Der erste vollständige industrielle Montageprozess auf Grundlage der Lasermessung
Die Montage ist eine gewaltige Herausforderung
Kontakt

Ausgerüstet mit modernster Technologie, was Materialien, Systeme und industrielle Verfahren angeht, erfüllt der A380 die strengsten internationalen Anforderungen für die Zulassung. Die europäischen Airbus-Standorte in Frankreich, Deutschland, Großbritannien und in Spanien sind an der Entwicklung und Fertigung der Maschine beteiligt.
Der Standort Jean-Luc Lagardère in Toulouse ist speziell für den A380 ausgelegt: Dort laufen alle Bauteile für die Montage des Flugzeugs zusammen. Die Montagestraße des jüngsten Airbus ist in mehrere Einheiten aufgeteilt. Die Einheit 1 ist mit der Montage der tragenden Teile des Flugzeugs befasst. Die Einheit Nummer 2 führt Tests und Versuche am montierten Flugzeug aus und übernimmt die Montage der Motoren. Die dritte Einheit nimmt die Tests im Freien vor, die das Flugzeug für den ersten Flug vorbereiten.
Dank der leistungsfähigen und zuverlässigen Laser Tracker von Leica Geosystems ist die Montage des Produktes auf der Grundlage der Lasermessung ein ausgereiftes System und kann bei anderen Programmen übernommen werden.Die grundlegende Idee bestand darin, das Flugzeug direkt zu vermessen, das heißt die Elemente in ihrem Bezug zu einander in ihrem eigenen Bezugssystem, anstatt die Rahmen als Bezugssystem zu verwenden (mit der ganzen Problematik der Toleranzkette). Die andere Aufgabe war, auch Lösungen für die Montage bei komplexen Schnittstellen zu finden (ovale Form, zwei Decks). Die Idee der Montage auf Grundlage der Lasermessung hat die Verantwortlichen für das A380-Programm überzeugt!
Thierry Fabre, zuständig für die Montage auf Grundlage der Lasermessung in Toulouse, erklärt: “Die Problematik dieser Arbeit ging weit über die einfache Montage hinaus. Es war notwendig, bei den Bezugssystemen für das Flugzeug alle europäischen Produktionsstandorte zu vereinheitlichen. Jeder hatte seine eigene Arbeitsweise, seine eigenen Zielsetzungen und seine eigenen Zwänge bei der Montage. Die Vorbereitungsphase war also entscheidend, um sicherzustellen, dass die Daten aus allen Airbusstandorten kohärent sind.”
Martial Charraud, der am Messprojekt in Nantes (RCT) und Toulouse (A320) beteiligt war und jetzt zum Team von Thierry FABRE für den A380 gehört, betont, “dass die ersten Projekte zur Montage von Airbussen mit Hilfe der Lasermessung in enger Zusammenarbeit mit der Hauptniederlassung von Leica Geosystems in der Schweiz entwickelt wurden. Durch diesen Erfolg bestätigt, haben wir uns natürlich an Leica Geosystems gewendet, als es darum ging, einen Anbieter für die Montage des A380 zu suchen. Das Ziel war, unsere Erfahrung zu nutzen und sie auf den A380 anzuwenden. Ich kenne außerdem die Produkte von Leica Geosystems sehr gut und wir haben volles Vertrauen in sie”.
Die Montagestraße des A380 ist auf eine Lebensdauer von 30 bis 40 Jahren angelegt. Umso wichtiger ist die Wahl guter, vertrauenswürdiger und dauerhafter Partner. Die verwendeten Systeme, vor allem die Computersoftware und die Automatisierungssoftware sind sehr schnell überholt. “Die Servicegarantie für das alte Material beispielsweise ist äußerst wichtig. Mit Leica Geosystems haben wir eine sehr langfristige Zusammenarbeit vereinbart. Wir haben auch die Garantie, dass die Werkzeuge bei Erreichen einer hohen Auslastung voll funktionsfähig und leistungsfähig sind”, betont Herr Fabre.
Die speziell entwickelte Steuerungs- und Mess-Software kommuniziert mit der EmScon-Software. Leica Geosystems hat bei der Entwicklung des Scripts Unterstützung geleistet. “Die Unterstützung durch Leica Geosystems war wesentlich, um die Kompatibilität des Programms und die Nutzung der richtigen Funktionen zu garantieren” fügt Herr Charraud an.
