Qualitätsgewinne einfahren
Qualitäts- und Produktivitätssteigerung dank quasi-automatischer High-Speed-Rohrvermessung
Kontakt

Von Beginn der über hundertjährigen Firmengeschichte an war die Entwicklungsstrategie des Erntemaschinenherstellers CLAAS auf Innovation ausgerichtet.
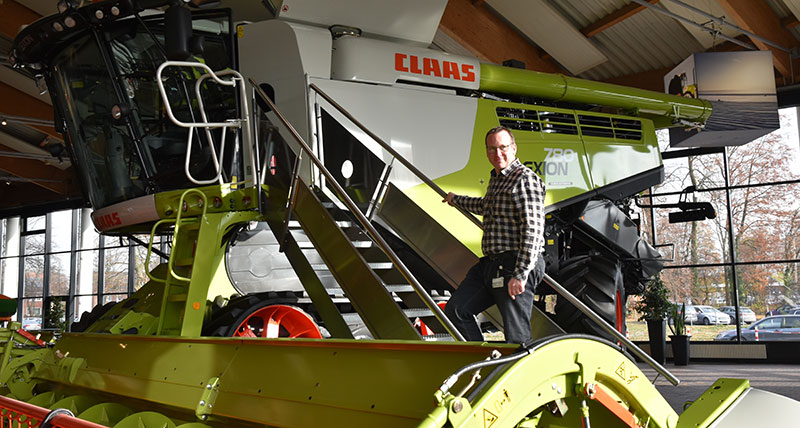
Heute beschäftigt CLAAS an seinen Produktionsstandorten weltweit über 11.000 Mitarbeiter. Der Stammsitz in Harsewinkel, Deutschland produziert auch heute noch und stellt auf über 400.000 Quadratmetern Mähdrescher, Feldhäcksler und allradgetriebene Großtraktoren her. Das Werk in Harsewinkel umfasst vier Produktionslinien: auf einer werden die Großmähdrescher-Serien LEXION 780-740 und 670-620 hergestellt, auf einer zweiten die Mähdrescher- Reihen TUCANO 570-320, AVERO 240/160 und DOMINATOR 40. Auf den beiden verbleibenden Montagelinien entstehen die Feldhäcksler-Serien JAGUAR 980-930 und 870-840 sowie die allradgetriebenen Großtraktoren XERION 5000-4000 mit einer Motorleistung von bis zu 530 PS.
Die hochauflösenden Digitalkameras messen unsere Rohrgeometrien innerhalb weniger Sekunden hochgenau. Die CLAAS-Erntemaschinen bestehen aus über 50.000 einzelnen Bauteilen, von denen alle die Unternehmensstandards für Qualität und Widerstandsfähigkeit erfüllen müssen.
Einen großen Teil dieser Bauteile machen unterschiedliche Rohre und Geländer aus. Früher wurden alle Geländer- und Hydraulikrohre mit Biegelehren oder -schablonen vermessen. In der Regel geschah dies mithilfe eines entsprechenden Blechmusters, an das die Rohre angelegt wurden.
