differenza di alcuni decimi nel punto di contatto dei tastatori dando un risultato di misura sbagliato. Con dei semplici clic del Con il 25.41 di m&h si possono misurare anche punti ”impossibili” Con contatto trasversale e molteplici stili di contatto pronti per ogni sfida di misura in arrivo 3RUAG Aerospace, Emmen, Svizzera | m&h SISTEMI DI TASTATORI E SOFTWARE mouse sul modello della superficie sullo schermo del computer l’operatore può determinare i punti da verificare.
A tutti i punti egli può aggiungere funzioni di misura come altezze, angoli, diametro di cerchi e altre. Nei protocolli il software controllerà automaticamente i valori a fronte delle dimensioni desiderate. Dopo aver determinato il tastatore che dovrebbe essere usato per i contatti, il 3D form Inspect genera i programmi a parte comprendenti il controllo di collisione del tastatore con le superfici del pezzo. Questo facilita molto il lavoro degli operatori ed assicura non solo la più alta precisione ma anche un processo affidabile e sicuro senza interruzioni. Gli operatori acquisiscono certezze sul loro operato e controllano i processi in qualunque momento durante la fabbricazione.
Un errore di valutazione rovinerebbe un pezzo molto costoso. “Se troviamo un errore in seguito e la rilavorazione è necessaria, dobbiamo riorganizzarci in modo totalmente diverso,” spiega Markus Graber. “La rilavorazione immediata sulla macchina utensile è impossibile perché non ritroviamo mai il punto di zero e la forma del pezzo in modo esatto.” Misurando tra una fase e l’altra della lavorazione, sono possibili una reazione immediata e la ri-lavorazione, risparmiando molto tempo e denaro.
Oggi alla RUAG tutto ciò è una pratica largamente utilizzata e molto attuale. Naturalmente per RUAG queste tecniche erano nuove e dapprima tutti erano scettici. “Siamo entrati in un territorio sconosciuto con questo tema e naturalmente eravamo molto scettici”, riferisce Markus Graber “Ma la gestione è veramente semplice come pure il sistema. I nostri dipendenti hanno fatto amicizia con questo software facilmente e oggi sono molto motivati ad utilizzare questo strumento ”. Conoscendone la complessità, con oltre 1,000 dimensioni da verificarsi su un unico pezzo, questa è veramente una bella affermazione. ”
In una divisione della RUAG ci è stato permesso di dare un’occhiata alla fabbricazione degli anelli delle ventole a parete sottile per i motori dei jet e di ascoltare le loro esperienze con la verifica dei pezzi mentre sono ancora staffati sulla macchina utensile. Nello stabilimento di Emmen, situato nel cuore della Svizzera, circa 1.000 dipendenti sono specializzati nella lavorazione di parti complesse fatte di alluminio e delle sue leghe, essenzialmente per aeroplani e sistemi di difesa.
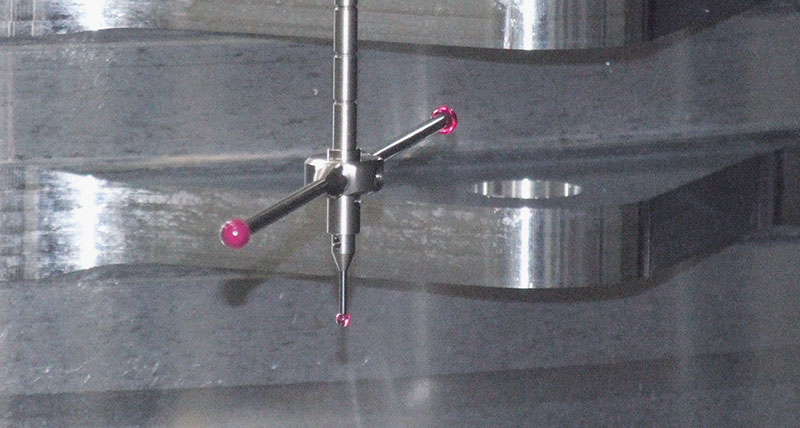
“Il problema principale era regolare il “run out” su una macchina di misura. All’inizio non potevamo misurare i pezzi su una macchina di misura a coordinate. La misura per mezzo del 3D Form Inspect di m&h mentre i componenti erano ancora staffati sulla macchina utensile era l’unico modo di fare il lavoro,” spiega Markus Graber. La lavorazione degli alloggiamenti delle ventola è eseguita su due centri di lavoro, tipo DMC 200 FD, con sistemi di cambio pallet. Comandate da un controllo Siemens 840D le macchine sono equipaggiate con tastatori m&h con trasmissione a infrarossi per mezzo di un piccolo ricevitore montato vicino al naso mandrino. Il software 3D Form Inspect di m&h veniva utilizzato su questo tipo di macchine utensili DMG per la prima volta ma la combinazione è stata vincente sin dall’inizio.