Da das Messsystem in den Montageprozess des Flugzeugs integriert ist, der vom Montagepersonal gesteuert wird, war dieses von Anfang an direkt an der Projektentwicklung und bei der Bestimmung der Schnittstellen Mensch/Maschine beteiligt. Das grundlegende Ziel war, die Bedienung für den Benutzer (der nicht Messspezialist ist) einfach zu gestalten. Und um das Werkzeug einfach zu gestalten, müssen vorher komplizierte Dinge gemacht werden: automatische Steuerung und Zielsuche, Wiedergabe der Ergebnisse auf dem Bildschirm, damit die Bediener die richtige Position der Elemente des Flugzeugs analysieren und bewerten können, uns so weiter.
Der Standort Jean-Luc Lagardère in Toulouse ist speziell für den A380 ausgelegt: Dort laufen alle Bauteile für die Montage des Flugzeugs zusammen. Die Montagestraße des jüngsten Airbus ist in mehrere Einheiten aufgeteilt. Die Einheit 1 ist mit der Montage der tragenden Teile des Flugzeugs befasst. Die Einheit Nummer 2 führt Tests und Versuche am montierten Flugzeug aus und übernimmt die Montage der Motoren. Die dritte Einheit nimmt die Tests im Freien vor, die das Flugzeug für den ersten Flug vorbereiten.
Neue Herausforderungen bei der Montage
Die Station 40 der Einheit 1 ist für die Endmontage des Flugzeugs verantwortlich (Segmente und Tragflächen). Dafür werden alle Elemente (Segmente/Tragflächen) miteinander abgeglichen. Schließlich muss die Flugzeuggeometrie, wie sie vom Entwicklungsbüro vorgegeben wurde, eingehalten werden. Das Projekt für die Montage des A380 wurde 1998 begonnen. Zahlreiche neue Herausforderungen mussten gemeistert werden: die außergewöhnlichen Ausmaße der Segmente, die ovale Form des Flugzeugs (kreisförmig bei den anderen Programmen), Rumpfsegmente mit zwei Decks, etc. Außerdem sollten die Rahmen, die bis zum Programm des A340 als Bezugssystem verwendet wurden, ersetzt werden. Diese Rahmen mussten sehr exakt sein, um die Montage des Flugzeugs zu ermöglichen, und sie mussten regelmäßig überprüft werden, denn der Rahmen selbst garantierte die richtige Position der Segmente im Raum.Dank der leistungsfähigen und zuverlässigen Laser Tracker von Leica Geosystems ist die Montage des Produktes auf der Grundlage der Lasermessung ein ausgereiftes System und kann bei anderen Programmen übernommen werden.Die grundlegende Idee bestand darin, das Flugzeug direkt zu vermessen, das heißt die Elemente in ihrem Bezug zu einander in ihrem eigenen Bezugssystem, anstatt die Rahmen als Bezugssystem zu verwenden (mit der ganzen Problematik der Toleranzkette). Die andere Aufgabe war, auch Lösungen für die Montage bei komplexen Schnittstellen zu finden (ovale Form, zwei Decks). Die Idee der Montage auf Grundlage der Lasermessung hat die Verantwortlichen für das A380-Programm überzeugt!
Thierry Fabre, zuständig für die Montage auf Grundlage der Lasermessung in Toulouse, erklärt: “Die Problematik dieser Arbeit ging weit über die einfache Montage hinaus. Es war notwendig, bei den Bezugssystemen für das Flugzeug alle europäischen Produktionsstandorte zu vereinheitlichen. Jeder hatte seine eigene Arbeitsweise, seine eigenen Zielsetzungen und seine eigenen Zwänge bei der Montage. Die Vorbereitungsphase war also entscheidend, um sicherzustellen, dass die Daten aus allen Airbusstandorten kohärent sind.”