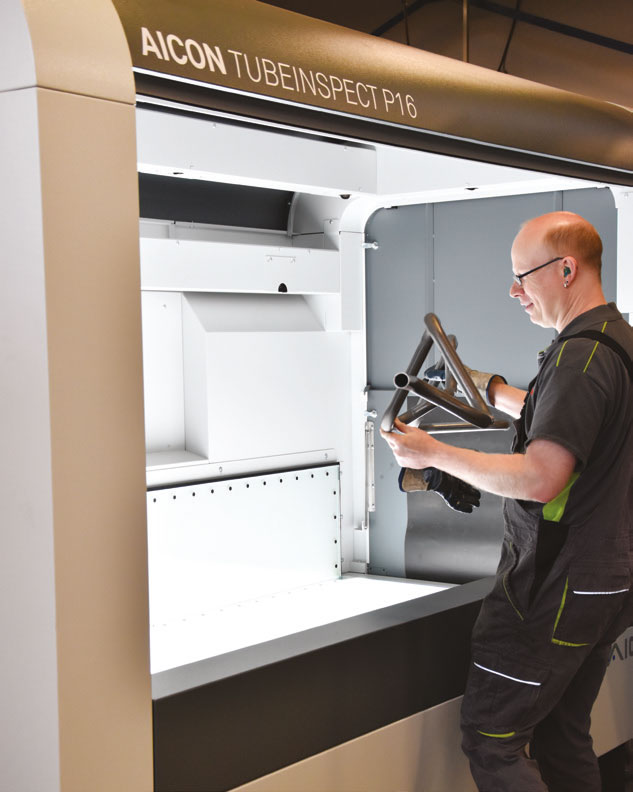
Modernisierter Fertigungsprozess
2007, während der Entwicklung neuer Produkte und angetrieben von dem Wunsch, seine Prozesse und die Produktionsgeschwindigkeit zu verbessern, begab sich CLAAS auf die Suche nach einem neuen hochmodernen Messsystem. Das Unternehmen zog sowohl ein handgeführtes Messgerät als auch die optische Messzelle AICON TubeInspect in Betracht. Dank der kurzen Einrichtungszeit, Benutzerfreundlichkeit und des quasi-automatischen Betriebs fiel die Entscheidung schnell zugunsten des TubeInspect P16 aus. „Der entscheidende Faktor war, dass die hochauflösenden Digitalkameras die Geometrie unserer Rohre innerhalb nur weniger Sekunden messen und wir mit einfachen und leicht zu bedienenden Programmen schnell ein Biegemodel oder auch Korrekturdaten erstellen können, ergänzt Thorsten Dammann, Sachbearbeiter in den Technischen Diensten der Baugruppenfertigung bei CLAAS.
Heute verwendet CLAAS das TubeInspect für die Vermessung von Rohrgeometrien jeder Art. Die unterschiedlich großen Rohre variieren zwischen 4 und 150 Millimeter im Durchmesser sowie zwischen 5 und 5.000 Millimeter in der Länge und können bis zu 20 Biegungen aufweisen. Es handelt sich um medienführende Rohre für Öl, Wasser oder Luft bzw. um Geländerrohre. Die von TubeInspect erzielten Messergebnisse sind auch ein wichtiger Aspekt im ISOZertifizierungsprozess bei CLAAS.
Integrierte Smart-Factory-Prozesse
Zu den sehr häufig konstruierten und geplanten Bauteilen bei CLAAS gehören auch neue Hydraulikrohre. Sie werden mithilfe des Programms CATIA V6 konstruiert. Im Anschluss erstellt ein Programm den Koordinatensatz. Die daraus resultierende Biegetabelle kann direkt von der Konstruktionsabteilung an die TubeInspect-Messzelle übertragen werden.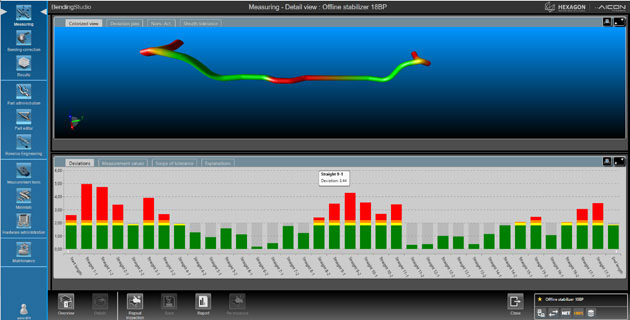
„Wir haben mittlerweile alle Konturlehren abgeschafft. Aber TubeInspect misst nicht nur, sondern prüft direkt gegen die hinterlegte Referenzgeometrie. Deshalb gibt es bei uns auch keine Musterleitungen mehr. Es gibt auch nur noch vereinzelt Schweißvorrichtungen, die sowohl für Prüfungen als auch später zum Schweißen verwendet werden“, sagt Dammann.
