Premier processus industriel total d'assemblage par la mesure
Défi d'assemblage à très grande échelle
Contact

Doté des technologies les plus avancées au niveau des matériaux, systèmes et processus industriels, l’A380 satisfait aux exigences internationales les plus strictes en matière de certification. Les sites européens d’Airbus, implantés en France, en Allemagne, au Royaume-Uni et en Espagne participent à la conception et à la fabrication de l’appareil.
Le site Jean-Luc Lagardère de Toulouse est spécifique à l’A380: on y reçoit tous les éléments de l’avion à assembler. La chaine de montage du dernier né d’Airbus est découpée en plusieurs unités. L’unité 1 est en charge du montage structural de l’avion. L’unité numéro 2 effectue les tests et essais sur l’avion assemblé et réalise le montage des moteurs. La troisième unité procède aux tests à l’extérieur qui préparent l’avion au premier vol.
Nouveaux défis d’assemblage
Le poste 40 au sein de l’unité 1 a la responsabilité de l’assemblage final de l’avion (tronçons et voilures). Pour cela, chaque élément (tronçons/voilures) sont mis en référence les uns par rapport aux autres. Au final il s’agit de respecter la géométrie de l’avion définie par le bureau d’étude. Le projet de l’assemblage de l’A380 fut initié dès 1998. Les nouveaux défis à relever furent nombreux : dimension exceptionnelle des tronçons, forme ovoïde de l’avion (circulaire sur les autres programmes), section fuselage à deux ponts, etc. L’objectif était également de supprimer les référentiel bâtis, utilisés jusqu’au programme A340. Ces bâtis, devaient être très précis pour permettre l’assemblage de l’avion et une vérification périodique était nécessaire puisque c’était le bâti lui-même qui garantissait la position des tronçons dans l’espace.
Grâce aux laser trackers performants et fiables de Leica Geosystems, l’assemblage par la mesure du produit est mature et peut être repris par les autres programmes...Au lieu de prendre les bâtis comme référentiel (avec toute une problématique de chaine de cote) l’idée maitresse consistait à aller mesurer directement l’avion, c’est-à-dire les éléments les uns par rapport aux autres dans leur propre référentiel. L’autre objectif était également de proposer des solutions d’assemblage sur des interfaces complexes (forme ovoïde, double pont).L’idée d’assemblage par la mesure à convaincu les responsables du programme A380! Thierry Fabre, en charge du projet d’assemblage par la mesure à Toulouse explique : “la base de ce travail résidait bien en amont du simple assemblage: il fallait mettre tous les sites de production en Europe d’accord sur les référentiels de l’avion. Chacun avait sa propre façon de travailler, ses propres objectifs et ses propres contraintes d’assemblages. La phase préparatoire fut ainsi primordiale afin d’assurer la cohérence des données issues de tous les sites Airbus.
Le choix logique de Leica Geosystems
De nombreux projets étaient déjà en production avec des lasers trackers Leica Geosystems en France (RCT à Nantes, Erebus à Meaulte, poste assemblage 15/21 à St Nazaire, mesure interface des tronçons A320 à Toulouse) ainsi que sur les sites de Brême (Allemagne), Broughton (Royaume‑Uni) et Filton (Royaume-Uni).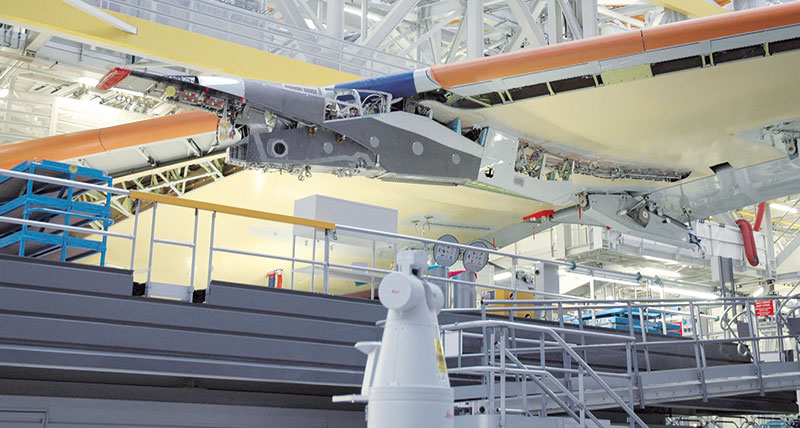
Détermination en amont des lignes de visée
Une fois les outillages et les méthodes de réglage définies, il a fallu étudier en CAO les lignes de visée des laser trackers dans un environnement très dense. En effet, dans l’ensemble des plates-formes et des structures métalliques qui composent le poste d’assemblage, il est difficile de garantir les “lignes de visée” entre les points de mesure sur l’avion et les laser tracker “il a fallu mettre en place le concept, déterminer le nombre de laser et déterminer la position optimale de chaque laser, un défi de plus à relever” cite Monsieur Charraud.Le choix de quatre Laser Trackers Leica Geosystems
A l’arrivée, le choix s’est portée sur 4 Leica laser trackers: deux pour le fuselage et deux pour les voilures. Ils sont tous les quatre interdépendants et liées par un référentiel commun. Ce dispositif garanti l’homogénéité et l’interchangeabilité des laser trackers. Le développement du logiciel spécifique de pilotage et de mesure s’interface avec le logiciel EmScon. Leica Geosystems a apporté son support au développement du script. “Le support de Leica Geosystems était essentiel pour assurer la cohérence du programme et l’utilisation des bonnes fonctions”, indique Monsieur Charraud.Une interface Homme-Machine simplifiée
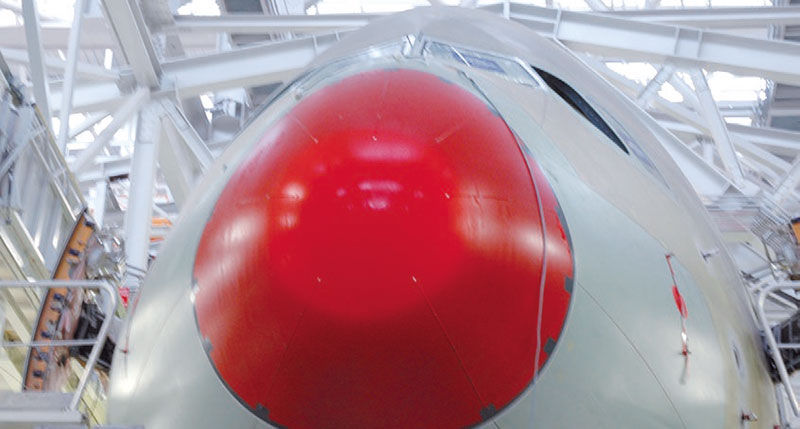
Test de validation et mise au point avant le premier avion
Une des difficultés du projet a consisté à valider avant le premier avion sur poste l’ensemble du process de mesure. (on ne pouvait pas disposer des tronçons et des voilures à l’avance !).Il a donc été nécessaire d’imaginer des procédures de test et validation avec des structures d’essais simulant partiellement les dimensions de l’avion. L’avion n° 1 (MSN O1) a permis de valider en grandeur réelle tout le processus de mesure.