Die logische Wahl von Leica Geosystems
In Frankreich liefen schon zahlreiche Projekte mit den Laser Trackern von Leica Geosystems (RCT in Nantes, Erebus in Meaulte, Montagestation 15/21 in St Nazaire, Messung der Schnittstellen der Segmente des A320 in Toulouse), ebenso am Standort Bremen (Deutschland), in Broughton (Großbritannien) und Filton (Großbritannien).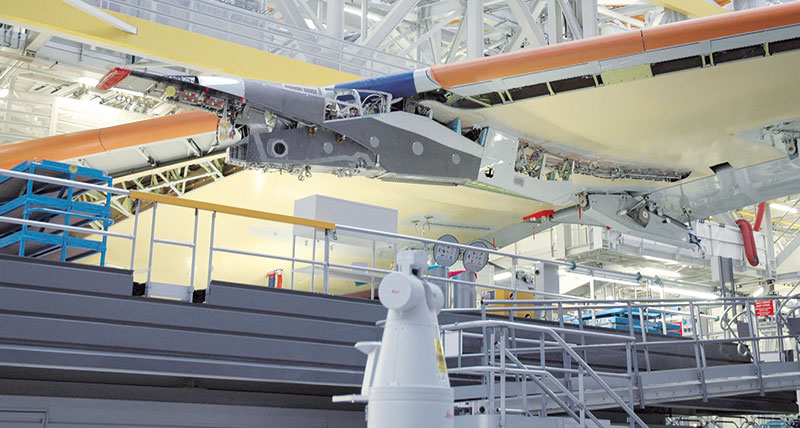
Die Montagestraße des A380 ist auf eine Lebensdauer von 30 bis 40 Jahren angelegt. Umso wichtiger ist die Wahl guter, vertrauenswürdiger und dauerhafter Partner. Die verwendeten Systeme, vor allem die Computersoftware und die Automatisierungssoftware sind sehr schnell überholt. “Die Servicegarantie für das alte Material beispielsweise ist äußerst wichtig. Mit Leica Geosystems haben wir eine sehr langfristige Zusammenarbeit vereinbart. Wir haben auch die Garantie, dass die Werkzeuge bei Erreichen einer hohen Auslastung voll funktionsfähig und leistungsfähig sind”, betont Herr Fabre.
Vorbestimmung der Sichtlinien
Nach der Festlegung der Werkzeuge und der Methoden der Justierung mussten die Sichtlinien der Laser Tracker in einer sehr dichten Umgebung mit CAD studiert werden. Denn bei all den Plattformen und Metallstrukturen, die die Montagestation bilden, ist es schwer, “Sichtlinien” zwischen den Messpunkten am Flugzeug und den Laser Trackern zu garantieren. “Es war erforderlich, ein Konzept auszuarbeiten, die Anzahl der Laser festzulegen und die optimale Position jedes Lasers zu bestimmen, eine zusätzliche Herausforderung”, sagt Herr Charraud.Die Wahl von vier Laser Trackern von Leica Geosystems
Zunächst fiel die Wahl auf vier Leica Laser Tracker: zwei für den Rumpf und zwei für die Tragflächen. Alle vier sind voneinander abhängig und durch ein gemeinsames Bezugssystem miteinander verbunden. Diese Anordnung garantiert die Homogenität und die Austauschbarkeit der Laser Tracker.Die speziell entwickelte Steuerungs- und Mess-Software kommuniziert mit der EmScon-Software. Leica Geosystems hat bei der Entwicklung des Scripts Unterstützung geleistet. “Die Unterstützung durch Leica Geosystems war wesentlich, um die Kompatibilität des Programms und die Nutzung der richtigen Funktionen zu garantieren” fügt Herr Charraud an.
Eine vereinfachte Schnittstelle Mensch-Maschine
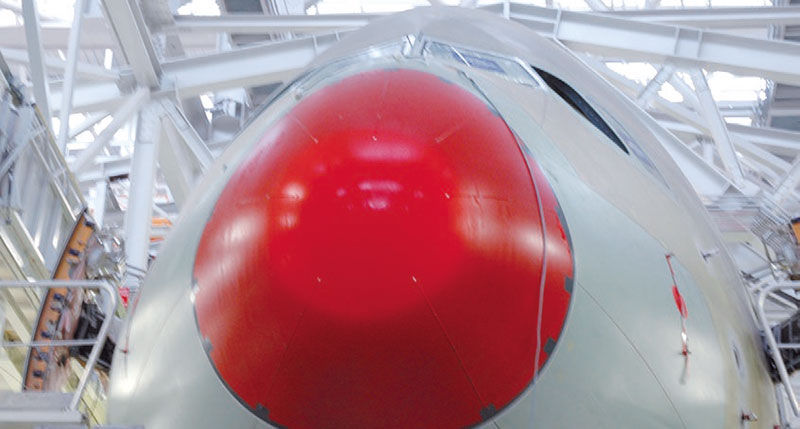