TubeInspect misst alle sieben Minuten
Die erste Überprüfung des gebogenen Rohres erfolgt gleich am Messgerät, da die Daten direkt auf dem Bildschirm angezeigt werden. Eventuelle Abweichungen werden sofort erkannt und die Korrekturdaten bei Bedarf an die Biegemaschine übermittelt.Da bei CLAAS alle Biegemaschinen mit dem Messsystem TubeInspect vernetzt sind, ist ein schneller und einfacher Austausch der Korrekturdaten gewährleistet. Ist das erste Rohr gebogen, das keine Korrektur erfordert,beginnt unverzüglich der Fertigungsprozess. Dabei wird der gesamte Auftrag in einem Durchlauf mit gleichbleibender Qualität gebogen.
„Unser AICON TubeInspect P16 misst Losgrößen von nur einem Bauteil – z.B. ein einzelnes Musterrohr – bis hin zu 150 Bauteilen. Pro Monat kommen ungefähr 50 bis 60 Teile dazu, die wir als Neuteile programmieren. So werden jeden Tag etwa 7.000 Leitungen gebogen, was ungefähr 200 Messvorgängen pro Tag in drei Schichten entspricht. Das heißt, es wird alle sieben Minuten eine Messung durchgeführt“, sagt Dammann.
TubeInspect P16 ist bereits das zweite Messgerät, das die Firma aus Harsewinkel erworben hat. Über zehn Jahre lang leistete das erste TubeInspect der Firma CLAAS hervorragende Dienste und erfüllte alle anspruchsvollen Messanforderungen. Dennoch interessierte sich das Unternehmen für ein Upgrade auf die verbesserte BendingStudio-Software, was jedoch mit einem älteren Messgerät kompliziert war.
„Dann erhielten wir ein überzeugendes Angebot für eine nagelneue Messzelle mit der aktuellsten Software, den neusten Kameras, LED-Technik und einem leicht vergrößerten Messraum, vom umfassendem Support einmal ganz abgesehen“, erinnert sich Dammann.
Der Umstieg auf neue Software
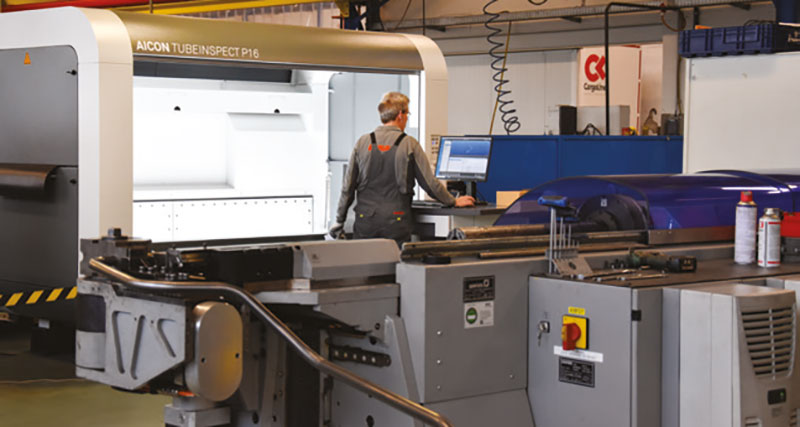
„Der Service und Support des AICON-Teams von Hexagon ist großartig“, sagte Dammann. „Das vorhandene Fachwissen im Bereich Rohfertigung ist einzigartig und ausgesprochen wertvoll.“
HxGN LIVE
HxGN LIVE, die jährliche konferenz von Hexagon, bietet inspirierende vorträge, unbegrenzte networking-möglichkeiten und neueste technologien.
TubeInspect
TubeInspect ist eine sofort einsatzbereite Messzelle, die speziell für die effiziente Qualitätskontrolle gebogener Rohre und Drähte entwickelt wurde.
BendingStudio XT
BendingStudio XT verknüpft alle Daten und Prozesse rund um die Fertigung von Biegebauteilen – von der Produktions- und Prozessplanung über die Fertigung bis hin zur Qualitätskontrolle.