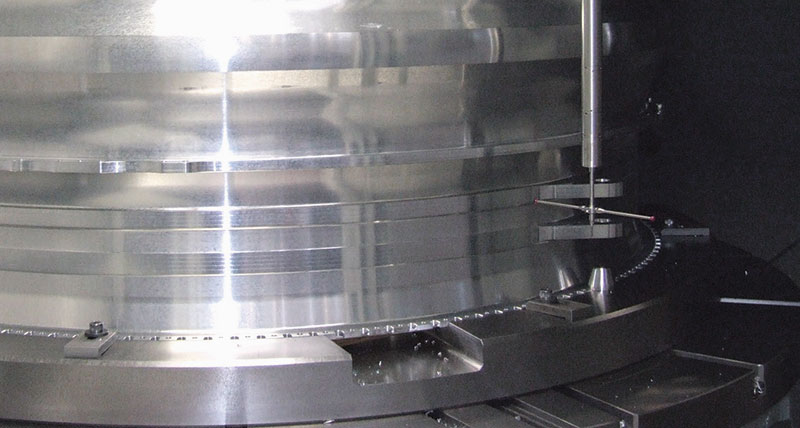
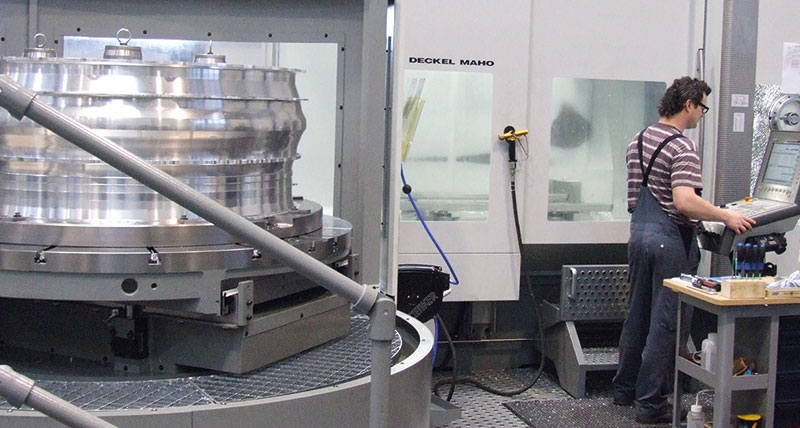
Molti test per paragonare le prestazioni hanno dimostrato che i risultati di misura sulle macchine utensili generati dai sistemi m&h differiscono di appena qualche micron da quelli ottenuti su una macchina di misura a coordinate e che sono assolutamente ripetibili. “I risultati di misura forniti dal 3D Form Inspect consentono la decisione di continuare o fermare la lavorazione dei pezzi in qualunque momento nel corso del processo”, conferma Markus Graber. “All’inizio la MMC non era ancora pronta. Tutto era stato realizzato sulla macchina utensile. Questo è stato possibile grazie all’ingegnosa strategia di calibrazione di m&h”. Tutte le variazioni termiche della macchina sono automaticamente rilevate e compensate. Grazie al fatto che il 3D Form Inspect rileva scostamenti sul 4° e 5°h asse, anche tutti gli errori di orientamento di quegli assi sono compensati automaticamente.
Semplicemente in produzione ci dà le certezze di cui abbiamo bisogno. E si ripaga in breve tempo, assolutamente.he è molto importante con questi tastatori lunghi. Altrimenti, utilizzando tastatori così lunghi, un leggero scostamento di alcuni micron al cono mandrino può causare una grossa differenza di alcuni decimi nel punto di contatto dei tastatori dando un risultato di misura sbagliato. Con dei semplici clic del Con il 25.41 di m&h si possono misurare anche punti ”impossibili” Con contatto trasversale e molteplici stili di contatto pronti per ogni sfida di misura in arrivo 3RUAG Aerospace, Emmen, Svizzera | m&h SISTEMI DI TASTATORI E SOFTWARE mouse sul modello della superficie sullo schermo del computer l’operatore può determinare i punti da verificare.
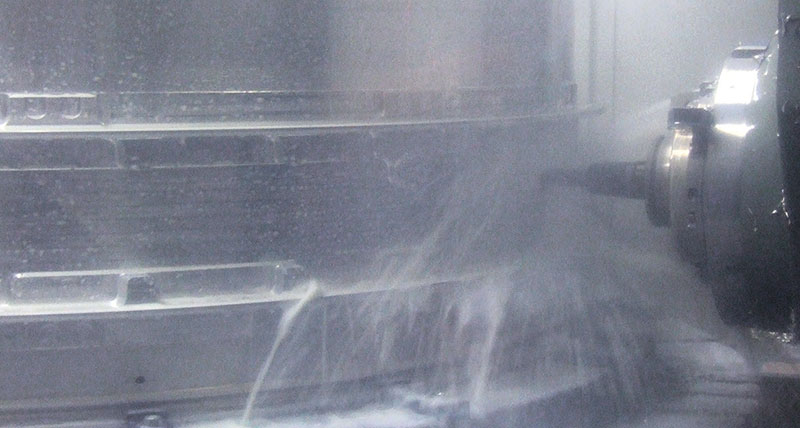
Un errore di valutazione rovinerebbe un pezzo molto costoso. “Se troviamo un errore in seguito e la rilavorazione è necessaria, dobbiamo riorganizzarci in modo totalmente diverso,” spiega Markus Graber. “La rilavorazione immediata sulla macchina utensile è impossibile perché non ritroviamo mai il punto di zero e la forma del pezzo in modo esatto.” Misurando tra una fase e l’altra della lavorazione, sono possibili una reazione immediata e la ri-lavorazione, risparmiando molto tempo e denaro.
Oggi alla RUAG tutto ciò è una pratica largamente utilizzata e molto attuale. Naturalmente per RUAG queste tecniche erano nuove e dapprima tutti erano scettici. “Siamo entrati in un territorio sconosciuto con questo tema e naturalmente eravamo molto scettici”, riferisce Markus Graber “Ma la gestione è veramente semplice come pure il sistema. I nostri dipendenti hanno fatto amicizia con questo software facilmente e oggi sono molto motivati ad utilizzare questo strumento ”. Conoscendone la complessità, con oltre 1,000 dimensioni da verificarsi su un unico pezzo, questa è veramente una bella affermazione. ”