El primer proceso de montaje industrial total mediante medición
Un reto de montajea a gran escala
Contacto

El A380 está equipado con las tecnologías más avanzadas en cuestión de materiales, sistemas y procesos industriales y cumple los requisitos internacionales más estrictos en materia de certificación. El diseño del A380 es europeo por excelencia, ya que han sido cuatro los países que han participado en su fabricación: Alemania, Reino Unido, España y Francia.
Las instalaciones de Jean-Luc Lagardère en Toulouse son esenciales para el A380 porque es en ellas en donde se reciben todos los elementos necesarios para montar el avión. La cadena de montaje del último modelo Airbus se divide en varias unidades. La unidad 1 se encarga del montaje estructural del avión y en la unidad 2 se llevan a cabo los ensayos del avión ya montado: pruebas de esfuerzo, llenado hidráulico, instalación de verificación del sistema, equipo de control de vuelo… En la unidad 3 se realizan ensayos exteriores que dejan el avión listo para el primer vuelo.
Nuevos retos de montaje
El puesto 40 de la unidad 1 se encarga del montaje final del avión (estructura del ala/alas). Para ello, se hace referencia a cada elemento (estructura del ala/alas) con respecto a los demás. Eso supone respetar la geometría del avión definida por el departamento de diseño. El proyecto de construcción del A380 comenzó en 1998 y planteó numerosos retos: las enormes dimensiones de las estructuras de las alas, la forma ovoide del avión (circular en otros casos) o el fuselaje con puente doble. El objetivo era suprimir también las plantillas de referencia que se habían utilizado hasta el programa A340. Estas plantillas debían ser muy precisas para proceder al montaje del avión y además era necesario realizar una verificación periódica, ya que era la propia plantilla la que garantizaba la posición de las estructuras de las alas en el espacio.
Gracias a los fiables y versátiles laser trackers de Leica Geosystems, el montaje mediante medición del producto ha podido desarrollarse completamente y puede extrapolarse a otros programas.En lugar de tomar las plantillas como referencia (lo que suponía múltiples problemas con respecto a la acumulación de tolerancias), se decidió medir el avión directamente, es decir, medir los elementos con respecto a los demás, que servían como referencia. Otro de los objetivos era conseguir soluciones de montaje para superficies de contacto complejas (forma ovoide, puente doble). La idea de realizar el montaje mediante mediciones convenció a los responsables del programa A380. Thierry Fabre, el encargado del proyecto de montaje mediante mediciones de Toulouse, explica: “la base de este trabajo se encuentra más allá del simple montaje: era necesario que todas las plantas de producción europeas se pusieran de acuerdo en cuanto a las referencias del avión; pero cada una tenía sus propias formas de trabajar, sus propios objetivos y sus propias restricciones de montaje. Por lo tanto, la fase preparatoria era esencial para garantizar la coherencia de los datos procedentes de todas las plantas Airbus.
La lógica elección de Leica Geosystems
Actualmente ya se están desarrollando múltiples proyectos con laser trackers de Leica Geosystems (RCT en Nantes, Erebus en Meaulte, puesto de montaje 15/21 en St Nazaire, medición de superficie de contacto de las estructuras del ala del A320 en Toulouse).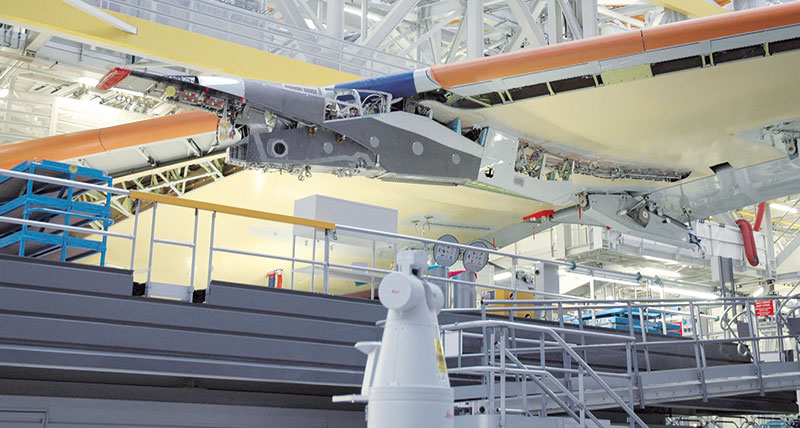
La cadena de montaje del A380 se diseñó para que su vida útil alcance los 30-40 años, por lo que la elección de buenos socios, fiables y duraderos, es muy importante. Los métodos utilizados se quedan obsoletos muy rápidamente, sobre todo los programas de automatización y computerización. “Por ejemplo, la garantía de mantenimiento del material antiguo es esencial. Nos basamos en una relación a muy largo plazo. Además, tenemos la seguridad de que durante el proceso gradual de montaje todas las herramientas estarán operativas y a pleno rendimiento” añade Fabre.
Determinación previa de las líneas de visión
Tras definir las herramientas y los métodos de configuración, era necesario estudiar con herramientas CAD [Diseño asistido por ordenador] las líneas de visión de los laser trackers en un entorno muy denso. De hecho, dentro del conjunto de plataformas y estructuras metálicas que forman el puesto de montaje, es difícil garantizar las “líneas de visión” entre los puntos de medición del avión y el laser tracker. “Teníamos que fijar el concepto, determinar el número de láseres y su posición óptima: un reto cada vez mayor”, apunta Charraud.La elección de cuatro laser trackers de Leica Geosystems
Inicialmente se seleccionaron cuatro laser trackers de Leica: dos para el fuselaje y dos para las alas. Los cuatro eran interdependientes y estaban vinculados mediante una referencia común. Este sistema garantiza la homogeneidad y la posibilidad de intercambiar los laser trackers. El desarrollo del programa específico de medición y pilotaje está vinculado al programa EmScon. Leica Geosystems ha proporcionado apoyo durante el desarrollo del script. Según Charraud, “la ayuda de Leica Geosystems fue esencial para garantizar la coherencia del programa y el uso de las funciones adecuadas”.Una interfaz de usuario simplificada
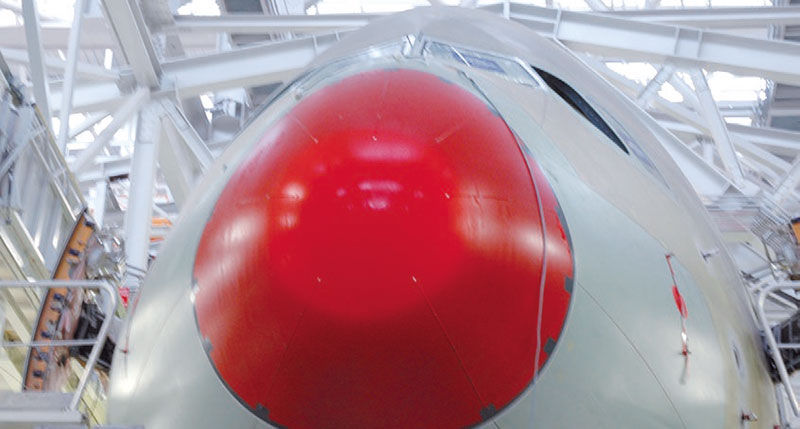
Ensayo de validación y puesta a punto antes del tener el primer avión
Una de las dificultades del proyecto fue validar todo el proceso de medición antes de tener el primer avión. (No contábamos con las estructuras de las alas ni con las alas con anterioridad).Por lo tanto, fue necesario hacerse una idea de los procedimientos de ensayo y validación con estructuras de prueba que simulaban parcialmente las dimensiones del avión. El avión nº 1 (MSN O1) permitió validar el proceso de medición completo a escala real.